Introduction:
In modern engineering, the demand for materials that balance strength, lightweight design, and environmental resilience drives innovation. Nylon bolts, high-performance polyamide fasteners, are critical solutions for challenges where metals fall short, such as conductivity, corrosion, and weight. These precision-engineered nylon bolts drive advancements in aerospace, electronics, automotive, medical, and renewable energy sectors.
This guide equips engineers, designers, and purchasing managers with a comprehensive understanding of nylon bolts. It explores their material properties, diverse grades, industry-specific applications, and why CNC machining is the preferred method for crafting custom nylon bolts tailored to exacting requirements.
Understanding Nylon Bolts: Core Properties and Engineering Advantages
Nylon bolts are selected to address engineering challenges that metals cannot, offering unique properties that make them indispensable for specialized applications requiring insulation, durability, and lightweight performance.
Electrical Insulation
With high dielectric strength, nylon bolts excel as electrical insulators. In electronics, nylon bolts secure printed circuit boards (PCBs), control panels, and wire harnesses, preventing short circuits without additional insulating components. This streamlines assembly and reduces costs in telecommunications, consumer electronics, and data centers.
Corrosion and Chemical Resistance
Nylon bolts resist rust and corrosion, thriving in humid, wet, or chemically aggressive environments. They withstand oils, fuels, solvents, and salt solutions, making nylon bolts ideal for marine applications (with appropriate grades), automotive components exposed to road salts, and chemical processing plants. While sensitive to strong acids, nylon bolts outperform untreated metals in chemical resilience.
Lightweight Strength
At half the density of aluminum and significantly lighter than steel, nylon bolts offer substantial weight savings. In aerospace and automotive industries, nylon bolts enhance fuel efficiency in non-structural applications like interior panels, avionics housings, and battery enclosures without compromising strength.
Vibration and Noise Damping
The elasticity of nylon bolts absorbs shock and vibration, preventing loosening in dynamic environments like vehicles, industrial machinery, and wind turbines. This property, seen in nylon insert lock nuts, ensures reliable nylon bolts in high-vibration settings while reducing operational noise for quieter systems.
Thermal Stability and Limitations
Standard nylon bolts operate up to 85°C (185°F), suitable for most applications but not high-heat environments like engine blocks. Advanced grades and additives extend thermal performance, making nylon bolts versatile for diverse conditions.
A Data-Driven Comparison: Nylon Bolts vs. Metal
Nylon bolts offer distinct advantages over metal fasteners but come with limitations. Below is a detailed comparison of key performance metrics:
- Strength and Elasticity: Nylon bolts (e.g., Nylon 6/6) have a tensile strength of ~11,600 psi, compared to Grade 5 steel’s 120,000 psi. However, nylon bolts elongate up to 60% before failure, compared to 10-15% for metals, providing superior resilience under sudden shock loads. This makes nylon bolts ideal for applications like automotive suspensions or aerospace interiors where dynamic loads are common.
- Temperature Performance: Standard nylon bolts operate up to 85°C (185°F), far below metals like steel or titanium (up to 400°C+). Reinforced nylon bolts, such as glass-filled variants, can withstand up to 250°C, expanding their use in moderate high-temperature applications.
- Cost-Effectiveness: Nylon bolts are significantly cheaper, often costing half as much as stainless steel or titanium. Combined with faster installation and reduced tooling needs, nylon bolts can lower total installed costs by up to 30% in applications like electronics or lightweight assemblies.
- Weight: Nylon bolts have a density of ~1.1 g/cm³, compared to aluminum (2.7 g/cm³) and steel (7.8 g/cm³), offering substantial weight reduction. In aerospace, reducing 1 kg with nylon bolts can improve fuel efficiency, while in electric vehicles, it extends battery range.
- Corrosion Resistance: Nylon bolts are inherently rust-proof, excelling in humid or saline environments. Unlike untreated steel or aluminum, which corrode, or even stainless steel, which may pit in saltwater, nylon bolts (e.g., Nylon 12) remain unaffected, ensuring longevity in marine or chemical settings.
- Electrical Conductivity and Insulation: The non-conductive nature of nylon bolts prevents galvanic corrosion in mixed-metal assemblies, extending component lifespan in applications like aircraft frames or battery systems. This eliminates the need for insulating washers, simplifying design and reducing costs.
