In the realm of modern manufacturing, the plastic mold stands as a pivotal cornerstone, shaping everything from intricate medical devices to robust automotive components. This high-precision tool, brought to life through CNC machining, ensures the quality, consistency, and cost-effectiveness of injection molding parts. Far more than a mere metal block, a plastic mold is a sophisticated instrument that transforms molten plastic into precise, repeatable forms with unparalleled accuracy. This comprehensive guide delves into the multifaceted world of plastic mold creation, exploring its design, components, and the advanced CNC machining processes that forge these critical tools, while highlighting emerging trends and best practices for optimal performance in injection molding.
The Heart of Production: Understanding the Plastic Mold
The plastic mold is the unsung hero of injection molding, enabling the mass production of precise components that power industries worldwide. Its design and fabrication demand meticulous precision to meet exacting standards, ensuring the plastic mold delivers consistent, high-quality parts.
What is a Plastic Mold?
A plastic mold is a precision-engineered tool, typically crafted from hardened tool steel or aluminum, that serves as the matrix in the injection molding process. The plastic mold receives molten polymer under immense pressure, shaping it into parts that adhere to strict design specifications. This process—melting resin, injecting it into the plastic mold, cooling it, and ejecting the solidified part—occurs in seconds, forming the backbone of mass production for industries like automotive, medical, consumer electronics, and packaging. The plastic mold, machined with CNC precision, ensures tight tolerances and repeatability, making it indispensable for high-volume manufacturing.
Anatomy of a Plastic Mold
A plastic mold is a complex assembly of components, each meticulously designed to work in harmony:
- Core and Cavity: These are the heart of the plastic mold, defining the part’s geometry. The cavity, or A-side, forms the exterior, often cosmetic, surfaces of the plastic mold’s output, while the core, or B-side, shapes internal features. Crafted with CNC machining, these components withstand the extreme pressures and thermal cycling of injection molding, ensuring the plastic mold produces defect-free parts.
- Mold Base: The structural backbone of the plastic mold, the mold base comprises steel plates that house the core, cavity, and supporting systems. It aligns the plastic mold’s halves, supports injection pressures, and facilitates mounting to the molding machine, ensuring durability over millions of cycles.
- Ejection System: After the part cools, the ejection system—using pins, sleeves, or plates—removes it from the plastic mold. Strategic placement prevents cosmetic blemishes, maintaining the plastic mold’s output quality.
- Cooling System: Integrated channels within the plastic mold circulate coolant to regulate temperature, ensuring uniform cooling and minimizing defects like warping. CNC machining enables precise channel design, enhancing plastic mold efficiency.
- Venting System: Small vents in the plastic mold allow trapped air to escape during injection, preventing burn marks or incomplete filling, ensuring high-quality injection molding parts.
The Role of Plastic Molds in Industry
The versatility of plastic molds makes them indispensable across sectors. In medical manufacturing, plastic molds produce precise components like syringe barrels and diagnostic device housings. In automotive, they create durable parts like dashboards and bumpers. Consumer goods, from phone cases to kitchenware, rely on plastic molds for consistent, cost-effective production. The CNC machining process ensures that each plastic mold meets the unique demands of these applications, delivering precision and reliability.
Hot Runner vs. Cold Runner Plastic Molds
The runner system in a plastic mold guides molten plastic from the molding machine to the cavity, with thermal management significantly impacting efficiency, cost, and part quality.
Cold Runner Plastic Molds
Cold runner plastic molds feature unheated channels machined into the plastic mold plates. The molten plastic in the runner solidifies alongside the part, forming a sprue and runner system that is ejected as a single piece. This attached material must be trimmed, often recycled, but generates waste. Cold runner plastic molds are cost-effective, with lower tooling and maintenance costs, making them ideal for low- to medium-volume production or heat-sensitive polymers. They also allow easy color changes. However, slower cycle times and material waste can limit their efficiency for high-volume injection molding.
