The honing rod is a term that spans two distinct realms: the culinary kitchen and the high-precision machine shop. In a chef’s hands, a honing rod realigns a knife’s edge for sharpness, but in CNC machining, the honing rod refers to abrasive stones that perfect internal bores with micron-level accuracy. This article explores the industrial honing rod, demystifying its critical role in achieving geometric precision, dimensional accuracy, and functional surface finishes in components for automotive, aerospace, hydraulics, and more. From the science of abrasives to emerging smart technologies, we uncover why the honing rod is a cornerstone of modern manufacturing and how it’s evolving in the Industry 4.0 era.
The Honing Rod: Clarifying a Precision Manufacturing Term
The phrase honing rod often sparks confusion due to its dual meanings across industries. Understanding its industrial significance is key to appreciating its transformative impact in CNC machining.
The Kitchen Honing Rod: A Common Misconception
In culinary settings, a honing rod—commonly known as a honing steel—is a steel or ceramic tool used to straighten a knife’s microscopic edge, restoring cutting efficiency without significant material removal. This burnishing process, while effective for edge maintenance, is entirely distinct from the industrial honing rod used in manufacturing.
The Industrial Honing Rod: Precision Abrasives
In CNC machining, the honing rod refers to abrasive stones or sticks integrated into a honing tool assembly. These honing rods are mounted on a mandrel, which expands to press them against a workpiece’s internal bore, removing minute amounts of material (0.01–0.2 mm) to achieve perfect geometry and surface finish. Unlike the kitchen honing rod, industrial honing rods are engineered for precision, making them indispensable for applications like engine cylinders, hydraulic actuators, and aerospace components. By clarifying this distinction, we guide readers from general curiosity to technical mastery of the honing rod’s role in advanced manufacturing.
This dual-meaning approach ensures the article captures diverse search intents, from novices searching for honing rod basics to professionals seeking in-depth CNC insights, aligning with Google’s AIO focus on user intent and comprehensive content.
Fundamentals of the Honing Process: Precision Beyond Alternatives
Honing is a precision abrasive machining process that refines internal cylindrical bores using honing rods. The honing rod, guided by a rotating and reciprocating tool, removes small amounts of material to achieve three critical engineering objectives:
- Geometric Correction: Honing rods correct bore imperfections such as ovality, taper, waviness, or straightness deviations, ensuring a perfectly round and straight bore.
- Dimensional Accuracy: Industrial honing rods deliver tolerances as tight as ±0.001–0.002 mm, critical for components requiring precise fits, like pistons or valve spools.
- Surface Finish Control: The honing rod creates a cross-hatch pattern, engineered to retain lubrication and minimize friction, achieving surface roughness (Ra) as low as 0.025 µm.
Honing vs. Competing Processes
The honing rod’s unique capabilities set it apart from other finishing methods:
- Internal Grinding: Removes significant material but generates heat, risking surface stress. Honing rods offer gentler, precision finishing with minimal thermal impact.
- Lapping: Excels at flat or spherical surfaces but not internal bores. Honing rods are ideal for cylindrical geometries.
- Reaming: Sizes holes quickly but lacks the geometric precision and surface finish of honing rods. Single-pass honing rods combine reaming’s speed with honing’s accuracy.
