Introduction to Nylon 12: A High-Performance Thermoplastic
Nylon 12, also known as Polyamide 12, is a high-performance engineering thermoplastic widely adopted in CNC machining for its exceptional combination of toughness, chemical resistance, and dimensional stability. These properties make Nylon 12 a top choice for precision components in industries such as aerospace, automotive, medical, and industrial manufacturing. Its ability to maintain performance under demanding conditions ensures reliable, high-quality parts. This comprehensive guide delves into Nylon 12’s material science, machining techniques, design considerations, and strategic applications, equipping engineers with the knowledge to leverage this versatile polymer effectively.
The Science Behind Nylon 12: Molecular Structure and Properties
Nylon 12, a semi-crystalline polyamide with the chemical formula [(CH₂)₁₁C(O)NH]ₙ, is synthesized from laurolactam monomers, each containing a 12-carbon chain. This long hydrocarbon chain reduces the density of hydrophilic amide groups, resulting in Nylon 12’s hallmark low moisture absorption (0.2%-0.8% at 23°C, 50% RH). Compared to short-chain nylons like PA6 or PA66, Nylon 12’s structure resembles polyolefins, imparting a paraffin-like quality that enhances dimensional stability and chemical resistance. This molecular advantage makes Nylon 12 uniquely suited for CNC machining applications requiring tight tolerances and environmental resilience, such as precision gears and medical device components.
Key Variants of Nylon 12: Tailored for Performance
Nylon 12 is available in multiple grades, each engineered to meet specific CNC machining requirements:
- Unfilled Nylon 12: Offers superior toughness, flexibility, and high impact strength, maintaining performance even at sub-zero temperatures, making it ideal for dynamic components like bushings.
- Glass-Filled PA12 (PA12-GF): Reinforced with 30% glass fibers, this variant significantly increases stiffness, tensile modulus, and heat deflection temperature, suitable for structurally demanding parts like automotive brackets.
- Carbon-Filled PA12 (PA12-CF): With 15-35% carbon fibers, it provides an exceptional strength-to-weight ratio and high flexural strength, positioning Nylon 12 as a lightweight alternative to metals in aerospace tooling and industrial fixtures.
- Specialty Grades: Variants like flame-retardant or UV-stabilized Nylon 12 cater to niche applications, such as electrical housings or outdoor components.
Table 1: Mechanical Properties of Nylon 12 Variants
Property | Unfilled Nylon 12 | PA12-GF (30%) | PA12-CF (20%) |
Tensile Strength (MPa) | 46-53 | 70-90 | 80-100 |
Flexural Modulus (GPa) | 1.4-1.7 | 4.5-6.0 | 6.0-8.0 |
Heat Deflection Temp (°C) | 80-100 | 140-160 | 150-170 |
Impact Strength (kJ/m²) | 50-60 (Notched) | 10-15 (Notched) | 15-20 (Notched) |
Analysis of Table 1: The mechanical properties of Nylon 12 variants highlight their adaptability. Unfilled Nylon 12 excels in impact resistance, ideal for parts subject to shock or vibration. Glass-filled PA12 offers enhanced stiffness and thermal resistance, perfect for structural components under load. Carbon-filled PA12 provides the highest rigidity and thermal stability, competing with metals in weight-sensitive applications. Engineers must select the appropriate Nylon 12 variant based on the part’s mechanical, thermal, and environmental demands.
Dimensional Stability: The Cornerstone of Nylon 12’s Machining Advantage
Nylon 12’s low moisture absorption sets it apart from other polyamides, absorbing only 0.2%-0.8% by weight compared to PA6’s 3-8% or PA66’s 2.5-7% at saturation. This property minimizes swelling and dimensional changes, ensuring Nylon 12’s superior stability during and after CNC machining. The table below compares moisture absorption across common polyamides, underscoring Nylon 12’s advantage.
Table 2: Moisture Absorption Comparison
Material | Moisture Absorption (% at Saturation, 23°C, 50% RH) | Impact on CNC Machining |
Nylon 12 | 0.2-0.8 | High dimensional stability, minimal pre-machining drying |
Nylon 6 | 3.0-8.0 | Significant swelling, requires extensive drying |
Nylon 66 | 2.5-7.0 | Moderate swelling, less stable than Nylon 12 |
Analysis of Table 2: Nylon 12’s minimal moisture absorption eliminates the need for extensive pre-machining drying cycles, unlike Nylon 6 or 66, which can swell significantly and compromise tolerances. This stability allows machinists to achieve tolerances as tight as ±0.05 mm, reducing scrap rates and ensuring consistent part dimensions. For precision applications, such as aerospace fittings or medical housings, Nylon 12’s reliability translates to lower manufacturing costs and higher-quality outcomes.
