Teflon, also known as polytetrafluoroethylene (PTFE), is a remarkable material renowned for its exceptional properties, which have revolutionized various industries. From aerospace to medical devices, PTFE material plays a crucial role in creating high-performance components. But how does PTFE, or Teflon, go from a raw material to a finished product? That’s where Teflon machining comes into play.
In this article, we will dive into the world of Teflon machining and explore the process of transforming this versatile material into precision-engineered parts. Whether you’re a design engineer, a manufacturer, or simply curious about the fascinating world of manufacturing, this comprehensive guide will take you through every step of the journey.
So without further ado, lets get started.
Understanding Teflon/PTFE Material Properties
Teflon is primarily composed of carbon and fluorine atoms, forming a highly stable and inert molecular structure. This unique composition gives Teflon its extraordinary properties, setting it apart from other materials. The carbon-fluorine bonds are incredibly strong, resulting in high chemical resistance and thermal stability.
Teflon possesses a range of remarkable characteristics that make it highly desirable for numerous industrial applications.
Let’s explore some of its key benefits:
Heat Resistance
Teflon exhibits exceptional resistance to high temperatures. It can withstand temperatures up to 260°C (500°F) without melting or degrading, making it suitable for applications in extreme heat environments.
Nonstick Properties
Teflon is renowned for its nonstick surface, which prevents adhesion of substances. This property is particularly useful in cookware, preventing food from sticking and making cleaning effortless.
Chemical Resistance
Teflon is highly resistant to chemicals, including acids, bases, and solvents. It remains unaffected by most corrosive substances, making it ideal for use in chemical processing equipment and containers.
Low Friction
Teflon exhibits an extremely low coefficient of friction, reducing frictional forces and enabling smooth movement. This property is valuable in applications such as bearings, seals, and sliding surfaces.
Electrical Insulation
Teflon is an excellent electrical insulator. It has a high dielectric strength, making it suitable for applications where electrical insulation is crucial, such as in wiring, connectors, and electronic components.
Biocompatibility
Teflon is biocompatible, meaning it is compatible with living tissues and fluids. This property makes it suitable for medical and pharmaceutical applications, including implantable devices and drug delivery systems.
Teflon’s unique combination of properties makes it an invaluable material in various industries, including aerospace, automotive, electronics, food processing, pharmaceuticals, and more. Its versatility and reliability have propelled it to the forefront of modern manufacturing.
Preparing for Teflon Machining
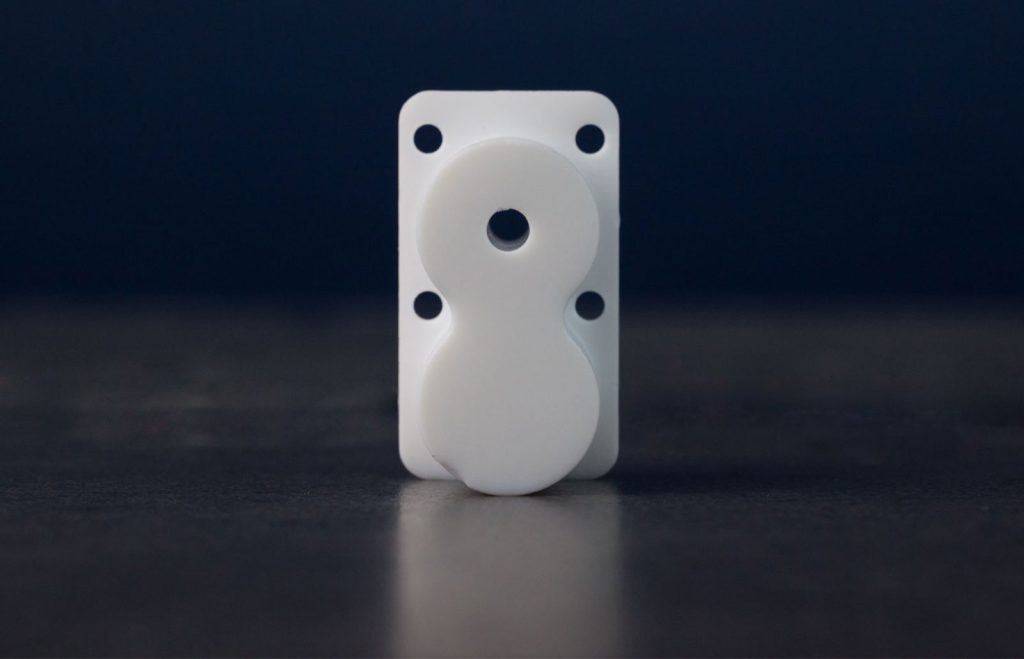
Before diving into Teflon/PTFE machining, thorough preparation is essential to ensure a smooth and successful manufacturing process.
