Introduction to Tool Chatter in CNC Machining of Aluminum
Tool chatter in CNC machining significantly undermines the quality and precision of machined aluminum parts. This phenomenon, characterized by oscillations and vibrations, arises due to the interaction between the cutting tool and the workpiece. Aluminum, with its relatively low modulus of elasticity and high ductility, is particularly susceptible to these issues.
China Online CNC Machining Service
Tool chatter not only affects the surface finish but also leads to increased tool wear and reduced dimensional accuracy. Furthermore, the operational costs increase due to reduced tool life and the potential for scrapped parts, making it crucial for manufacturers to understand and address this issue effectively.
What Causes Tool Chatter in Aluminum CNC Operations?
Tool chatter is influenced by several factors in the context of aluminum machining:
- Tool and Material Interaction: Aluminum’s properties, such as its softness and stickiness, can cause material adhesion on the cutting tool, exacerbating chatter. This interaction leads to irregular tool paths and vibrations.
- Cutting Tool Design: The choice of tool material, its coating, and sharpness play a significant role in how vibrations are initiated and amplified. Incorrect tool design can increase the likelihood of chatter.
- Machine Dynamics: Factors such as machine rigidity, spindle condition, and alignment critically impact whether vibrations are damped or amplified. Ensuring that the CNC machine is properly maintained and aligned can greatly reduce the occurrence of chatter.
- Cutting Parameters: Inappropriate cutting speeds, feeds, and depths of cut can also induce chatter.
Data Table: Impact of Cutting Parameters on Chatter
Cutting Speed (RPM) | Feed Rate (mm/rev) | Depth of Cut (mm) | Chatter Incidence (Measured as Vibration Amplitude) |
---|---|---|---|
1000 | 0.1 | 2 | High |
1500 | 0.1 | 2 | Medium |
2000 | 0.1 | 2 | Low |
1500 | 0.2 | 2 | High |
1500 | 0.05 | 2 | Medium |
1500 | 0.1 | 1 | Low |
This table illustrates how varying speeds, feeds, and depths affect the vibration amplitude, indicating the presence of chatter.
How Can Tool Geometry Influence Chatter in CNC Machining?
The geometry of the cutting tool is critical in influencing its performance and tendency to induce chatter. Adjusting features such as rake angle, helix angle, and flute count can significantly impact cutting forces and the stability of the tool during machining.
Critical Design Features:
- Rake Angle: A positive rake angle can help in reducing cutting resistance, thereby minimizing chatter.
- Helix Angle: A larger helix angle improves chip evacuation and reduces heat buildup, which in turn decreases chatter.
- Flute Count: Increasing the number of flutes distributes the cutting load and reduces deflection and vibration.
Diagram: Tool Geometry Modifications
Here is the technical diagram illustrating different cutting tool geometries for CNC machining. This diagram focuses on variations in rake angle, helix angle, and flute count, with labels and annotations explaining how changes in these features influence machining stability and reduce chatter. The diagram is presented in a professional technical drawing style for clarity.
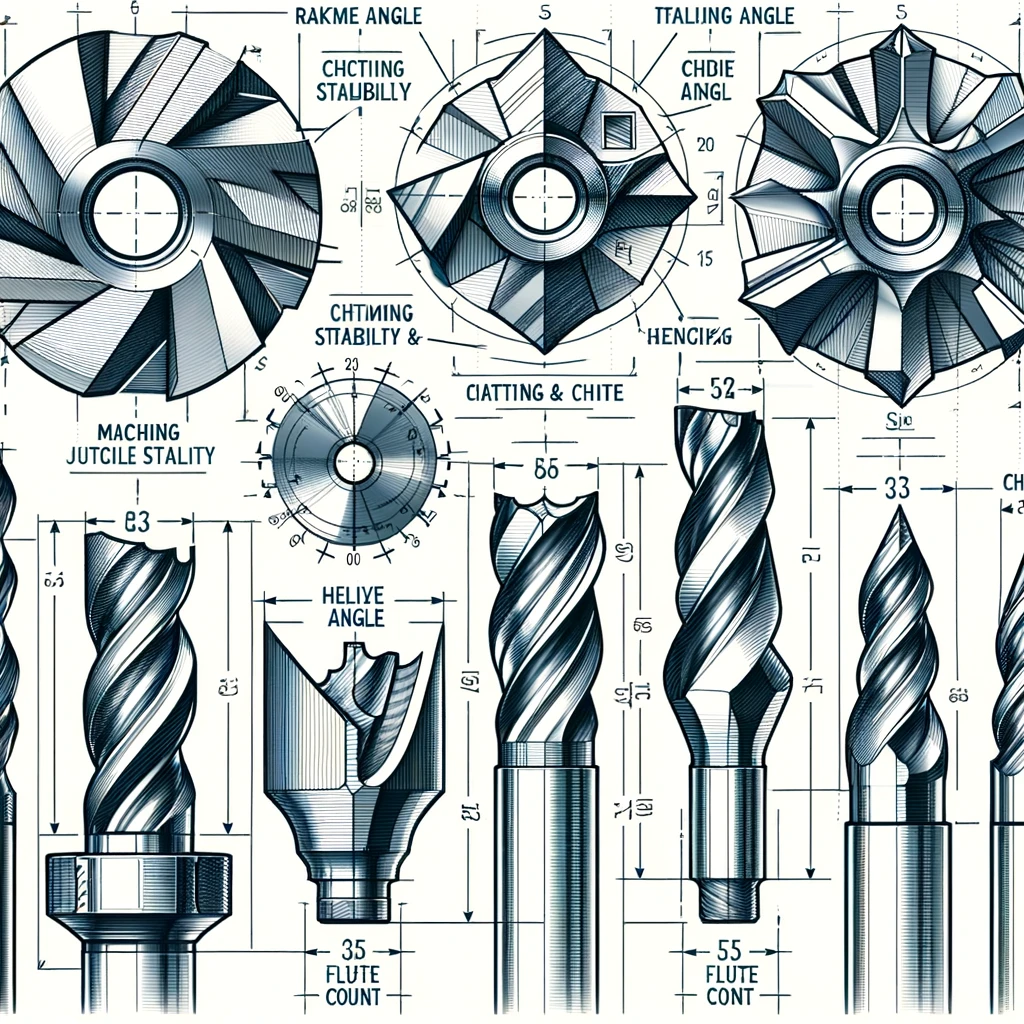
Case Study Table: Tool Geometry Modification Impact
