Introduction: Unraveling the Honing Misconception
The term “honing” spans two vastly different worlds: the culinary realm, where a honing steel is a staple for knife maintenance, and the industrial domain, where honing is a cornerstone of precision manufacturing. This semantic duality often leads to confusion, as the honing steel used by chefs to realign a knife’s edge bears little resemblance to the sophisticated abrasive process that perfects internal bores in high-performance machinery. By clarifying the distinction between the honing steel in kitchens and industrial honing, this article provides a comprehensive exploration of both, with a deep dive into the science, tools, and transformative applications of industrial honing in modern manufacturing.
Honing in the Kitchen: The Art of Edge Maintenance with a Honing Steel
In the culinary world, a honing steel is an indispensable tool for keeping knives razor-sharp. Unlike sharpening, which removes significant material to create a new edge, using a honing steel involves realigning the microscopic edge of a blade through plastic deformation. Daily knife use causes the edge to roll or deflect slightly, dulling its performance. A honing steel, typically a slender rod made of steel, ceramic, or diamond-coated material, applies controlled pressure to push the rolled metal back to its original centerline, restoring cutting efficiency. This process, often mistaken for sharpening, is more akin to burnishing, with minimal material removal through adhesive wear forming a subtle micro-bevel as a secondary effect.
Exploring Types of Honing Steels
The honing steel comes in various forms to suit different knives and user preferences:
- Smooth Honing Steel: Ideal for daily maintenance of high-quality kitchen knives, a smooth honing steel gently realigns the edge without aggressive action, preserving the blade’s longevity.
- Grooved Honing Steel: Featuring fine ridges, this type provides slightly more abrasive action, suitable for knives with minor edge damage, offering a balance between maintenance and light material removal.
- Diamond-Coated Honing Steel: Embedded with diamond particles, this honing steel is more aggressive, removing small amounts of metal to restore edges on heavily used or slightly dulled knives.
- Ceramic Honing Steel: Known for its hardness, a ceramic honing steel is perfect for fine-tuning high-carbon steel or premium knives, delivering a polished edge with minimal wear.
Choosing the right honing steel depends on the knife’s material, edge geometry, and usage frequency. For instance, a home cook might prefer a smooth honing steel for regular upkeep, while a professional chef might opt for a diamond-coated honing steel for faster results. This versatility makes the honing steel a critical tool in culinary arts, extending the time between sharpening sessions and ensuring consistent cutting performance.
Industrial Honing: A Science of Precision and Performance
In stark contrast to the honing steel’s role in edge maintenance, industrial honing is a meticulously controlled abrasive machining process designed to perfect the geometry, dimensional accuracy, surface finish, and texture of internal bores. Far from the simple strokes of a honing steel, industrial honing employs a tool head fitted with abrasive stones that rotate and reciprocate within a bore, removing micron-level material to correct imperfections from prior operations like drilling or boring. This process creates a functional micro-topography, essential for components in high-performance internal combustion engines, hydraulic systems, and aerospace machinery. By bridging the gap between the honing steel and industrial honing, this article illuminates the latter’s role as a cornerstone of modern engineering.
Part I: The Physics of Perfection — Mastering Bore Geometry
Industrial honing’s value lies in its ability to transform an imperfect bore into a near-perfect cylinder, driven by unique kinematics and a self-correcting mechanism known as the “averaging effect.”
The Kinematics of Honing
The hallmark of industrial honing is its compound motion: the tool head simultaneously rotates and reciprocates, causing each abrasive grain to trace a helical path along the bore’s surface. Unlike the linear strokes of a honing steel, this non-repetitive path, controlled by the ratio of rotational to reciprocation speed, ensures uniform machining, preventing localized over- or under-cutting. This precision creates consistent geometry and surface texture, critical for high-stakes applications, unlike the edge-focused action of a honing steel.
The Averaging Effect: A Self-Correcting Marvel
Honing’s “averaging effect” sets it apart from other finishing processes, enabling geometric accuracy that can surpass the machine tool itself. Unlike rigid grinding wheels, which transfer their imperfections to the workpiece, honing uses compliant stones under constant radial pressure, guided by the bore’s surface. High spots experience greater cutting force, allowing the stones to preferentially remove material and converge toward an ideal cylindrical shape. This self-correcting process, absent in honing steel applications, ensures exceptional precision, making honing a unique “self-organizing” manufacturing technique.
