Introduction: The Promise and Challenge of Plastic Lumber
Plastic lumber, forged from recycled plastics, is a game-changer for manufacturers, designers, and engineers across industries. Its resistance to rot, moisture, insects, and UV degradation makes it ideal for harsh environments where traditional wood fails. From marine docks to outdoor furniture, plastic lumber offers unmatched durability and sustainability. However, CNC machining plastic lumber is not a simple swap for woodworking. Its unique properties—low stiffness, high thermal expansion, and heat sensitivity—create a paradox: it looks like wood but behaves like a thermoplastic under the CNC router. Treating it as a wood substitute risks material waste, poor finishes, and project failure.
Success in CNC machining plastic lumber demands a shift in approach, embracing material science, thermal management, and precision techniques. This comprehensive guide transforms these challenges into opportunities, offering expert strategies to master CNC machining plastic lumber. From material selection to advanced toolpaths, we’ll explore how to create high-value, precision-engineered products that leverage plastic lumber’s strengths. Whether you’re crafting marine components or architectural signage, this journey from challenge to excellence unlocks a world of possibilities.
Chapter 1: Understanding Plastic Lumber: A Material Unlike Wood
The foundation of successful CNC machining plastic lumber lies in recognizing it as a distinct engineering material, not a wood alternative. Misconceptions about its properties lead to flawed designs and fabrication errors. This chapter delves into its composition, performance characteristics, and design considerations.
1.1 Composition and Variants of Plastic Lumber
Plastic lumber is typically made from High-Density Polyethylene (HDPE), sourced from recycled items like milk jugs, shampoo bottles, and detergent containers. Unlike Wood-Plastic Composites (WPC), which blend plastics with organic fibers, 100% plastic lumber is fully waterproof and immune to rot, mold, and insects. Other polymers, such as Polyvinyl Chloride (PVC), Polypropylene (PP), or Acrylonitrile Butadiene Styrene (ABS), are also used, each offering unique properties. Additives like UV inhibitors prevent solar degradation, while colorants ensure consistent, through-body hues. For enhanced strength, manufacturers may incorporate chopped fiberglass or co-extrude continuous fiberglass rebar.Table 1: Common Plastic Lumber Materials and Properties
Material | Common Use | Key Properties | Melting Point (°F/°C) | Stiffness (psi) |
HDPE | Outdoor furniture, marine | Waterproof, flexible, UV-resistant | 220–230 / 104–108 | 112,000–114,000 |
PVC | Signage, structural | Rigid, fire-resistant | 176–212 / 80–100 | 400,000–500,000 |
PP | Industrial components | Lightweight, chemical-resistant | 266–340 / 130–171 | 200,000–300,000 |
ABS | Decorative elements | Impact-resistant, smooth finish | 221–248 / 105–120 | 300,000–400,000 |
1.2 Performance Gaps and Design Solutions
Plastic lumber’s unique properties require specific design adjustments during CNC machining:
- Low Stiffness: Plastic lumber is significantly less rigid than wood. For example, HDPE’s modulus of elasticity (112,000–114,000 psi) is a fraction of wood’s (1,500,000 psi for oak). This causes sagging in long spans, requiring shorter spans, thicker profiles, or reinforced plastic lumber.
- High Thermal Expansion: Plastic lumber expands and contracts with temperature changes far more than wood. For instance, HDPE expands by 0.0001 inches per inch per °F, compared to wood’s 0.00002 inches. Designs must include expansion gaps or slotted fastener holes to prevent buckling.
- Heat Sensitivity: With a low melting point (e.g., 220–230°F for HDPE), plastic lumber softens during CNC machining if heat isn’t managed, impacting tool performance and part accuracy.
To succeed, designers must treat plastic lumber as a thermoplastic, leveraging its durability while addressing these limitations through informed design and CNC machining strategies.
1.3 Practical Design Tips
- Structural Reinforcement: Use fiberglass-reinforced plastic lumber for load-bearing applications like decking or marine fenders.
- Thermal Planning: Account for thermal expansion in outdoor installations by calculating expansion gaps based on local temperature ranges.
- Material Selection: Choose PVC for rigid signage or HDPE for flexible, impact-resistant components.
By understanding these properties, fabricators can optimize CNC machining plastic lumber for precision and durability.
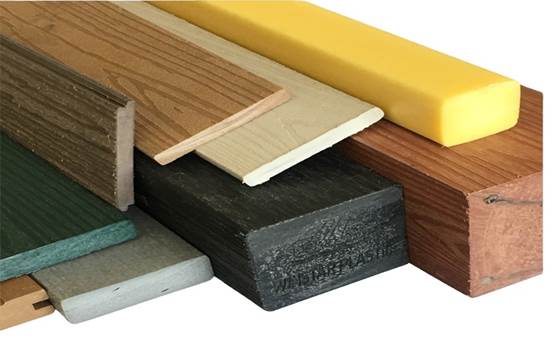
Chapter 2: Mastering Thermal Control in CNC Machining Plastic Lumber
The primary challenge in CNC machining plastic lumber is managing frictional heat, which can exceed the material’s low melting point, causing melting, tool clogging, and poor surface finishes. Effective thermal control hinges on tooling, machining parameters, and chip evacuation.