Tool Feature Modified | Before Modification (Vibration) | After Modification (Vibration) |
---|---|---|
Rake Angle | High | Low |
Helix Angle | High | Moderate |
Flute Count | Moderate | Low |
This case study table shows how specific changes to tool geometry have effectively reduced vibration levels, thereby mitigating chatter in real machining scenarios.
Advanced Techniques to Suppress Chatter
To effectively suppress chatter, several advanced techniques can be employed, integrating innovative technologies designed to enhance tool stability and overall machining performance.
- Tuned Mass Dampers: These devices, attached to the tool or spindle, are designed to absorb and dissipate vibrations at specific frequencies known to cause chatter. By finely tuning these dampers to the dominant vibration frequencies of the machining process, they can significantly reduce the amplitude of these vibrations.
- Active Vibration Control Systems: These sophisticated systems utilize sensors to detect vibrations and then actively counteract them with controlled forces. This approach not only reduces the vibrations that lead to chatter but also adapts to changing machining conditions in real-time.
- Tool Holders with Damping Properties: Modern tool holders are designed with materials and geometrical features that inherently dampen vibrations. These holders provide a more stable interface between the machine and the tool, reducing the transmission of vibration energy.
Case Studies and Data Illustration:
- Example of Tuned Mass Damper Effectiveness: A CNC machine retrofitted with a tuned mass damper showed a 30% reduction in vibration levels, leading to a noticeable improvement in surface finish quality and tool life extension.
- Active Vibration Control Implementation: Implementation of an active vibration control system in a high-speed milling operation reduced chatter significantly, allowing for a 20% increase in feed rates without compromising surface quality.
Why Is Machine Setup Critical for Reducing Chatter?
Proper machine setup is fundamental in reducing the risk of chatter, especially when machining materials as challenging as aluminum. This section discusses the key aspects of machine setup that directly influence machining stability.
- Machine Alignment: Ensuring that the CNC machine’s spindle and axes are precisely aligned is crucial for smooth operation. Misalignment can lead to uneven cutting forces and exacerbate vibration issues.
- Fixture Stability: The stability of how the workpiece is secured significantly affects machining performance. Using advanced clamping systems and vibration-damping materials can help maintain a rigid setup, minimizing movement and vibrations.
- Regular Maintenance Checks: Routine checks and maintenance of the machine and its components prevent the deterioration of machine conditions that might contribute to increased chatter.
Table: Effects of Machine Setup Adjustments on Chatter Reduction
Adjustment Type | Chatter Reduction (%) | Additional Notes |
---|---|---|
Improved Alignment | 25% | Significant impact on precision. |
Enhanced Fixture | 30% | Increased stability during cuts. |
Maintenance Routine | 20% | Extended tool and machine life. |
This table illustrates the tangible benefits of various machine setup adjustments on reducing chatter in CNC machining operations.