Table 1: Comparative Analysis of Precision Finishing Processes
Feature | Honing (Honing Rod) | Internal Grinding | Lapping | Reaming |
Primary Goal | Geometric correction, surface texture | Stock removal, size/location | Ultimate flatness, finish | Hole sizing |
Material Removal | Low (0.01–0.2 mm) | High (thousandths of inch) | Very low (microns) | Moderate |
Tool Contact | Surface (honing rod) | Line/Point | Surface | Cutting Edge |
Tolerances | ±0.001–0.002 mm (IT6–IT7) | ±0.002–0.005 mm (IT5–IT6) | ±0.0005 mm | ±0.005–0.01 mm (IT7–IT9) |
Surface Finish (Ra) | 0.025–0.8 µm | 0.4–1.6 µm | <0.1 µm | 0.8–3.2 µm |
Position Correction | No (follows bore axis) | Yes | No | No |
Alt-Text: Comparison table of honing, grinding, lapping, and reaming, highlighting honing rod advantages in bore precision and surface texture. |
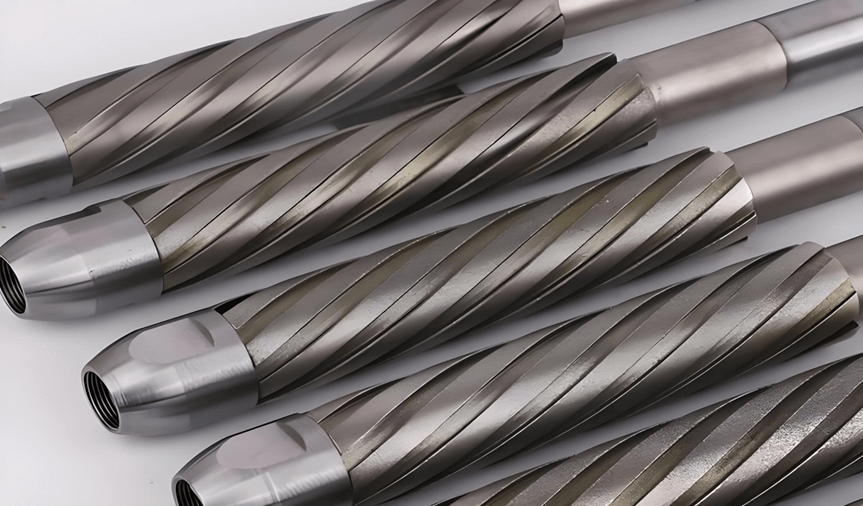
The Anatomy of a CNC Honing Ecosystem
CNC honing integrates honing rods, tooling, fluids, and automation to deliver precision and efficiency. Each component is engineered to optimize the honing rod’s performance.
Honing Tools and Mandrels
The honing tool’s mandrel positions the honing rod precisely within the bore. Multi-stone mandrels handle complex geometries, while single-pass honing rods, coated with diamond or CBN, size and finish bores in one stroke, ideal for high-volume production like engine crank bores. Leading manufacturers like Sunnen and Nagel offer versatile honing rod systems for through-holes and blind bores.
The Science of the Honing Rod
The honing rod—an abrasive stick—is tailored to the workpiece material:
- Aluminum Oxide (AO): Cost-effective for softer metals like aluminum or brass.
- Silicon Carbide (SC): Sharp and friable, ideal for cast iron and mild steel.
- Cubic Boron Nitride (CBN): For hardened steels and superalloys, offering thermal stability.
- Diamond: For ultra-hard materials like ceramics, carbide, or chrome plating.
Grit size (80–150 for roughing, 400+ for finishing) and bond type (vitrified, resin, or metal) optimize the honing rod for specific applications, balancing cutting speed and surface quality.
Table 2: Honing Rod Abrasive Selection Guide
Abrasive | Abbreviation | Workpiece Material | Key Characteristics |
Aluminum Oxide | AO | Aluminum, Brass, Bronze | Cost-effective, general-purpose |
Silicon Carbide | SC | Cast Iron, Mild Steel | Sharp, friable, self-sharpening |
CBN | CBN | Hardened Steels, Superalloys | High thermal stability, durable |
Diamond | D | Carbide, Ceramics, Chrome | Hardest material, wear-resistant |
Alt-Text: Guide to selecting honing rod abrasives for CNC honing, detailing material applications and performance. |
Honing Fluids: The Unsung Hero
Honing oils cool the honing rod, flush away swarf, and lubricate the bore interface, enhancing surface finish and extending honing rod life. Modern chlorine-free fluids reduce environmental impact, aligning with sustainable manufacturing trends.
Tool Wear and Maintenance
Honing rods wear gradually, requiring periodic replacement. CNC systems monitor honing rod condition, ensuring consistent performance. Advanced honing rod designs, like diamond-plated single-pass tools, offer extended life for high-volume applications.
The Power of CNC Honing: Automation and Precision
CNC technology transforms the honing rod into a precision instrument, automating the process for consistency and efficiency. A typical CNC honing cycle includes:
- Programming: Operators input bore specifications and honing rod parameters.
- Gauging: Sensors measure initial bore conditions, detecting errors like taper.
- Execution: The honing rod rotates and reciprocates under CNC control, applying precise pressure.
