Executive Summary
CNC-machined plastic bushings are transforming industrial applications by addressing the inherent failures of metal bushings. Unlike bronze or steel, plastic bushings eliminate lubrication needs, resist corrosion, and reduce weight and vibration. Precision-engineered from materials like PEEK, POM, PTFE, and UHMW-PE, these bushings deliver reliable, cost-effective solutions for industries such as aerospace, marine, automotive, and food processing. This report explores how plastic bushings enhance system efficiency, minimize downtime, and drive long-term savings, offering a proactive approach to modern engineering challenges.
Introduction: The Anatomy of a Preventable Failure
In a bustling food processing plant, a critical conveyor line halts due to a seized bronze bushing. This minor component failure triggers costly downtime, risks contamination from grease and metal particulates, and damages expensive steel shafts. Such incidents expose the limitations of metal bushings in modern industries. CNC-machined plastic bushings provide a transformative solution, eliminating lubrication dependency, corrosion, and performance penalties. This report details how plastic bushings overcome the systemic flaws of metal components, delivering reliable performance across diverse applications.
1. The Hidden Liabilities of Traditional Metal Bushings: A Systemic Analysis
The perceived reliability of metal bushings, such as bronze or steel, conceals significant operational and financial liabilities. Operating within a narrow optimal window, deviations lead to a cycle of degradation and premature failure. Four core vulnerabilities undermine their performance and inflate ownership costs.
1.1 The Lubrication Paradox: A Solution That Fuels Failure
Metal bushings rely on external lubrication to reduce friction, but this creates a paradox: grease attracts contaminants like dust, dirt, and metal shavings, forming an abrasive slurry. This accelerates wear, scores shafts, and escalates maintenance costs. For example, a manufacturing client removed 400-pound barrels of greasy sludge from bronze bushings, requiring dedicated labor for degreasing. Plastic bushings, with self-lubricating properties, eliminate this failure loop, operating without grease and reducing contamination risks, ensuring cleaner and more efficient systems.
1.2 The Inevitability of Corrosion: A Ticking Clock
Metal bushings corrode in harsh environments. Bronze degrades in moisture, chemicals, or saltwater, while steel is even more vulnerable unless costly stainless grades are used. Galvanic corrosion occurs when dissimilar metals, like a bronze bushing and steel shaft, form an electrochemical cell in an electrolyte (e.g., seawater), pitting the shaft and increasing repair costs. Graphite-based lubricants can worsen this by enhancing electrical pathways. Plastic bushings, being chemically inert, are immune to corrosion, protecting critical components in marine or chemical settings.
1.3 The Inertia Penalty: Costs of Mass and Vibration
The mass of metal bushings increases inertia in dynamic systems like robotics or aerospace, raising energy consumption and limiting speed or payload capacity. A PEEK plastic bushing, up to 80% lighter than metal, reduces these penalties. Metals’ rigid structure also transmits vibrations, causing noise and potential damage to electronics. Plastic bushings, with viscoelastic properties, absorb vibrational energy, ensuring quieter operation and enhanced system longevity.
1.4 The Maintenance Burden: A Hidden Cost Multiplier
Metal bushings demand frequent maintenance to monitor wear, reapply grease, and replace failed components, diverting resources and increasing downtime costs. In high-throughput industries, hours of unplanned maintenance can result in significant revenue losses. Plastic bushings, designed for low maintenance, reduce these burdens by offering long service life and eliminating regular interventions, making them ideal for cost-conscious operations.