2.1 Tooling for Plastic Lumber
Standard wood or metal tools fail in CNC machining plastic lumber. Specialized tools are essential:
- O-Flute Bits: Single-flute or two-flute O-flute bits, with polished, rounded channels, are ideal for soft plastics like HDPE. They maximize chip evacuation, reducing heat buildup.
- Up-Cut Spirals: These pull chips upward, clearing the cutting zone, unlike down-cut bits that trap chips and generate heat.
- Fewer Flutes: A single-flute tool creates larger chips, carrying more heat away, critical for CNC machining plastic lumber.
2.2 Optimizing Machining Parameters
Balancing spindle speed, feed rate, and depth of cut prevents thermal issues:
- Low RPM, High Feed Rate: High spindle speeds (e.g., 20,000 RPM) cause rubbing, generating excessive heat. For CNC machining plastic lumber, use 10,000–14,000 RPM and high feed rates (e.g., 100–200 inches per minute) to ensure clean cuts.
- Chip Load: Target a chip load of 0.005″–0.010″ for a 1/4″ tool. Chip load = Feed Rate / (RPM × Number of Flutes). For example, a single-flute tool at 12,000 RPM and 120 IPM yields a 0.010″ chip load, ideal for heat removal.
- Shallow Cuts: Limit depth to half the tool’s diameter (e.g., 1/8″ for a 1/4″ bit) and use multiple passes to reduce heat and tool stress.
2.3 Advanced Chip Evacuation Techniques
Forced Air Blast: A high-pressure air stream (80–100 psi) clears chips and cools the cutting zone, essential for CNC machining plastic lumber.
Ramping Toolpaths: Gradual entries reduce heat and tool wear compared to vertical plunges.
Vacuum Systems: High-volume dust collection systems remove chips, enhancing cooling and visibility.
2.4 Case Study: Optimizing a Marine Component
A marine manufacturer machining plastic lumber for dock fenders faced melting issues with a 1/4″ two-flute wood bit at 18,000 RPM. Switching to a single-flute O-flute bit at 12,000 RPM, a 150 IPM feed rate, and a 0.125″ depth of cut, combined with an air blast, eliminated melting and improved edge quality by 35%. This example underscores the importance of tailored parameters in CNC machining plastic lumber.Table 2: Recommended CNC Parameters for Plastic Lumber
Material | Tool Type | RPM | Feed Rate (IPM) | Chip Load (in) | Depth of Cut (in) |
HDPE | Single O-Flute | 10,000–14,000 | 100–200 | 0.005–0.010 | 0.125–0.250 |
PVC | Two O-Flute | 12,000–16,000 | 80–150 | 0.004–0.008 | 0.100–0.200 |
PP | Single O-Flute | 10,000–13,000 | 120–180 | 0.006–0.012 | 0.125–0.250 |
ABS | Two O-Flute | 14,000–18,000 | 100–160 | 0.005–0.009 | 0.100–0.200 |
Chapter 3: Achieving Precision and Flawless Finishes
Beyond thermal control, CNC machining plastic lumber requires techniques to ensure dimensional accuracy and smooth surfaces, addressing warping, burring, and cracking.
3.1 Common Precision Challenges
Warping: Internal stresses or heat cause deformation, especially in thin parts.
Burring: HDPE’s softness leads to burrs along cut edges, affecting aesthetics.
Cracking: High cutting forces or dull tools can chip brittle plastics like PVC.
3.2 Solutions for Precision
Stable Workholding: Vacuum tables provide even pressure for sheets, while high-strength tape or screws secure smaller parts. Avoid overtightening to prevent stress-induced warping.
Sharp Tools: A sharp O-flute bit is critical for clean cuts in CNC machining plastic lumber. Replace or sharpen tools regularly.
Optimized Toolpaths: Use a roughing pass leaving 0.02″ stock, followed by a full-depth finishing pass. Machine both sides to balance stresses.
Manual Deburring: A utility knife or deburring tool removes residual burrs for a polished finish.
3.3 Advanced Techniques
Coolant Alternatives: For large-scale CNC machining plastic lumber, mist cooling with water-based solutions can supplement air blasts, maintaining low temperatures without residue.
Toolpath Simulation: Use CAM software to simulate toolpaths, identifying potential stress points before machining.
Stress-Relieving Annealing: For high-precision parts, anneal plastic lumber at 180°F for 1–2 hours before machining to reduce internal stresses.
