When it comes to manufacturing parts and components, CNC machining is a popular method used across various industries. CNC, or Computer Numerical Control, machining involves the use of computer software to control the movement and operation of cutting tools and machinery. One particular type of CNC machining that has gained traction in recent years is 5 axis CNC machining.
So, what exactly is 5 axis CNC machining? In simple terms, it refers to a CNC machining process that utilizes five axes of motion to cut and shape a workpiece. The five axes include X, Y, and Z (which represent the linear movements of the cutting tool), as well as A and B (which represent the rotation of the workpiece).
Why is 5 axis CNC machining important? Well, it allows for the creation of complex and intricate parts and components that may not be possible with traditional machining methods. With 5 axis CNC machining, manufacturers can produce parts with complex geometries, angles, and curves that would be difficult or impossible to achieve with traditional 3 axis machining.
The advantages of 5 axis CNC machining are numerous. For one, it provides greater precision and accuracy in machining. This is because the five axes of motion allow for the cutting tool to move in multiple directions and angles, which results in a more accurate and consistent finish. Additionally, 5 axis CNC machining can be more time-efficient compared to traditional machining methods, as it can cut and shape multiple sides of a workpiece in a single setup.
Moreover, 5 axis CNC machining is more versatile in terms of the types of materials it can handle. It can work with a wide range of materials, including metals, plastics, composites, and ceramics, making it a popular choice across various industries.
Understanding 5 Aixs CNC Machining
5 axis CNC machining is a highly advanced manufacturing process that involves the use of computer-controlled cutting tools to create complex and precise shapes and designs. The process utilizes five axes of motion, including three linear axes (X, Y, and Z) and two rotational axes (A and B), to cut and shape a workpiece from all sides and angles.
Types of 5 Axis CNC Machining:
There are two main types of 5 axis CNC machining: simultaneous and indexed. In simultaneous 5 axis CNC machining, the cutting tool moves along all five axes at the same time, allowing for continuous and smooth cutting of the workpiece. Indexed 5 axis CNC machining, on the other hand, involves moving the workpiece to different angles and positions to enable cutting along the required axes.
How Does 5 Axis CNC Machining Work?
5 axis CNC machining begins with the design of a CAD (Computer-Aided Design) model of the desired part or component. The CAD model is then converted into a CAM (Computer-Aided Manufacturing) program, which specifies the cutting tool path and parameters. The CAM program is then loaded into the CNC machine, which sets up the workpiece and cutting tool accordingly.
Once the setup is complete, the CNC machine starts the cutting process by moving the cutting tool along the X, Y, and Z axes, while also rotating the workpiece along the A and B axes as required. The process continues until the entire part or component has been cut and shaped to the desired specifications.
During the cutting process, the CNC machine continuously monitors the cutting tool and adjusts its position and cutting speed as needed to ensure accurate and consistent cutting. The finished part or component is then removed from the CNC machine and subjected to any required post-processing steps, such as polishing or coating.
Tools used in 5 Axis CNC Machining:
The success of 5 axis CNC machining relies heavily on the tools used in the process. Here are some of the cutting tools that are commonly used in 5 axis CNC machining:
End Mills
End mills are cutting tools that are used for removing material from the workpiece. They come in various shapes and sizes and can be used for cutting a range of materials, including metal, wood, and plastics.
Drills
Drills are used for creating holes in the workpiece. They come in various sizes and can be used for drilling through different materials, including metals, plastics, and ceramics.
Reamers
Reamers are used for enlarging and smoothing out holes in the workpiece. They come in different shapes and sizes and can be used for different materials, including metal, wood, and plastics.
Taps
Taps are used for cutting internal threads in the workpiece. They come in various sizes and can be used for different materials, including metals, plastics, and composites.
In addition to these cutting tools, 5 axis CNC machining also uses various other tools and accessories, including holders, chucks, collets, and tool setters, among others. These tools and accessories help ensure accuracy, efficiency, and consistency in the manufacturing process.
The selection and use of the right tools are critical to the success of 5 axis CNC machining. Manufacturers must carefully choose the appropriate cutting tools and accessories based on the materials being machined, the geometry of the part, and the desired surface finish.
Recommended Read: Industry 4.0 and CNC Machining: Revolutionizing Manufacturing
Comparison of 5 Axis CNC Machining with other CNC Machining Techniques
5 axis CNC machining has its fair share of advantages over the traditional 3 axis machining method, but that doesn’t mean other CNC machining techniques should be overlooked. It’s important to weigh the pros and cons of each technique before selecting the best one for your project. So, let’s take a closer look at how 5 axis CNC machining compares to other popular CNC machining methods.
