Best Injection Molding Service for Custom Parts
Looking for reliable plastic injection molding manufacturer for your next project? Try us today! Get an quick online quote to start now!
- Instant Quote
- Fast Turnaround
- Pay After Delivery
- All uploads are secure and confidential
Premium Injection Molding Service Trusted by
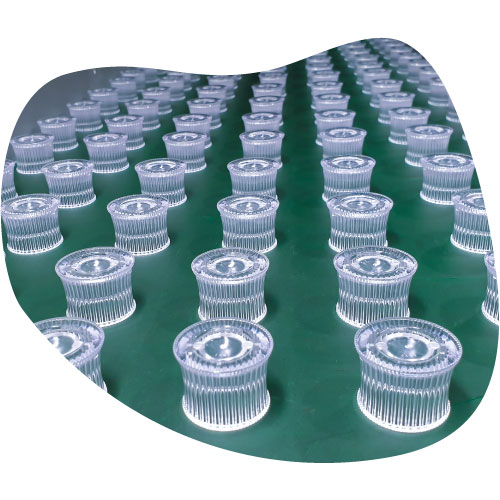
Working with The Best Injection Molding Suppliers in China
As an on-demand online manufacturer, Want.net partners with hundreds of injection molding manufacturers in China. We review their capacity and service level from time to time. Only the top 10% companies within the industry can be included in our network. And Want.net will take care of the quality inspection process once our partners finish the project. All of these will ensure your projects will only be produced by the best of the best.
How Custom Plastic Injection Molding Works
The plastic injection molding process requires an injection molding machine, raw plastic material, and a machined mold. The raw plastic material is first melted in the injection unit and is then injected into the mold—most often machined from steel or aluminum—where it cools and solidifies into the final plastic part.
At Want.net, we first review your plastic injection molding online quote, then consult with you to ensure your specifications, lead time, and price fit your project needs. We then use your 3D part data to CNC machine a high-quality injection mold. Once the molded parts are created, we send samples for your approval. Once the mold is approved, we will begin the mass production process.
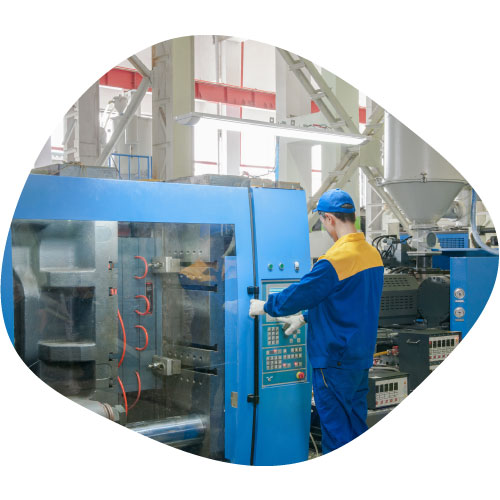
Why Choose Our Injection Mold Making Services
We at Want.net provide one-stop plastic injection molding service with our advanced network of Chinese manufacturer network. Our technical supports will help you from material selections, tool design, prototype, mass production, and quality inspection.
Our Custom Injecction Molding Capabilities
Rapid prototype tooling, also known as soft tooling, is a process of creating the tooling for plastic injection molding at a lower price and quicker lead time. The main goal of prototype tooling is to create a tooling for the manufacturer to validate and test before the final production. Rapid prototype tooling is an essential part of the product development process. It’s a budget-friendly method to find the potential defects of the product at the early stage.
As you can tell by its name, production tooling is to create the tooling for mass production of your plastic injection molding project. When your product has been thoroughly tested, tweaked, and ready for mass production. It’s time to create production tooling. Since production tooling will be used to produce the final product at a large scale, it has to be of the best quality and precise. That’s why it’s more expensive than prototype tooling and takes longer to produce.