3.4 Example: Signage Production
A signage company machining plastic lumber for outdoor displays struggled with burring. By adopting a two-stage toolpath (roughing at 0.15″ depth, finishing at 0.02″ stock) and using a sharp single-flute bit, they achieved crisp edges, reducing manual deburring time by 40%. This highlights the value of refined strategies in CNC machining plastic lumber.
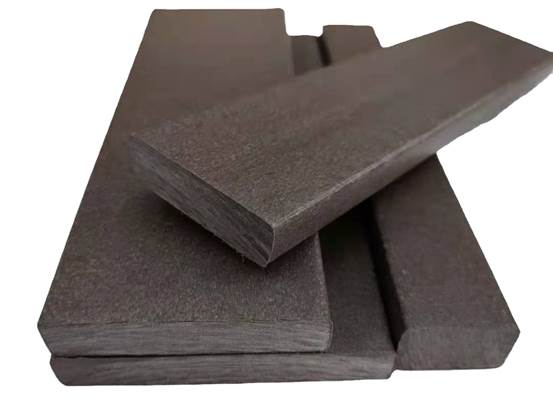
Chapter 4: Applications of CNC Machined Plastic Lumber
Mastering CNC machining plastic lumber unlocks its potential for diverse, high-performance applications, leveraging its durability and versatility.
4.1 Marine and Waterfront Construction
Plastic lumber excels in marine environments, resisting water, salt, and borers. CNC machining enables:
- Fender Systems: Precise profiles for docks and piers, absorbing vessel impacts.
- Boat Components: Custom panels, hatches, and platforms with tight tolerances.
- Seawalls: Interlocking panels machined for structural integrity.
4.2 Outdoor Furniture and Public Amenities
Plastic lumber’s splinter-free, weatherproof nature is ideal for public spaces. CNC machining creates:
- Engraved Signage: Permanent text or logos for parks and trails.
- Decorative Elements: Intricate patterns for benches and tables.
- Ergonomic Designs: Contoured seats for comfort and aesthetics.
4.3 High-End Signage and Architectural Elements
Co-extruded plastic lumber, with a contrasting core and cap layer, allows CNC routers to mill crisp, durable graphics without paint or vinyl. Applications include:
- Wayfinding Signs: Weather-resistant displays for campuses.
- Architectural Cladding: Decorative panels for building exteriors.
4.4 Industrial and Agricultural Applications
CNC machining plastic lumber produces:
- Conveyor Components: Wear-resistant parts for manufacturing lines.
- Livestock Fencing: Durable, chemical-resistant structures for farms.
- Storage Systems: Custom bins for harsh industrial environments.
4.5 Emerging Applications
Renewable Energy: Plastic lumber components for solar panel mounts, machined to precise specifications.
Playground Equipment: Safe, splinter-free structures with custom shapes.
Urban Infrastructure: CNC-machined plastic lumber for bus shelters and bike racks, combining durability with aesthetic appeal.
Chapter 5: Advanced Strategies for CNC Machining Plastic Lumber
To elevate CNC machining plastic lumber to the next level, consider these advanced techniques:
5.1 Material Testing and Calibration
Before full-scale production, test plastic lumber batches for consistency. Variations in recycled content can affect machining behavior. Use a test piece to calibrate RPM, feed rate, and chip load.
5.2 Multi-Axis CNC Machining
For complex geometries, 5-axis CNC routers enable intricate cuts in plastic lumber, ideal for curved marine components or decorative panels. These machines reduce setup time and improve precision.
5.3 Automation and Workflow Optimization
Integrate CNC machining plastic lumber with automated workflows:
- CAD/CAM Integration: Streamline design-to-production with software like Fusion 360 or Mastercam.
- Robotic Loading: Automate material handling for high-volume production.
- In-Line Quality Control: Use sensors to monitor surface finish and dimensions during machining.
5.4 Sustainability Considerations
Plastic lumber’s recycled nature aligns with sustainability goals. Highlight this in marketing to appeal to eco-conscious clients. CNC machining minimizes waste by optimizing toolpaths, further enhancing environmental benefits.
Chapter 6: Troubleshooting Common Issues
Even with best practices, challenges arise in CNC machining plastic lumber. Here are solutions to common problems:
- Melting: Reduce RPM, increase feed rate, or enhance chip evacuation with air blasts.
- Rough Edges: Use a sharper tool or add a finishing pass with minimal stock removal.
- Warping: Anneal the material or machine both sides to balance stresses.
- Tool Wear: Switch to carbide or diamond-coated O-flute bits for longer life.