1. Gathering Design Requirements and Specifications
To commence Teflon machining, it is crucial to gather comprehensive design requirements and specifications to achieve tight tolerances for your Teflon parts. This involves collaborating closely with design engineers, product developers, and stakeholders to understand the desired characteristics and functionality of the final Teflon component. Considerations such as dimensions, tolerances, surface finishes, and performance requirements should be clearly defined to guide the machining Teflon process effectively.
2. Choosing the Appropriate Teflon Grade for the Project
Teflon is available in various grades, each with its own specific properties and applications. Selecting the appropriate Teflon grade is crucial to ensure the desired performance and functionality of the machined component. Factors such as temperature resistance, chemical compatibility, electrical properties, and mechanical strength should be carefully evaluated when choosing the Teflon grade. Consultation with material experts and suppliers can aid in identifying the most suitable grade for the project.
3. Preparing the Machining Equipment and Tools
Effective machining Teflon requires proper preparation of machining equipment and tools. Firstly, the machining equipment, such as CNC machines or manual machining setups, should be inspected, calibrated, and maintained to ensure optimal performance. This includes verifying the accuracy of measurements, checking the alignment of cutting tools, and confirming the functionality of control systems.
Secondly, selecting the appropriate tools for Teflon machining is essential. Teflon is a relatively soft material, and therefore, tools with sharp cutting edges and appropriate geometries should be chosen. Carbide or high-speed steel (HSS) cutting tools are commonly used for Teflon machining due to their excellent wear resistance and durability. Proper tool selection, along with regular tool maintenance, ensures precise cuts and prolongs tool life.
By meticulously gathering design requirements, choosing the suitable Teflon grade, and adequately preparing the machining equipment and tools, you lay a solid foundation for a successful Teflon machining process.
Designing for Teflon/PTFE Machined Parts
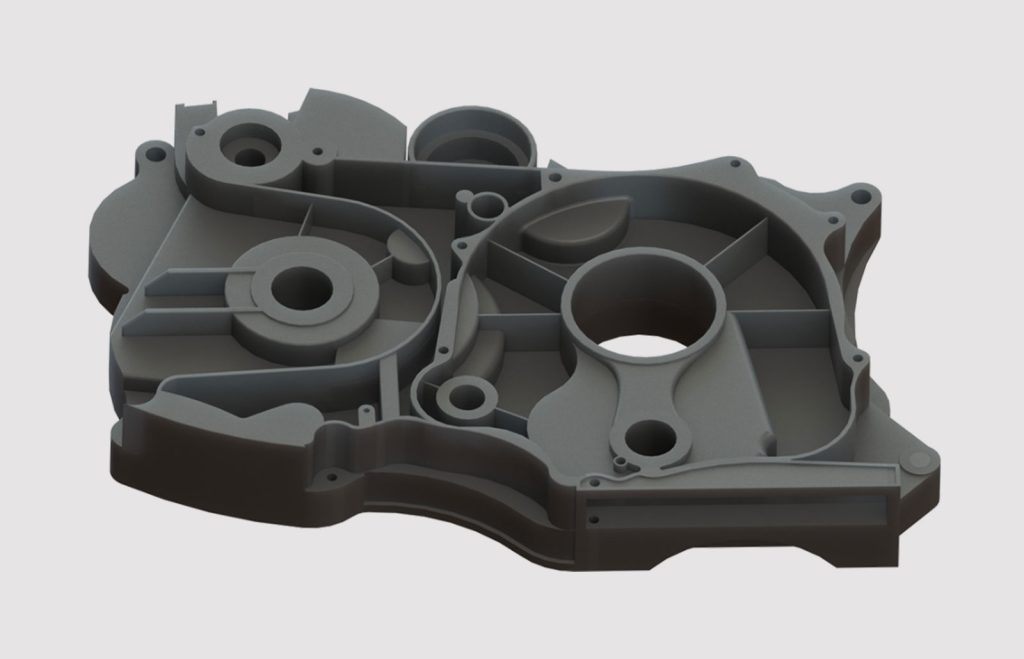
Designing for Teflon/PTFE machined parts requires careful consideration to fully leverage the unique properties of this remarkable material. In this section, we will explore the key design considerations necessary for successful Teflon machining.