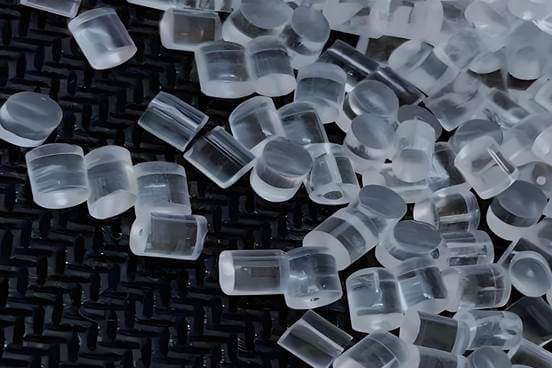
Mastering CNC Machining of Nylon 12: Techniques and Best Practices
Tooling Selection
CNC machining Nylon 12 requires precise tooling to prevent deformation and ensure clean cuts. Polished carbide tools are recommended for unfilled Nylon 12 due to their wear resistance and sharpness. For abrasive glass- or carbon-filled PA12 grades, Polycrystalline Diamond (PCD) tools are essential to combat rapid tool wear, though their higher cost is justified for high-volume production. Tools with high positive rake angles (10-20°) and generous relief angles minimize cutting forces and promote a shearing action, critical for Nylon 12’s soft, ductile nature.
Cutting Parameters
Nylon 12’s poor thermal conductivity necessitates careful heat management. High feed rates (0.1–0.3 mm/rev for turning, 0.1–0.25 mm/tooth for milling) produce thick chips that carry heat away, preventing melting or gumming. Cutting speeds of 150-300 m/min are suitable for unfilled Nylon 12, while 90-180 m/min is optimal for filled grades to manage abrasion-induced heat. Climb milling is preferred to reduce surface tearing and improve chip evacuation.
Coolant Use
Unfilled Nylon 12 can be machined dry with air blasts to clear chips and cool the tool, minimizing thermal buildup. For heavy roughing, deep drilling, or filled PA12 grades, water-soluble, non-aromatic coolants are effective, as Nylon 12 resists most oils and solvents. Proper coolant application ensures dimensional accuracy and extends tool life.
Troubleshooting Common Machining Issues
Warpage: Mitigate by using stress-relieved Nylon 12 stock, minimal clamping pressure, and separate roughing and finishing passes with a stabilization period to release internal stresses.
Burrs: Use sharp tools, high feed rates, and climb milling to minimize burr formation. In-machine deburring with chamfer tools eliminates manual post-processing.
Surface Finish: Optimized parameters yield Ra 3.2 µm or better. Bead blasting creates a uniform matte finish, while mechanical polishing achieves a glossy surface for aesthetic or functional parts.
Design for Manufactability (DFM): Optimizing Nylon 12 Parts
Designing Nylon 12 parts for CNC machining requires adapting metal machining principles to account for Nylon 12’s higher thermal expansion and lower rigidity:
- Wall Thickness: Maintain ≥1.5 mm to ensure rigidity and prevent warping, especially for thin-walled components.
- Internal Radii: Use radii ≥1/3 of cavity depth to reduce stress concentration and enable smoother toolpaths.
- Holes: Limit depths to 4-6× diameter, employing peck drilling for deeper holes to clear chips and dissipate heat.
- Threads: Opt for metal inserts (e.g., Helicoils) for durable, load-bearing threads in high-stress applications.
- Tolerances: Standard tolerances for Nylon 12 are ±0.1–0.2 mm, but ±0.05 mm is achievable in temperature-controlled environments with conditioned material.
These DFM principles ensure Nylon 12 parts are manufacturable, cost-effective, and reliable in service.
Strategic Applications of Nylon 12: Industry-Specific Solutions
Nylon 12’s unique properties make it indispensable across high-stakes industries:
- Automotive: Nylon 12’s chemical resistance to fuels, oils, and coolants makes it ideal for fuel lines, connectors, and under-hood components, ensuring leak-free performance in harsh environments.
- Aerospace: Its high strength-to-weight ratio and low-temperature toughness suit non-structural components like brackets, ducting, and cabin interiors, critical for high-altitude reliability.
- Medical: Biocompatible Nylon 12 (ISO 10993 certified) withstands sterilization methods (autoclave, EtO, gamma), making it perfect for surgical guides, instruments, and device housings.
