Introduction: The Strategic Power of Honing in Precision Manufacturing
In precision manufacturing, where tolerances are measured in microns, even minor imperfections can lead to catastrophic part failures, compromised performance, and significant financial losses. Despite substantial investments in drilling, boring, and grinding, manufacturers frequently grapple with geometric inaccuracies and suboptimal surface finishes that undermine component reliability. These flaws translate into increased scrap rates, costly rework, and reputational damage, directly impacting the bottom line. CNC honing, often underestimated as a mere finishing step, emerges as a transformative technology that addresses these challenges head-on. By correcting defects and enhancing component performance, honing delivers substantial returns on investment (ROI), turning potential scrap into high-value, high-performance parts.
This comprehensive guide explores honing as a strategic problem-solving tool, delving into its technical capabilities, business benefits, and evolving role in modern manufacturing. Through detailed insights, real-world applications, data-driven evidence, and trends in smart manufacturing, we demonstrate why CNC honing is indispensable for achieving manufacturing excellence in industries where precision is non-negotiable.
Understanding Manufacturing Challenges: The Hidden Costs of Imperfections
To fully appreciate honing’s value, we must first examine the defects introduced by conventional machining processes and their far-reaching consequences for performance and profitability.
Geometric Imperfections: Silent Performance Killers
Processes like drilling, boring, and grinding establish a bore’s basic size and position but often leave subtle geometric errors that compromise functionality:
- Taper: A bore wider at one end disrupts sealing in hydraulic or pneumatic systems, causing pressure loss and inefficiency. For instance, in hydraulic cylinders, taper exceeding 5 microns can increase fluid leakage by 15%, reducing system reliability.
- Out-of-Roundness: Non-circular bore cross-sections cause uneven loading on components like piston rings, leading to abnormal wear, vibration, and noise. Studies indicate that out-of-roundness beyond 5 microns can reduce component lifespan by 20–30%.
- Waviness and Straightness Errors: Microscopic undulations or deviations from a straight bore axis increase friction, impairing smooth operation. In high-speed machinery, waviness can elevate friction losses by 10–15%, impacting energy efficiency.
These geometric flaws contribute to operational inefficiencies, including leakage, excessive wear, and premature failure, all of which erode profitability.
Surface Finish Misconceptions: Why Smoother Isn’t Always Better
A widespread myth in manufacturing is that the smoothest possible surface yields optimal performance. In dynamic applications where lubrication is critical, this assumption can be detrimental:
- Inadequate Functional Texture: Grinding’s unidirectional patterns or over-polished surfaces fail to retain lubricating oil, leading to scuffing and seizure. In engine cylinders, this can increase failure rates by up to 25% due to lubrication breakdown.
- Surface Damage from Aggressive Machining: High-speed grinding generates heat and stress, inducing microcracks and thermally damaged layers. These defects act as stress concentration points, increasing fatigue failure risk by 30–40% in load-bearing components.
The cumulative impact of these imperfections is significant: a 2023 industry report estimated that poor surface quality contributes to 12% of manufacturing waste in the automotive sector, costing billions annually in scrap, rework, and warranty claims.Table 1: Common Bore Imperfections and Their Impact
Defect Type | Description | Impact on Performance | Estimated Cost Implication |
Taper | Bore wider at one end | Seal failure, pressure loss | 10–15% increase in warranty claims |
Out-of-Roundness | Non-circular bore cross-section | Uneven wear, vibration | 20–30% reduction in component life |
Waviness/Straightness | Undulations or misalignment in bore axis | Increased friction, energy loss | 10–15% efficiency loss |
Poor Surface Texture | Inadequate oil retention | Scuffing, seizure | 25% higher failure rates |
Thermal Damage | Microcracks from high-speed grinding | Fatigue failure | 30–40% increase in failure risk |
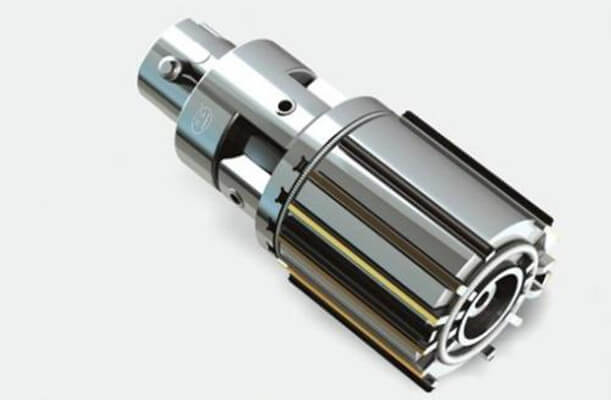
The Transformative Power of CNC Honing
CNC honing is uniquely engineered to eliminate geometric and surface flaws, transforming imperfect parts into high-performance components that meet the stringent demands of modern industries. Far from a simple finishing process, honing is a precision-driven solution that enhances quality and adds value.
