CNC lathes have revolutionized the manufacturing industry with their precision, efficiency, and remarkable capabilities. These machines are true marvels when it comes to crafting rotationally symmetric parts, such as cylindrical shapes, tubes, and shafts. In contrast to CNC mills, CNC lathes possess a unique set of features that make them indispensable in certain applications. In this article, we are going to discuss the main features of CNC lathes. With this comprehensive guide, you will gain a deeper understanding of their contribution to shaping the industry of custom machined parts manufacturing.
What is a CNC Lathe and How Does it Works?
CNC lathe is a machining tool that utilizes computer programming and automation to shape various materials, such as metal or plastic, with incredible accuracy. Unlike traditional lathes that require manual operation, CNC lathes are driven by computerized instructions, allowing for precise and repeatable operations.
The working principle of a CNC lathe revolves around the concept of rotational machining. The machine securely holds the workpiece in place while a cutting tool, controlled by the computer program, moves along the material, removing excess material and creating the desired shape. This process enables the production of rotationally symmetric parts, including cylindrical shapes, tubes, and shafts.
Main Features of CNC Lathes
Now it’s time to explore the fascinating features that set CNC lathes apart from other machining tools. These features not only showcase the versatility and precision of CNC lathes but also highlight their unique capabilities that make them indispensable in various industries.
#1 Rotational Symmetry
Rotational symmetry is a key feature that distinguishes CNC lathes from other machining tools, particularly CNC mills. In CNC lathes, rotational symmetry refers to the ability to machine parts that possess a high degree of symmetry around a central axis. This means that the shape of the part remains unchanged when rotated around its axis.
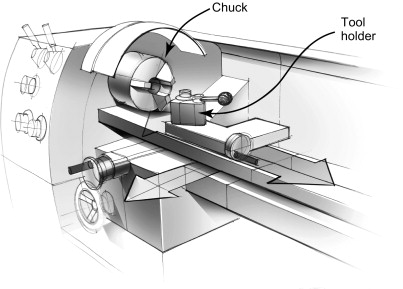
CNC lathes excel at machining rotationally symmetric parts, such as cylindrical shapes, tubes, and shafts. The rotational capability of the lathe allows for precise and consistent machining along the entire length of the part. This symmetry is achieved by rotating the workpiece while the cutting tool removes material, ensuring uniformity and accuracy throughout the machining process.
The applications for rotational symmetry in CNC lathes are vast, with numerous parts benefiting from this capability. Some common examples include:
- Shafts
- Rods
- Pipes
- Rotors and impellers
- Bearings and bushings
- Threaded parts
Rotational symmetry is a defining feature of CNC lathes, allowing for precise machining of rotationally symmetric parts. This capability provides numerous advantages over CNC mills.
#2 Turning Operations
Turning operations form a vital aspect of CNC lathe functionality, offering a wide range of machining possibilities. In turning operations, the lathe removes material from the workpiece to create rotational symmetry and achieve desired shapes and dimensions. CNC lathes are specifically designed to excel in these operations, providing precision and versatility.
When it comes to turning operations, CNC lathes offer a level of versatility that sets them apart from CNC mills. While CNC mills primarily excel in linear and vertical movements, CNC lathes leverage rotational capabilities for enhanced functionality. Here’s a comparison of the two:
- CNC lathes can perform a broad range of turning operations, including contouring, taper turning, chamfering, threading, parting off, and grooving. CNC mills, on the other hand, are more limited in their turning capabilities, with contouring and chamfering being challenging to achieve.
- CNC lathes hold the workpiece in a rotating spindle, allowing for continuous machining and the ability to work on both ends of the part. This setup enables the creation of symmetrical and complex features without the need for repositioning. CNC mills, by contrast, typically hold the workpiece stationary, limiting their ability to efficiently handle rotational symmetry.
- CNC lathes offer specialized tooling options for turning operations, allowing for greater flexibility in achieving desired shapes and dimensions. CNC mills rely on different cutting tools and techniques, primarily suited for linear and vertical movements.
#3 Thread Cutting
CNC lathes are renowned for their thread cutting capabilities, CNC mills rely on alternative techniques known as thread milling to achieve similar results. Thread milling involves using specialized cutting tools to create threads in a milling operation.
