The CNC Machining Academy
Have you ever wondered how the parts of your car or the components of your phone are made with such precision? The answer lies in CNC machining, one of the most important technologies in the manufacturing industry today.
Overview
CNC machining is a technology that uses computer-controlled machines to create parts with extreme precision. These machines can cut, drill, and shape materials like metal, plastic, and wood into complex shapes and designs with incredible accuracy. The result is a finished product that is reliable, consistent, and meets exact specifications.
One of the key advantages of CNC machining is its speed and efficiency. Unlike manual machining, which requires skilled operators to guide the cutting tools, CNC machines are fully automated and can work 24/7 without interruption. This means that parts can be produced faster and at a lower cost, which is crucial in today’s competitive manufacturing landscape.
Another advantage of CNC machining is its accuracy and repeatability. Because the machines are controlled by computer programs, they can produce identical parts with incredible precision, down to thousandths of an inch. This level of consistency is essential in industries like aerospace and medical device manufacturing, where even small variations can have serious consequences.
CNC machining is a critical technology that has revolutionized the manufacturing industry. Its speed, precision, and versatility make it an indispensable tool for creating high-quality, reliable products that meet exact specifications. Whether you realize it or not, CNC machining is all around us, playing a vital role in the products we use every day.
Recommended Read:
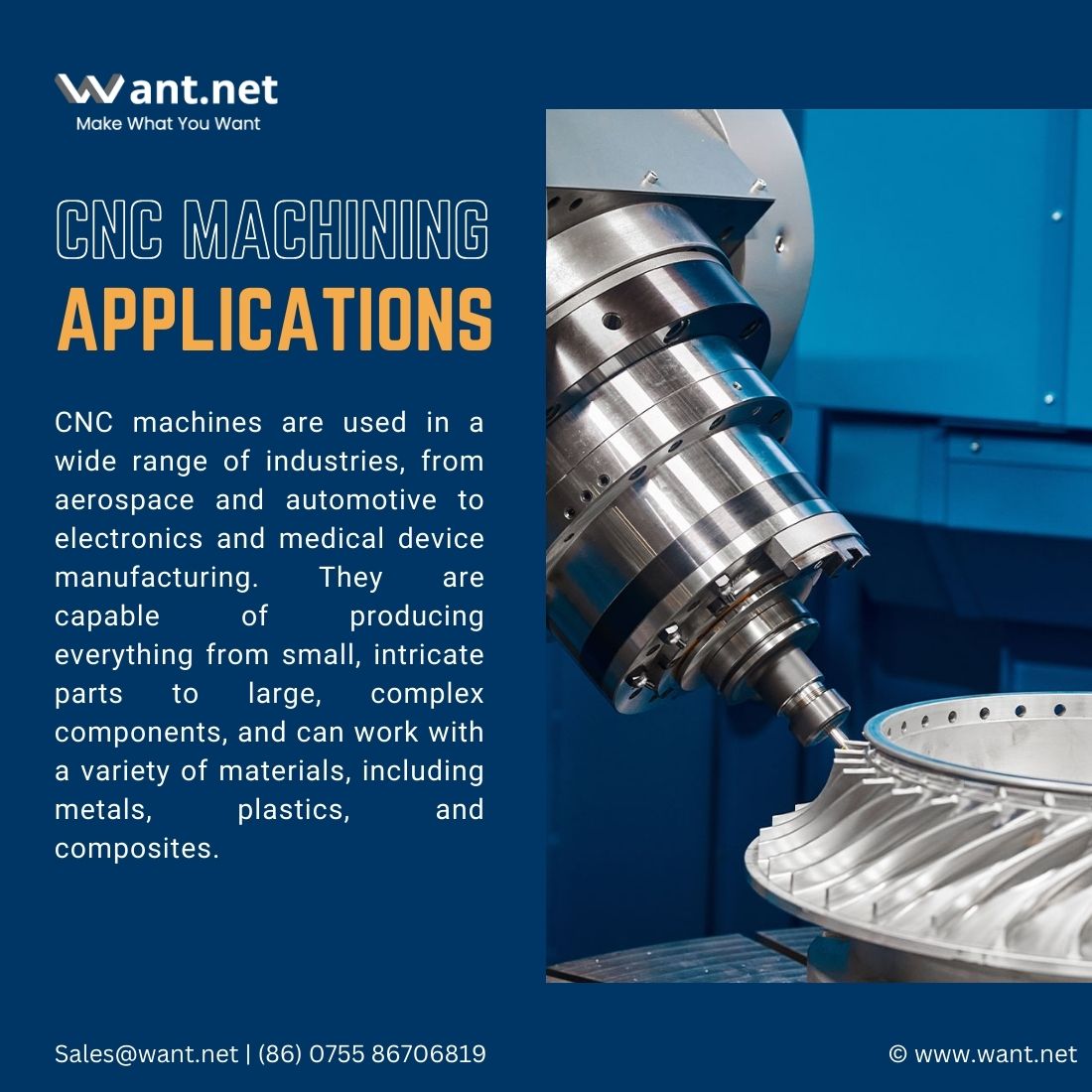
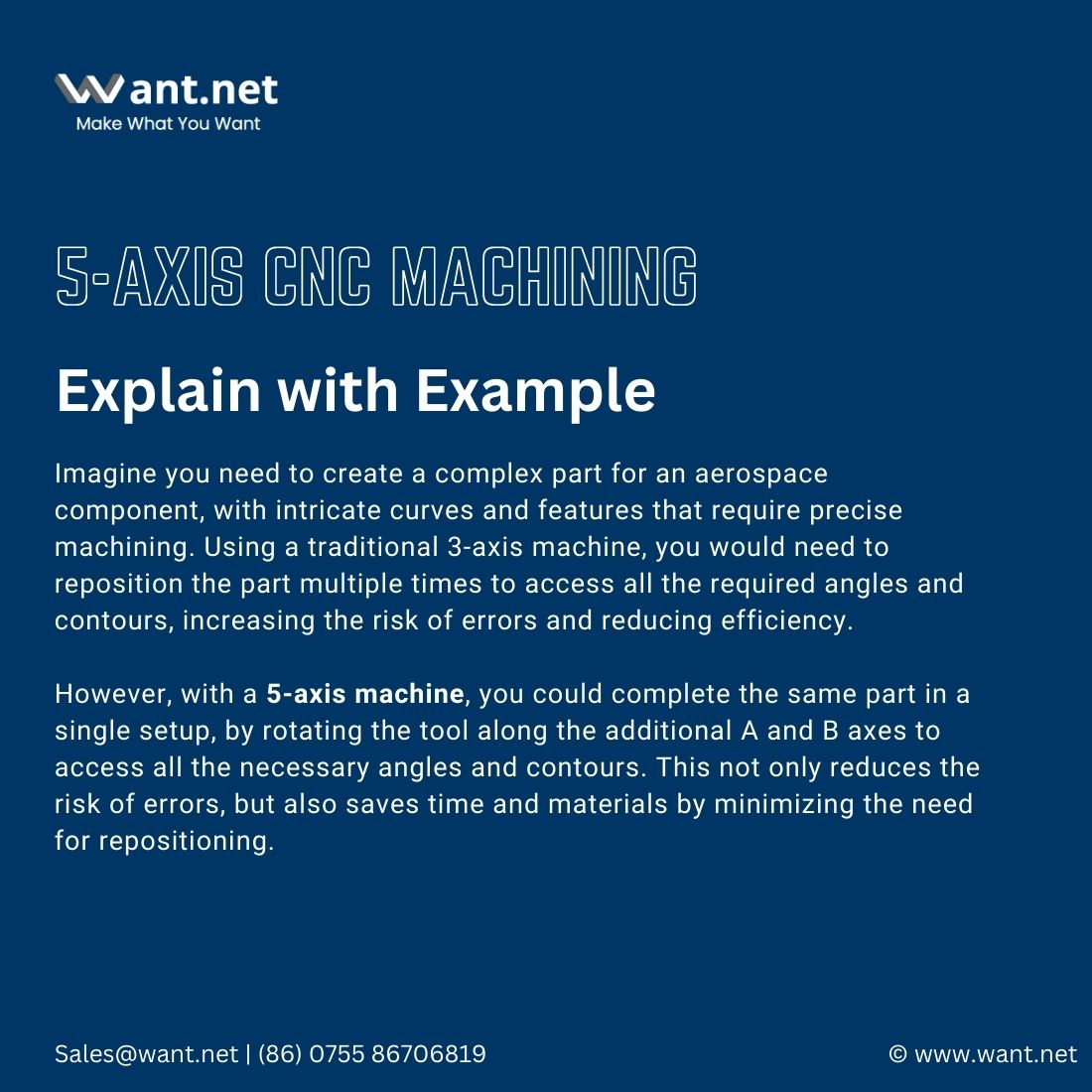
CNC PROCESS
CNC machining is a process in which computer-controlled machines are used to cut and shape materials into precise, complex parts. There are several types of CNC machining processes, including milling and turning.