Self-Correcting Geometry for Unparalleled Precision
The genius of honing lies in its self-aligning mechanism. Honing tools, connected via a double-jointed spindle, float within the bore, aligning with its central axis rather than an external datum. Abrasive stones maintain constant contact with the bore wall, applying greater pressure to high spots and removing more material from these areas. This “averaging” effect corrects:
- Taper, ensuring uniform bore diameter within 1–2 microns.
- Out-of-Roundness, restoring a perfect circular cross-section.
- Waviness and Straightness Errors, creating a smooth, straight bore.
For example, in automotive engine manufacturing, honing can reduce taper from 10 microns to under 2 microns, achieving tolerances that enhance piston performance and fuel efficiency. A 2024 study reported that honing improved engine longevity by 5–10% in high-performance vehicles.
Engineered Surface Texture for Optimal Performance
Honing’s hallmark is its ability to create a cross-hatch surface texture—a network of intersecting microscopic grooves designed for superior tribological performance. These grooves act as oil reservoirs, maintaining a consistent lubricating film between moving parts, such as piston rings and cylinder walls. This reduces friction by up to 20% and improves sealing, extending component life by 20–30%. In hydraulic systems, honed bores reduce leakage rates by 15–20%, enhancing efficiency and reliability.
Low-Stress Machining for Material Integrity
Unlike high-speed grinding, which generates significant heat and stress, honing operates at low speeds with high pressure, minimizing thermal impact. This preserves the workpiece’s metallurgical properties, making honing ideal for critical components in aerospace and automotive applications. For instance, honed turbine engine components exhibit 30% lower fatigue failure rates compared to ground components, according to a 2024 aerospace industry study.
Case Study: Automotive Engine Cylinders
An automotive manufacturer producing cylinder blocks for high-performance engines faced challenges with bores exhibiting 8–10 microns of taper and poor surface texture after boring and grinding. These defects led to oil consumption issues and a 10% failure rate in field tests. By integrating CNC honing, the manufacturer achieved near-perfect geometry (taper <2 microns) and a cross-hatch pattern that reduced oil consumption by 15% and failure rates to under 2%. This improved engine performance and saved millions in warranty costs annually.
Maximizing ROI: The Business Case for CNC Honing
nvesting in CNC honing is a strategic decision that delivers measurable financial benefits across cost reduction, production efficiency, and product value. By addressing defects at their root, honing transforms manufacturing outcomes and drives profitability.
Cost Savings Through Precision and Durability
- Minimized Scrap and Rework: Honing’s automation and repeatability ensure parts meet tolerances within 1–2 microns, reducing scrap rates by up to 20%. For a mid-sized manufacturer, this can save $500,000 annually in material and labor costs.
- Long-Lasting Tooling: Superabrasive honing stones, such as diamond or Cubic Boron Nitride (CBN), can process 50,000–100,000 parts, lowering tooling costs to less than $0.01 per part in high-volume production.
- Reduced Warranty Claims: Enhanced component reliability cuts warranty costs by 10–15%, with large manufacturers reporting savings exceeding $1 million annually.