Key Design Considerations for Successful Teflon Machining
When designing components for Teflon machining, several factors should be taken into account to ensure optimal results:
- Simplicity: Keep the design as simple as possible. Teflon machining is best suited for components with straightforward geometries and fewer complex features. Simplicity aids in achieving accurate and efficient machining.
- Avoid Sharp Corners: Teflon has a low tensile strength, making it susceptible to stress concentrations. Minimize sharp corners and utilize rounded or filleted edges to reduce stress concentrations and improve the structural integrity of the machined part.
- Consider Wall Thickness: Optimal wall thickness is crucial for Teflon components. Avoid excessive thickness, as it can lead to difficulties in machining and increased costs. Conversely, inadequate thickness may compromise the part’s strength. Find a balance based on the specific application requirements.
Incorporating Tolerances and Surface Finishes
Incorporating appropriate tolerances and surface finishes is vital to ensure the functional integrity and performance of Teflon components:
- Tolerances: Teflon machining requires specific tolerances tailored to the material’s properties. Factors such as thermal expansion, shrinkage, and machining allowances must be considered when defining tight tolerances. Consult with machining experts to determine suitable tolerances that align with the intended application.
- Surface Finishes: Teflon has a naturally low coefficient of friction, but specific surface finishes can further enhance its performance. Considerations such as smoothness, roughness, and lubricity are crucial. Machining techniques, such as polishing or adding micro-textures, can be employed to achieve the desired surface finish.
Optimizing Designs for Teflon’s Unique Properties
Teflon’s unique mechanical properties, such as heat resistance, nonstick characteristics, and chemical resistance, can be harnessed through optimized designs:
- Heat Dissipation: Design components with features that promote heat dissipation, such as fins or ventilation channels, to manage thermal effects effectively.
- Nonstick Performance: Leverage Teflon’s nonstick properties by incorporating smooth, rounded surfaces and reducing areas where material buildup could occur.
- Chemical Compatibility: Consider the specific chemical environment in which the Teflon component will operate. Ensure compatibility with the intended chemicals, and design features that prevent chemical entrapment or degradation.
By considering these design principles and optimizing designs to suit Teflon’s unique mechanical properties, you can maximize the performance and functionality of Teflon machined components.
Teflon Machining Techniques
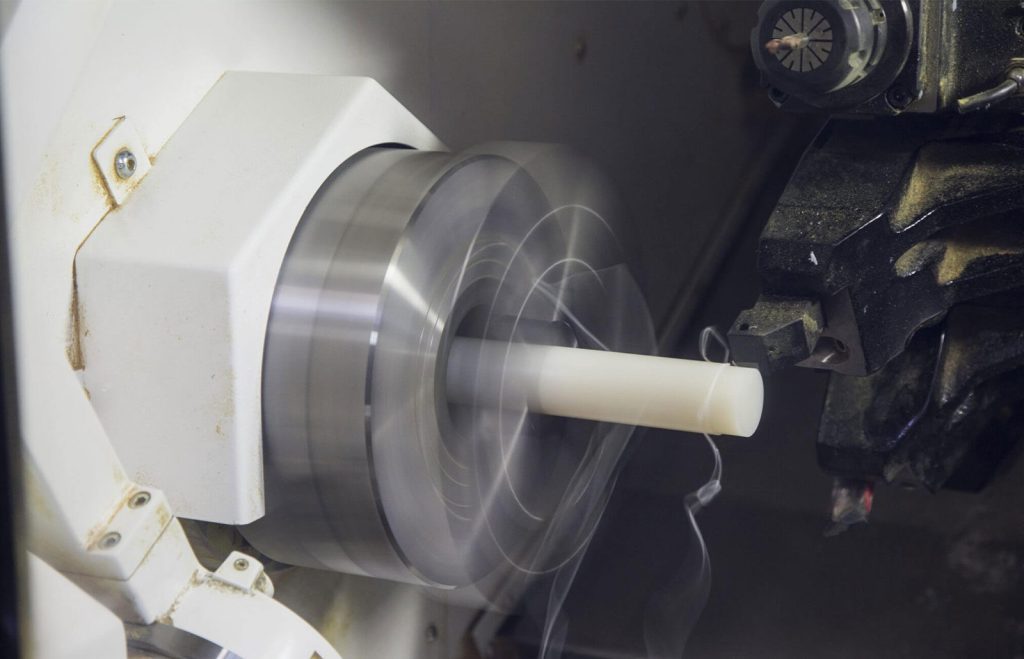
Teflon machining encompasses various techniques that enable the transformation of this remarkable material into precision-engineered components. Now let’s explore the primary Teflon machining methods.
