What is Inventory Management in the Context of Brass CNC Machining Parts?
Inventory management in the brass CNC machining sector involves overseeing the flow of components from suppliers to the production floor and then to the customers. Effective management ensures that the right amount of raw materials and finished products are available at the right time, minimizing costs and maximizing production efficiency.
Key Components:
- Stock Control: Monitoring levels of raw brass and finished parts to prevent overstocking and understocking.
- Supplier Management: Coordinating with suppliers to ensure timely delivery of high-quality brass.
- Demand Forecasting: Predicting future demand for brass parts to adjust inventory levels proactively.
Why Is Accurate Demand Forecasting Critical for Inventory Management?
Accurate demand forecasting allows manufacturers to produce brass CNC machining parts efficiently, ensuring they meet market demand without overproducing.
Demand Forecasting Techniques:
- Historical Sales Analysis: Using past sales data to predict future trends.
- Market Analysis: Monitoring industry trends and economic conditions that influence demand.
Data Table: Impact of Demand Forecasting on Inventory Levels
Month | Predicted Demand | Actual Demand | Variance | Inventory Adjustment Needed | Production Adjustment |
---|---|---|---|---|---|
January | 1000 units | 1100 units | +10% | Increase order by 10% | Increase by 100 units |
February | 1200 units | 1150 units | -4% | Decrease order by 4% | Decrease by 50 units |
March | 900 units | 900 units | 0% | No adjustment needed | No change |
April | 850 units | 900 units | +6% | Increase order by 6% | Increase by 50 units |
May | 950 units | 1000 units | +5% | Increase order by 5% | Increase by 50 units |
June | 1100 units | 1050 units | -5% | Decrease order by 5% | Decrease by 50 units |
July | 1200 units | 1250 units | +4% | Increase order by 4% | Increase by 50 units |
August | 1300 units | 1350 units | +4% | Increase order by 4% | Increase by 50 units |
September | 800 units | 750 units | -6% | Decrease order by 6% | Decrease by 50 units |
October | 850 units | 900 units | +6% | Increase order by 6% | Increase by 50 units |
November | 950 units | 1000 units | +5% | Increase order by 5% | Increase by 50 units |
December | 1000 units | 950 units | -5% | Decrease order by 5% | Decrease by 50 units |
Case Study:
A manufacturer of brass fittings used advanced predictive analytics to refine their demand forecasting model, resulting in a 20% reduction in excess inventory and a 15% increase in customer satisfaction due to better product availability.
How Can Lean Manufacturing Principles Be Applied to Brass Parts Production?
Lean manufacturing principles can significantly enhance inventory management by reducing waste and increasing efficiency in the production of brass CNC machining parts.
Lean Techniques:
- Kanban Systems: Using visual signals to control the flow of materials.
- Continuous Improvement (Kaizen): Regularly seeking ways to improve processes and reduce waste.
Case Study:
A brass parts manufacturer implemented a Kanban system to manage inventory, resulting in a 30% decrease in the time components spent in inventory and a 25% reduction in material waste due to overproduction.
How Does Just-In-Time (JIT) Inventory Management Reduce Costs?
Just-In-Time (JIT) inventory management is a strategy that aligns raw material orders from suppliers directly with production schedules. It is highly effective in reducing inventory holding costs and increasing the efficiency of production operations.
Benefits of JIT:
- Reduced Storage Space: Less need for large storage areas as parts are used immediately in production.
- Minimized Waste: Reduction in the risk of stock becoming obsolete.
- Enhanced Cash Flow: Money is not tied up in excessive inventory; it can be used for other operational needs.
Graphical Representation:
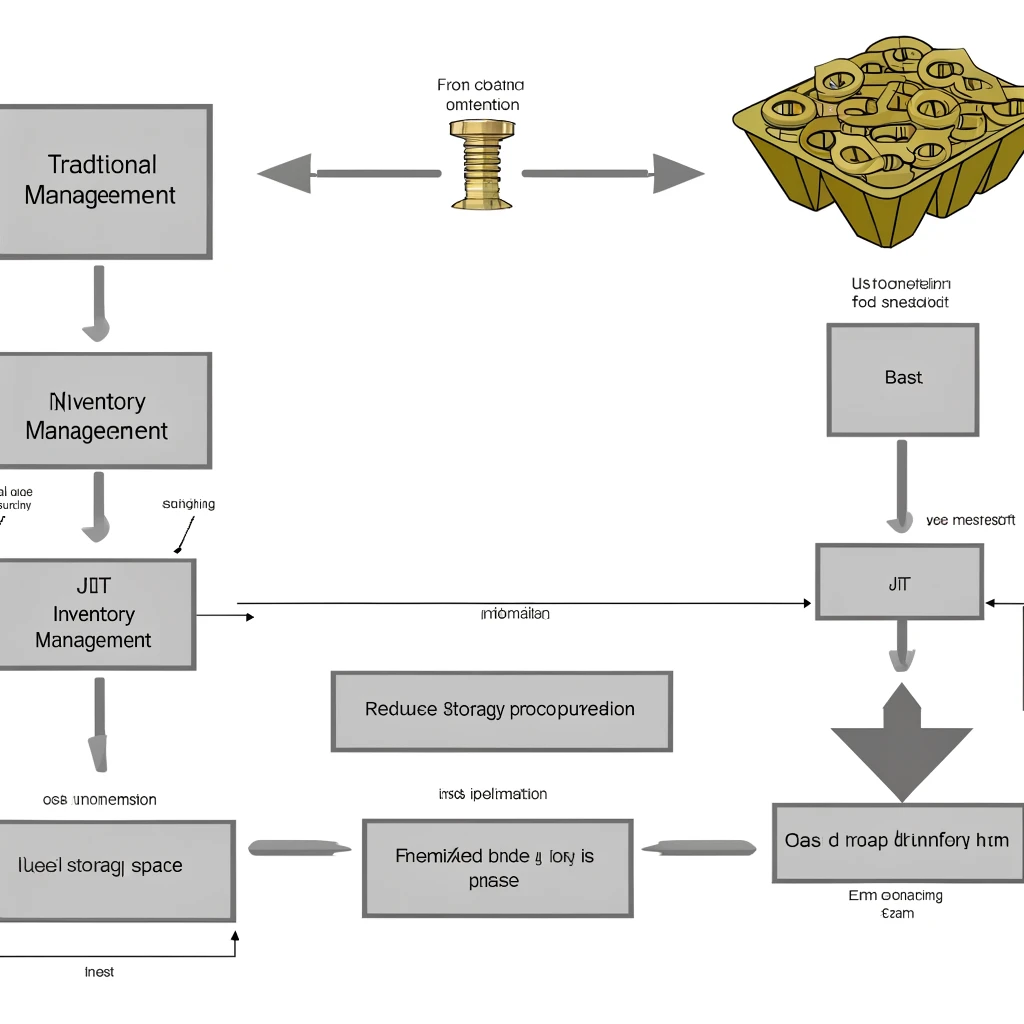
A before-and-after flowchart showing the production process with traditional inventory management vs. JIT implementation, highlighting how JIT streamlines operations and reduces delays.