- Monitoring: Real-time adjustments compensate for honing rod wear, ensuring accuracy.
Advantages of CNC Honing Rods:
Precision: Honing rods achieve micron-level tolerances across thousands of parts.
Efficiency: Automation reduces labor and cycle times, boosting throughput.
Safety: Enclosed systems protect operators from moving honing rods.
Cost Savings: Precise honing rods minimize scrap and extend component life, reducing warranty costs.
CNC honing rods enable advanced techniques like plateau honing, creating pre-broken-in surfaces that reduce initial wear in engines or hydraulic systems.
Mastering the Surface: The Cross-Hatch Pattern
The honing rod’s hallmark is the cross-hatch pattern, a functional texture formed by its rotation and reciprocation. The pattern’s angle (45–60°) is precisely controlled by CNC settings, optimizing performance for specific applications.
Functions of the Cross-Hatch:
- Oil Retention: Valleys created by honing rods hold lubricating oil, reducing friction.
- Piston Ring Seating: The texture ensures proper sealing, maximizing engine compression.
- Heat Dissipation: Increased surface area aids cooling in high-friction zones.
- Wear Reduction: The pattern minimizes abrasive contact, extending component life.
Plateau Honing: A secondary honing rod cycle with finer abrasives flattens sharp peaks, creating stable plateaus while retaining oil-holding valleys. This reduces initial wear, accelerates ring seating, and enhances durability.
The cross-hatch pattern also serves as a diagnostic tool. Uniform patterns indicate optimal honing rod performance; irregularities like stacking or circular marks suggest tool wear or CNC faults, enabling proactive maintenance.
CNC Honing in Action: Industry Applications
The honing rod’s precision powers critical components across industries, ensuring performance and reliability.Automotive and High-Performance Engines
- Applications: Cylinder bores, connecting rod bores, fuel injector bodies.
- Why Honing Rods Matter: Honing rods create perfectly round bores with cross-hatch patterns, ensuring piston sealing for maximum horsepower, fuel efficiency, and emissions control. Torque plates simulate operational stress, optimizing honing rod results.
- Value: Honing rods enhance engine longevity and performance, surpassing OEM standards in rebuilt or high-performance engines.
Aerospace and Defense
- Applications: Hydraulic actuators, turbine shafts, missile components.
- Why Honing Rods Matter: Honing rods deliver leak-free, reliable bores for landing gear and flight controls, handling exotic alloys like titanium or Inconel without thermal damage.
- Value: Micron-level precision from honing rods ensures safety and extends maintenance intervals.
Hydraulics and Pneumatics
- Applications: Cylinder bores, valve bodies, pump housings.
- Why Honing Rods Matter: Honing rods create precise, lubricated surfaces for efficient fluid power systems, minimizing leaks and wear.
- Value: Honing rods restore worn cylinders cost-effectively, extending seal and component life.
Oil and Gas
- Applications: Downhole drilling tools, high-pressure valves.
- Why Honing Rods Matter: Honing rods ensure durability in extreme conditions, handling corrosive fluids and high pressures.
- Value: Reliable honing rod-finished components reduce downtime and costly failures.
Medical and Precision Instruments
- Applications: Surgical tool bores, precision pump components.
- Why Honing Rods Matter: Honing rods deliver ultra-precise bores for biocompatible materials, ensuring reliability in life-critical devices.
- Value: Honing rods support stringent regulatory standards, enhancing patient safety.
