Examining the Distinctive Functions and Design Considerations of Jigs and Fixtures
Manufacturing processes often rely on two critical tools: jigs and fixtures. While these terms are often used interchangeably, it is important to understand their distinctive functions and design considerations. Jigs and fixtures play a vital role in enhancing manufacturing efficiency, reducing production costs, and ensuring precise results. In this article, we will explore the differences between jigs and fixtures and delve into their design considerations, shedding light on these indispensable components of various manufacturing technologies.
Jigs: Enhancing Reproducibility and Precision
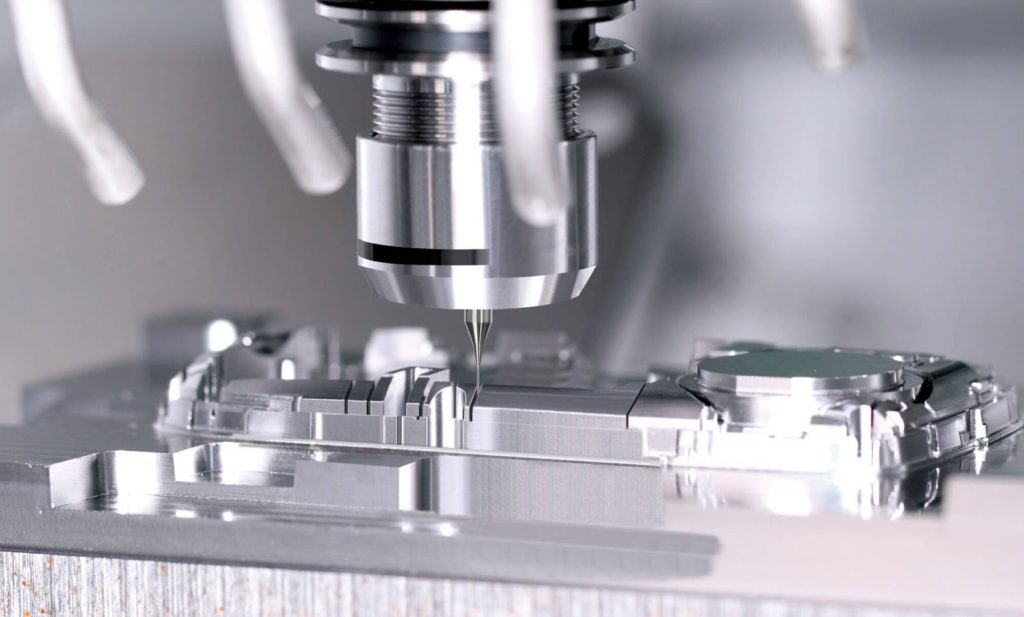
Jigs are tools specifically designed to hold and locate workpieces during the production process. They serve as a reliable support system, guiding cutting tools with the aim of increasing reproducibility, precision, and productivity in manufacturing operations.
For instance, consider a drill jig, a common example of a jig. It guides the drill, enabling the creation of holes in predetermined locations. The use of drill jigs significantly boosts manufacturing efficiency by ensuring accurate hole placement. Various types of jigs are utilized, each catering to specific purposes and accommodating different workpiece shapes and sizes.
Types of Jigs
Let’s explore the various types of jigs commonly employed in manufacturing:
- Template Jig: The simplest form of a jig, it consists of a plate with holes that serve as a template for machining the workpiece. The holes on the template guide the drill, allowing the same holes to be drilled on the workpiece.
- Plate Jig: An improvement on the template jig, the plate jig includes additional holes on its surface. This design enables precise hole spacing when drilling larger components.
- Channel Jig: The channel jig features a cross-sectional design resembling a channel. By rotating the knurled knob, the component is located and securely clamped inside the channel. The drill bush serves as a guide for the cutting tool.
- Diameter Jig: This type of jig is specifically used for drilling radial holes in cylindrical or spherical workpieces.
- Leaf Jig: A leaf jig facilitates the loading and unloading of workpieces, streamlining the manufacturing process.
