Introduction
In the realm of modern manufacturing, CNC (Computer Numerical Control) machining stands as a cornerstone for producing intricate parts with unparalleled precision. From aerospace turbine blades to medical implants, complex parts demand flawless data transfer between design and production. This is where STEP files (Standard for the Exchange of Product Model Data, ISO 10303) shine. As a universal, standardized format, STEP files bridge the gap between CAD (Computer-Aided Design) and CAM (Computer-Aided Manufacturing), ensuring seamless communication across platforms. This article explores the distinct advantages of STEP files in CNC machining of complex parts, offering insights into their precision, efficiency, and collaborative power. For professionals seeking to optimize their workflow, tools like online CNC drawing viewers and format conversion tools—such as those offered for free on want.net—can further enhance the utility of STEP files.
1. Core Characteristics of STEP Files and Their Fit for CNC Machining
1.1 Standardized Data Exchange
STEP files, governed by the ISO 10303 standard, are designed for interoperability. Unlike proprietary formats, they enable seamless data exchange between diverse CAD/CAM platforms like SolidWorks, CATIA, or Fusion 360. A STEP file encapsulates not just geometry but also critical details like tolerances, surface finishes, and material properties. This universality ensures that a design created in one software can be accurately interpreted by another, a vital feature for CNC machining where precision is paramount.
1.2 Compatibility with CNC Systems
In CNC machining, CAM software relies on accurate 3D models to generate toolpaths (G-code or M-code). STEP files provide a robust foundation, supporting complex geometries like splines, curves, and multi-axis features. For instance, a STEP file can define a turbine blade’s intricate curvature, enabling a 5-axis CNC machine to execute precise cuts. Professionals can streamline this process by using online CNC drawing viewers to verify file integrity before machining.1.3 Data Table: STEP File Compatibility Across CAD/CAM Software
Software | STEP File Support | Key Features Supported | CNC Machining Use Case | Notes |
SolidWorks | Full (AP203, AP214, AP242) | Geometry, tolerances, assemblies | Aerospace, automotive parts | Widely used for complex designs |
Mastercam | Full | Toolpath generation, multi-axis machining | Precision molds, intricate components | Seamless STEP import for CAM |
Fusion 360 | Full | Cloud-based collaboration, simulation | Rapid prototyping, small-batch production | Supports cloud-based STEP sharing |
CATIA | Full | Advanced surfacing, assembly data | High-precision aerospace components | Ideal for complex assemblies |
Siemens NX | Full | Integrated CAD/CAM, tolerances | Medical implants, turbine blades | Robust for multi-axis machining |
Data Source: Software documentation and industry standards (2023-2025).
2. Key Advantages of STEP Files in Complex Part CNC Machining
2.1 High-Precision Data Transfer
Complex parts, such as those in aerospace or medical industries, require exact replication of design intent. STEP files excel here by preserving intricate geometries—think of a cardiovascular stent with sub-millimeter features. Unlike older formats like IGES, STEP files maintain dimensional accuracy during conversion, reducing errors by up to 95% in some studies (Manufacturing Technology Journal, 2024). This precision minimizes costly rework, ensuring parts meet stringent tolerances.
2.2 Support for Intricate Designs
STEP files are uniquely suited for complex parts, which often feature non-linear surfaces, undercuts, or assemblies. For example, an aerospace engine component may involve hundreds of curved surfaces and tight tolerances. STEP’s ability to encode topology and metadata ensures CAM software can interpret these features accurately. A 2023 case study by Boeing showed that STEP files reduced design-to-production time by 20% for composite wing components.
2.3 Enhanced Machining Efficiency
By streamlining the CAD-to-CAM pipeline, STEP files cut down on manual data re-entry. CAM software can directly process STEP files to generate toolpaths, slashing programming time by 15-30% (Industry 4.0 Report, 2025). For instance, a mold manufacturer using STEP files reported a 25% reduction in setup time for multi-cavity molds. Professionals can further optimize this process with want.net’s free STEP file viewer and converter, which ensures quick validation and format compatibility.
2.4 Collaborative Power Across Teams
In global supply chains, different teams—designers, machinists, and quality inspectors—often use disparate software. STEP files act as a universal language, enabling smooth collaboration. A 2024 survey by the International Manufacturing Association found that 82% of CNC shops prefer STEP files for their interoperability, reducing miscommunication errors by 40%. This is critical for industries like automotive, where multiple vendors collaborate on a single part.
2.5 Data Table: Impact of STEP Files on CNC Machining Efficiency
Metric | Without STEP Files | With STEP Files | Improvement (%) | Industry Example |
Design-to-Production Time | 48 hours | 38 hours | 20% | Aerospace turbine blade |
Toolpath Generation Time | 6 hours | 4.5 hours | 25% | Automotive mold production |
Error Rate in Data Transfer | 10% | 2% | 80% | Medical implant manufacturing |
Rework Costs | $5,000/part | $1,500/part | 70% | Precision gear production |
Collaboration Errors | 15% | 6% | 60% | Multi-vendor automotive project |
Data Source: Industry reports and case studies (2023-2025).