- Industrial: Nylon 12’s wear resistance and dimensional stability support jigs, fixtures, and wear-resistant components like bearings and rollers in manufacturing systems.
- Electronics: Flame-retardant or UV-stabilized Nylon 12 grades are used for electrical housings and connectors, offering durability in challenging environments.
CNC Machining vs. 3D Printing for Nylon 12: A Comparative Analysis
Engineers must choose between CNC machining and 3D printing (Selective Laser Sintering or Multi Jet Fusion) for Nylon 12 parts based on project requirements. The table below compares these methods.
Table 3: CNC Machining vs. 3D Printing for Nylon 12
Attribute | CNC Machining | 3D Printing (SLS/MJF) | Winner For |
Dimensional Tolerance | ±0.05 mm | ±0.3 mm | CNC Machining |
Surface Finish | Smooth, non-porous (Ra 3.2 µm) | Grainy, matte, requires post-processing | CNC Machining |
Mechanical Properties | Isotropic | Near-isotropic to anisotropic | CNC Machining |
Geometric Complexity | Limited by tool access | Nearly unlimited (lattices, channels) | 3D Printing |
Cost (Low Volume, 1-10) | High (setup costs) | Low (no setup) | 3D Printing |
Cost (High Volume, 50+) | Lower (amortized setup) | High (linear per-part cost) | CNC Machining |
Lead Time (Prototype) | Longer (programming, setup) | Fast (direct from CAD) | 3D Printing |
Analysis of Table 3: CNC machining Nylon 12 excels in precision, achieving tolerances of ±0.05 mm and smooth, non-porous surfaces, making it ideal for functional parts like medical implants or automotive fittings. 3D printing Nylon 12 is superior for complex geometries, such as lattice structures or internal channels, and is cost-effective for low-volume prototypes. A hybrid approach—3D printing for intricate shapes followed by CNC machining for critical features—combines the strengths of both methods, optimizing precision and design freedom for Nylon 12 parts.
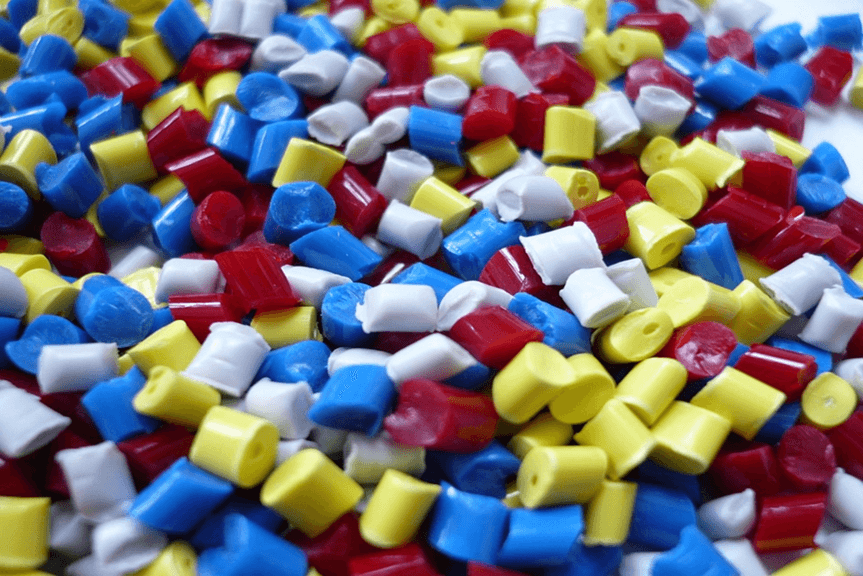
Cost and Efficiency Considerations for Nylon 12 Machining
While Nylon 12’s material cost is higher than other polyamides like PA6, its dimensional stability reduces total manufacturing costs by minimizing scrap, rework, and drying time. For high-volume production, CNC machining Nylon 12 amortizes setup costs, making it more economical than 3D printing. Additionally, Nylon 12’s ease of machining reduces tool wear for unfilled grades, further lowering costs. For filled grades, investing in PCD tools ensures long-term efficiency despite higher upfront costs. Engineers should weigh these factors against project budgets and production scales to optimize cost-effectiveness.
Conclusion: Strategic Recommendations for Nylon 12 CNC Machining
Nylon 12’s low moisture absorption, dimensional stability, and robust mechanical properties make it a premier material for CNC machining precision components. Its versatility across unfilled, glass-filled, and carbon-filled grades supports applications in automotive, aerospace, medical, and industrial sectors. For projects requiring tight tolerances and superior surface finishes, CNC machining Nylon 12 is the optimal choice. For complex geometries, 3D printing Nylon 12 offers design freedom, with hybrid approaches bridging both worlds. By aligning material selection, DFM principles, and machining strategies, engineers can unlock Nylon 12’s full potential for durable, high-performance parts. Ready to machine precision Nylon 12 components? Contact our CNC machining experts or explore our material selection guide at want.net.