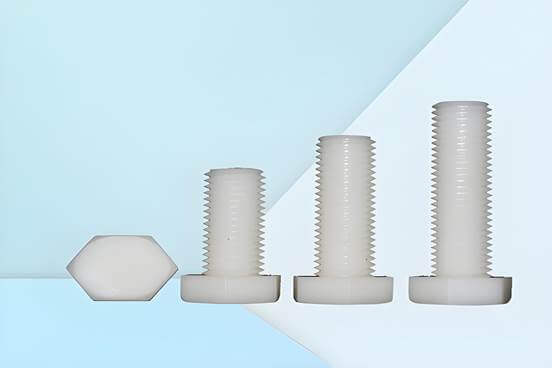
Addressing Material Limitations
Nylon bolts face challenges with moisture absorption and UV sensitivity, but these can be effectively managed through material selection and process optimization.
- Moisture Absorption: Nylon bolts absorb water, potentially causing dimensional swelling or changes in mechanical properties. For example, Nylon 6 has a 24-hour water absorption rate of ~2.7%. Low-absorption grades like Nylon 12 (0.2%) or pre-drying treatments ensure nylon bolts maintain stability in humid environments, such as marine or outdoor applications. Controlled swelling can even enhance fit, preventing loosening in certain designs.
- UV Sensitivity: Prolonged UV exposure can degrade standard nylon bolts, affecting strength and appearance. Adding UV stabilizers or selecting UV-resistant grades like Nylon 12 makes nylon bolts suitable for outdoor use, such as solar panel mounts or construction equipment.
- Fatigue Performance: Nylon bolts have lower fatigue strength than metals, risking failure under prolonged cyclic loads. Glass-filled or carbon-filled nylon bolts significantly improve fatigue resistance, making them viable for high-stress applications like robotics or heavy machinery.
- Post-Machining Stability: To ensure nylon bolts maintain precise dimensions after machining, pre-processing steps like annealing (to relieve internal stresses) or moisture conditioning are critical. This is especially important for high-precision applications, such as medical devices or aerospace instruments, where dimensional consistency is non-negotiable.
A Deep Dive into Nylon Grades for High-Stakes Fastening
Selecting the right grade is critical for nylon bolts to meet performance, environmental, and cost requirements. The polyamide family offers diverse options for custom nylon bolts.
The Workhorses: Nylon 6 vs. Nylon 6/6 (PA6 vs. PA66)
Nylon 6/6 (PA66): Stiffer, stronger, and more abrasion-resistant, with a melting point of 265°C and lower water absorption, Nylon 6/6 is ideal for machining nylon bolts for demanding applications like gears, electrical connectors, and high-load nylon bolts.
Nylon 6 (PA6): More flexible with superior impact strength, Nylon 6 is ~30% cheaper, making it suitable for nylon bolts in general-purpose parts like housings and components where high temperature resistance is less critical.
Advanced Polyamides for Specialized Environments
Nylon 11 and 12 (PA11 & PA12): With minimal moisture absorption (Nylon 12 at 0.2%), these grades ensure nylon bolts maintain dimensional stability in humid or submerged conditions, ideal for fuel lines, pneumatic tubing, and marine-grade nylon bolts.
Nylon 4/6 (PA46): Offering superior heat resistance (up to 295°C melting point), Nylon 4/6 is used for nylon bolts in high-temperature applications like automotive under-hood components.
Nylon 6/12 (PA612): Balancing low moisture absorption and flexibility, Nylon 6/12 is suited for nylon bolts in precision instruments and outdoor equipment.
Supercharging Performance: Reinforced and Filled Nylons
Glass-Filled (GF) Nylon: Adding 30% glass fibers boosts tensile strength to ~130 MPa and heat resistance, making nylon bolts viable for structural components in automotive and aerospace applications.
MDS-Filled Nylon: Self-lubricating nylon bolts with molybdenum disulfide excel in high-wear applications like bearings, gears, and sliding components, reducing maintenance needs.
Carbon-Filled Nylon: With enhanced stiffness and conductivity control, carbon-filled nylon bolts are used in static-dissipative applications, such as electronics manufacturing.
Aramid-Filled Nylon: Incorporating aramid fibers, these nylon bolts offer exceptional toughness and impact resistance, ideal for high-stress applications in robotics and heavy machinery.