Table 3: Honing Rod Applications Across Industries
Industry | Applications | Honing Rod Benefit | Impact |
Automotive | Cylinder Bores | Precise geometry, oil retention | Improved efficiency, longevity |
Aerospace | Actuators, Shafts | Leak-free, reliable bores | Enhanced safety, reduced maintenance |
Hydraulics | Cylinder Bores | Tight tolerances, smooth finish | Leak prevention, extended seal life |
Oil & Gas | Drilling Tools | Durability in harsh conditions | Reduced downtime |
Medical | Surgical Tools | Ultra-precise bores | Regulatory compliance, reliability |
Alt-Text: Table showcasing honing rod applications in automotive, aerospace, hydraulics, oil & gas, and medical industries, highlighting precision benefits. |
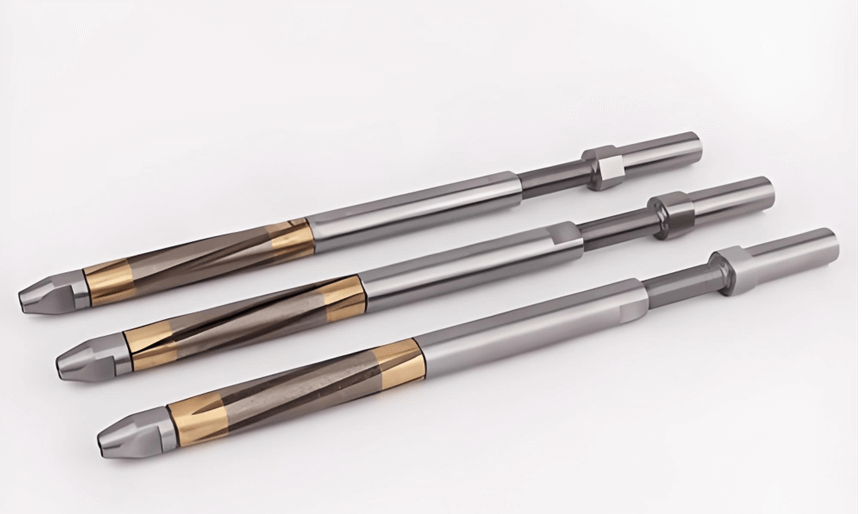
The Future of Honing: Smart Manufacturing and Industry 4.0
The honing rod is at the forefront of manufacturing’s digital transformation, integrating with Industry 4.0 technologies for smarter, more sustainable production.
Smart Honing Systems
Modern CNC honing machines, equipped with honing rods, connect to factory-wide systems via IoT protocols, enabling real-time production tracking and workflow optimization. Key advancements include:
In-Process Gauging: Sensors measure bore dimensions during honing rod operation, ensuring instant accuracy.
Acoustic Emission Sensors: Detect honing rod wear by analyzing cutting sounds, preventing defective parts.
Emerging Sensors: Eddy current or ultrasonic probes monitor honing rod performance, insensitive to fluids, enhancing quality control.
AI and Data Analytics
AI algorithms analyze honing rod data (force, torque, vibration) to:
- Predict Maintenance: Forecast honing rod wear or machine servicing needs, minimizing downtime.
- Optimize Processes: Adjust honing rod parameters for peak efficiency and quality.
- Digital Twins: Virtual models of honing rods and machines enable simulations, reducing trial-and-error and supporting autonomous operation.
Sustainability Trends
Eco-friendly honing rod processes use biodegradable fluids and energy-efficient CNC systems, aligning with green manufacturing goals. Recycling programs for worn honing rods further reduce environmental impact.
Case Study: Smart Honing in Action
A leading automotive manufacturer recently integrated AI-driven honing rod systems, reducing cycle times by 15% and scrap rates by 20%. Real-time honing rod monitoring ensured consistent quality across 10,000 engine cylinders monthly, showcasing Industry 4.0’s potential.
Challenges and Solutions in Honing Rod Technology
While honing rods are highly effective, challenges persist:
- Tool Wear: Honing rods wear over time, affecting precision. Solution: AI-driven wear detection and diamond-plated honing rods for longer life.
- Material Diversity: Hard or brittle materials challenge honing rod selection. Solution: Advanced CBN and diamond honing rods tailored to exotic alloys.
- Operator Skill: Manual honing relies on expertise. Solution: CNC automation standardizes honing rod performance, reducing skill dependency.
Future innovations, like self-regenerating honing rods or nanotechnology-enhanced abrasives, promise to address these challenges, further elevating precision and efficiency.
Conclusion
The honing rod, far from its culinary counterpart, is the abrasive cornerstone of CNC honing, delivering precision that powers automotive engines, aerospace systems, hydraulic cylinders, and medical devices. By perfecting bore geometry, achieving micron-level tolerances, and creating functional cross-hatch patterns, honing rods ensure component reliability and performance. In the Industry 4.0 era, honing rods integrate with AI, sensors, and sustainable fluids, becoming smarter and greener. From traditional craftsmanship to cutting-edge technology, the honing rod shapes the future of precision manufacturing. Explore honing rod solutions for your CNC needs at want.net.