3 axis CNC machining
3 axis CNC machining is the most basic type of CNC machining and involves the movement of the cutting tool along three axes: X, Y, and Z. While 3 axis machining is simple and efficient for machining simple parts with straight edges, it is limited in its ability to machine complex geometries and curved surfaces. 5 axis CNC machining, on the other hand, offers greater flexibility and can be used to machine more complex parts with curved and angled surfaces.
4 axis CNC machining
4 axis CNC machining involves the same X, Y, and Z movements as 3 axis machining, but with the addition of a rotary axis that allows the cutting tool to rotate around the part. This allows for more complex machining operations, such as engraving and carving on curved surfaces. However, 4 axis machining is limited to rotational movements in one plane, whereas 5 axis CNC machining allows for simultaneous movement in multiple planes.
6 axis CNC machining
6 axis CNC machining adds an additional linear axis to the X, Y, and Z movements, as well as a second rotary axis. This allows for even greater flexibility and can be used to machine parts with very complex geometries. However, 6 axis CNC machining is typically more expensive and complex than 5 axis machining, and may not be necessary for all applications.
Applications of 5 Axis CNC Machining
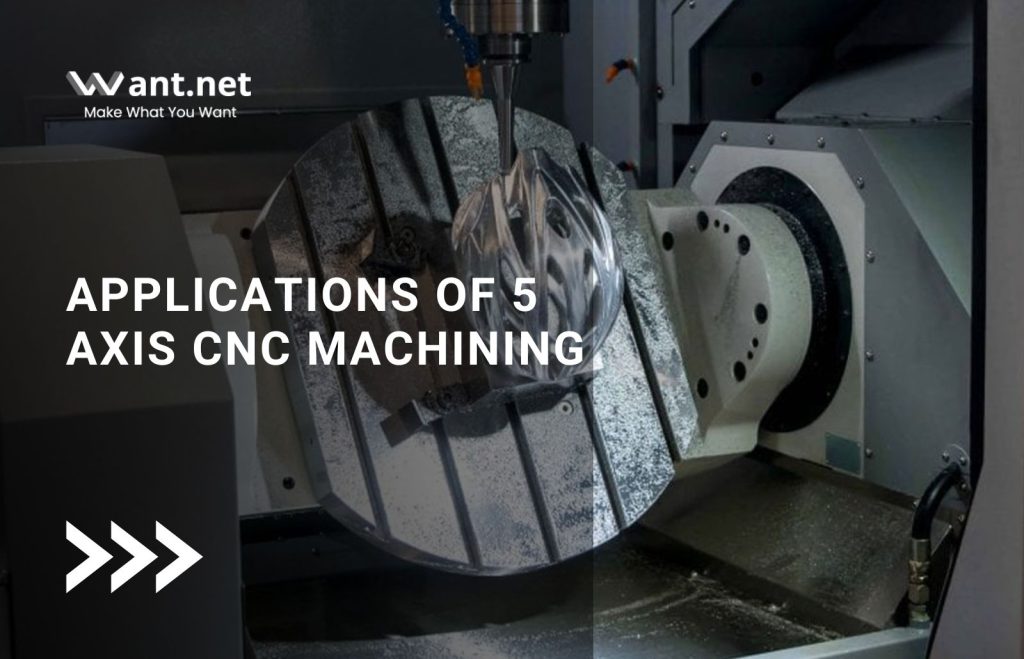
5 axis CNC machining is a versatile and powerful manufacturing process that finds applications across various industries. Here are some of the major applications of 5 axis CNC machining:
Aerospace: The aerospace industry requires high-precision and complex parts that are often made from tough materials like titanium and composites. 5 axis CNC machining can produce these parts with extreme accuracy and consistency, making it a popular choice in the industry.
Automotive: The automotive industry also requires high-precision and complex parts, especially for engines, transmissions, and suspension systems. 5 axis CNC machining can produce these parts with a high degree of accuracy and efficiency, reducing manufacturing time and costs.
Medical: 5 axis CNC machining is widely used in the medical industry for the production of orthopedic implants, prosthetics, surgical instruments, and other medical devices. The process ensures precision and accuracy in the manufacturing of these critical components.
Defense: The defense industry requires components that are highly accurate and reliable. 5 axis CNC machining can produce complex parts with tight tolerances, making it ideal for manufacturing components such as missile parts, gun components, and armor.
Artistic: 5 axis CNC machining has found applications in the artistic world, as it can be used to create intricate and complex sculptures, moldings, and other decorative pieces with great precision and accuracy.
Industrial: 5 axis CNC machining is also used in industrial manufacturing for a range of components, including pumps, valves, and gears, among others. It allows for efficient and accurate production of these critical components.