Correcting Common Geometric Errors
Honing excels at addressing bore imperfections:
- Out-of-Roundness: Elliptical or polygonal bores are corrected as stones remove material from high spots, forming a circular cross-section.
- Taper: CNC honing adjusts dwell time or uses short strokes to equalize diameters along the bore’s length.
- Bow/Camber: Long stones bridge curved bores, straightening the axis for perfect alignment.
These corrections are critical for components like engine cylinders, far beyond the capabilities of a honing steel used for knife edges.
Honing vs. Grinding vs. Lapping: A Comparative Perspective
To understand honing’s unique role, compare it with internal grinding and lapping:
- Honing: A low-speed, surface-contact process using bonded abrasives, it corrects geometry and creates a cross-hatch pattern. Unlike a honing steel, it focuses on bore precision.
- Internal Grinding: A high-speed, point-contact process, it achieves precise size but risks thermal damage and is less effective for long bores.
- Lapping: Using loose abrasives, lapping produces mirror-like finishes but has limited geometric correction, unlike the honing steel or industrial honing.
Table 1: Comparative Analysis of Bore Finishing Processes
Feature | Honing | Internal Grinding | Lapping |
Primary Application | Geometry correction, cross-hatch texture | Precise size and position | Ultra-fine surface finish |
Mechanism | Low-speed, surface-contact cutting | High-speed, point-contact cutting | Loose abrasive micro-cutting |
Abrasive Type | Bonded stones | Bonded wheel | Loose slurry |
Material Removal Rate | Moderate | High | Very Low |
Surface Finish (Ra) | 0.05μm–0.8μm | 0.4μm–1.6μm | <0.1μm |
Geometric Correction | Excellent | Good | Limited |
Surface Feature | Cross-hatch | Grinding marks | Matte/mirror finish |
Caption: Unlike a honing steel for knife maintenance, these processes target bore precision.
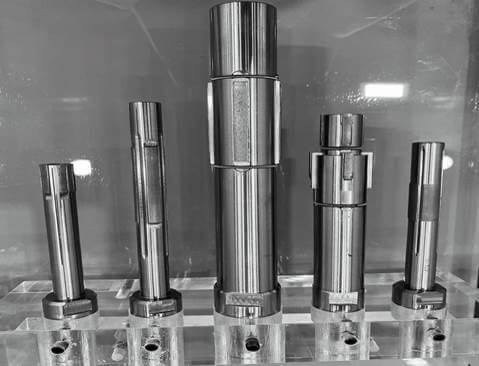
Part II: Engineering Micro-Topography — The Honed Surface
The honed surface is a meticulously engineered micro-landscape, unlike the edge-focused honing steel. Its cross-hatch pattern dictates friction, wear, lubrication, and sealing performance.
The Cross-Hatch Pattern: A Functional Masterpiece
Formed by the helical paths of honing stones, the cross-hatch pattern creates a network of microscopic grooves that retain lubricating oil, reducing friction and wear in components like piston rings. These grooves also act as a “liquid gasket,” enhancing sealing in high-pressure systems like engines, preventing gas leakage (blow-by). This functional design is absent in honing steel applications, which focus on edge alignment.
Optimizing the Cross-Hatch Angle
The cross-hatch angle, determined by the rotation-to-reciprocation ratio, is tailored to specific applications:
- 45° (Included Angle): Balances oil retention and sealing for most engines.
- 60°: Ensures lubrication in long-stroke engines, promoting oil migration to the top dead center.
- 30°: Used in short-stroke racing engines but risks piston ring chatter if too shallow.
Inconsistent angles, known as “stacking,” disrupt oil distribution, a defect irrelevant to honing steel use.
Surface Metrology: Quantifying Performance
Engineers use profilometers to measure surface parameters:
- Ra, Rz: Indicate average roughness and peak-to-valley height but lack functional insight.
- Rk Family: Includes Rk (core roughness), Rpk (peak height), and Rvk (valley depth), quantifying load-bearing area, break-in wear, and oil retention. These metrics, critical for tribological performance, are unrelated to honing steel applications.