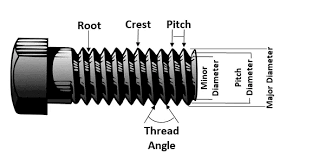
However, it’s important to note the distinctions between thread cutting on CNC lathes and thread milling on CNC mills:
- CNC lathes cut threads by removing material in a rotational manner, following a predefined path along the workpiece. In contrast, thread milling on CNC mills involves moving the milling tool in a linear or helical path to gradually create the thread profile.
- CNC lathes offer greater flexibility when it comes to thread cutting, allowing for the production of various thread profiles, such as metric, unified, or custom threads. Thread milling on CNC mills, while versatile, may have limitations in producing specific thread profiles due to the nature of the milling process.
- CNC lathes often outperform CNC mills in thread cutting. The rotational nature of the lathe spindle enables continuous cutting, resulting in faster thread production and reduced cycle times compared to thread milling on CNC mills.
#4 Live Tooling
Live tooling refers to the capability of the lathe to perform additional operations beyond traditional turning while the workpiece remains in rotation. This integration of live tooling expands the range of possibilities and enhances the overall versatility of CNC lathes.
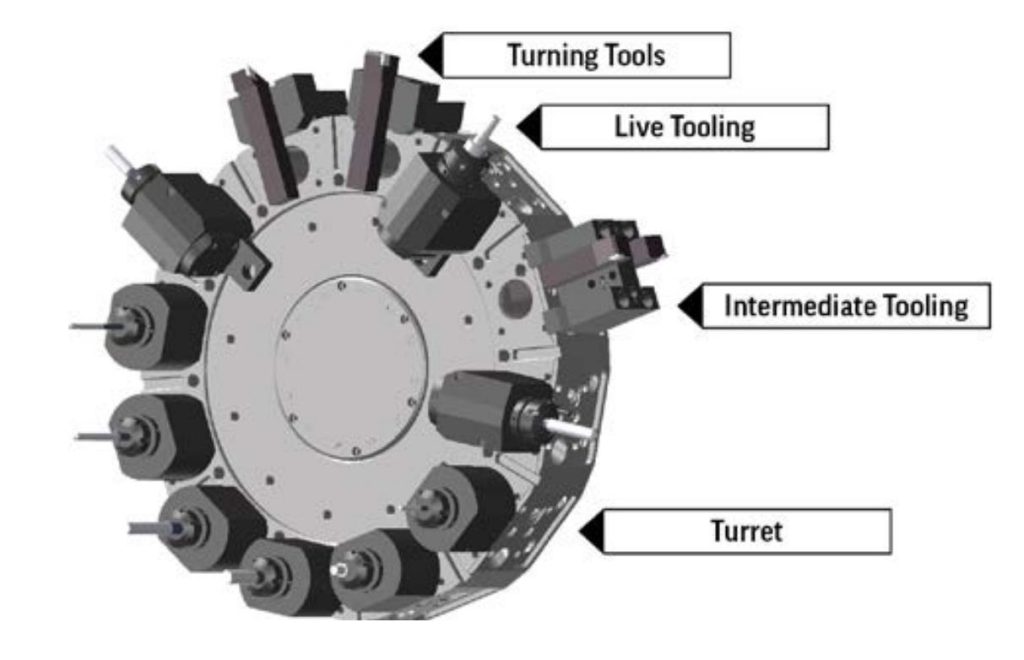
The introduction of live tooling opens up a myriad of possibilities for performing secondary operations directly on the rotating workpiece. Some common examples of additional operations facilitated by live tooling include:
- Drilling
- Milling
- Tapping
The presence of live tooling in CNC lathes not only streamlines the manufacturing process but also allows for greater flexibility and faster production. By eliminating the need for workpiece transfers or tool changes, CNC lathes with live tooling enable seamless integration of multiple operations, reducing setup times, and maximizing productivity.
#5 Single-Setup Machining
One of the remarkable advantages of CNC lathes is their ability to machine complex parts in a single setup. This capability stems from the rotational nature of the lathe, which allows for efficient and precise machining of various features without the need for multiple setups.