Milling is a process in which a cutting tool rotates and removes material from a workpiece. The tool can move along multiple axes, allowing it to create complex shapes and features. Milling is commonly used to create parts with flat or curved surfaces, slots, and holes.
Turning, on the other hand, involves rotating a workpiece while a cutting tool removes material from its surface. The tool moves along a single axis, creating cylindrical shapes like shafts and pipes. Turning is commonly used to create parts with round shapes and features like threads and grooves.
In addition to milling and turning, there is also 5 axis machining. This process involves a machine with the ability to move along five axes, allowing it to create parts with even more complex shapes and features. 5 axis machining is particularly useful for creating parts with curved surfaces, as the machine can rotate and tilt the tool to reach every angle.
Recommended Read:
CNC Design
Before a part can be manufactured with CNC machining, it must first be designed using computer-aided design (CAD) software. CAD software allows designers to create 3D models of parts that can be used to generate the toolpaths and G-code needed to control the CNC machine.
When designing parts for CNC machining, there are several factors that designers should consider to ensure that the part can be manufactured accurately and efficiently. One important consideration is material selection. Different materials have different properties and respond differently to machining, so it’s important to choose a material that is suitable for the part’s intended use and can be machined effectively.
Another consideration is the part’s geometry. Complex shapes and features can be difficult and time-consuming to machine, so designers should aim to create parts that can be manufactured as efficiently as possible. This may involve simplifying the part’s design, reducing the number of features, or using alternative manufacturing processes for certain parts of the design.
Tolerances are also an important consideration in CNC design. Tolerances are the allowable variations in dimensions and other properties of the part, and they can have a significant impact on the part’s performance and cost. Designers should aim to specify tolerances that are appropriate for the part’s intended use and can be achieved with the available manufacturing processes.
Finally, designers should consider the manufacturability of the part. This means designing the part in a way that makes it easy to machine and minimizes the risk of errors or defects. This may involve avoiding sharp corners or tight radii, designing features that can be machined from multiple angles, and ensuring that the part can be securely held in place during machining.
Recommended Read:
Materials
CNC machining can be used to manufacture parts from a wide range of materials, including metals, plastics, and composites. The choice of material can have a significant impact on the part’s performance, cost, and manufacturability, so it’s important to carefully consider the options.
When selecting a material for CNC machining, there are several factors to consider. These include:
- Mechanical properties: the material’s strength, stiffness, and other mechanical properties should be appropriate for the part’s intended use
- Chemical properties: the material’s resistance to corrosion, heat, and other chemicals should be considered if it will be exposed to harsh environments
- Cost: the cost of the material can have a significant impact on the overall cost of the part, so it’s important to choose a material that is both suitable for the application and affordable
- Machinability: some materials are more difficult to machine than others, so the machinability of the material should be considered when selecting a material for CNC machining
The machinability of different materials can vary widely, depending on factors such as their hardness, ductility, and thermal conductivity. Materials that are easy to machine typically have low hardness and high ductility, while harder, more brittle materials can be more difficult to machine. In addition, materials with high thermal conductivity can be challenging to machine due to the heat generated during machining.