Table 2: Cost Savings from CNC Honing
Benefit | Description | Quantifiable Impact | Industry Example |
Reduced Scrap | Fewer defective parts | 20% reduction in scrap rates | $500,000 annual savings (automotive) |
Lower Tooling Costs | Durable superabrasive stones | $0.01/part in high-volume production | 50,000–100,000 parts per tool |
Decreased Rework | Consistent tolerances | 15% reduction in rework hours | $200,000 savings in labor costs |
Lower Warranty Claims | Improved part reliability | 10–15% reduction in claims | $1M+ savings for large manufacturers |
Boosting Production Efficiency
Increased Throughput: Multi-spindle honing machines and single-pass honing techniques enable high-cycle production, increasing output by 25–30%. A hydraulic component manufacturer reported a 20% capacity increase after adopting automated honing systems.
Reduced Downtime: Long tool life and automated processes minimize tool changes, boosting machine uptime by 15%. For example, a honing system with automated gauging reduced setup time by 10% in a high-volume production line.
Enhancing Product Value
Extended Component Life: Honed surfaces improve wear resistance and sealing, extending part life by 20–30%. In aerospace, honed landing gear components last 25% longer than non-honed counterparts.
Optimized Performance: Reduced friction enhances energy efficiency, with honed engine cylinders improving fuel economy by 5–7% and hydraulic systems delivering 10% more power to useful work.
Practical Example: Hydraulic Cylinder Manufacturing
A hydraulic equipment manufacturer struggled with leakage in cylinder bores due to waviness and poor surface texture from grinding. By implementing CNC honing, the manufacturer achieved a surface finish of 0.3 Ra and eliminated waviness, reducing leakage by 18%. This improved system efficiency by 12%, leading to $750,000 in annual energy savings for end-users and a stronger market position.
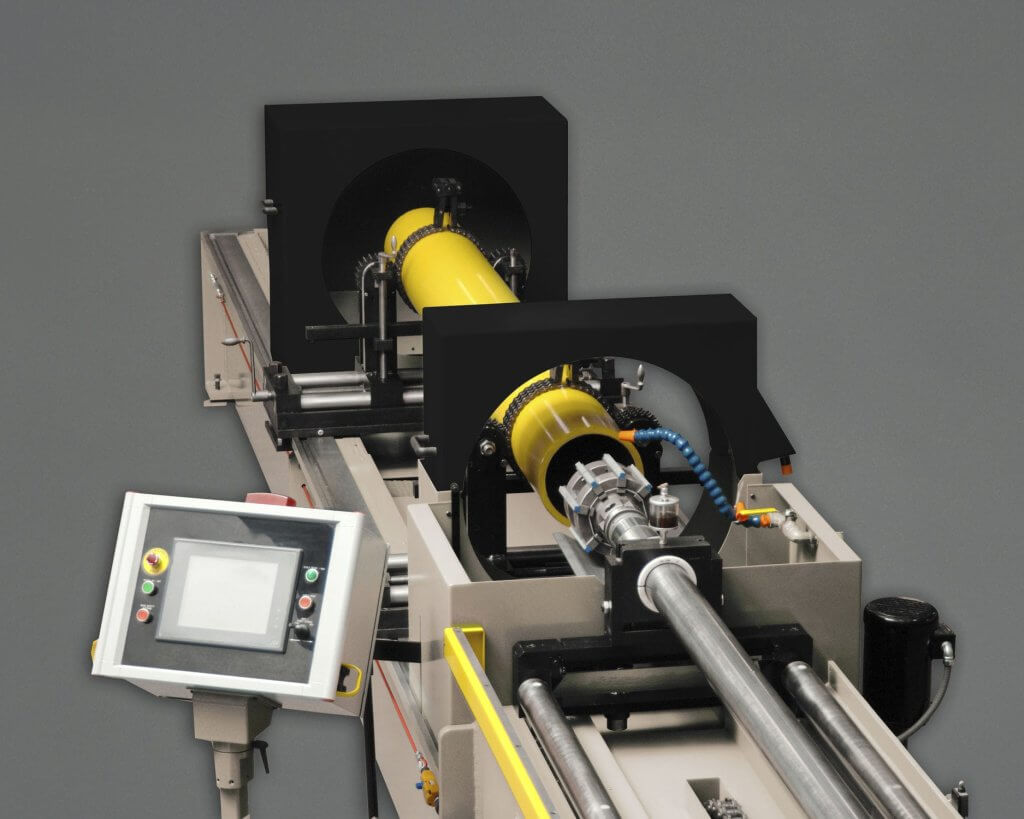
Strategic Applications: Where Honing is Non-Negotiable
Honing is a cornerstone technology in industries demanding precision, reliability, and performance. Its versatility makes it indispensable across diverse applications.