PTFE-Filled Nylon: With added polytetrafluoroethylene, these nylon bolts provide ultra-low friction and enhanced chemical resistance, suitable for precision components in chemical processing.
Table 1: Comparative Properties of Key Nylon Grades for Machining
Grade | Tensile Strength | Heat Deflection Temp. ( @0 .45 MPa) | Water Absorption (24hr, %) | Flexural Modulus | Impact Strength | Key Advantages | Common Applications |
Nylon 6 (PA6) | ~80 MPa (11,600 psi) | ~75°C | ~2.7% | ~2.8 GPa | High | Cost-effective, high impact strength | General-purpose nylon bolts, housings |
Nylon 6/6 (PA66) | ~85-95 MPa (12,400 psi) | ~250°C | ~2.0% | ~3.0 GPa | Moderate | High strength, stiffness, heat resistance | Gears, nylon bolts, connectors |
Nylon 12 (PA12) | ~60 MPa (8,700 psi) | ~140°C | ~0.2% | ~1.4 GPa | Moderate | Low moisture absorption, dimensional stability | Fuel lines, marine nylon bolts |
Nylon 4/6 (PA46) | ~100 MPa (14,500 psi) | ~290°C | ~3.5% | ~3.2 GPa | Moderate | Superior heat resistance | High-temp nylon bolts, automotive |
Nylon 6/12 (PA612) | ~70 MPa (10,150 psi) | ~180°C | ~0.3% | ~2.0 GPa | Moderate | Low moisture, flexibility | Precision nylon bolts, outdoor equipment |
Nylon 6/6, 30% GF | ~130 MPa (18,850 psi) | ~250°C | Low | ~9.0 GPa | Moderate | Extreme strength, high stability | Structural nylon bolts, aerospace |
Nylon MDS | High | High | Low | ~3.5 GPa | Moderate | Self-lubricating, high wear resistance | Bearings, gears, wear pads |
Nylon, Carbon-Filled | ~90 MPa (13,050 psi) | ~240°C | Low | ~10.0 GPa | Moderate | Stiffness, static dissipation | Electronics nylon bolts, anti-static components |
Nylon, Aramid-Filled | ~95 MPa (13,775 psi) | ~245°C | Low | ~8.5 GPa | Very High | Exceptional toughness, impact resistance | Robotics, heavy-duty nylon bolts |
Nylon, PTFE-Filled | ~65 MPa (9,425 psi) | ~230°C | Low | ~2.5 GPa | Moderate | Ultra-low friction, chemical resistance | Chemical processing nylon bolts, precision parts |
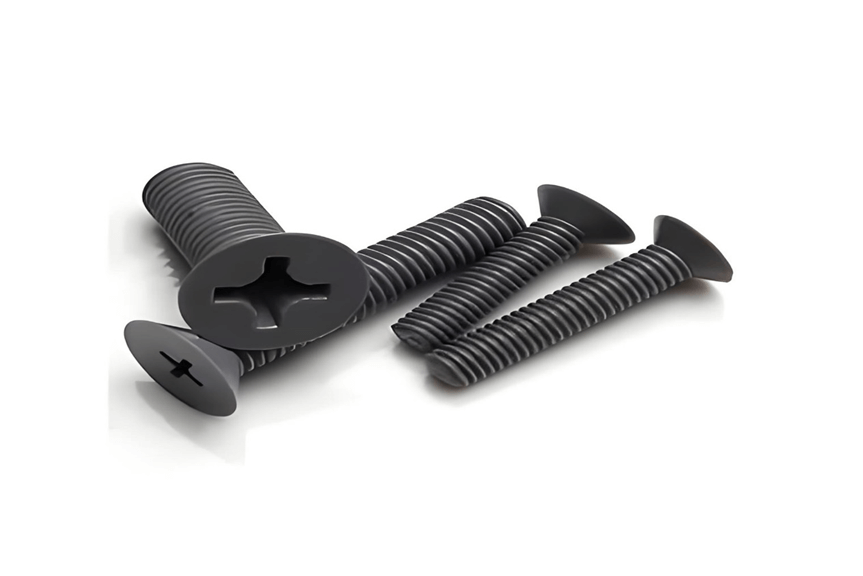
Nylon Bolts in Action: Critical Applications Across Industries
Electronics and Telecommunications
Nylon bolts are vital for their insulation properties, securing PCBs, wiring, and control panels in consumer electronics, servers, and telecommunications equipment. Non-conductive nylon bolts ensure safety and reliability in high-voltage environments.