Conclusion
CNC machining plastic lumber transforms a durable, sustainable material into precision-engineered products for marine, outdoor, industrial, and architectural applications. By mastering material properties, thermal control, and precision techniques, fabricators can overcome challenges like low stiffness, thermal expansion, and heat sensitivity. Specialized tools, optimized parameters, and advanced strategies unlock plastic lumber’s potential, delivering high-value solutions that thrive in demanding environments. Ready to elevate your projects? Explore advanced CNC tools and plastic lumber suppliers at want.net to start creating durable, innovative products today.
FAQ:
- What is plastic lumber, and how does it differ from wood for CNC machining?
Answer: Plastic lumber is a thermoplastic material, typically made from recycled High-Density Polyethylene (HDPE) or other polymers like PVC or PP. Unlike wood, plastic lumber is waterproof, rot-resistant, and insect-proof, making it ideal for harsh environments. However, CNC machining plastic lumber requires specialized techniques due to its low stiffness (112,000–114,000 psi vs. wood’s 1,500,000 psi), high thermal expansion, and low melting point (220–230°F for HDPE). Woodworking tools and parameters often lead to melting or poor finishes when used on plastic lumber.
2. Why is thermal management critical in CNC machining plastic lumber?
Answer: Plastic lumber has poor thermal conductivity, causing frictional heat from CNC machining to build up at the cutting point. If heat exceeds the material’s melting point (e.g., 220–230°F for HDPE), it results in melting, tool clogging, and rough surfaces. Effective thermal management—using low RPMs (10,000–14,000), high feed rates (100–200 IPM), O-flute tools, and air blasts—ensures clean cuts and prevents damage during CNC machining plastic lumber.
3. What tools are best for CNC machining plastic lumber?
Answer: Single-flute or two-flute O-flute bits with polished, rounded channels are ideal for CNC machining plastic lumber. These tools maximize chip evacuation, reducing heat buildup. Up-cut spiral bits pull chips upward, preventing clogging, while carbide or diamond-coated options enhance durability. Avoid wood or metal tools, as they cause melting and poor finishes when machining plastic lumber.
4. How can I prevent warping when CNC machining plastic lumber?
Answer: Warping in plastic lumber occurs due to internal stresses or heat buildup during CNC machining. To prevent it:
- Use stable workholding, like vacuum tables or high-strength tape, to minimize vibration.
- Machine both sides to balance stresses.
- Limit depth of cut to half the tool’s diameter (e.g., 1/8″ for a 1/4″ bit).
- Consider annealing plastic lumber at 180°F before machining to reduce stresses.
5. What are the best CNC parameters for machining plastic lumber?
Answer: Optimal parameters for CNC machining plastic lumber depend on the material (e.g., HDPE, PVC). For HDPE, use:
- RPM: 10,000–14,000
- Feed Rate: 100–200 inches per minute
- Chip Load: 0.005″–0.010″ (calculated as Feed Rate / (RPM × Flutes))
- Depth of Cut: 0.125″–0.250″ per pass These settings ensure thick chips remove heat, preventing melting. Adjust for other plastics like PVC (12,000–16,000 RPM, 80–150 IPM) based on their properties.
6. Can I use standard woodworking CNC routers for plastic lumber?
Answer: Yes, but adjustments are necessary. Standard CNC routers can machine plastic lumber if equipped with O-flute bits, low RPM settings, and enhanced chip evacuation (e.g., air blasts or vacuum systems). Without these modifications, CNC machining plastic lumber on woodworking routers risks melting, burring, or dimensional inaccuracies due to the material’s thermoplastic nature.
Reference:
https://www.sciencedirect.com/science/article/abs/pii/S2352710223000013
Other Articles You Might Enjoy
- Beyond Bronze: How CNC-Machined Plastic Bushings Solve the Core Failures of Metal Components
Executive Summary CNC-machined plastic bushings are transforming industrial applications by addressing the inherent failures of metal bushings. Unlike bronze or steel, plastic bushings eliminate lubrication needs, resist corrosion, and reduce…
- Beyond the Bolt: How CNC-Machined Plastic Screws Solve Modern Engineering's Toughest Challenges
Fasteners are the unsung heroes of engineering, silently ensuring the integrity of everything from life-saving medical implants to spacecraft exploring the cosmos. For decades, metal fasteners dominated due to their…
- CNC Machining of Polymers: A Comparative Analysis of Thermoplastic vs. Thermoset
In CNC machining, selecting the right polymer for precision components is a pivotal decision that defines performance, durability, and manufacturability. The choice between Thermoplastic vs. Thermoset is especially critical, as…
- Avoid Melting and Delamination When Machining Plastic Laminate
Introduction Plastic laminate is a beautiful material when it’s done right—and a real nightmare when it isn’t. I’ve been working with CNC machines for years, and if there’s one thing…
- Master CNC Machining with ABS Plastic Sheet: Tools, Tips, and Techniques
Introduction: Mastering CNC Machining with ABS Plastic Sheet When it comes to CNC machining, the choice of material can make or break a project. ABS plastic sheet is one of the most…