Advanced Surface Engineering
Modern honing designs surfaces for specific functions, such as maximizing oil retention (high Rvk) or minimizing break-in wear (low Rpk). This precision, far beyond the honing steel’s scope, links manufacturing to tribological performance, ensuring components meet stringent demands.
Part III: The Arsenal of Precision — Honing Tools and Materials
Industrial honing relies on a tribological system of mandrel, abrasives, and coolant, contrasting with the simplicity of a honing steel.
The Mandrel: Structural Foundation
Mandrels position abrasive stones and guide shoes, with material choice critical for stability:
- Soft Steel: Suitable for general-purpose honing, paired with soft shoes.
- Hardened Tool Steel (58-62 HRC): Resists wear in high-volume or superabrasive applications.
- Bronze: Prevents galling in fine-finish or stainless steel applications.
- Carbide: Ensures longevity in high-wear scenarios.
Unlike a honing steel, mandrels use a cone/wedge mechanism for sub-micron expansion control.
Abrasives: The Cutting Edge
Honing stones determine efficiency and quality:
- Silicon Carbide: Aggressive, for soft materials like aluminum.
- Aluminum Oxide: For medium-hard steels.
- CBN: For hardened steels, offering extreme durability.
- Diamond: For ceramics and carbides, unmatched in hardness.
Bonds (vitrified, resinoid, metal) balance grain retention and cutting efficiency, unlike the static surface of a honing steel.
Coolant: The Lifeblood
Honing fluids lubricate, cool, and flush swarf, using low-viscosity oils with additives like sulfur or chlorine. This ensures dimensional stability and surface quality, a complexity absent in honing steel use.Table 2: Honing Abrasive and Mandrel Selection
Workpiece Material | Goal | Abrasive | Mandrel Material |
Aluminum, Brass | Stock removal | Silicon Carbide | Soft Steel, Bronze |
Cast Iron | Cross-hatch | Silicon Carbide, Diamond | Soft Steel, Tool Steel |
Soft Steel | Finish, control | Aluminum Oxide | Soft Steel |
Hardened Steel | Precision | CBN | Tool Steel |
Carbide, Ceramics | Precision | Diamond | Tool Steel, Carbide |
Stainless Steel | Fine finish | Aluminum Oxide, CBN | Bronze, Carbide |
Caption: Industrial honing systems contrast with the simplicity of a honing steel.
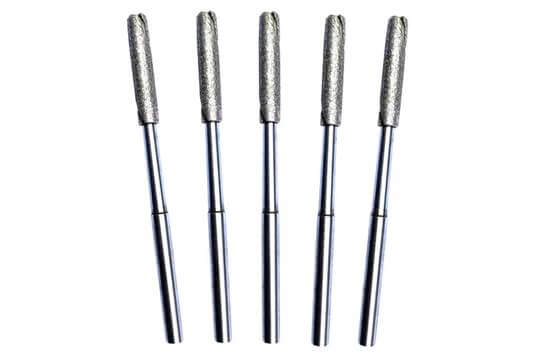
Part IV: Technological Evolution — From Traditional to Advanced Honing
Honing has evolved from basic finishing to functional surface design, far surpassing the honing steel’s role.
Traditional Single-Stage Honing
Early honing used one grit to achieve final size, requiring a lengthy break-in period that accelerated wear. Unlike a honing steel, which maintains edges, this process focused on bore geometry.
Plateau Honing: Pre-Breaking In
Plateau honing creates a “pre-broken-in” surface:
- Rough Honing: Coarse stones (220–280 grit) correct geometry and form deep valleys (high Rvk).
- Finishing: Fine stones (400–600 grit) shave peaks, creating plateaus (low Rpk).
This reduces wear and oil consumption, unlike the honing steel’s edge-focused action.
Helical Slide Honing (HSH): Tribological Innovation
HSH uses a 130°–140° cross-hatch angle, achieved by high reciprocation and low rotation speeds. It reduces friction and oil consumption by over 40%, offering smoother surfaces (lower Sq) than plateau honing, far beyond honing steel capabilities.
Single-Stroke Honing: High-Volume Efficiency
Using a tapered, diamond-coated tool, single-stroke honing completes sizing in one pass, ideal for short bores but lacking cross-hatch or geometric correction, unlike honing steel or multi-stroke honing.