FAQ:
1. What is a honing rod in CNC machining?
A honing rod in CNC machining refers to an abrasive stone or stick used within a honing tool to refine internal cylindrical bores. Unlike the culinary honing rod used for knife sharpening, industrial honing rods remove minute material (0.01–0.2 mm) to achieve precise geometry, tight tolerances, and functional surface finishes for components like engine cylinders and hydraulic actuators.
2. How does a honing rod differ from a kitchen honing steel?
A kitchen honing rod (or honing steel) is a steel or ceramic tool that realigns a knife’s edge without significant material removal. In contrast, an industrial honing rod is an abrasive component in CNC honing, designed to precisely shape and finish internal bores in materials like steel, aluminum, or ceramics, achieving tolerances as tight as ±0.001 mm.
3. What materials are used in industrial honing rods?
Industrial honing rods are made from abrasives like:
- Aluminum Oxide (AO): For softer metals like aluminum or brass.
- Silicon Carbide (SC): For cast iron and mild steel.
- Cubic Boron Nitride (CBN): For hardened steels and superalloys.
- Diamond: For ultra-hard materials like ceramics or chrome.
The choice depends on the workpiece material and desired finish.
4. Why is the cross-hatch pattern created by honing rods important?
The cross-hatch pattern, formed by the honing rod’s rotation and reciprocation, creates microscopic valleys that retain lubricating oil, reducing friction and wear. This pattern, typically at 45–60° angles, ensures proper piston ring seating in engines, enhances sealing in hydraulic systems, and improves component durability.
5. What industries rely on honing rods for precision manufacturing?
Honing rods are critical in:
- Automotive: For cylinder bores and fuel injector bodies.
- Aerospace: For hydraulic actuators and turbine shafts.
- Hydraulics: For cylinder bores and valve bodies.
- Oil & Gas: For drilling tools and high-pressure valves.
- Medical: For surgical tool bores and precision pumps.
They ensure reliability and performance in high-stakes applications.
6. How does CNC technology enhance honing rod performance?
CNC automation controls honing rod rotation, reciprocation, and pressure, achieving micron-level precision and repeatability. Real-time sensors monitor honing rod wear and bore dimensions, reducing errors and labor while enabling advanced techniques like plateau honing for optimized surface finishes.
7. What is plateau honing, and how do honing rods contribute?
Plateau honing is a secondary process using finer honing rods to flatten sharp peaks on a bore’s surface while retaining oil-holding valleys. This creates a pre-broken-in surface, reducing initial wear, improving seal performance, and extending component life in applications like engines and hydraulics.
Reference:
https://zh.wikipedia.org/wiki/%E7%8F%A9%E7%A3%A8
https://zh.wikipedia.org/wiki/%E6%9C%BA%E6%A2%B0%E5%8A%A0%E5%B7%A5
Other Articles You Might Enjoy
- Elevating Surface Finish of CNC Machining Parts with High-Speed Techniques
High-speed cutting techniques have revolutionized CNC machining, offering not only increased production efficiency but also superior surface finishes on machined parts. The appeal of high-speed machining lies in its ability…
- How Can Surface Finish Be Optimized in CNC Machining of Stainless Steel?
What Factors Affect Surface Finish in CNC Machining of Stainless Steel? The quality of the surface finish in CNC machining stainless steel is influenced by a variety of factors ranging…
- Precision Perfected: The Science and Strategy of Honing Oil in CNC Machining
Introduction: The Art and Science of Precision Machining In the high-stakes world of modern manufacturing, precision is not just a goal—it’s the cornerstone of success. Industries such as aerospace, automotive,…
- Precision Perfected: Elevating CNC Surface Finishing with Vapor Honing Technology
Introduction In the competitive landscape of precision CNC machining, achieving a flawless surface finish efficiently and consistently remains a critical challenge. Manual deburring is labor-intensive, time-consuming, and prone to human…
- Mastering Surface Perfection: The Role of Honing Tools in Modern CNC Machining
In the dynamic world of Computer Numerical Control (CNC) machining, achieving precise dimensions and impeccable surface characteristics is as critical as primary shaping operations. While processes like boring and reaming…