Monitoring and Adjusting Processes in Real-Time
The ability to monitor and adjust machining processes in real-time is a powerful method for combating tool chatter. Utilizing modern sensor technology and data analytics can lead to substantial improvements in machining performance.
- Sensory Feedback Systems: By integrating sensors such as accelerometers and acoustic emission sensors, CNC machines can dynamically adjust parameters such as feed rate and spindle speed in response to detected chatter conditions.
- Data Analytics in Machining: Advanced analytics can predict when conditions are likely to lead to chatter, allowing preemptive adjustments to be made. This proactive approach uses historical data combined with real-time data to fine-tune machining operations.
- Automated Control Systems: Modern CNC machines equipped with sophisticated control systems can automatically make adjustments based on the input from sensors, ensuring optimal machining conditions are maintained continuously.
Graph: Impact of Real-Time Feedback on Machining Quality
Here’s the graph depicting the impact of real-time feedback on machining quality. This visualization shows the improvement in quality scores over several months, comparing conditions before and after the implementation of real-time feedback systems. As illustrated, the quality scores significantly improve following the introduction of dynamic adjustments based on sensor feedback.
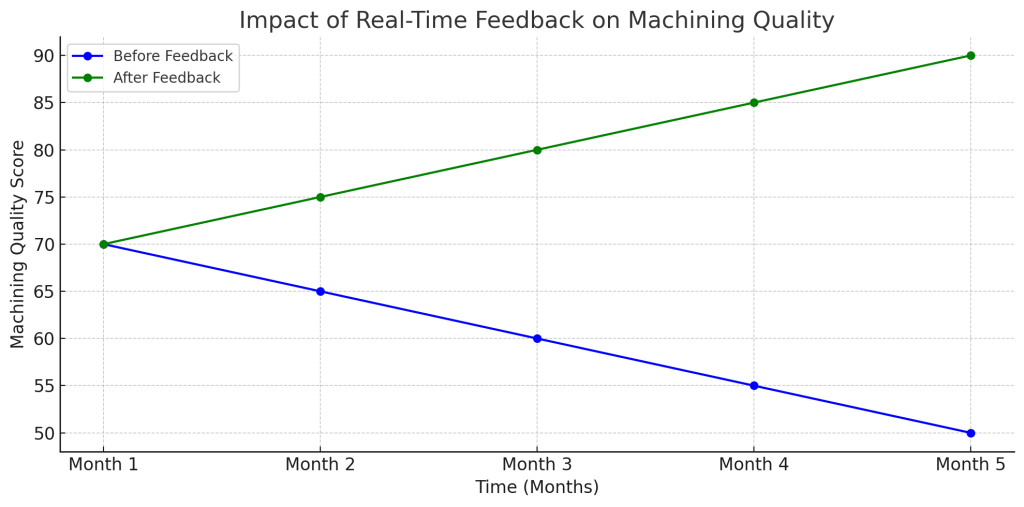
Related Posts
- Tool compensation in CNC machining, our quest for precision in CNC machining
Introduction to CNC Machining and Precision CNC (Computer Numerical Control) machining stands at the forefront of modern manufacturing, utilizing computerized controls to operate complex machinery with remarkable accuracy. This process…
- Elevating Precision Standards through Chamfer in CNC Machining
1. Introduction: The Pursuit of Unparalleled Precision In the realm of CNC machining, precision is paramount. This section introduces the article by exploring the significance of precision in manufacturing and…
- Precision Prowess: Unveiling the Advantages of China CNC Machining
1. Introduction: The Role of Precision in Manufacturing Excellence In this introductory section, we delve into the critical role that precision plays in manufacturing and set the stage for an…
- Revolutionizing CNC Machining for Complex Aerospace Assemblies
Introduction to CNC Machining in Aerospace Assemblies Computer Numerical Control (CNC) machining represents a significant technological development playing a notable role in the creation of complex aerospace assemblies. CNC machining…
- The Role of Prototype Machining in Accelerating Product Development
Introduction: The Importance and Definition of Prototype Machining Prototype machining is a critical element advancing product development. It involves the technique of manufacturing an early model or sample, known as…
- Maximizing Precision in CNC Machining: Techniques and Tips
Importance of Precision in CNC Machining Precision is an fundamental component in the field of Computer Numerical Control (CNC) machining. It entails producing parts that are not only accurate but…