Inconel vs. Stainless Steel in Extreme Temperature CNC Operations
Selecting the right material for extreme temperature CNC operations is a crucial decision that impacts the efficiency and longevity of components. Two popular choices for these demanding circumstances are Inconel and stainless steel, each offering specific benefits and potential drawbacks. Inconel, well-known for its exceptional resistance to oxidation and corrosion, especially at high temperatures, provides endurance in severe conditions while ensuring minimal wear and tear on parts. On the other hand, stainless steel, with its excellent machinability and strength-to-weight ratio, aids in easier fabrication and manipulation during machining processes.
- The superior heat tolerance of Inconel allows it to preserve its mechanical properties even under intense thermal stress, making it ideal for turbine blades, turbocharger rotors, and exhaust systems where performance can’t be compromised.
- Stainless steel’s inherent ductility, weld-ability and cost-effectiveness make it a preferable option for applications like surgical instruments, kitchen utensils, and chemical containers where formability and affordability matter.
A thorough comparative analysis based on the specific requirements of the CNC project can aid in choosing the most suitable material between Inconel and stainless steel.
Understanding Inconel and Stainless Steel as Materials
In the world of CNC operations, selecting the right material for extreme temperature conditions is crucial. Known for its high-temperature resistance, Inconel is a superalloy that consists mainly of nickel but includes important elements like chromium, iron, and molybdenum. It displays excellent oxidation and corrosion-resistant properties, even when exposed to intense heat or pressure. This makes it suitable for industries such as aerospace, nuclear reactors, and gas turbine engines.
Stainless Steel, on the other hand, is an alloy that comprises mainly iron, with additional elements including nickel, carbon, and chromium. Notable for its resistance to rust and tarnish, Stainless steel can maintain structural integrity in both low and high temperatures. With these properties, stainless steel finds use in diverse areas from food processing equipment to automotive parts and marine applications.
- Inconel: High temperature and pressure resistant; used in aerospace, nuclear reactors, and gas turbines.
- Stainless Steel: Resistant to rusting and maintains stability at various temperatures; used in food processing, automobiles, and marine applications.
The Key Differences Between Inconel and Stainless Steel in Manufacturing
Inconel and stainless steel exhibit significant differences in their properties and performance in extreme temperature CNC operations. Understanding these differences is crucial in selecting the most suitable material for manufacturing parts that will be exposed to extreme temperatures.
Effects of Extreme Temperatures on Material Performance: Inconel vs. Stainless Steel
In machining processes involving extreme temperatures, the choice of material is crucial. High-temperature scenarios can severely impact the performance capacities and physical properties of metals, notably Inconel and stainless steel. Both these materials react differently when exposed to harsh conditions.
- Inconel: This superalloy excels regarding strength and stability even at astronomical temperature levels due to its impressive resistance to oxidation and corrosion. For instance, in jet engines operating under exceedingly hot environments, inconel components retain their structural integrity, successfully resisting degradation and maintaining their hardness.
- Stainless Steel: Although known for its durability and versatility, stainless steel performances lag behind when exposed to extremely high temperatures. Unlike Inconel, it tends to lose a degree of its strength during thermal expansion, leading to deformation or weakness over time. A common illustration of this limitation would be stainless steel cookware that could warp or discolor when consistently subjected to high heat usage.
Hence, understanding how various materials behave under severe temperature fluctuations can guide appropriate selection specific to each CNC operation’s demands, ensuring overall component longevity, safety, and performance efficiency.
Cost Considerations in Using Inconel vs. Stainless Steel
In manufacturing industries, the selection of appropriate material is critical due to its considerable impact on overall costs and operational efficiency. Inconel and stainless steel are two widely used materials, each with its unique characteristics that determine their cost-effectiveness in extreme temperature CNC operations.
The cost of using inconel is generally higher than that of using stainless steel. This price difference arises from a few factors like:
- Material acquisition: The initial purchasing cost of inconel tends to be higher due to it being a nickel-based alloy, and hence more costly to produce.
- Machinability: Inconel’s high strength makes it difficult to machine, thereby increasing operation time, exploiting tool life, and elevating machining expenses.
- Longevity: Yet, it should not be forgotten that inconel exhibits significantly better resistance to heat, corrosion and pressure variations compared to stainless steel; potentially lengthening its lifecycle and offering potential long-term savings.
- Operating Environment: If the operation involves corrosive environments with extreme temperatures, certainly above 1000°F, then Inconel should typically be the material of choice. This is due to its incredible resistance to intense heat and stability over high-pressure ranges.
- Cost-Effectiveness: On the other hand, if the application doesn’t demand such intensive features and budget constraints exist, opting for stainless steel might be the more feasible option as it generally shows decent performance in moderately high-temperature scenarios and proves to be less expensive.