Table 1: Cost Comparison of Metal vs. Plastic Bushings
Component Type | Initial Cost (USD) | Annual Maintenance Cost (USD) | Expected Service Life (Years) | Downtime Cost Impact (USD/Hour) |
Bronze Bushing | 5–20 | 1,000–5,000 | 1–3 | 1,000–10,000 |
Plastic Bushing (PEEK) | 20–50 | 100–500 | 5–10 | Minimal |
Plastic Bushing (POM) | 10–30 | 50–200 | 4–8 | Minimal |
Plastic Bushing (PTFE) | 15–40 | 50–200 | 3–7 | Minimal |
Note: Costs vary by application; data based on typical industrial scenarios. |
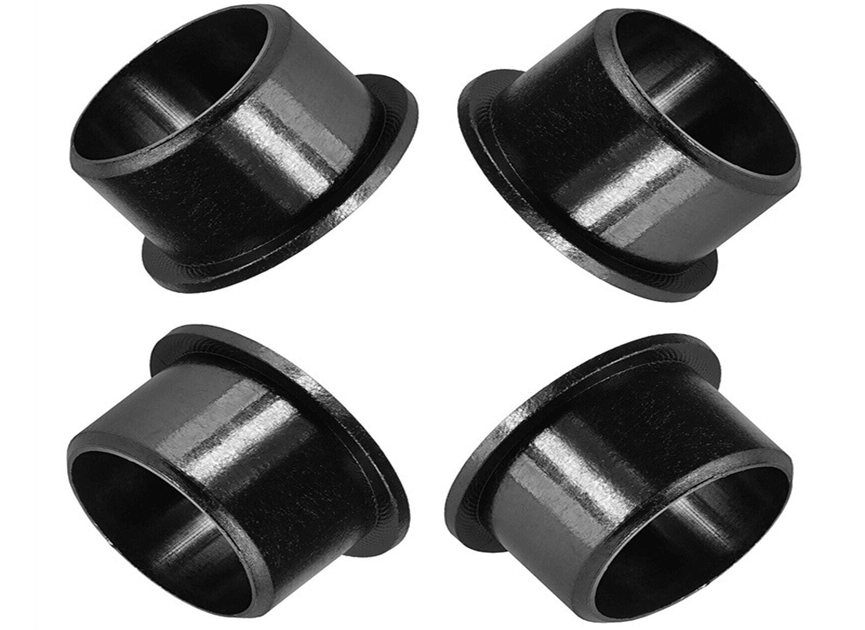
2. The Solution Synthesis: CNC-Machined Plastic Bushings and Advanced Polymers
Addressing metal bushing failures requires a paradigm shift. CNC-machined plastic bushings, crafted from advanced polymers, are engineered to eliminate lubrication dependency, corrosion, and performance penalties, offering a proactive solution for modern industries.
2.1 A New Class of Materials: Engineering Reliability
Plastic bushings leverage self-lubricating polymers like POM, Nylon, and PTFE, eliminating grease-related contamination. PTFE forms a low-friction transfer film during operation, ensuring durable performance. These materials resist corrosion, making them ideal for harsh environments like marine or food processing. By protecting mating components, plastic bushings extend system life and reduce replacement costs.
2.2 Why CNC Machining is Critical for Plastic Bushings
CNC machining transforms high-performance polymers into precise plastic bushings without expensive molding. Its advantages include:
- No Tooling Costs: Economical for prototypes to mid-volume runs.
- Precision: Tolerances of ±0.05 mm ensure perfect fit for plastic bushings.
- Geometric Flexibility: Enables complex features like flanges or grooves.
This synergy makes plastic bushings accessible for critical applications, maximizing material performance.
2.3 The Role of Material Innovation in Plastic Bushings
Advancements in polymer science enhance plastic bushings. Reinforced PEEK with carbon fibers improves strength, while additives like molybdenum disulfide boost POM’s lubricity. These innovations allow plastic bushings to meet high-load, high-speed, or extreme-temperature demands, replacing metal in critical systems.
3. Strategic Material Selection: A Data-Driven Framework for Plastic Bushings
Selecting the optimal plastic bushing requires matching material properties to application demands, considering load, speed, temperature, chemical exposure, and dimensional stability.
3.1 The Performance Spectrum: Matching Plastic Bushings to Applications
Four materials dominate plastic bushing applications: PEEK, POM, PTFE, and UHMW-PE, each tailored to specific conditions.
3.2 Material Profiles
PEEK (Polyetheretherketone):
- Strengths: Tensile strength of 14,000–16,000 psi, thermal stability up to 500°F, excellent chemical resistance, low moisture absorption (0.50%).
- Applications: Aerospace, oil and gas, and medical plastic bushings.