- Ring Jig: When drilling holes in circular flanged items, a ring jig comes into play. The tool is guided through drill bushes while the workpiece remains securely attached.
- Box Jig: The box jig, with its box-like design, tightly holds the workpiece, allowing drilling or machining from multiple angles simultaneously.
Fixtures: Enabling Automation and Stability
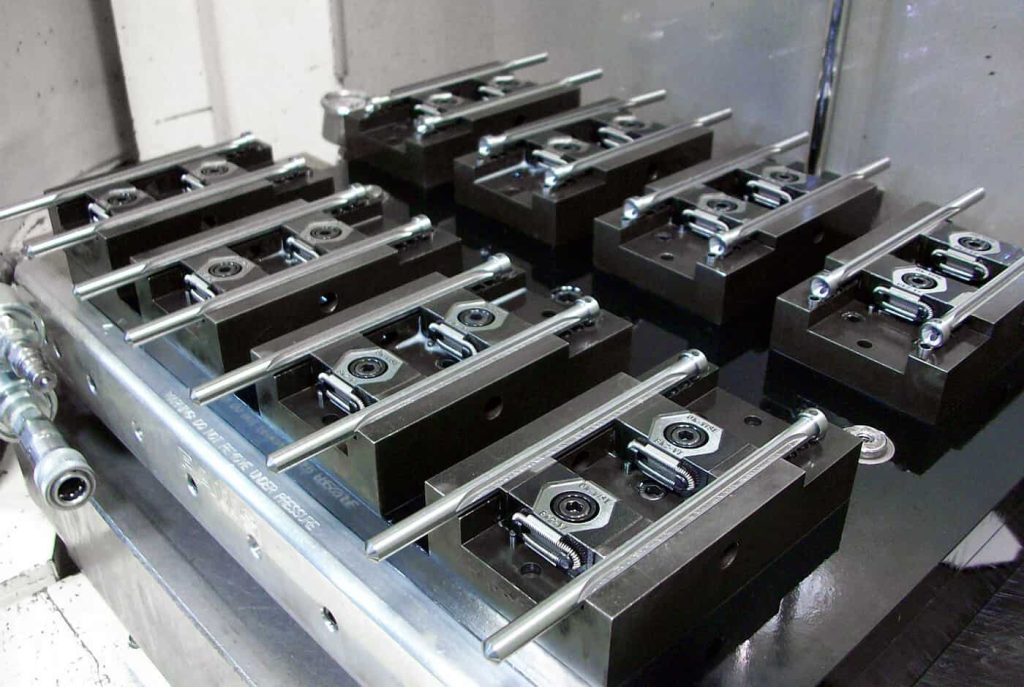
Fixtures, on the other hand, are indispensable components of automated industrial processes. They are specifically designed to provide support and guidance to workpieces during manufacturing operations, ensuring accurate and consistent results.
For instance, in automobile assembly lines, fixtures play a vital role in holding and guiding automobiles during welding and assembly processes. They not only enable automation but also facilitate quality checks by holding products in place while optical or laser scans examine them. Fixtures are ubiquitous in production facilities, contributing to streamlined and efficient manufacturing processes.
Types of Fixtures
Let’s explore the various types of fixtures commonly used in manufacturing:
- Turning Fixture: Lathes typically employ job holding devices like chucks and collectors for regular workpieces. However, irregularly shaped components pose a challenge. Turning fixtures come to the rescue, securely holding such workpieces in place on the spindle’s nose or a faceplate.
- Milling Fixture: Milling fixtures hold workpieces in place while milling operations are carried out. They are fixed on the spindle’s nose or a faceplate, allowing precise positioning of the workpiece in relation to the cutter. The table is shifted and positioned to achieve the desired results. Before commencing the process, the workpieces are placed in the fixture’s base and clamped.