CNC Machining of Teflon
Computer Numerical Control (CNC) machining is a widely used technique in the manufacturing industry, including CNC turning and CNC milling. This method utilizes computer-controlled machines to precisely shape and cut Teflon components.
CNC machining involves programming a computer to control the movements of cutting tools. Teflon machined parts are machined using CNC mills, lathes, or routers, ensuring high accuracy and repeatability.
CNC machining offers several advantages, including automation, precise control, and the ability to create complex geometries. However, Teflon’s low thermal conductivity and potential for melting present challenges during CNC machining, requiring careful consideration of cutting speeds, tool selection, and coolant usage.
To achieve optimal CNC turn/mill machining results with Teflon, factors such as tooling selection, proper fixturing, suitable feeds and speeds, and effective chip evacuation must be considered. Rigorous testing and fine-tuning of parameters may be necessary to achieve the desired precision and surface finish.
Manual Machining of Teflon
Traditional manual machining methods are still employed for Teflon components, particularly for smaller-scale projects and intricate designs. Here’s an overview of manual machining for Teflon:
Manual machining techniques for Teflon include turning, milling, drilling, and grinding. These methods utilize manually operated equipment and tools, such as lathes and milling machines, to shape and finish Teflon components.
Essential tools for manual Teflon machining include carbide or high-speed steel cutting tools, drills, reamers, and files. Techniques such as careful feed rates, light cuts, and appropriate tool speeds help maintain precision and prevent melting or chipping of the material.
Manual machining of Teflon requires attention to detail and adherence to best practices. Challenges such as chip control, heat generation, and dimensional stability should be addressed through proper tool selection, cooling techniques, and monitoring of machining parameters.
Other Teflon Machining Processes
In addition to CNC and manual machining, other specialized processes are employed for Teflon machining. Here are a few notable techniques:
Waterjet Cutting for Teflon
Waterjet cutting utilizes a high-pressure stream of water mixed with abrasive particles to precisely cut Teflon sheets or components. This process is particularly suitable for intricate designs and does not generate heat, minimizing the risk of material distortion.
Laser Cutting and Engraving Techniques
Laser cutting and engraving provide precise and intricate machining of Teflon. The focused laser beam melts or vaporizes the material, allowing for intricate cuts and engravings. Laser machining offers high accuracy and is ideal for producing custom designs.
Thermoforming and Molding Teflon
Thermoforming involves heating Teflon sheets and shaping them using molds or vacuum forming techniques. Molding processes, such as compression molding or injection molding, can also be employed to create complex Teflon PTFE parts with high repeatability.