What Are the Challenges of Implementing an Automated Inventory System?
Implementing an automated inventory system can streamline operations but comes with its own set of challenges. These can range from technical issues to resistance from staff and integration complexities with existing processes.
Key Challenges:
- Integration Complexity: Ensuring the new system integrates seamlessly with existing software and hardware.
- Upfront Costs: The initial investment in automated systems can be significant.
- Employee Training: Staff may require extensive training on the new systems, which can be time-consuming and expensive.
Case Study:
A brass valve manufacturer faced difficulties integrating an automated inventory system with their legacy production software. Despite initial setbacks, including a temporary decrease in production efficiency, the company ultimately enhanced its inventory accuracy by 40% after successful integration and training.
How Can Technology Improve Inventory Accuracy for Brass CNC Parts?
Technology plays a crucial role in enhancing the accuracy of inventory management. Advanced tools and software help in tracking, managing, and forecasting inventory needs more precisely.
Technological Tools:
- RFID Tags: Allow for real-time tracking of parts throughout the warehouse.
- Inventory Management Software: Provides tools for better forecasting and trend analysis.
- Automated Reordering Systems: Minimize human error and ensure orders are placed at the optimal time.
Data Table: Technological Impact on Inventory Accuracy
Technology | Before Implementation | After Implementation | Improvement |
---|---|---|---|
RFID Tracking | 80% accuracy | 98% accuracy | 18% |
Software Management | 75% accuracy | 95% accuracy | 20% |
Automated Reordering | 70% accuracy | 90% accuracy | 20% |
Example:
An electronics manufacturer that implemented RFID tagging for their brass components reduced misplacement and theft, significantly improving inventory accuracy and reducing unnecessary reorder costs.
What Case Studies Demonstrate Successful Inventory Management Strategies?
Examining real-world applications provides valuable insights into effective inventory management strategies. These case studies highlight successful practices and the measurable benefits achieved.
Case Studies:
- Automotive Supplier: Implemented a cloud-based inventory system that reduced cycle time by 25% and lowered inventory carrying costs by 30%.
- Aerospace Manufacturer: Introduced a vendor-managed inventory (VMI) system that decreased stock-outs by 45% and enhanced supplier relationships.
- Medical Devices Producer: Utilized IoT devices for inventory tracking, which reduced the time spent on inventory management by 50% and improved order accuracy by 35%.
Data Table: Summary of Case Studies
Company | Strategy Used | Results Achieved |
---|---|---|
Automotive Supplier | Cloud-Based System | 25% faster cycle time, 30% lower costs |
Aerospace Manufacturer | Vendor-Managed Inventory | 45% reduction in stock-outs |
Medical Devices Producer | IoT Tracking | 50% reduction in management time, 35% increase in accuracy |
Related Posts
- What Are the Latest Trends in Sourcing Brass CNC Machining Parts?
How Are Global Market Dynamics Shaping the Sourcing of Brass CNC Machining Parts? The global landscape for sourcing brass CNC machining parts is heavily influenced by international trade dynamics, including…
- CNC Machining Aluminum vs. Brass: A Detailed Comparison for Precision Parts Manufacturing
Introduction to CNC Machining and Material Choices CNC (Computer Numerical Control) machining is a critical process in precision parts manufacturing. Its importance lies in its ability to create intricate and…
- CNC Machining Aluminum vs. Brass: A Detailed Comparison for Precision Parts Manufacturing
CNC Machining: Aluminum vs. Brass in Precision Parts Manufacturing The continuous quest for efficiency and precision has made CNC (Computer Numerical Control) machining a vital process in the manufacturing of…
- How Do Import Regulations Affect the Procurement of Brass CNC Machining Parts?
What Are the Global Import Regulations for Brass CNC Machining Parts? The global landscape for importing brass CNC machining parts is complex and varies significantly by country. Key players such…
- What are the requirements for CNC machining of bearing parts?
Bearings are common and important parts in the automotive industry, which can support transmission components and transmit torque. Generally, CNC machining centers are used to process bearing parts. So what…
- Precision CNC Machining: Aluminum vs. Brass for Your Custom Parts
Introduction to Precision CNC Machining and Custom Parts Precision CNC (Computer Numeric Control) machining is a cutting-edge manufacturing process that utilizes computer-controlled machinery to produce intricately designed custom parts, adhering…