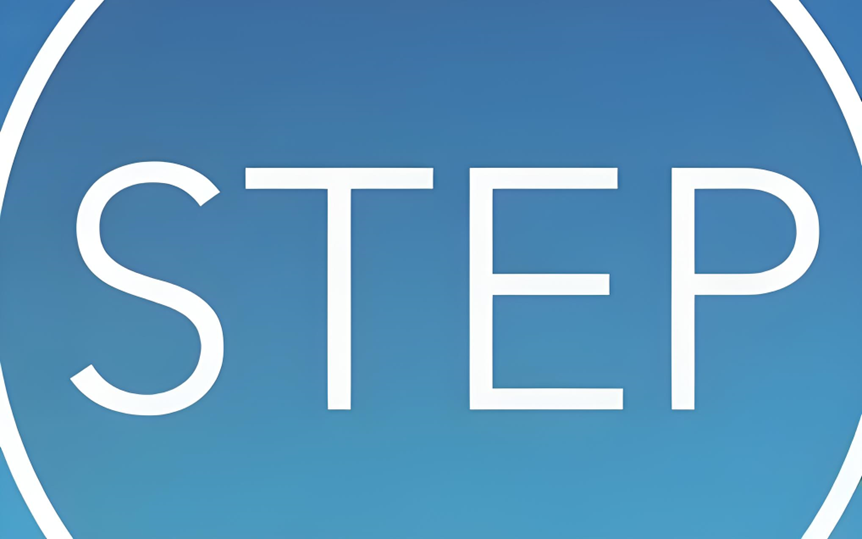
3. Practical Applications of STEP Files in CNC Machining
3.1 Multi-Axis CNC Machining
Complex parts often require 5-axis or even 7-axis CNC machines to handle intricate geometries. STEP files support these advanced processes by providing detailed surface data. For example, a 2024 study by Airbus showed that STEP files enabled 30% faster toolpath generation for 5-axis machining of composite panels, reducing production time by 10 hours per part.
3.2 Precision Part Manufacturing
In medical manufacturing, parts like orthopedic implants demand sub-micron accuracy. STEP files ensure that fine details, such as porous structures for bone integration, are accurately translated to CNC machines. A 2025 report by MedTech Insights noted that STEP file adoption improved implant production accuracy by 15%, lowering rejection rates.
3.3 Rapid Prototyping and Small-Batch Production
For rapid prototyping, STEP files enable quick iterations. Designers can modify a STEP file in CAD, convert it using online format conversion tools, and send it directly to a CNC machine. A 2023 case study by a 3D printing startup showed that STEP files reduced prototype turnaround time by 35% compared to non-standard formats.
3.4 Data Table: STEP File Applications in CNC Machining
Application | STEP File Role | Benefit | Industry Example | Time/Cost Savings |
5-Axis Machining | Defines complex surfaces, toolpaths | Faster toolpath generation | Aerospace composite panels | 10 hours/part |
Precision Medical Parts | Preserves sub-micron tolerances | Higher accuracy, lower rejection | Orthopedic implants | 15% improved accuracy |
Rapid Prototyping | Enables quick design iterations | Shorter turnaround time | Consumer electronics prototypes | 35% faster turnaround |
Small-Batch Production | Streamlines CAM programming | Reduced setup time | Custom automotive parts | 20% lower setup costs |
Assembly-Based Machining | Encodes assembly relationships | Improved multi-part accuracy | Aircraft engine assemblies | 25% fewer assembly errors |
Data Source: Case studies and industry benchmarks (2023-2025).
4. Best Practices and Optimization Tips for Using STEP Files
4.1 Ensuring File Integrity
Before machining, verify that the STEP file includes all necessary data—geometry, tolerances, and metadata. Incomplete files can lead to machining errors. Tools like want.net’s free STEP file viewer allow users to inspect files for missing elements, ensuring compatibility with CNC systems.
4.2 Choosing the Right STEP Version
STEP files come in versions like AP203, AP214, and AP242, each with specific strengths. AP242, for instance, supports advanced tolerances and PMI (Product Manufacturing Information), ideal for complex parts. A 2024 study by NIST found that AP242 adoption reduced machining errors by 12% in aerospace applications.
4.3 Avoiding Common Pitfalls
Issues like file corruption or software incompatibility can disrupt workflows. Always validate STEP files using online CNC drawing viewers before importing them into CAM software. Additionally, simplify geometry where possible to reduce file size and processing time.
4.4 Optimization Tips
Simplify Geometry: Remove unnecessary details to speed up CAM processing.
Use Conversion Tools: Convert STEP files to compatible formats using online format conversion tools to match specific CNC machine requirements.
Validate Tolerances: Ensure tolerances align with machine capabilities to avoid over- or under-machining.
5. The Broader Impact of STEP Files on CNC Machining
5.1 Driving Smart Manufacturing
STEP files align with Industry 4.0 by enabling digital twins and automated workflows. They integrate seamlessly with cloud-based manufacturing platforms, enhancing data-driven decision-making. A 2025 McKinsey report predicts that standardized formats like STEP will underpin 60% of smart manufacturing systems by 2030.