POM (Acetal/Delrin®):
- Strengths: Tensile strength of 9,100–9,500 psi, low moisture absorption (0.20–0.22%), dimensional stability.
- Applications: Precision gears, conveyor plastic bushings, automotive components.
PTFE (Teflon®):
- Strengths: Lowest friction (0.05–0.10), chemical inertness, wide temperature range (-400°F to 500°F).
- Weaknesses: Lower strength, susceptible to creep.
- Applications: Food-grade plastic bushings, seals, chemical processing components.
UHMW-PE (Ultra-High Molecular Weight Polyethylene):
- Strengths: High impact and abrasion resistance, near-zero water absorption (<0.01%).
- Weaknesses: Limited to 180°F, high thermal expansion.
- Applications: Marine and conveyor plastic bushings in high-abrasion settings.
3.3 The Critical Metric: PV Value for Plastic Bushings
The PV value (Pressure × Velocity) quantifies frictional heat in plastic bushings. Exceeding a material’s limiting PV causes softening and failure. Calculations include:
- Pressure (P): Load ÷ Contact Area (psi).
- Velocity (V): 0.262 × rpm × shaft diameter (fpm).
PTFE supports up to 10,000 psi-fpm, while POM handles bond 3,000–4,000 psi-fpm, guiding material selection for plastic bushings.
3.4 Key Data Comparison Table
Plastic Bushing Material | Tensile Strength (psi) | Max Service Temp (°F) | Coefficient of Friction | Water Absorption (%) | Limiting PV (psi-fpm) |
PEEK | 14,000–16,000 | 480–500 | 0.25–0.35 | 0.50 | High |
POM (Acetal) | 9,100–9,500 | 180–212 | 0.35 | 0.20–0.22 | 3,000–4,000 |
PTFE | 3,000–4,000 | 500 | 0.05–0.10 | <0.01 | 7,500–10,000 |
UHMW-PE | 2,800–3,100 | 180 | 0.12–0.25 | <0.01 | Low |
Cast Nylon 6 | 10,000–13,500 | 230 | 0.20–0.40 | 0.05–1.40 | 3,600 |
Bronze (SAE 841) | 14,000 | 350–400 | High (Lubricated) | 0 | High (Lubricated) |
3.5 Cost-Benefit Analysis of Plastic Bushings
High-performance plastic bushings like PEEK have higher upfront costs than bronze but offer significant long-term savings. A food processing plant replacing bronze with PTFE plastic bushings reported a 90% reduction in maintenance costs and zero contamination incidents over three years, highlighting the economic advantage of plastic bushings.Table 2: Environmental Resistance of Plastic Bushings
Material | Corrosion Resistance | Chemical Resistance | Water Absorption (%) | Suitable Environments |
PEEK | Excellent | Excellent | 0.50 | Aerospace, Oil/Gas, Medical |
POM | Good | Good | 0.20–0.22 | Automotive, Conveyors |
PTFE | Outstanding | Outstanding | <0.01 | Food Processing, Chemical |
UHMW-PE | Outstanding | Good | <0.01 | Marine, High-Abrasion |
Bronze | Moderate | Poor | 0 | Limited (Non-Corrosive) |
4. The Manufacturing Imperative: CNC Strategy for Plastic Bushings
Transforming polymers into high-performance plastic bushings requires sophisticated CNC strategies to address material-specific challenges and ensure precision.
4.1 Machining Challenges for Plastic Bushings
PEEK: Abrasive, requiring Polycrystalline Diamond (PCD) tooling for reinforced grades.
POM: Heat-sensitive, needing controlled speeds and cooling to prevent melting.
UHMW-PE: Forms long swarf, requiring coolants to manage thermal expansion.
PTFE: Soft, needing sharp tools to avoid smearing and distortion.
Expert CNC machining ensures plastic bushings meet stringent performance requirements.
4.2 Annealing: A Critical Step for Plastic Bushings
Annealing relieves internal stresses in plastic bushings, preventing warping during machining. This ensures dimensional stability for high-precision applications like aerospace or medical plastic bushings.
4.3 Design for Manufacturability (DfM) for Plastic Bushings
Tolerances: Design for ±0.2 mm to accommodate thermal expansion.