Finishing and Surface Treatments for Teflon
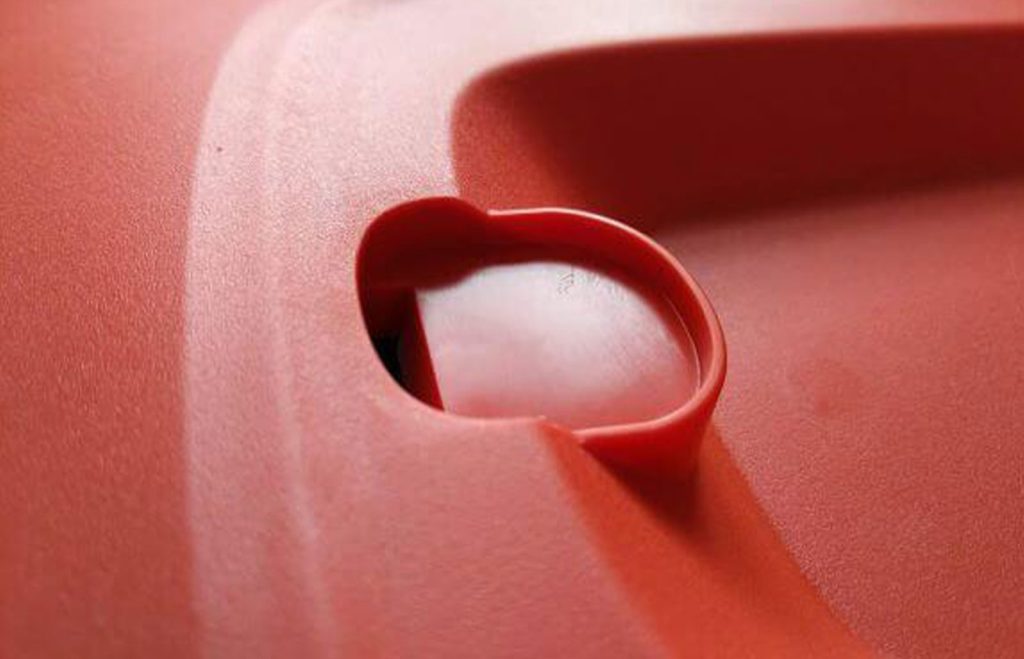
To further enhance the performance and properties of machined Teflon components, various finishing techniques and surface treatments can be applied. In this section, we will explore surface modification techniques, coatings for Teflon, and post-machining finishing options.
Surface Modification Techniques for Teflon
Surface modification techniques can alter the surface properties of Teflon components to enhance functionality or improve specific characteristics. Some common surface modification techniques include:
- Chemical Etching: Chemical etching involves treating the Teflon surface with specific chemical solutions to create microscale or nanoscale surface textures. This technique can improve bonding strength, adhesion properties, and lubricity.
- Plasma Treatment: Plasma treatment involves subjecting the Teflon surface to a low-pressure plasma gas. This process modifies the surface by increasing surface energy, which improves wettability and promotes bonding with adhesives or coatings.
- Surface Activation: Surface activation techniques, such as flame treatment or corona discharge treatment, create reactive sites on the Teflon surface, enhancing its adhesive properties and promoting better bonding with paints, adhesives, or coatings.
Enhancing Teflon’s Properties through Coatings
Applying coatings to Teflon components can enhance their properties or introduce additional functionalities. Some common coatings used for Teflon include:
- Nonstick Coatings: Teflon itself already possesses excellent nonstick properties. However, applying specialized nonstick coatings, such as fluoropolymer-based coatings, can further enhance the nonstick characteristics for specific applications.
- Wear-Resistant Coatings: Coatings such as polyimide or ceramic coatings can improve the wear resistance of Teflon components, extending their lifespan in applications where friction or abrasion is a concern.
- Chemical Resistance Coatings: Teflon already exhibits excellent chemical resistance. However, certain specialized coatings can further enhance its resistance to specific chemicals or provide additional protection in aggressive chemical environments.
Exploring Post-Machining Finishing Options
After the machining process, several post-machining finishing options can be employed to refine the surface quality and appearance of Teflon components:
- Polishing: Polishing involves smoothing the surface of Teflon through abrasion, resulting in a glossy and refined finish. Polishing can improve the aesthetics and cleanability of the component.
- Deburring: Deburring process removes any sharp edges, burrs, or rough areas created during the machining process. This ensures smooth edges and eliminates any potential snagging points or risks of injury.
- Cleaning and Surface Treatment: Thorough cleaning and surface treatment help remove any machining residues or contaminants. It can also prepare the surface for further coatings or treatments, ensuring optimal adhesion and performance.