Hot Runner Plastic Molds
Hot runner plastic molds, often called runnerless systems, employ heated manifolds and nozzles to keep plastic molten, injecting it directly into the plastic mold’s cavity. This eliminates runner waste, speeds up cycle times, and enhances part consistency, making hot runner plastic molds ideal for high-volume production. They also allow flexible gate placement and lower injection pressures, improving injection molding efficiency. The trade-off is higher initial tooling costs and increased maintenance complexity, which may not suit low-volume runs.
Attribute | Cold Runner Plastic Mold | Hot Runner Plastic Mold |
Initial Tooling Cost | Low | High |
Maintenance Cost | Low | High |
Cycle Time | Slower | Faster |
Material Waste | High (runner is waste) | None (runner stays molten) |
Part Consistency | Good | Excellent |
Gate Location Flexibility | Limited (often on perimeter) | High (can gate anywhere) |
Color Change Ease | Easy | Difficult |
Suitable Production Volume | Low to Medium | High |
Heat-Sensitive Polymers | Suitable | Can be challenging |
Table 1: Comparing hot runner and cold runner plastic molds for injection molding efficiency and cost.
Strategic Considerations
Choosing between hot and cold runner plastic molds is a critical business decision. High-volume manufacturers, such as those producing consumer electronics, benefit from hot runner plastic molds due to reduced waste and faster cycles, which lower per-part costs. Conversely, low-volume medical or specialty manufacturers may opt for cold runner plastic molds to minimize upfront investment. The plastic mold’s runner system directly influences production economics, with CNC machining ensuring the precision needed for both configurations.
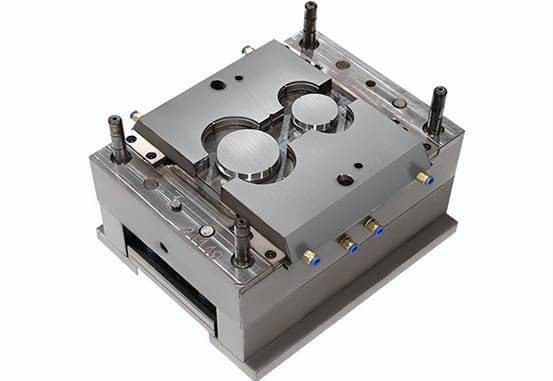
Structural Blueprints: Two-Plate vs. Three-Plate Plastic Molds
The structural design of cold runner plastic molds impacts gating flexibility and part release, with two primary configurations.
Two-Plate Plastic Molds
Two-plate plastic molds are the simplest and most common design, featuring a single parting line where the plastic mold splits into core and cavity halves. The runner system, machined into the plastic mold, is ejected with the part, limiting gate placement to the perimeter. This simplicity reduces plastic mold costs, making two-plate designs ideal for straightforward parts and cost-conscious projects.
Three-Plate Plastic Molds
Three-plate plastic molds use two parting planes, separating the runner system from the part during ejection. This allows flexible gate placement, such as pin-point gates in the part’s center, optimizing filling and aesthetics. While offering superior design flexibility, three-plate plastic molds are more complex and costly, suitable for intricate injection molding applications where gate placement is critical.
Hybrid Designs
Some plastic molds combine elements of both configurations, using CNC machining to integrate complex runner systems or custom gating. These hybrid plastic molds balance cost and flexibility, catering to specialized injection molding needs.
From Digital Blueprint to Hardened Steel: CNC Plastic Mold Creation
The creation of a plastic mold is a testament to the precision of CNC machining, transforming digital designs into durable, high-performance tools capable of producing millions of parts.
CAD Design for Plastic Molds
The plastic mold creation process begins with a 3D CAD model of the final part. Engineers design the plastic mold’s core, cavity, runner, cooling, and ejection systems using specialized software. This digital blueprint specifies every dimension, tolerance, and feature, ensuring the plastic mold meets injection molding requirements. CNC machining relies on this data to produce a plastic mold with exact precision.
CAM Programming for Precision
The CAD file is imported into CAM software, where programmers generate G-code toolpaths. These instructions guide the CNC machine’s cutting tools, translating the digital plastic mold design into a physical reality. This step is critical for ensuring the plastic mold’s components are machined accurately, minimizing errors in injection molding.