By utilizing the rotational capability of CNC lathes, complex parts can be machined with greater ease and accuracy. The workpiece can be continuously rotated, enabling access to different angles and surfaces for machining operations. This eliminates the need to reposition or readjust the workpiece, reducing the potential for errors and increasing overall efficiency.
In contrast to CNC lathes, CNC mills often require multiple setups to machine complex parts. Each setup involves repositioning the workpiece and adjusting the milling tools to access different areas of the part. This process can be time-consuming and introduces the potential for misalignment or inaccuracies.
Multiple setups not only increase the setup time but also introduce cumulative errors that may affect the final part’s quality. In contrast, CNC lathes with their rotational capability offer a streamlined approach to machining complex parts, minimizing setup times and ensuring consistent accuracy throughout the process.
The single-setup machining capability of CNC lathes is a significant advantage in industries that demand efficiency, precision, and reduced production times. It allows for the manufacturing of intricate and sophisticated parts with minimal disruptions, leading to higher productivity and improved overall quality.
#6 Bar Feeding
The bar feeder is designed to securely hold the bar stock and feed it into the lathe as the previous piece is being machined. This seamless integration ensures a smooth and uninterrupted workflow, maximizing productivity and reducing downtime.
Bar feeders enhance efficiency by minimizing setup times. The automatic feeding mechanism ensures a constant supply of material, reducing the time spent on material handling and allowing operators to focus on other critical aspects of the machining process.
CNC mills often face limitations when it comes to bar feeding. CNC mills typically operate using individual workpieces or stock material in the form of sheets or blocks, rather than long bars. This restricts their ability to handle continuous production of long, slender parts efficiently.
While some CNC mills may incorporate bar feeders for specific applications, their design and functionality are primarily optimized for different machining processes. As a result, the seamless integration and automated bar feeding capabilities found in CNC lathes are not inherent in CNC mills.
#7 Specialized Geometry
CNC lathes possess the capability to handle a wide range of specialized geometries, making them invaluable in various industries. These geometries include convex shapes, concave shapes, spherical forms, and intricate contours that require precise machining.
Convex shapes are characterized by outward curvatures and find applications in industries such as aerospace and automotive, where aerodynamics and fluid dynamics play a critical role. CNC lathes can accurately machine convex profiles, ensuring optimal performance and functionality of the components.
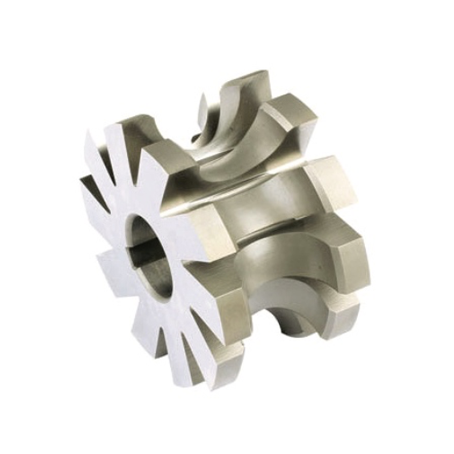
To provide a clearer picture, consider some examples of components that benefit from the specialized geometry capabilities of CNC lathes:
- Convex Shapes: Aircraft wing sections, automobile intake manifolds, and turbine blades.
- Concave Shapes: Surgical instruments, optical reflectors, and die-casting molds.
- Spherical Forms: Precision ball bearings, telescope lenses, and satellite dish components.
- Intricate Contours: Custom jewelry pieces, decorative handles, and ornamental moldings.
CNC mills primarily excel at 2D and 3D milling operations, where the cutting tool moves along X, Y, and Z axes. The absence of continuous rotational motion limits their ability to efficiently machine rotational symmetrical parts and intricate contours. In complex geometries like convex and concave shapes or spherical forms, CNC mills may encounter difficulties in achieving the required level of accuracy, surface finish, and dimensional precision. The absence of dedicated turning operations, which CNC lathes offer, hinders their performance in these areas.
#8 Parting and Grooving
CNC lathes offer dedicated tools and techniques for parting off workpieces, ensuring clean and accurate cuts. The workpiece is securely held in place and rotated while the cutting tool moves radially to remove material, resulting in a clean separation. This capability is particularly beneficial for applications where components need to be separated from a larger stock or when precise lengths are required.