Family injection mold is used to make more than one different molded parts that are made in the same material. Usually, those parts will be fit together. If two halves of molded parts construct your product, a family injection mold will be a great choice. Instead of making multiple injection molds to make one parts, family injection mold can make more molded parts with one single injection mold. That will hugely reduce the cost and time of your plastic injection molding project.
Single cavity injection mold consists of only one cavity. That means one molded part is produced per injection cycle. Here are the benefits of single cavity mold:
- Cost-effective. Single cavity mold is cheaper than multi-cavity one.
- Quick lead time. It takes a shorter turnaround time for the production of single cavity molds because it’s easy to manufacture.
- Easy to design. Single cavity molds are easy to design because of their simple construction.
Multi-cavity injection mold consists of more than one cavity so it can make more than one part per injection cycle. Multi-cavity molds are more expensive than single cavity, and production takes a longer turnaround time. But you will benefit from the higher output per batch, lower cost per unit, and quicker lead time for your molded parts.
Overmolding, also known as two-shot injection molding, is a multi-step plastic injection method where two or more parts are molded over top of one another. It’s widely used to create multi-colour molded parts or combine more than one material into a single molded part.
If you need a plastic layer around metal parts, insert molding is what you need. Here’s an example to better understand insert molding: imagine you are developing a screwdriver, and you need to add a plastic handle to the metal parts. The process of insert molding will create a place to fix the metal screwdriver and insert the metal into the cavity. In that way, the plastic will be injected around the metal screwdriver.
IMD (In Mold Decorating) and IML (In Mold Labeling) are used to create a visually appearance, like patterns or labels, during the injection molding cycle. A variety of textures, colors and surface coatings are available.
Custom Injection Molding Materials
Our plastic injection molding service uses a wide range of plastic, making it suitable for several applications across many industries. As a leading plastic injection molding company, we have over 50 thermoplastics and thermosetting plastics for injection molding. Check out some of the plastic materials you can choose for your parts.
* If you can’t find the materials you are looking for, we can still source for you. Just contact us to discuss more.
Surface Finishing for Plastic Injection Molding
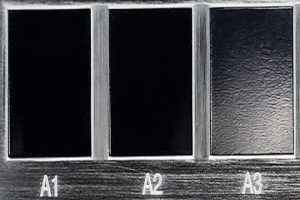
B-grade finishes use grit sandpaper to produce parts with a slightly rougher finish than grade A. Custom molded plastic parts that undergo B-grade finishing have a matte surface texture.
C-grade finishes use grit sanding stones to produce a rough, uneven surface. Injection molded plastic parts that undergo C-grade finishing have a matte surface texture.
D-grade finishes use grit and dry glass beads or oxide to produce a rough, textured finish. Products can have a satin or dull finish depending on the type of material used.
Injection Molding Surface Finishes can create a smooth, glossy appearance on plastic objects. This procedure is frequently used to reduce wear and friction while also enhancing the part’s visual appeal.
Surface treatments can be created using a variety of techniques, including tumbling, polishing, sanding, and buffing.
Online Injection Molding Service for Custom Parts
At Want.net, customers can get the finest quality injection molding services for custom parts. Not only this, they can order customized molding parts anywhere in the world by accessing our instant quote service for injection molding in China.
Injection Molding Process
Injection molding is a process of making parts and components by inserting molten material into a mold. A wide range of materials, including confections, metals, elastomers, glassware and most frequently thermosetting and thermoplastic polymers, are used for injection molding.
The material is heated until it becomes molten, injected into a mold cavity, where it cools and takes on the desired shape, and then removed from the mold.
The procedure is frequently used to make intricately shaped items, including components with complicated geometries.
The part goes through several post-molding operations, such as trimming, painting, or assembly, after being molded before being normally ejected from the mold by a stripper plate. Following are the steps in the injection molding process:
What Steps Are Involved in the Injection Molding Process?
- Design: The first step is to create a design for the molded part. The design must be appropriate for injection molding, taking into account the selected material, the part’s size and form, and the desired surface polish.