Wall Thickness: Minimum 1.5 mm to prevent vibration and warping.
Internal Radii: Use radii at least one-third the cavity depth for better tool stability.
Thermal Management: Use appropriate coolants (e.g., compressed air for medical-grade plastic bushings) to prevent melting.
These considerations optimize the production of plastic bushings, enhancing quality and reducing costs.
4.4 Quality Control in CNC Machining
Advanced CNC systems use real-time monitoring to ensure plastic bushings meet exact specifications. Post-machining inspections, including dimensional checks and surface finish analysis, guarantee reliability in applications from conveyors to aerospace assemblies.
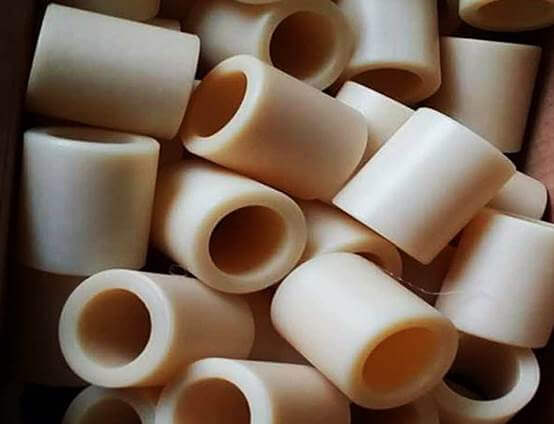
5. Proven in the Field: Application Spotlights for Plastic Bushings
CNC-machined plastic bushings excel in demanding industries, solving real-world challenges with proven results.
5.1 Aerospace: Weight Reduction with Plastic Bushings
Aerospace demands weight reduction to improve fuel efficiency. PEEK plastic bushings, 85% lighter than steel, offer strength comparable to aluminum while resisting aviation fluids and high temperatures. They are used in landing gear, flight control systems, and engine plastic bushings, enhancing performance without compromising reliability.
5.2 Marine: Conquering Corrosion with Plastic Bushings
Saltwater corrodes metal bushings, and galvanic corrosion in bronze-steel pairings causes seizure in marine systems like rudders. UHMW-PE plastic bushings resist corrosion, absorb no water, and operate without grease. Case studies show UHMW-PE plastic bushings lasting years longer than bronze, reducing maintenance and improving reliability.
5.3 Food Processing: Eliminating Contamination with Plastic Bushings
In food processing, grease from metal bushings risks contamination, while washdowns accelerate corrosion. Self-lubricating plastic bushings (PTFE, POM, UHMW-PE) eliminate grease, resist caustic cleaners, and comply with FDA standards. Case studies show plastic bushings extending component life from weeks to years in conveyors and filling machines, saving millions in downtime and contamination costs.
5.4 Automotive: Enhancing Efficiency with Plastic Bushings
Plastic bushings reduce vehicle weight and improve fuel efficiency in automotive applications. POM and PEEK plastic bushings are used in suspension systems, steering assemblies, and transmissions, offering low friction and high durability. Their grease-free operation simplifies assembly and reduces maintenance, making them ideal for modern vehicles.
5.5 Medical Devices: Precision and Biocompatibility
Medical devices require precision and biocompatibility. PEEK plastic bushings, machined to tight tolerances, are used in surgical instruments and imaging equipment, offering chemical resistance and compatibility with sterilization processes. Their lightweight and low-friction properties enhance device performance and patient safety.
6. The Broader Impact: Sustainability and Future Trends
Plastic bushings contribute to sustainability by reducing energy consumption (due to lower weight), minimizing waste (through longer service life), and eliminating grease-related environmental hazards. As industries prioritize eco-friendly solutions, plastic bushings align with green manufacturing trends. Future advancements, such as bio-based polymers and AI-driven CNC optimization, promise enhanced performance and sustainability for plastic bushings.