CNC Machining Execution
A block of tool steel or aluminum is secured in the CNC machine, which executes the G-code, removing material to form the plastic mold’s components. Key operations include:
- CNC Milling: The primary method for shaping the plastic mold’s core and cavity, milling uses rotating tools to carve complex 3D contours.
- CNC Turning: This process rotates the workpiece against a stationary tool, creating cylindrical components like guide pins for the plastic mold.
- High-Speed Machining (HSM): Using high spindle speeds and feed rates, HSM achieves smooth finishes on plastic molds, reducing manual polishing and enhancing injection molding part quality.
- Electrical Discharge Machining (EDM): Wire EDM cuts sharp corners, while sinker EDM forms deep ribs or textures in the plastic mold, enabling features unattainable with milling alone.
- Grinding and Polishing: Post-machining processes refine the plastic mold’s surface, ensuring mirror-like finishes for cosmetic parts in injection molding.
Quality Control in Plastic Mold Fabrication
Post-machining, the plastic mold undergoes rigorous inspection using coordinate measuring machines (CMMs) and laser scanners to verify tolerances. This ensures the plastic mold aligns perfectly, preventing defects like flash or misalignment during injection molding. CNC machining’s precision minimizes rework, saving time and cost.
Why CNC Machining Excels in Plastic Mold Creation
CNC machining is the gold standard for plastic mold production due to its unmatched precision, versatility, and reliability.
- Unmatched Precision: CNC machines achieve tolerances as tight as ±0.127 mm, ensuring the plastic mold’s core and cavity align perfectly, preventing defects in injection molding.
- Complex Geometries: Multi-axis CNC machining creates intricate plastic mold features, such as undercuts and organic shapes, enabling innovative part designs.
- Repeatability: Once programmed, CNC machines produce identical plastic molds, critical for high-volume injection molding and replacement components.
- Material Mastery: CNC machining handles tough tool steels like P20 and H13, crafting durable plastic molds capable of millions of injection molding cycles.
- Efficiency and Scalability: Automated CNC processes reduce labor and errors, making plastic mold production scalable for global supply chains.
This data-driven approach transforms plastic mold manufacturing into a predictable, repeatable process, ensuring consistent quality and reducing reliance on manual craftsmanship.
Design for Manufacturability (DFM): Optimizing Plastic Molds
Design for Manufacturability (DFM) is critical for plastic molds, ensuring parts are produced efficiently and defect-free.
- Uniform Wall Thickness: Consistent thickness in the plastic mold’s output prevents warping, sink marks, and voids due to uneven shrinkage. A nominal thickness of 1.2-3 mm is ideal, with ribs used for strength.
- Draft Angles: A 1-2° taper on plastic mold walls ensures clean part release, preventing drag marks or damage. Textured surfaces require additional draft (e.g., 1° per 0.025 mm of texture depth).
- Ribs and Bosses: These should be 40-60% of the adjacent wall thickness to avoid sink marks on the plastic mold’s cosmetic surfaces.
- Corner Radii: Internal radii ≥ 50% of wall thickness reduce stress and improve plastic flow in the plastic mold’s cavity.
- Parting Line and Gate Placement: The parting line, where the plastic mold’s halves meet, should be on non-cosmetic edges. Gates, placed in thick sections, ensure proper filling and minimize defects in injection molding.
Design Feature | Key Rule | Rationale / Risk of Non-Compliance |
Uniform Wall Thickness | Maintain consistent thickness; use gradual transitions. | Prevents warping, sink marks, and voids due to shrinkage. |
Draft Angle | Apply 1-2° per side; more for textured surfaces. | Ensures clean part release; prevents drag marks and damage. |
Ribs & Bosses | Base thickness 40-60% of adjacent wall. | Prevents cosmetic sink marks on opposite surface. |
Internal Corner Radii | Radius ≥ 50% of wall thickness (R ≥ 0.5T). | Reduces stress concentration, improves plastic flow. |
Gate Location | Place in thickest section, non-cosmetic area. | Ensures complete filling, prevents defects like weld lines. |
Table 2: DFM checklist for designing plastic molds to ensure defect-free injection molding parts.Early DFM collaboration with plastic mold manufacturers identifies potential issues, reducing costly rework and ensuring high-quality injection molding outcomes.