Aerospace and Automotive
Nylon bolts reduce weight in non-structural components like avionics housings, interior panels, and electric vehicle battery enclosures, improving fuel efficiency and range. Their vibration damping ensures nylon bolts remain secure in engines, suspensions, and aircraft assemblies, reducing maintenance.
Medical and Healthcare Devices
Medical-grade nylon bolts are used in diagnostic equipment, imaging systems, and handheld tools, offering non-conductivity and precision for sensitive electronics. Lightweight nylon bolts enhance ergonomics in portable medical devices.
Marine and Industrial Machinery
Low-absorption nylon bolts (e.g., Nylon 12) resist saltwater corrosion, making them ideal for marine applications like boat fittings and offshore equipment. In industrial machinery, nylon bolts enhance durability through vibration damping and chemical resistance, extending service life in harsh environments.
Renewable Energy Systems
In wind turbines and solar panel assemblies, nylon bolts provide lightweight, corrosion-resistant fastening solutions. Their vibration damping ensures nylon bolts maintain integrity in dynamic wind turbine components, while UV-stabilized nylon bolts withstand prolonged outdoor exposure in solar installations.
Robotics and Automation
Nylon bolts, particularly aramid-filled variants, offer toughness and lightweight properties for robotic arms and automated machinery. Their low friction and wear resistance make nylon bolts ideal for high-precision, repetitive-motion applications.
Standard vs. Custom: Why CNC Machining is the Premier Choice
Off-the-shelf nylon bolts are limited to standard sizes, threads, and grades, often requiring design compromises. Custom CNC-machined nylon bolts deliver tailored solutions for high-performance applications, offering flexibility and precision.
CNC Machining vs. Injection Molding
- Cost and Volume: CNC machining eliminates tooling costs, making it cost-effective for prototypes, small batches, and low-to-medium volume nylon bolts, unlike injection molding’s high upfront mold costs.
- Lead Time and Flexibility: CNC produces nylon bolts in days from a CAD file, enabling rapid prototyping and design iteration compared to molding’s weeks-long lead times.
- Precision and Quality: CNC achieves tolerances of ±0.05 mm, ensuring nylon bolts meet exact specifications with consistent material properties, free from molding’s shrinkage issues.
A proven strategy uses CNC-machined nylon bolts for prototyping and initial production, transitioning to injection molding for cost-effective mass production once designs are validated.
The Art and Science of Precision CNC Machining for Nylon Bolts
Machining nylon bolts requires specialized expertise in thermal control, material preparation, and tool selection to achieve precision and quality.
The CNC Workflow
A 3D CAD model is converted to G-code, guiding CNC turning (for shanks, threads, and cylindrical features) and milling (for head features like hexagonal flats or Allen sockets) to produce nylon bolts with exact specifications.
Critical Success Factors
Heat Management: Sharp, high-speed tools and coolants like compressed air prevent melting or warping during machining of nylon bolts, ensuring clean cutsVitalSource Media cuts and dimensional accuracy.
Workholding: Gentle fixtures, such as multi-jaw chucks or custom supports, avoid deforming nylon bolts, maintaining tight tolerances.
Material Preparation: Annealing relieves internal stresses, and drying stabilizes moisture content in nylon bolts, preventing post-machining dimensional changes.
Tool Selection: Polycrystalline diamond (PCD) or carbide tools are preferred for machining nylon bolts, minimizing friction and ensuring smooth surface finishes.
Conclusion: Partnering for Performance
Nylon bolts are versatile, high-performance fasteners for applications requiring electrical insulation, corrosion resistance, lightweight strength, and vibration damping. Selecting the right grade—Nylon 6/6, Nylon 12, glass-filled, carbon-filled, or aramid-filled variants—is critical to unlocking their potential. Custom CNC-machined nylon bolts offer unmatched precision, flexibility, and cost-effectiveness for prototyping and production, enabling engineers to meet exact design requirements without the high costs of injection molding.
Partner with a CNC machining service specializing in engineering plastics to ensure nylon bolts deliver optimal performance. Visit [Insert Company Website] to request a quote, explore case studies, or consult with our team to discover how custom nylon bolts can elevate your project’s efficiency and reliability.