The precision control offered by CNC lathes in parting and grooving operations ensures consistent and accurate results. Depth control allows for the creation of grooves with specific dimensions, ensuring a proper fit for mating components or accommodating specific features like O-rings or retaining rings. Width control enables the machining of grooves with precise tolerances, ensuring the component’s functionality and structural integrity.
CNC lathes employ various cutting tools, such as parting tools, grooving tools, and form tools, each designed to handle specific parting and grooving requirements. These tools, combined with the programmability and accuracy of CNC lathes, enable manufacturers to achieve tight tolerances, smooth surface finishes, and repeatable results.
On the other hand, CNC mills face certain limitations when it comes to parting and grooving operations. CNC mills primarily operate with rotary cutting tools that move along multiple axes to remove material. While they can perform slotting and pocketing operations, parting off workpieces and creating grooves require specific tooling and rotational movement, which are not inherent in CNC mills.
#9 High-Speed Machining
Another notable features of CNC lathes is their ability to achieve high spindle speeds. The spindle refers to the rotating component of the lathe that holds the workpiece and drives the cutting tool. CNC lathes are equipped with powerful motors and advanced control systems that allow them to reach and maintain high rotational speeds.
High-speed machining offers several advantages in terms of efficient material removal. When CNC lathes operate at high spindle speeds, the cutting tools engage with the workpiece at a faster rate, resulting in reduced cutting times. This increased speed leads to improved productivity and shorter machining cycles.
Furthermore, high-speed machining enables the use of smaller cutting tools with higher cutting velocities. Smaller tools can access tighter spaces and intricate features, allowing for greater precision in the machining process. The higher cutting velocities contribute to enhanced surface finishes and reduced tool wear, leading to improved overall part quality and longer tool life.
#10 Rapid Prototyping
Rapid prototyping involves quickly creating functional prototypes to validate and iterate on a product design before mass production. CNC lathes offer unique advantages that make them ideal for this purpose.
One of the key advantages of using CNC lathes for rapid prototyping is the ability to quickly iterate and make adjustments in the design process. Traditional prototyping methods often involve time-consuming manual processes or the need to create custom tooling. In contrast, CNC lathes offer a more streamlined approach.
With CNC lathes, designers can make changes to the digital design file and rapidly produce updated prototypes. The ability to automate the machining process allows for consistent and repeatable results, reducing the chances of errors or variations between iterations. This iterative approach enables designers to evaluate the functionality, fit, and aesthetics of the prototypes, identify potential design flaws or improvements, and make necessary adjustments in a timely manner.
By leveraging CNC lathes for rapid prototyping, designers and manufacturers can significantly reduce the time and cost associated with traditional prototyping methods. The ability to quickly iterate and refine designs allows for faster development cycles, leading to accelerated product development and a competitive edge in the market.
Conclusion
CNC lathes, with their remarkable capabilities and versatile features, are truly fascinating machines that have revolutionized the manufacturing industry. The unique capabilities of CNC lathes open up a world of possibilities for manufacturers, engineers, and designers. The ability to precisely machine rotationally symmetric parts, create intricate contours, handle specialized geometries, and achieve high spindle speeds provides a level of precision and efficiency that is unparalleled.
Embrace the possibilities offered by CNC lathes, stay up to date with the latest advancements in technology, and continue exploring the vast potential they hold. The world of CNC lathes is evolving rapidly, and there is much more to discover and leverage. So, step into the world of CNC lathes and discover more article here.
Related Posts
- Differences Between CNC Lathes and CNC Mills
In the world of manufacturing, two machines play pivotal roles: CNC lathes and CNC mills. These machines share the purpose of material removal using cutting tools, yet they possess unique…
- Precision CNC Machining of Steel: High-Volume Production
Precision CNC Machining and High-Volume Production As an integral part of modern manufacturing processes, Precision Computer Numerical Control (CNC) machining brings about unmatched accuracy and consistency in the production of…
- Material Versatility in CNC Machining: From Titanium to Thermoplastics
Introduction to CNC Machining CNC machining stands as a cornerstone in the manufacturing sector, enabling the precise creation of parts and components. This process utilizes computer numerical control (CNC) to…