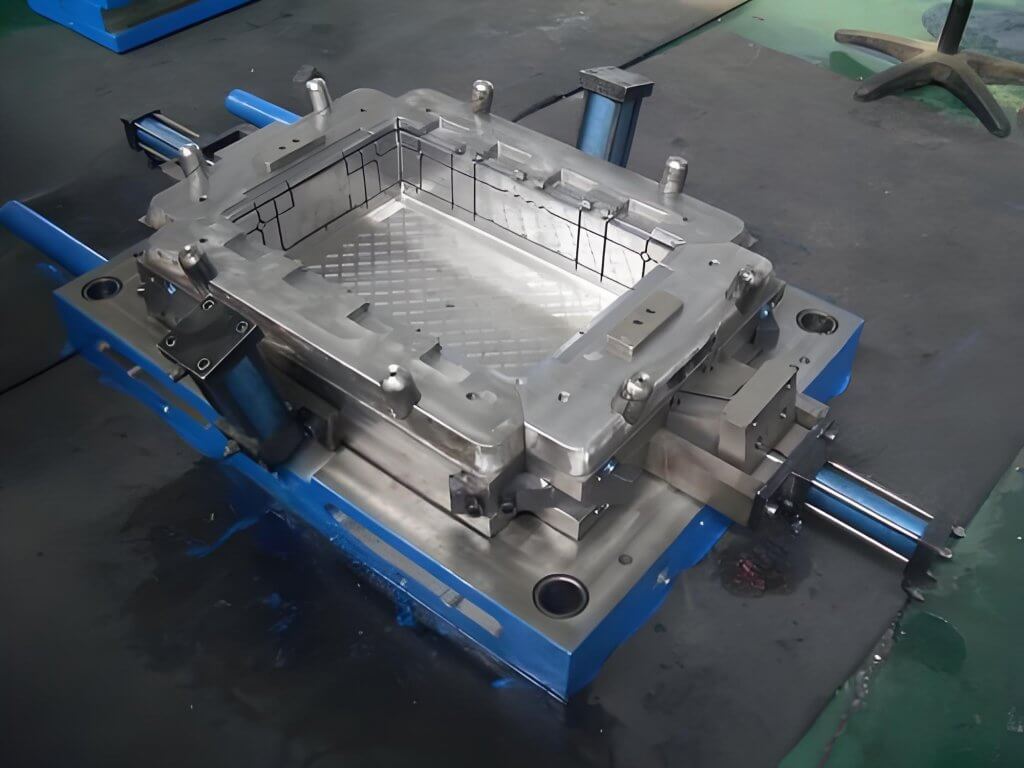
CNC Machining vs. Alternative Technologies for Plastic Molds
3D Printing vs. CNC Machining
- 3D Printing: Produces rapid prototype plastic molds from plastic or resin for 10-100 parts. Fast and low-cost, these plastic molds are ideal for design validation but lack durability for injection molding production.
- CNC Machining: Creates durable steel or aluminum plastic molds for millions of injection molding cycles, offering high precision and excellent surface finishes. The trade-off is higher costs and longer lead times.
Attribute | 3D Printing (Additive) | CNC Machining (Subtractive) |
Primary Application | Rapid prototype molds | Production molds, prototypes |
Tooling Material | Plastic, Resin | Tool Steel, Aluminum |
Tooling Lifespan (Shots) | Very Low (10-100) | Very High (100,000 to 1M+) |
Lead Time | Very Fast (1-5 days) | Slow (2-6+ weeks) |
Cost (per Tool) | Low | High |
Dimensional Accuracy | Lower | High |
Surface Finish | Poorer (layer lines) | Excellent |
Suitability for Production | No | Yes |
Table 3: Comparing 3D printing and CNC machining for plastic mold creation in injection molding.A hybrid approach—using 3D-printed plastic molds for prototyping and CNC-machined plastic molds for production—optimizes development timelines and costs.