- Broaching Fixture: Broaching fixtures are utilized to locate, hold, and support workpieces during operations such as keyway broaching and hole broaching. They ensure precise machining of internal pull-type holes and may involve the use of clamping plates as fixtures.
- Grinding Fixture: Grinding machines employ a variety of fixtures to locate, hold, and support workpieces during the grinding process. These fixtures work in conjunction with work-holding devices like chucks and mandrels, facilitating precise grinding operations.
- Boring Fixture: Unlike milling fixtures, boring fixtures do not require the same level of robustness, as they are not subjected to heavy cutting loads. They primarily hold workpieces in place during the boring process, ensuring accuracy and stability.
- Indexing Fixture: In cases where multiple surfaces of a component require machining with uniform spacing, indexing fixtures come into play. These fixtures incorporate an indexing mechanism that allows the workpiece to be rotated or positioned a specific number of times, ensuring consistent machining.
- Tapping Fixture: Tapping fixtures are designed to hold and stabilize workpieces during the cutting of internal threads in drilled holes. They prove especially useful for machining unevenly shaped and imbalanced parts, particularly in mass production scenarios.
- Duplex Fixture: A duplex fixture holds two identical components simultaneously, enabling them to be machined at different stations simultaneously. This design significantly improves productivity by reducing machining time.
- Welding Fixture: Welding fixtures play a critical role in ensuring the alignment and stability of welded structures during the welding process. They provide clamping and support to various components, minimizing distortion. Welding fixtures must be robust and rigid enough to withstand the forces involved in welding operations.
- Assembly Fixture: Assembly fixtures securely hold various parts of an assembly in their correct relative positions, facilitating accurate alignment during the assembly process.
Jigs vs. Fixtures: Differentiating Their Functions
Understanding the distinction between jigs and fixtures is essential, as they serve different purposes. Although often used interchangeably, jigs and fixtures have separate functions in the manufacturing process.
Jigs primarily guide cutting tools to predetermined locations on the workpiece, enhancing reproducibility and precision. They securely hold the workpiece in place while facilitating accurate CNC machining. Unlike fixtures, jigs do not hold the cutting tool itself.
In contrast, fixtures provide support and guidance to workpieces, ensuring accurate and consistent results during automated manufacturing processes. They hold the workpiece in place, maintaining stability and precise positioning during machining operations.
The Significance of Jigs and Fixtures in CNC Machining
In CNC machining, the careful selection and utilization of jigs and fixtures significantly improve the fabrication process. They allow for smooth operation, simplify production, and enable quick transitions between processes. Jigs and fixtures compensate for the limitations of CNC machines when working with specific parts, ensuring secure mounting and reliable positioning during the machining process.
Roles of Jigs and Fixtures in CNC Machining
Let’s explore the various roles that jigs and fixtures play in custom CNC machining:
- Part Holding: Jigs and fixtures securely hold the workpiece during the machining process. Custom-designed to fit the specific part, they provide secure and precise positioning. Fixtures such as vises, chucks, centers, and milling fixtures ensure stability and prevent inaccuracies caused by tool pull-out or vibration.
- Parts Protection: Jigs and fixtures play a crucial role in protecting the workpiece during machining. They help maintain the desired surface finish and prevent damage caused by metal chips or swarf generated during the machining process. Customized fixtures like sleeves, bushings, and masking fixtures are designed to protect the surface finish of the part, ensuring consistent quality.
- Location Control and Foolproofing: Jigs and fixtures are essential for maintaining dimensional and location accuracy during machining. They ensure the workpiece remains in the correct position and orientation throughout the process, reducing errors caused by human factors. Fixtures control location, orientation, and stability by constraining degrees of freedom in the workpiece using pins, clamps, planes, and fasteners. This precise location control enables machining of specific features that may be challenging to access due to mounting constraints.
- Part Consistency: Fixtures enable the machining of multiple parts while maintaining consistent quality. They ensure that key features, such as flatness, parallelism, and perpendicularity, are controlled and maintained uniformly across all parts. This consistency is crucial for meeting quality standards and ensuring the proper functioning of the final products.