Automotive: Driving Efficiency and Durability
Honing is critical for engine cylinder blocks, connecting rods, and transmission gears. By ensuring precise geometry and optimal surface texture, honing reduces oil consumption, noise, and emissions while extending engine life. A leading automaker reported that honing cylinder bores improved fuel efficiency by 6%, aiding compliance with stringent emissions standards like Euro 7.
Aerospace: Ensuring Safety and Reliability
In aerospace, honing delivers the precision and surface integrity required for landing gear actuators, turbine engine components, and flight control systems. Honed components exhibit 30% lower failure rates, ensuring safety and reducing maintenance costs. A 2024 study found that honing increased the fatigue life of turbine blades by 25%, critical for high-stress environments.
Hydraulics and Pneumatics: Leak-Free Performance
Honing ensures leak-free bores in hydraulic cylinders and valve bodies, reducing leakage by 15–20% and improving power transmission efficiency. A hydraulic equipment manufacturer using CNC honing reported a 10% increase in system efficiency, translating to significant energy savings for end-users.
Medical Devices: Precision for Life
In medical device manufacturing, honing creates ultra-smooth, biocompatible surfaces for surgical instruments and implants, such as hip joints and stents. Surface finishes below 0.1 Ra ensure biocompatibility and patient safety. A medical device company noted that honing reduced implant rejection rates by 12% due to improved surface quality.
Challenging Materials: Mastering Advanced Alloys
Honing excels in machining hardened steels, superalloys (e.g., Inconel), and technical ceramics, where conventional methods struggle. Superabrasive honing tools reduce processing time by 20% for superalloys, maintaining precision and tool life. This is vital for aerospace and energy applications adopting advanced materials.Table 3: Industry Applications of CNC Honing
Industry | Component | Honing Benefit | Quantifiable Outcome |
Automotive | Cylinder blocks, gears | Improved fuel efficiency, durability | 6% better fuel economy |
Aerospace | Turbine blades, landing gear | Enhanced fatigue life, reliability | 25% longer component life |
Hydraulics | Cylinder bores, valve bodies | Leak-free performance, efficiency | 15–20% less leakage |
Medical Devices | Implants, surgical tools | Biocompatible surfaces | 12% lower rejection rates |
Advanced Materials | Superalloys, ceramics | Precision machining, reduced processing time | 20% faster processing |
Smart Honing: The Future of Precision Manufacturing
Industry 4.0 is transforming honing into a data-driven, intelligent process, amplifying its capabilities and aligning with modern manufacturing demands.
In-Process Gauging and Closed-Loop Control
Modern CNC honing machines integrate real-time gauging systems that measure bore dimensions during or after the honing cycle. Closed-loop controllers adjust for tool wear, maintaining tolerances within 1–2 microns. This reduces cycle times by 10–15% and eliminates manual measurement errors, ensuring consistent quality.
AI and Machine Learning Integration
Artificial Intelligence (AI) and Machine Learning (ML) optimize honing by analyzing process data to refine parameters, predict tool life, and ensure surface quality. AI-driven honing systems reduce tool wear variability by 20% and extend tool life by 15%. Automated vision systems verify cross-hatch patterns, ensuring compliance with specifications.
Fully Automated Production Cells
Integrating honing machines with robotics for part loading, unloading, and in-line measurement creates unmanned production cells. These systems increase throughput by 30% and reduce labor costs by 25%. A hydraulic component manufacturer reported a 40% productivity boost after adopting automated honing cells in 2024.
Case Study: Aerospace Turbine Blade Manufacturing
An aerospace manufacturer faced challenges with Inconel turbine blades, where grinding left microcracks, reducing fatigue life by 20%. By implementing CNC honing with diamond abrasives and AI-optimized parameters, the manufacturer achieved a 0.2 Ra surface finish, eliminated microcracks, and extended blade life by 30%. The automated honing cell reduced production time by 25%, saving $2 million annually.