CNC vs. Manual Machining
Before CNC machining, plastic molds were crafted manually, relying on artisan skill. Manual machining is less precise, slower, and incapable of handling complex plastic mold geometries. CNC machining’s automation, precision, and safety make it the standard for professional plastic mold production.
The Future of CNC-Powered Plastic Mold Making
Innovations are transforming plastic mold manufacturing, aligning with Industry 4.0 principles.
5-Axis CNC Machining
5-axis CNC machines move tools along five axes simultaneously, enabling complex plastic mold geometries with fewer setups. This enhances precision and efficiency, reducing plastic mold production time.
Hybrid Manufacturing
Combining additive (metal 3D printing) and subtractive (CNC machining) processes, hybrid manufacturing creates plastic molds with internal conformal cooling channels. These channels follow the part’s contours, improving cooling uniformity, reducing cycle times, and enhancing injection molding part quality.
AI and Automation in Plastic Mold Production
- Automation: Robotic arms and “lights-out” cells enable 24/7 plastic mold production, increasing efficiency.
- Artificial Intelligence (AI): AI optimizes CNC machining by predicting maintenance, adjusting cutting parameters, and enabling real-time quality control. Integrated sensors and machine vision ensure plastic mold precision.
- Digital Twin Technology: A virtual model of the plastic mold and injection molding process, updated with real-time data, allows AI to optimize performance, blurring the line between digital and physical manufacturing.
These advancements promise smarter, faster, and more reliable plastic mold production, redefining manufacturing as a data-driven service.
Case Studies: Plastic Molds in Action
Medical Industry
A leading medical device manufacturer used CNC machining to create a plastic mold for syringe barrels. The plastic mold’s tight tolerances (±0.05 mm) ensured consistent part dimensions, critical for patient safety. CNC machining’s precision and EDM capabilities enabled intricate features, while a hot runner plastic mold reduced material waste, lowering costs.
Automotive Sector
An automotive supplier developed a plastic mold for dashboard panels using 5-axis CNC machining. The plastic mold’s complex geometry and conformal cooling channels, created via hybrid manufacturing, reduced cycle times by 20%, improving injection molding efficiency and part quality.
Consumer Electronics
A smartphone case manufacturer employed a three-plate plastic mold with pinpoint gating, machined via CNC processes, to achieve flawless aesthetics. The plastic mold’s high repeatability ensured consistent production across millions of units, meeting consumer demand.
Best Practices for Plastic Mold Design and Production
Collaborate Early: Engage plastic mold manufacturers during design to conduct DFM analysis, reducing rework.
Material Selection: Choose tool steels like H13 for high-volume plastic molds or aluminum for prototypes, balancing durability and cost.
Leverage Technology: Use 5-axis CNC machining and EDM for complex plastic molds, and explore hybrid manufacturing for advanced features.
Test Prototypes: Validate designs with 3D-printed plastic molds before investing in CNC-machined production plastic molds.
Optimize Cooling: Design conformal cooling channels in the plastic mold to enhance injection molding efficiency.
Conclusion
The plastic mold remains the foundation of injection molding, enabling the mass production of high-quality, precise parts across industries. CNC machining transforms digital designs into durable, high-precision plastic molds, ensuring consistency and reliability in injection molding. As innovations like 5-axis machining, hybrid manufacturing, and AI-driven automation advance, the partnership between plastic molds and CNC machining will drive manufacturing forward, delivering smarter, more efficient plastic molds for global industries. Contact us to start designing your high-precision plastic mold today and unlock the full potential of injection molding.
FAQ:
- What is a plastic mold, and why is it essential for injection molding?