7. Conclusion: A Strategic Shift to Plastic Bushings
Choosing CNC-machined plastic bushings over metal represents a shift from maintenance-heavy systems to engineered reliability. Plastic bushings eliminate lubrication, corrosion, and weight penalties, replacing ongoing costs with a one-time investment in advanced materials and CNC precision. Engineers can select optimal polymers—PEEK for aerospace, UHMW-PE for marine, PTFE for food processing, or POM for automotive—to build efficient, reliable, and profitable machinery. Ready to upgrade with plastic bushings? Contact a trusted supplier at x.ai/grok (#) for custom solutions tailored to your industry’s needs.
FAQ:
1. Why choose plastic bushings over metal bushings?
Plastic bushings outperform metal with self-lubrication, corrosion resistance, up to 80% weight reduction, and vibration damping, reducing maintenance and downtime in industries like aerospace and food processing.
2. How does CNC machining improve plastic bushings?
CNC machining ensures precision (±0.05 mm tolerances), complex designs, and cost-effective production without molding, making plastic bushings ideal for custom applications.
3. Which industries use plastic bushings?
Aerospace (PEEK for weight savings), marine (UHMW-PE for corrosion resistance), food processing (PTFE for FDA compliance), automotive (POM for efficiency), and medical (PEEK for biocompatibility).
4. How do I select the right plastic bushing material?
Match material to application: PEEK for high loads/temperatures, POM for precision, PTFE for low friction, UHMW-PE for abrasion resistance. Check PV value (Pressure × Velocity) against material limits.
5. Are plastic bushings cost-effective?
Higher initial costs (e.g., $20–50 vs. $5–20 for bronze) are offset by lower maintenance, longer life (5–10 years vs. 1–3), and reduced downtime, saving thousands per hour.
6. Can plastic bushings handle high loads/speeds?
Yes, PEEK and POM manage high loads (up to 14,000 psi), and PTFE supports high speeds (10,000 psi-fpm). Verify PV values to ensure suitability.
7. Do plastic bushings support sustainability?
Plastic bushings reduce energy use, waste, and grease pollution. Future bio-based polymers and AI-driven CNC machining will enhance eco-friendliness.
8. What are the machining challenges for plastic bushings?
PEEK requires PCD tooling, POM needs heat control, UHMW-PE forms long swarf, and PTFE demands sharp tools. Annealing ensures stability.
9. Are plastic bushings FDA-compliant?
Yes, PTFE, POM, and UHMW-PE in FDA-compliant grades are ideal for food processing plastic bushings, resisting washdowns and eliminating contamination.
10. How do I implement plastic bushings?
Assess application needs, select the right material, and partner with a CNC machining expert. Contact x.ai/grok (#) for custom plastic bushing solutions.
Reference:
https://www.linguee.com/english-chinese/translation/nylon+bushing.html
https://www.sciencedirect.com/science/article/abs/pii/S2214785315004484
https://zh.wikipedia.org/wiki/%E8%BD%B4%E5%A5%97
Other Articles You Might Enjoy
- Unlocking the Potential of Bronze Bushings with CNC Machining
I. Introduction Bronze bushings are an indispensable component in the world of mechanical engineering. They provide critical support for rotating parts, reduce friction, and enhance the efficiency of countless machines.…
- CNC Machining of Polymers: A Comparative Analysis of Thermoplastic vs. Thermoset
In CNC machining, selecting the right polymer for precision components is a pivotal decision that defines performance, durability, and manufacturability. The choice between Thermoplastic vs. Thermoset is especially critical, as…
- Unraveling the World of CNC Machined Plastic Parts(CNC machined plastic parts Mabel)
Modern innovations have taken traditional manufacturing methods to new heights. One such innovation that stands out is Computer Numerical Control (CNC) machining, a process used extensively in various industries from…
- CNC Machined Plastic Parts: An In-depth Overview(CNC machined plastic parts Norman)
Computer Numeric Control (CNC) machining is an advanced manufacturing process where pre-programmed software dictates the movement of factory machinery and tools. These applications can carry out complicated manufacturing tasks with…
- Avoid Melting and Delamination When Machining Plastic Laminate
Introduction Plastic laminate is a beautiful material when it’s done right—and a real nightmare when it isn’t. I’ve been working with CNC machines for years, and if there’s one thing…