Common Materials Used in CNC Machining
- Aluminum: a lightweight and corrosion-resistant material that is easy to machine
- Stainless steel: a strong and durable material that is resistant to corrosion and heat
- Brass: a relatively soft material that is easy to machine and has good electrical conductivity
- Copper: a highly conductive material that is often used for electrical components
- Bronze: a copper alloy that is hard and corrosion-resistant with a golden-brown hue.
- Steel: a versatile and strong alloy consisting of iron and carbon that can be hardened or softened depending on its composition.
- Titanium: a lightweight and strong metal with high corrosion resistance and biocompatibility, commonly used in aerospace and medical industries.
- Zinc: a bluish-white metal that is malleable, ductile, and corrosion-resistant, often used for galvanizing steel or as an alloy in brass.
- ABS: a tough, impact-resistant thermoplastic that is commonly used for 3D printing and injection molding applications.
- Acetal: a low-friction, wear-resistant thermoplastic that is often used in gears, bearings, and other mechanical parts.
- Acrylic: a transparent thermoplastic that is lightweight and has high impact resistance, commonly used for windows, signs, and lighting applications.
- Garolite G-10: a composite material made of layers of fiberglass cloth and epoxy resin, known for its high strength and electrical insulation properties.
- HDPE: a strong, rigid thermoplastic with excellent chemical resistance, commonly used for bottles, pipes, and other applications where durability is important.
- Nylon: a strong, lightweight thermoplastic with excellent wear resistance and low friction properties, commonly used in automotive and industrial applications.
- PC: a clear, impact-resistant thermoplastic that is commonly used for safety glasses, riot shields, and other applications requiring high toughness.
Want to know more about plastic machining? Check out this article.
Surface Finishes
Surface finishes are an essential aspect of CNC machining that can have a significant impact on the final product’s appearance, functionality, and performance. In CNC machining, surface finish refers to the texture, roughness, and overall quality of the surface of a machined part.
The importance of surface finishes in CNC machining cannot be overstated. Surface finishes can affect the part’s friction, wear resistance, and ability to withstand corrosion. A high-quality surface finish can also improve the part’s aesthetic appeal and reduce the risk of defects such as cracks, burrs, and rough edges.
There are several common types of surface finishes that are commonly used in CNC machining, including:
1. Smooth
a smooth surface finish is free of any visible bumps, scratches, or other imperfections. This type of finish is ideal for parts that will be exposed to a lot of friction or require a high level of precision.
2. Matte
A matte surface finish has a slightly rough texture that can help to reduce glare and improve grip. This type of finish is often used for parts that will be handled frequently or for aesthetic purposes.
3. Polished
A polished surface finish has a highly reflective, mirror-like appearance that can enhance the part’s aesthetic appeal. This type of finish is often used for parts that will be on display, such as jewelry or decorative items.
4. Textured
A textured surface finish has a deliberately rough texture that can help to improve the part’s grip or create a specific aesthetic effect. This type of finish is often used for parts that will be used in industrial or outdoor settings.
Achieving the desired surface finish in CNC machining requires careful planning and execution. Techniques such as sanding, polishing, and blasting can be used to achieve specific textures and finishes. CNC machines can also be programmed to create precise surface finishes by adjusting the speed, pressure, and other parameters of the cutting tool.
Advance Tips
- 5 Innovative Applications of CNC Machining
- Streamline Your CNC Machining Workflow: Tips and Techniques
- The Advantages of CNC Machining for Precision Prototyping
- Avoiding 5 Common Mistakes in CNC Machining
- Industry 4.0 and CNC Machining: Revolutionizing Manufacturing
- The Vital Role of CNC Machining in Aerospace Industry
- CNC Machining vs. 3D Printing: Which is Better?
- Troubleshooting Common CNC Machining Problems
- Understanding CNC Machining vs. Traditional Methods
- The Future of CNC Machining: Trends and Insights
- The Future of CNC Machining: Automation and Robotics
- 7 Effective Strategies to Reduce CNC Machining Costs