By utilizing those techniques above, manufacturers can tailor the properties of Teflon components to meet specific requirements, enhance functionality, and achieve the desired surface characteristics.
Best Practices for Teflon Machining
To ensure efficient and accurate PTFE machined parts, it is essential to follow best practices that encompass tips for optimal performance, maintenance of machinery and tools, and adherence to safety precautions. In this section, we will explore these best practices to enhance your PTFE machining processes.
A. Tips for Efficient and Accurate Teflon Machining
- Optimize Cutting Parameters: Machining Teflon requires careful consideration of cutting parameters such as cutting speed, feed rate, and depth of cut. Experiment with different parameters to achieve the best balance between material removal and surface quality.
- Use Proper Coolants: Coolants are crucial during Teflon machining to dissipate heat and prevent material melting or deformation. Consider using coolants specifically formulated for machining Teflon to ensure effective heat control without compromising the material’s properties.
- Maintain Sharp Cutting Tools: Blunt or worn-out cutting tools can lead to poor surface finish and increased machining forces. Regularly inspect and replace cutting tools as needed to maintain optimal cutting performance and prevent damage to the machined components.
- Implement Chip Control Measures: Teflon can generate stringy or sticky chips during machining, which can interfere with the machining process. Implement effective chip control techniques, such as using proper chip breakers, coolant flow, or air blasts, to ensure uninterrupted machining and prevent chip entanglement.
B. Maintaining Machinery and Tools for Longevity
- Regular Cleaning and Lubrication: Clean the machining equipment regularly to remove any Teflon residues, dust, or debris that may accumulate. Apply appropriate lubricants to moving parts to reduce friction and ensure smooth operation.
- Perform Routine Maintenance: Follow the manufacturer’s recommended maintenance schedule for your CNC machines. Regularly inspect and calibrate critical components, such as spindle accuracy, axes alignment, and tool holders, to maintain accuracy and prolong the life of the machinery.
- Tool Maintenance and Replacement: Maintain cutting tools by regularly inspecting them for wear or damage. Clean and sharpen cutting tools when necessary, and replace them promptly to ensure optimal performance and prevent poor quality cuts.
C. Safety Precautions and Considerations
- Personal Protective Equipment (PPE): Wear appropriate PPE, such as safety glasses, gloves, and protective clothing, to protect against potential hazards during Teflon machining.
- Ventilation and Dust Control: Teflon machining can generate fine particles or fumes, which may pose respiratory hazards. Ensure proper ventilation in the machining area and implement dust collection systems to minimize exposure.
- Machine Safeguarding: Follow machine safeguarding guidelines, such as using machine guards and implementing emergency stop features, to ensure operator safety and prevent accidents during Teflon machining.
Final Thoughts
Teflon machining is a vital process that transforms the remarkable properties of Teflon, or PTFE, into high-performance components. By understanding Teflon’s unique characteristics, gathering design requirements, and employing appropriate machining techniques such as multi-axis CNC turning and CNC milling, manufacturers can unlock the full potential of this versatile material.
At Want.Net, we offer affordable CNC machining services for a wide range of materials, including Teflon. Our team of skilled professionals and state-of-the-art equipment are well-equipped to handle complex projects. Feel free to contact us today to get an instant quote and discover the expertise and reliability of Want.Net for all your Teflon machining needs.
Other Articles You Might Enjoy
- Nickel vs. Cobalt Alloys in High-Temperature CNC Machining: A Detailed Analysis?
Nickel and Cobalt Alloys in High-Temperature CNC Machining Both Nickel and Cobalt alloys play an essential role in high-temperature CNC machining. These metal alloys are popular choices due to their…
- Precision CNC Machining of Steel: Tailored Solutions for Every Need
Introduction to Precision CNC Machining Precision CNC machining, an integral part of modern manufacturing processes, is key in delivering high-accuracy and consistency in shaping a variety of materials. At its…
- The Impact of Cheap China CNC Machining in Product Development
1. Introduction: Revolutionizing Product Development through Affordability In this opening section, we explore the transformative impact of affordable China CNC machining on the landscape of product development. We set the…