Aluminum CNC machining stands at the forefront of modern manufacturing, epitomizing precision, versatility, and efficiency. With its widespread applications across industries ranging from aerospace to automotive and beyond, aluminum CNC machining has revolutionized the production of intricate components with unparalleled accuracy and consistency.
Why use CNC machining of aluminum alloy?
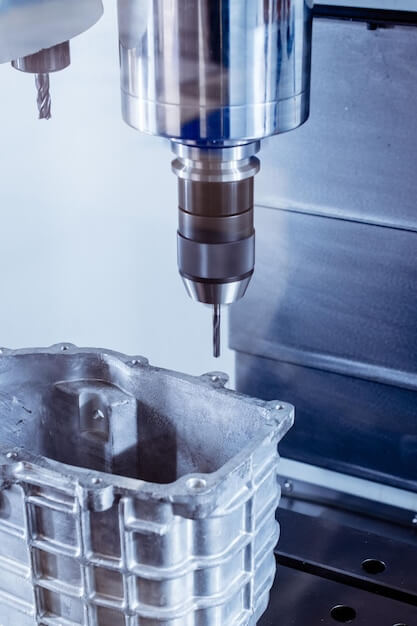
At the heart of aluminum CNC machining lies Computer Numerical Control (CNC) technology, which utilizes computer programs to control the movement and operation of machining tools with exceptional precision. When applied to aluminum, CNC machining offers numerous advantages, making it the preferred choice for fabricating complex parts with intricate geometries.
One of the primary benefits of aluminum CNC machining is its ability to achieve tight tolerances and exact specifications consistently. Whether producing aerospace components or intricate automotive parts, CNC machines can replicate designs with microscopic accuracy, ensuring uniformity and reliability across large production runs.
Moreover, aluminum’s inherent properties make it an ideal candidate for CNC machining. As a lightweight yet durable material with excellent machinability, aluminum enables swift and precise machining processes, reducing production times and costs while maintaining high quality.
Furthermore, the versatility of aluminum CNC machining extends beyond traditional manufacturing constraints. With advanced multi-axis CNC machines, manufacturers can create complex shapes and contours previously deemed unattainable, pushing the boundaries of design and innovation.
The aerospace industry, in particular, has embraced aluminum CNC machining for its ability to produce lightweight yet robust components vital for aircraft performance and fuel efficiency. From structural elements to intricate engine parts, aluminum CNC machining plays a pivotal role in enhancing aircraft safety and performance.
In the automotive sector, aluminum CNC machining facilitates the production of lightweight components that contribute to fuel efficiency and vehicle performance. From engine blocks to suspension components, CNC-machined aluminum parts are integral to modern automotive engineering, meeting the demands for both strength and efficiency.
Beyond aerospace and automotive applications, aluminum CNC machining finds use in diverse sectors, including electronics, medical devices, and consumer goods. Its adaptability and precision make it indispensable for manufacturing components across a broad spectrum of industries, driving innovation and progress.
In conclusion, aluminum CNC machining represents a pinnacle of modern manufacturing, combining precision, versatility, and efficiency to produce complex components with unparalleled accuracy. As technology continues to advance, the role of aluminum CNC machining will only grow, shaping the future of manufacturing across industries worldwide.
Why do many use aluminum alloys to customize parts?
Aluminum is a popular choice for custom parts due to its favorable properties such as lightweight, durability, and excellent machinability. By utilizing CNC machining, manufacturers can produce intricate and complex parts with high precision and repeatability, making it suitable for various industries including aerospace, automotive, electronics, and more.
Here are common aluminum alloy grades suitable for CNC machining:
- 6061 Aluminum Alloy: This is a common general-purpose aluminum alloy known for its good machinability and weldability, suitable for various CNC machining applications such as milling, drilling, and turning.
- 7075 Aluminum Alloy: This is a high-strength aluminum alloy often used in applications requiring high strength and wear resistance, such as CNC machining of aerospace and automotive parts.
- 2024 Aluminum Alloy: This is a high-strength aluminum alloy commonly used in the aerospace industry, known for its excellent machinability, suitable for CNC milling and drilling operations.