Tips for 5 Axis CNC Machining:
While 5 axis CNC machining offers a wide range of benefits, it requires careful planning and execution to ensure optimal results. Here are some tips for achieving success in 5 axis CNC machining:
Preparing the workpiece: Preparing the workpiece is critical to ensuring optimal results in 5 axis CNC machining. The workpiece must be properly secured and positioned on the machine to prevent movement during the machining process. Additionally, the surface of the workpiece must be properly cleaned and prepared to ensure proper adhesion of the cutting tool.
Choosing the right tool: Choosing the right cutting tool is essential for achieving optimal results in 5 axis CNC machining. The tool must be properly sized and shaped for the specific material being machined and the geometry of the part. Additionally, the cutting tool must be made from the appropriate material to withstand the demands of the machining process.
Optimizing cutting parameters: Optimizing cutting parameters, such as cutting speed, feed rate, and depth of cut, is essential for achieving optimal results in 5 axis CNC machining. The cutting parameters must be carefully selected based on the material being machined, the geometry of the part, and the desired surface finish.
Performing regular maintenance: Performing regular maintenance on the machine and cutting tools is critical for achieving optimal results in 5 axis CNC machining. The machine must be regularly cleaned and lubricated to ensure smooth and accurate movement. Additionally, the cutting tools must be regularly sharpened and replaced to maintain optimal cutting performance.
5 axis CNC machining requires careful planning, execution, and maintenance to achieve optimal results. By following these tips, manufacturers can maximize the efficiency and accuracy of their 5 axis CNC machining processes.
Recommended Read: How to Achieve High-Quality CNC Machining Results
Challenges in 5 Axis CNC Machining:
While 5 axis CNC machining offers a wide range of benefits, it also presents a number of challenges. Here are some of the key challenges associated with 5 axis CNC machining:
Complexity: 5 axis CNC machining is inherently more complex than traditional 3 axis machining. The additional degrees of freedom and movement required in 5 axis machining require more complex programming, tool paths, and machine setups. As a result, manufacturers may need to invest in specialized software, equipment, and training to successfully implement 5 axis CNC machining.
Operator skill: 5 axis CNC machining requires highly skilled operators who are familiar with the complex programming, tool paths, and machine setups required for this type of machining. Additionally, operators must be able to monitor the machining process closely and make adjustments as needed to ensure optimal results.
Machine rigidity: 5 axis CNC machining requires a high degree of machine rigidity to ensure optimal cutting performance and accuracy. The additional degrees of movement required in 5 axis machining can put additional stress on the machine, leading to deflection, vibration, and other issues that can affect the quality of the machined part.
Material selection: The selection of materials for 5 axis CNC machining can also be a challenge. Some materials may be more difficult to machine than others, requiring specialized cutting tools, parameters, and machine setups. Additionally, the choice of material can affect the overall performance and accuracy of the machined part.
Future of 5 Axis CNC Machining
The future of 5 axis CNC machining looks bright, with advancements in technology and integration with AI and automation promising to revolutionize the industry. These innovations will not only improve efficiency and accuracy but also open up new possibilities for industries that rely on CNC machining.
One of the biggest advancements in 5 axis CNC machining is the development of hybrid machines that combine additive and subtractive manufacturing. These machines can print metal parts and then use CNC machining to refine and finish them, reducing waste and improving the speed of production.
Integration with AI and automation will also play a key role in the future of 5 axis CNC machining. With the use of sensors and data analytics, machines will be able to optimize their own cutting parameters and adjust in real-time to changes in the material being machined. This will lead to increased efficiency, accuracy, and reduced downtime.
The potential impact of these advancements on industries such as aerospace, automotive, medical, defense, and artistic is significant. With greater precision and speed, 5 axis CNC machining will allow manufacturers to create more complex and intricate parts that were previously impossible to make. This will ultimately lead to more innovative products and better outcomes for these industries.
FAQ
What are the disadvantages of 5-axis machining?
One of the main disadvantages of 5-axis machining is the higher cost of the machines and tooling. Additionally, 5-axis machining requires highly skilled operators and programmers, which can increase labor costs. The complexity of 5-axis machining can also lead to longer lead times and increased setup times.
Can any material be machined with 5 axis CNC machines?
In theory, any material that can be machined with traditional 3-axis machines can also be machined with 5-axis CNC machines. However, certain materials may require specialized tooling and cutting parameters to achieve optimal results.
How long does it take to set up a 5 axis CNC machine?
The setup time for a 5-axis CNC machine can vary depending on the complexity of the part being machined and the experience of the operator. Generally, setup times can range from a few hours to several days.
What CAD/CAM software is best for 5 axis CNC machining?
There are several CAD/CAM software programs that are specifically designed for 5-axis CNC machining, including Mastercam, NX, and PowerMill. The best software for a particular application will depend on the specific needs and requirements of the project.