FAQ:
1. What are the main advantages of using nylon bolts over metal bolts?Nylon bolts offer electrical insulation, corrosion resistance, lightweight strength, and vibration damping, making them ideal for applications where metals fall short. They prevent short circuits in electronics, resist rust in marine environments, reduce weight in aerospace and automotive designs, and dampen noise in dynamic systems. Additionally, nylon bolts are often more cost-effective, reducing total installed costs by up to 30% in suitable applications due to lower material costs and faster installation.
2. In which industries are nylon bolts most commonly used?Nylon bolts are widely used in electronics (for PCB and wire harness mounting), aerospace (for lightweight, non-structural components), automotive (for battery enclosures and interior panels), medical (for diagnostic equipment and handheld devices), marine (for corrosion-resistant fittings), renewable energy (for wind turbines and solar panels), and robotics (for high-precision, repetitive-motion applications). Their versatility makes nylon bolts a go-to choice across these sectors.
3. What nylon grades are best for specific applications?The choice of nylon grade depends on the application:
- Nylon 6/6 (PA66): Ideal for high-strength nylon bolts in gears, connectors, and high-load applications due to its stiffness and heat resistance.
- Nylon 12 (PA12): Best for marine or humid environments due to low moisture absorption (0.2%).
- Glass-Filled Nylon: Suited for structural nylon bolts in aerospace and automotive applications for enhanced strength.
- MDS-Filled Nylon: Perfect for high-wear nylon bolts in bearings and gears.
- Carbon-Filled Nylon: Used for static-dissipative nylon bolts in electronics.
- Aramid-Filled Nylon: Optimal for high-impact nylon bolts in robotics.
- PTFE-Filled Nylon: Ideal for low-friction, chemically resistant nylon bolts in chemical processing.
4. How do nylon bolts perform in high-temperature environments?Standard nylon bolts operate reliably up to 85°C (185°F), unsuitable for high-heat applications like engine blocks. However, advanced grades like Nylon 4/6 (up to 295°C melting point) or glass-filled Nylon (up to 250°C) extend thermal performance, making nylon bolts viable for moderate high-temperature applications, such as automotive under-hood components.
5. Are nylon bolts suitable for outdoor or marine applications?Yes, nylon bolts are excellent for outdoor and marine applications when using low-moisture-absorption grades like Nylon 12 or UV-stabilized variants. These nylon bolts resist saltwater corrosion and UV degradation, making them ideal for boat fittings, offshore equipment, and solar panel mounts, unlike metals that may corrode or require costly coatings.
6. How does CNC machining improve the quality of nylon bolts?CNC machining offers superior precision (±0.05 mm tolerances), flexibility for custom designs, and no tooling costs, making it ideal for prototyping and low-to-medium volume nylon bolts. Unlike injection molding, CNC avoids shrinkage issues, ensuring consistent material properties. Specialized techniques like heat management and gentle workholding produce high-quality nylon bolts with smooth finishes and exact specifications.
Reference:
https://zh.wiktionary.org/zh-hans/nylon
https://zh.wikipedia.org/wiki/%E5%B0%BC%E9%BE%99
https://www.wikiwand.com/zh/articles/%E5%B0%BC%E9%BE%99
Other Articles You Might Enjoy
- Titanium Bolts: The Ultimate Guide to High-Strength, Lightweight Fasteners
Introduction: Why Titanium Bolts and CNC Machining Matter? Welcome, and thanks for reading my in-depth guide on titanium bolts. I’ve been working around metals and machining for a good part…
- Nylon Material Properties and Applications in CNC and Other Machining Methods
I chose this title because I believe it captures the essence of what we’ll explore: the fundamental properties of nylon material, its applications, and especially its role in CNC and…
- How Nylon Washers Are Made: From CNC Machining to Injection Molding
Introduction: What Are Nylon Washers and Why They Matter in Machining? Nylon washers are one of the unsung heroes of modern manufacturing. These simple yet versatile components are indispensable in…
- In-Depth Analysis of Nylon 66: Machining Properties and Applications
Introduction I want to share my personal experiences and observations regarding the remarkable material called Nylon 66. I’ve seen plenty of engineering plastics throughout my career, and each has its…
- Choosing the Right Concrete Anchor Bolts: A Guide for Engineers and Machinists
Why Concrete Anchor Bolts Matter When I first encountered concrete anchor bolts in my career as an engineer, I didn’t fully realize how critical these small, yet highly specialized fasteners…