A plastic mold is a precision-engineered tool, typically made from steel or aluminum, used in the injection molding process to shape molten plastic into precise, repeatable parts. The plastic mold is critical because it determines the quality, consistency, and cost-effectiveness of injection molding parts, enabling mass production for industries like medical, automotive, and consumer electronics. CNC machining ensures the plastic mold achieves the tight tolerances required for high-quality output.
- How does CNC machining improve plastic mold production?
CNC machining enhances plastic mold production by delivering unmatched precision, repeatability, and versatility. It achieves tolerances as tight as ±0.127 mm, ensuring the plastic mold’s core and cavity align perfectly to prevent defects. Multi-axis CNC machines create complex plastic mold geometries, while high-speed machining (HSM) and EDM produce smooth finishes and intricate features, making CNC machining the gold standard for plastic mold fabrication.
- What are the differences between hot runner and cold runner plastic molds?
Hot runner plastic molds use heated manifolds to keep plastic molten, eliminating runner waste and speeding up injection molding cycles, ideal for high-volume production. Cold runner plastic molds have unheated channels, producing solid runners that require trimming, which generates waste but lowers tooling costs, suiting low- to medium-volume runs. The choice of plastic mold type impacts cost, efficiency, and part quality in injection molding.
- Why is Design for Manufacturability (DFM) important for plastic molds?
DFM ensures that plastic molds produce defect-free parts efficiently by optimizing design features like uniform wall thickness, draft angles, and gate placement. Proper DFM minimizes issues like warping, sink marks, and poor part release in injection molding, reducing costly rework. Early collaboration with plastic mold manufacturers during DFM analysis enhances plastic mold performance and lowers production costs.
- Can 3D printing replace CNC machining for plastic mold creation?
3D printing is ideal for rapid prototype plastic molds, producing low-cost tools in days for 10-100 injection molding parts. However, these plastic molds lack the durability and precision of CNC-machined steel plastic molds, which support millions of cycles. A hybrid approach—using 3D-printed plastic molds for prototyping and CNC machining for production—optimizes development timelines and ensures high-quality injection molding output.
- What materials are used to make plastic molds?
Plastic molds are typically made from hardened tool steels like P20 or H13 for high-volume injection molding, offering durability for millions of cycles. Aluminum is used for prototype plastic molds or low-volume runs due to its lower cost and machinability. CNC machining excels at shaping these tough materials, ensuring the plastic mold meets precise tolerances and withstands injection molding pressures.
Reference:
https://zh.wikipedia.org/wiki/%E6%A8%A1%E5%85%B7
https://patents.google.com/patent/CN101454138A/zh
https://zh.wikipedia.org/w/index.php?title=%E5%A1%91%E6%96%99&oldformat=true&variant=zh-cn
Other Articles You Might Enjoy
- How CNC Machining Delivers Precision in Custom POM Plastic Parts
Working with POM plastic in CNC machining has become a popular choice for manufacturers due to its excellent mechanical properties, low friction, and high dimensional stability. Customizing parts using this…
- Elevating Precision Standards through Chamfer in CNC Machining
1. Introduction: The Pursuit of Unparalleled Precision In the realm of CNC machining, precision is paramount. This section introduces the article by exploring the significance of precision in manufacturing and…
- Precision Prowess: Unveiling the Advantages of China CNC Machining
1. Introduction: The Role of Precision in Manufacturing Excellence In this introductory section, we delve into the critical role that precision plays in manufacturing and set the stage for an…
- Revolutionizing CNC Machining for Complex Aerospace Assemblies
Introduction to CNC Machining in Aerospace Assemblies Computer Numerical Control (CNC) machining represents a significant technological development playing a notable role in the creation of complex aerospace assemblies. CNC machining…
- The Role of Prototype Machining in Accelerating Product Development
Introduction: The Importance and Definition of Prototype Machining Prototype machining is a critical element advancing product development. It involves the technique of manufacturing an early model or sample, known as…
- High-Precision CNC Machining for Military Applications
Introduction to High-Precision CNC Machining in Military Applications The technical realm of high-precision Computer Numeric Control (CNC) machining is fast becoming integral to the military sector. This process, which relies…