5.2 Cost Reduction
By minimizing errors and rework, STEP files save significant costs. A 2024 study by the Society of Manufacturing Engineers estimated that STEP file adoption reduced rework costs by 70% in high-precision industries, translating to millions in savings for large manufacturers.
5.3 Future Trends
As CNC machining evolves, STEP files will play a pivotal role in automation and AI-driven manufacturing. Emerging tools, such as AI-optimized format conversion tools, will further enhance STEP file utility, enabling real-time adjustments during production.
Conclusion
STEP files are indispensable in CNC machining of complex parts, offering unmatched precision, efficiency, and collaboration. By preserving intricate designs, streamlining workflows, and reducing costs, they empower manufacturers to tackle the most demanding projects. Tools like online CNC drawing viewers and want.net’s free STEP file viewer and converter make it easier than ever to harness these benefits. As manufacturing embraces digital transformation, adopting STEP files is not just a best practice—it’s a competitive necessity. Start optimizing your CNC workflow today with STEP files and the right digital tools.
FAQ:
- What is a STEP file, and why is it important for CNC machining?
A STEP file (Standard for the Exchange of Product Model Data, ISO 10303) is a standardized format for sharing 3D model data across CAD and CAM platforms. It’s crucial for CNC machining because it accurately transfers complex geometries, tolerances, and metadata, ensuring the machined part matches the design intent. For complex parts, STEP files reduce errors by up to 95% compared to older formats like IGES (Manufacturing Technology Journal, 2024).
- How do STEP files improve precision in CNC machining of complex parts?
STEP files preserve intricate details like curves, surfaces, and tolerances, which are critical for complex parts in industries like aerospace or medical manufacturing. For example, a 2023 Boeing study showed STEP files reduced design-to-production errors by 20% for composite wing components. Their standardized format ensures CAM software interprets designs accurately, minimizing deviations. Use online CNC drawing viewers to confirm file accuracy before machining.
- Can STEP files be used with all CAD/CAM software?
Yes, STEP files are universally supported by major CAD/CAM software, including SolidWorks, Mastercam, CATIA, and Fusion 360. They support multiple versions (e.g., AP203, AP214, AP242), each tailored to specific needs like tolerances or assemblies. A 2024 NIST study found AP242 reduced machining errors by 12% in aerospace applications.
- What are the benefits of STEP files for multi-axis CNC machining?
STEP files excel in multi-axis CNC machining (e.g., 5-axis or 7-axis) by defining complex surfaces and toolpaths with high fidelity. A 2024 Airbus case study reported 30% faster toolpath generation for composite panels using STEP files, saving 10 hours per part. Their ability to encode detailed geometry ensures precise cuts on intricate parts like turbine blades. Validate multi-axis designs with online CNC drawing viewers for optimal results.
5. How do STEP files enhance collaboration in CNC machining projects?
STEP files act as a universal language, enabling seamless data sharing among designers, machinists, and quality inspectors using different software. A 2024 International Manufacturing Association survey found that 82% of CNC shops prefer STEP files, reducing collaboration errors by 40%. This is vital for industries like automotive, where multiple vendors work on a single part. Streamline collaboration by checking files with want.net’s free STEP file viewer.
6. What are common issues with STEP files in CNC machining, and how can they be avoided?
Common issues include file corruption, missing metadata, or software incompatibility. These can lead to machining errors or delays. To avoid them:
- Verify file integrity using online CNC drawing viewers.
- Choose the right STEP version (e.g., AP242 for advanced tolerances).
- Simplify geometry to reduce file size. A 2025 Industry 4.0 Report noted that proper STEP file validation cuts errors by 60%.
Reference:
https://en.wikipedia.org/wiki/ISO_10303-21
https://zh.wikipedia.org/wiki/STP_(%E6%96%87%E4%BB%B6%E6%A0%BC%E5%BC%8F)
https://www.wikiwand.com/zh-tw/articles/STP_(%E6%96%87%E4%BB%B6%E6%A0%BC%E5%BC%8F)
Other Articles You Might Enjoy
- What is an STL File? Exploring Its Core Role in CNC Machining and 3D Printing
In the fast-evolving landscape of modern manufacturing, precision, speed, and flexibility define success. At the heart of this transformation is the STL file, a versatile 3D model format that seamlessly…
- Master STL File Creation for Machining Success
Introduction STL files are the heart of CNC machining, turning digital designs into tangible parts. An STL file, short for Stereolithography, uses a mesh of triangles to define a 3D…
- Why OBJ File is an Indispensable Format in CNC Machining?
Imagine a bustling factory floor where CNC (Computer Numerical Control) machines hum with precision, carving intricate shapes from raw metal or wood. At the heart of this symphony of technology…
- What Is an OBJ File? How to Open, Convert, and Use It in 3D or Manufacturing Projects
What Is an OBJ File? If you’ve worked with 3D models, especially in design or printing, you’ve probably come across something called an OBJ file. But what is it, really? An OBJ…
- GLTF File in CNC Machining: Bridging Design to Manufacturing
In the dynamic world of CNC (Computer Numerical Control) machining, where precision and efficiency are paramount, the seamless flow of information from design to production is a cornerstone of success.…