- In contrast, Inconel’s manufacturing process has wider implications for the environment. While it is corrosion-resistant and provides greater durability than stainless steel when used in extreme temperatures, these strengths come at a cost to the environment. Notably, extraction processes for Inconel’s key ingredient, Nickel, pose substantial environmental challenges due to the deforestation and soil degradation associated with mining activities.
- The processing and refining stages for Inconel are more complex and energy-intensive compared to stainless steel, often involving hazardous chemicals- this contributes further to greenhouse gas emissions.
- Lastly, while Inconel can be recycled, overall recycling rates are lower than those for stainless steel.
- Understanding Rivets and Tack Welding Through CNC Machining( lightweight metal Brian)
CNC (Computer Numerical Control) machining is an advanced technology that has revolutionized the manufacturing industry. This transformative technique allows for precise control in processing materials such as metal, plastic, foam,…
- CNC Machining of Stainless Steel: Tips and Common Pitfalls?
CNC Machining and the Importance of Stainless Steel Computer Numerical Control (CNC) machining is a production process whereby pre-programmed computer software directs the movement of factory machinery or tools, enabling…
- Mastering Rivets and Tack Welding in CNC Machining(bending sheet metal Violet)
CNC (Computer Numerical Control) machining has revolutionized the manufacturing industry, enabling the production of complex parts with precision and efficiency. This article aims to shed light on two critical aspects…
Conversely, stainless steel provides manufacturers with lower initial expense but might come with increased maintenance charges due to lesser durability at very high temperatures. Therefore, determining which material offers better value requires balanced consideration between short-term financial concern and eventual functionality or endurance.
Decision Factors: Selecting Between Inconel and Stainless Steel
In choosing between Inconel and stainless steel for extreme temperature CNC operations, there are several factors to consider. The primary consideration is the operational environment including aspects like heat intensity and corrosion potential. Following this, cost-effectiveness also plays a key role as superalloys like Inconel tend to be pricier than standard stainless steel grades.
In particular settings where the initial costs can be justified by long-term benefits, such as in applications demanding high structural integrity or tough aerospace uses, Inconel would potentially provide superior value despite its higher upfront expense.
Environmental Impacts of Stainless Steel and Inconel Use in Manufacturing
Manufacturing plays a significant role in environmental sustainability, with both stainless steel and Inconel presenting distinct footprints. Stainless steel is composed of natural elements such as iron ore, chromium, silicon, nickel, carbon, nitrogen, which are all abundantly available in nature hence its production leads to relatively minimal environmental impact. It is also recyclable making it an even more environmentally friendly metal. The production process involves melting the raw materials in a furnace before casting them into shapes, during this process, energy consumption can be high leading to increased CO2 emissions.
In conclusion, though each material has its unique advantages for specific applications relating mainly to their artisanal functionalities, stainless steel tends toward lesser environmental impacts from a complete lifecycle perspective because of its composition, abundant availability, efficient production, and higher recyclability compared to Inconel.
Case Study: Successful Implementations of Inconel and Stainless Steel in Extreme Temperature Conditions
Both Inconel and stainless steel have showcased successful implementations in real-world scenarios that entail extreme temperature conditions. For instance, Inconel has shown its mettle as a reliable material choice for aerospace engines which are subjected to incredibly high temperatures and pressures. Besides coping with these demanding conditions, it maintains structural integrity over prolonged usage periods thus proving essential for safe air travel.
We find another compelling example in the nuclear industry. Here, Inconel’s resistance to extreme heat and radiation makes it an effective coolant tube material within nuclear reactors. Its impressive durability under such intense conditions helps in preventing catastrophic failures within these systems.
Stainless steel equally shines in high-temperature roles, most prominently in the automobile exhaust systems. Car exhausts frequently deal with extremely hot gases, and standard materials cannot withstand this consistent exposure without warping or breaking down prematurely. But, stainless steel objects can endure such brutal temperature extremes continuously while effectively maintaining their structure and function over time.
In another application; notably, cooking equipment like BBQ grills regularly undergoes intense heat ups and downs – stainless steel implements here prove not just durable, but also sanitary and relatively easy-to-clean improving overall practicality. These case studies bear testimony to each material’s adaptability enhancing extreme-temperature operations across industries.
Other Articles You Might Enjoy
The Knowledge Base
Our Service
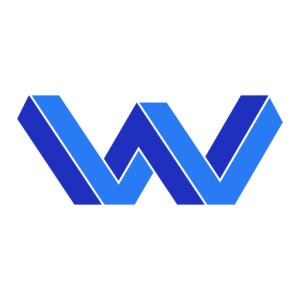
Want.Net Technical Team
The Want.Net Technical Team has diverse members with extensive education and training in CNC machining. They prioritize precision, efficiency, and innovation to provide high-quality manufacturing solutions globally.