- Setup Reduction: Fixtures eliminate the tedious process of inspecting while loading a part, saving valuable setup time for other value-adding processes. A well-designed fixture tailored to a specific part streamlines the CNC process, making it a plug-and-play operation. Operators only need to load the workpiece, as the fixture takes care of location control and part referencing. This setup reduction technique allows manufacturers to allocate more time to value-adding processes, enhancing overall productivity.
Basic Methods and Steps for Jig and Fixture Design
Designing jigs and fixtures requires careful planning and consideration. Let’s explore the basic methods and steps involved in their design:
- Pre-design Preparation: Gather the necessary information, including design specifications, finished parts diagrams, blank diagrams, and process routes. Understand the requirements of each process, such as positioning and clamping programs, previous process machining content, machine tools used, tools and inspection gauges, machining allowances, and cutting amounts.
- Production Batch and Quantity: Determine the production batch size and the number of jigs and fixtures required for efficient manufacturing.
- Machine Lathe Parameters: Understand the technical parameters of the machine lathe used, including its performance, specifications, accuracy, and the dimensions of the contact points with the jig or fixture.
- Material Selection: Choose appropriate materials for constructing the jigs and fixtures based on the project’s requirements. Options include hardened steel, gray cast iron, plastic, carbide, epoxy resins, stainless steel, bronze, and low-melt alloy steel.
Design Considerations for Jigs and Fixtures
To create effective jig and fixture designs, careful attention should be given to the following considerations:
- Blank Allowance: Consider the required blank size to avoid interference during the machining process. Prepare a blank drawing and leave sufficient space for machining.
- Chip Evacuation: Ensure smooth chip evacuation within the fixture. Compact fixture designs often overlook the storage of chips generated during machining, leading to poor chip flow and subsequent difficulties in processing. Address chip evacuation issues from the outset to maintain efficiency and ease of operation.
- Openness: Design fixtures with openness in mind to facilitate easy loading and unloading of workpieces. Neglecting this aspect can lead to time-consuming and labor-intensive operations for operators.
- Theoretical Design Principles: Each jig and fixture undergoes countless clamping and unclamping actions, emphasizing the need for accuracy retention. Avoid designs that go against the fundamental principles of jigs and fixtures, as they may only yield short-term benefits and prove unsustainable in the long run. A well-designed jig or fixture should withstand the test of time.
- Replaceability of Positioning Elements: Consider the replaceability of positioning elements, as these elements may experience significant wear over time. Design them for quick and easy replacement, particularly for larger parts, to minimize downtime during maintenance.
In conclusion, jigs and fixtures are indispensable tools in the manufacturing process. Their distinctive functions and design considerations make them essential for enhancing efficiency, reducing costs, and ensuring precise results. By carefully selecting and designing jigs and fixtures, manufacturers can optimize their manufacturing processes, achieving smooth operations, simplified production, and improved overall productivity.
Recommended Reads:
- Metal Prototype: Exploring Four Metal Rapid Prototyping Methods
- Tapped Holes: A Guide to Creating Threaded Connections
- Feed Rate And Cutting Speed: What’s The Difference In CNC Machining
- Choosing the Right CNC Machining Services in China
- Types Of CNC Machine Tools: A Comprehensive Guide
Related Posts
- Difference Between CNC and Manual Machining
Humans do not like change. Some people were unwilling to let go of their slide rules after calculators were created. While CNC machining has been around for decades, some still…
- How To Adapt Fixtures and Jigs for Intelligent Manufacturing
At the forefront of modern production lie intelligent manufacturing systems, meticulously crafted to meet the flexible demands of cnc machining various parts and swiftly adapt to the ever-changing needs of…
- Precision CNC Machining of Steel: High-Volume Production
Precision CNC Machining and High-Volume Production As an integral part of modern manufacturing processes, Precision Computer Numerical Control (CNC) machining brings about unmatched accuracy and consistency in the production of…