- Mold Design: The design of the mold itself comes next. To inject the molten material and shape the part, it is necessary to create an inner and outer surface.
- Tooling: Making the mold’s actual tooling is the third phase. The injection mold, a die, and the ejector pins must all be made.
- Injection Molding: The molten material is then injected into the mold cavity. An injection molding machine with high pressure is used for this.
- Cooling and Ejection: The part is ejected from the mold after cooling down in the fifth phase. Ejector pins or stripper plates are frequently used to do this.
- Post-Molding Processes:The last stage is to carry out any post-molding procedures, such as trimming, painting, or assembly.
How to Save Cost on Tooling with Injection Molding?
- Choose a Standard Mold Base:You can save money on tooling costs by purchasing a conventional mold base. Standard mold bases can be used to create injection molds from a range of materials because they are already constructed.
- Use a Hot Runner System: A hot runner method can reduce the amount of steel required to create the mold, lowering the cost of tooling.
- Choose Low-Cost Tooling Materials:Use less expensive materials like aluminum or plastic instead of stainless steel or other pricy tooling materials.
- Choose a Simpler Mold Design: Making complex molds costs more money. To save money, try to simplify the mold design.
- Outsource Tooling:You can save money by buying sourcing tooling for injection mold.
What Is Custom Injection Molding?
Custom injection molding is a way to create custom-designed parts or components by melting down plastic resin pellets and injecting them under high pressure into a mold. The method is frequently used to generate intricate pieces that are impossible to produce using traditional manufacturing processes.
The injection molding process is generally rapid, allowing for several iterations of a product to be created in a short period.
What Are the Advantages of Injection Molding?
- Cost Efficiency:Injection molding is a unique method of producing large quantities of products with strict tolerances.
- Time Efficiency: Compared to more conventional manufacturing techniques like handcrafting or machining, injection molding is a faster process.
- Design Flexibility: The process can create parts with intricate detailing and complex geometry.
- Durability: Injection-molded components are sturdy and extremely durable, making them ideal for goods that must endure wear and tear.
- Repeatability: The parts made via injection molding are always accurate and of high quality. The technique is highly repeatable, even over extended manufacturing runs.
What Are the Best Applications for Injection Molding?
- Automotive components: Injection molding is frequently used to make parts including dashboards, doors, panels, and instrument panels.
- Home appliances:Injection molded plastics are used in the construction of many household appliances, including toasters, refrigerators, and dishwashers.
- Electronics: Electronic parts such as connectors, buttons, and protective housings are all produced using injection molded plastic.
- Medical equipment: Medical equipment items such as syringes, catheters, and IV drip bags are made via injection molding.
FAQs About Injection Molding Service
The easiest way to get an online quote for a custom injection molding part is to send your requirement and let our sales department contact you.
Generally, two major factors determine the manufacturing time of an injection molding part: the complexity of the part design and available tooling.
Normally, the price for customized injection molding parts varies according to order size and design.
Injection molding is used across a wide range of industries including aerospace, medical devices, consumer goods, energy, electronics, automotive, robotics, toys, and more.
Our plastic injection mold making includes 6 steps:
#1 Get a quote from Want.net
#2 Our technical support will analyse your file and send you a free DfM report.
#3 We will produce a sample for your approval
#4 Production will be started once you approve the sample
#5 After the project is completed, we will stock your mold for your next job
Generally, the tolerance can be as low as +/- 0.003 in. (0.08mm), with a resin tolerance that can be greater than but no less than +/- 0.002 in./in. (0.002mm/mm).
It takes about 35 days for mold design and making. And extra 3 to 5 days for molded parts production.
Put your injection molded parts into production today!
You’re one-step away from the most affordable injection molding service. Fill the form beside and we will get back to you within 24 hours.
GET QUICK QUOTE
- All uploads are secure and confidential