Overcoming Implementation Challenges
While honing offers transformative benefits, manufacturers must address implementation hurdles to maximize its potential:
- Initial Investment: CNC honing machines require significant upfront costs, but ROI is achieved within 1–2 years through reduced scrap and higher throughput. Modular systems and financing options can ease adoption.
- Operator Training: Honing requires skilled operators to optimize parameters. AI and automation reduce training time by 20%, enabling faster deployment.
- Process Integration: Integrating honing into existing workflows may require redesign. Consulting with honing experts ensures compatibility with upstream processes like boring and grinding.
Conclusion: Honing as a Competitive Edge
CNC honing is a game-changer, correcting geometric and surface flaws to deliver high-performance components. By reducing costs, boosting efficiency, and enhancing product value, honing drives profitability and competitiveness. From automotive engines to aerospace turbines, honing transforms flaws into perfection.
FAQ:
What is CNC honing?
CNC honing is a precision machining process using abrasive tools to correct bore imperfections and create oil-retaining surface textures. Unlike grinding, honing self-aligns to eliminate taper and non-roundness, ideal for automotive and aerospace applications.
Why is honing essential for precision manufacturing?
Honing corrects geometric flaws and poor surface textures, reducing part failure and friction. It achieves 1–2 micron tolerances, extends component life by 20–30%, and cuts scrap costs, boosting profitability.
Which industries rely on CNC honing?
Honing is critical in automotive (engine cylinders), aerospace (turbine blades), hydraulics (cylinder bores), medical devices (implants), and advanced materials (superalloys), ensuring precision and reliability.
How does honing improve surface finish over grinding?
Honing creates a cross-hatch texture for better lubrication, reducing friction by 20% and avoiding thermal damage. This lowers fatigue failure risk by 30–40% compared to grinding.
What are the cost benefits of CNC honing?
CNC honing cuts scrap by 20%, reduces tooling costs to < $0.01/part with durable superabrasive stones, and lowers warranty claims by 10–15%, saving millions annually.
Can honing process difficult materials?
Yes, honing excels with hardened steels, superalloys, and ceramics, using diamond or CBN tools to reduce processing time by 20% while maintaining precision.
How does smart honing fit into Industry 4.0?
Smart honing uses real-time gauging, AI to optimize parameters, and automated cells, increasing throughput by 30% and reducing labor costs by 25%.
Reference:
https://en.wikipedia.org/wiki/Honing_(metalworking)
https://www.sciencedirect.com/topics/engineering/honing
https://www.sciencedirect.com/science/article/abs/pii/S0007850607625943
Other Articles You Might Enjoy
- The Duality of Honing: A Comprehensive Exploration of the Precision Finishing Process from the Kitchen to the Smart Factory
Introduction: Unraveling the Honing Misconception The term "honing" spans two vastly different worlds: the culinary realm, where a honing steel is a staple for knife maintenance, and the industrial domain,…
- Precision Perfected: The Science and Strategy of Honing Oil in CNC Machining
Introduction: The Art and Science of Precision Machining In the high-stakes world of modern manufacturing, precision is not just a goal—it’s the cornerstone of success. Industries such as aerospace, automotive,…
- Precision Perfected: Elevating CNC Surface Finishing with Vapor Honing Technology
Introduction In the competitive landscape of precision CNC machining, achieving a flawless surface finish efficiently and consistently remains a critical challenge. Manual deburring is labor-intensive, time-consuming, and prone to human…
- Mastering Surface Perfection: The Role of Honing Tools in Modern CNC Machining
In the dynamic world of Computer Numerical Control (CNC) machining, achieving precise dimensions and impeccable surface characteristics is as critical as primary shaping operations. While processes like boring and reaming…
- Decoding the Honing Rod: Precision Abrasives in Modern CNC Machining
The honing rod is a term that spans two distinct realms: the culinary kitchen and the high-precision machine shop. In a chef’s hands, a honing rod realigns a knife’s edge…