FAQ:
1.What is Nylon 12, and why is it used in CNC machining?
Nylon 12, also known as Polyamide 12, is a high-performance engineering thermoplastic valued for its toughness, chemical resistance, and low moisture absorption (0.2%-0.8%). Its exceptional dimensional stability makes it ideal for CNC machining precision components, as it minimizes swelling and maintains tight tolerances (±0.05 mm). Nylon 12 is widely used in industries like aerospace, automotive, and medical for parts requiring reliability and durability.
2.What are the key variants of Nylon 12 for CNC machining?
Nylon 12 is available in several grades tailored for specific applications:
- Unfilled Nylon 12: Offers high toughness and flexibility, ideal for dynamic parts like bushings.
- Glass-Filled PA12 (PA12-GF): Contains 30% glass fibers for increased stiffness and heat resistance, suitable for structural components.
- Carbon-Filled PA12 (PA12-CF): Includes 15-35% carbon fibers for a high strength-to-weight ratio, used in lightweight alternatives to metal.
- Specialty Grades: Flame-retardant or UV-stabilized Nylon 12 for electrical or outdoor applications.
3.How does Nylon 12’s dimensional stability benefit CNC machining?
Nylon 12’s low moisture absorption (0.2%-0.8% vs. 3-8% for Nylon 6) prevents swelling, ensuring consistent dimensions during and after machining. This allows for tight tolerances (±0.05 mm), reduces scrap rates, and eliminates extensive pre-machining drying, lowering manufacturing costs and improving precision for parts like gears or medical housings.
4.What tools are best for CNC machining Nylon 12?
For unfilled Nylon 12, polished carbide tools with high positive rake angles (10-20°) and generous relief angles are recommended for clean cuts. For abrasive glass- or carbon-filled PA12, Polycrystalline Diamond (PCD) tools are preferred to combat tool wear, especially in high-volume production, ensuring durability and precision.
5.What are the recommended cutting parameters for Nylon 12?
To manage Nylon 12’s low thermal conductivity:
- Cutting Speed: 150-300 m/min for unfilled Nylon 12; 90-180 m/min for filled grades.
- Feed Rate: 0.1–0.3 mm/rev for turning; 0.1–0.25 mm/tooth for milling.
- Strategy: Use high feed rates to produce thick chips that dissipate heat, preventing melting. Climb milling is preferred to minimize surface tearing.
6.Should I use coolant when machining Nylon 12?
Unfilled Nylon 12 can be machined dry with air blasts to clear chips and cool the tool. For heavy roughing, deep drilling, or filled PA12 grades, water-soluble, non-aromatic coolants are effective, as Nylon 12 resists most oils and solvents, ensuring dimensional accuracy and tool longevity.
Reference:
https://en.wikipedia.org/wiki/Nylon_12
https://www.wikiwand.com/zh/articles/%E5%B0%BC%E9%BE%99
https://pubs.acs.org/doi/10.1021/ie50723a005
Other Articles You Might Enjoy
- CNC-Machined Nylon Bolts: An In-Depth Look at Material Grades, Industry Applications, and Precision Manufacturing
Introduction: In modern engineering, the demand for materials that balance strength, lightweight design, and environmental resilience drives innovation. Nylon bolts, high-performance polyamide fasteners, are critical solutions for challenges where metals…
- Polyamide vs. Nylon: The Ultimate Engineer's Guide to Properties, Types, and Applications
Introduction As an engineer with over a decade of experience in polymer applications, I’ve frequently tackled the polyamide vs. nylon confusion, especially when selecting materials for CNC machining projects. Polyamide…
- In-Depth Analysis of Nylon 66: Machining Properties and Applications
Introduction I want to share my personal experiences and observations regarding the remarkable material called Nylon 66. I’ve seen plenty of engineering plastics throughout my career, and each has its…
- How Nylon Washers Are Made: From CNC Machining to Injection Molding
Introduction: What Are Nylon Washers and Why They Matter in Machining? Nylon washers are one of the unsung heroes of modern manufacturing. These simple yet versatile components are indispensable in…
- Nylon Material Properties and Applications in CNC and Other Machining Methods
I chose this title because I believe it captures the essence of what we’ll explore: the fundamental properties of nylon material, its applications, and especially its role in CNC and…