- 5052 Aluminum Alloy: This is a commonly used aluminum alloy for sheet metal processing, known for its good formability and corrosion resistance, suitable for CNC cutting, bending, and forming.
- 6063 Aluminum Alloy: This is a commonly used aluminum alloy for component machining, known for its good corrosion resistance and decorative properties, suitable for CNC milling and turning.
These aluminum alloy grades exhibit good machinability and surface quality during CNC machining processes, meeting various requirements from simple parts to complex components.
CNC machining of aluminum can achieve the following precision:
- Dimensional Accuracy: Typically around ±0.01 mm (10 microns). High-precision machining can achieve ±0.005 mm (5 microns) or even better.
- Surface Roughness: Usually can reach Ra 0.4 microns (16 microinches) or better. Further improvements can be made through fine machining or grinding.
- Positional Accuracy: Positioning accuracy is usually around ±0.01 mm, depending on the calibration of the machine and measuring equipment.
After completing CNC machining of aluminum, several subsequent steps are typically required to ensure the quality, functionality, and appearance of the parts. These steps may include the following:
Post-Processing Steps
Deburring: Removing burrs produced during machining to ensure smooth and even surfaces.
- Manual Deburring: Using tools such as scrapers, sandpaper, or stones to remove burrs by hand.
- Mechanical Deburring: Using deburring machines, polishers, or tumblers for burr removal.
- Chemical Deburring: Using chemical solutions to dissolve burrs.
Cleaning: Removing cutting fluids, grease, and other contaminants from the part surfaces to ensure cleanliness.
- Ultrasonic Cleaning: Using ultrasonic vibrations in cleaning liquid to clean small holes and complex surfaces.
- Spray Cleaning: Using high-pressure spray equipment to clean the part surfaces.
Heat Treatment: Performing heat treatment to alter the mechanical properties (such as hardness and strength) of the material as needed.
- Annealing: Relieving internal stress and improving material ductility.
- Quenching: Rapid cooling to increase material hardness.
- Aging Treatment: Heating and holding for a period to improve the mechanical properties of the material.
Surface Treatment: Enhancing the surface properties and appearance of the parts, including corrosion resistance and hardness.
- Anodizing: Forming an oxide layer on the aluminum surface through an electrolytic process to improve corrosion resistance and hardness.
- Plating: Coating the part surface with a layer of metal to enhance wear resistance and corrosion protection.
- Coating: Applying a coating to the part surface for protection and decorative effects.
Finishing: Further improving the precision and surface finish of the parts.
- Grinding: Using a grinding machine for precise grinding to achieve high accuracy and surface quality.
- Polishing: Improving surface smoothness through polishing to achieve a mirror finish.
Inspection and Testing: Inspecting parts for dimensions, geometric tolerances, and surface quality to ensure they meet design requirements.
- Coordinate Measuring: Using a coordinate measuring machine (CMM) for precise measurements.
- Visual Inspection: Detecting surface defects using microscopes or other optical devices.
- Non-Destructive Testing: Detecting internal defects using methods like ultrasonic or X-ray testing.
Assembly and Installation: Assembling the machined parts with other components to complete the final product.
- Manual Assembly: Operators manually assembling the parts.
- Automated Assembly: Using automated equipment for assembly to improve efficiency and consistency.
These post-processing steps ensure that CNC-machined aluminum parts have high quality, performance, and appearance, meeting the requirements of their final application.
Other Articles You Might Enjoy
- CNC Machining Materials: Acrylic vs. Polycarbonate for Transparent Components
CNC Machining: An Introduction and the Importance of Material Type Computer Numerical Control (CNC) machining is a manufacturing process where pre-programmed computer software dictates the movement of factory tools and…
- 10 Advantages of CNC Machining for Custom Parts
CNC machining services produce high-quality parts with accuracy and efficient production. These CNC machines use computer numerical control machining tools to cut and shape materials precisely. Additionally, CNC machining services…
- Aluminum Grades: Key Characteristics and CNC Machining(Aluminum Grades and Properties Gemma)
As advancements in manufacturing technologies continue to evolve, industries are leveraging more efficient methods like CNC machining for their production processes. One of the commonly used materials in these operations…