Table 3: Comparison of Honing Technologies
Technology | Kinematics | Cross-Hatch Angle | Goal | Advantage | Application |
Traditional | Rotation + Reciprocation | 45°–50° | Geometry correction | Basic precision | General bores |
Plateau | Multi-step | 45°–50° | Pre-broken-in surface | Low wear | Engine liners |
HSH | High reciprocation | 130°–140° | Friction control | Low oil consumption | Advanced engines |
Single-Stroke | Single pass | None | Efficiency | High consistency | Short bores |
Caption: These technologies advance far beyond the honing steel’s culinary role.
Part V: Applications in High-Stakes Industries
Honing’s precision is critical in demanding sectors, unlike the honing steel’s kitchen applications.
Automotive Engine Cylinders
Honing ensures optimal piston ring sealing, reducing friction, emissions, and oil consumption. CNC honing with torque plates simulates cylinder head stress, ensuring bore accuracy under operating conditions, a precision unattainable with a honing steel.
Hydraulic Valve Bodies
Honing achieves micron-level clearances for smooth spool movement and minimal leakage, ensuring rapid response and reliability in aerospace and machinery. Single-stroke honing creates burr-free ports, unlike honing steel applications.
Aerospace and Medical Applications
In aerospace, honing perfects fuel injector bores for precise flow, while in medical devices, it ensures smooth, biocompatible surfaces for implants. These applications highlight honing’s versatility, far beyond the honing steel’s scope.
Part VI: Honing in the Industry 4.0 Era
Honing is evolving into an intelligent process, unlike the manual honing steel.
Smart Honing with IoT
Modern honing machines use IoT to monitor spindle load, vibration, and stone wear, integrating with Manufacturing Execution Systems for real-time optimization. This connectivity ensures consistent quality, unlike honing steel use.
AI and Machine Learning
AI adjusts parameters dynamically, optimizing feed pressure or speed based on material variations. Machine learning predicts maintenance needs, reducing downtime, a sophistication absent in honing steel applications.
Digital Twins
Digital twins simulate honing processes, enabling virtual process development and continuous optimization. Real-time data synchronizes physical and virtual machines, enhancing efficiency beyond honing steel capabilities.
Part VII: The Future of Honing — Sustainability and Innovation
Honing is poised for further advancements:
- Eco-Friendly Coolants: Biodegradable fluids reduce environmental impact.
- Nano-Abrasives: Enhance surface finishes for ultra-low friction.
- Hybrid Processes: Combine honing with laser texturing for tailored surfaces.
These innovations, unimaginable in honing steel contexts, will drive efficiency and sustainability.
Conclusion: Honing as a Cornerstone of Precision
From the honing steel in kitchens to the intelligent systems of smart factories, honing bridges art and science. Industrial honing functionalizes components through precise geometry and micro-topography, enabling high-performance engines, hydraulics, and aerospace systems. Unlike the honing steel’s edge maintenance, it shapes the future of manufacturing with Industry 4.0 integration. Whether you’re choosing a honing steel for your kitchen or exploring industrial honing solutions, contact us to discover precision finishing at its finest.
FAQ:
- What is the difference between a honing steel and industrial honing?
A honing steel is a tool used in kitchens to realign a knife’s edge, maintaining its sharpness without significant material removal. It works through plastic deformation, pushing the blade’s microscopic edge back into alignment. Industrial honing, in contrast, is a precision abrasive machining process that removes micron-level material to perfect the geometry, surface finish, and texture of internal bores in components like engine cylinders or hydraulic valves. While a honing steel is a manual tool for culinary edge upkeep, industrial honing is a sophisticated manufacturing process for high-performance machinery.
- How often should I use a honing steel on my kitchen knives?
The frequency of using a honing steel depends on knife usage. For home cooks, honing with a honing steel every few uses (e.g., weekly) keeps the edge aligned and extends sharpness. Professional chefs may use a honing steel daily due to frequent cutting. Regular use of a honing steel delays the need for sharpening, which removes more material. Always hone before significant cutting tasks to ensure optimal performance.
- Can a honing steel sharpen a dull knife?
No, a honing steel does not sharpen a dull knife. It realigns the edge to restore cutting efficiency but does not remove enough material to create a new edge. For dull knives, sharpening with a whetstone or electric sharpener is necessary. A honing steel is best for maintenance between sharpening sessions, with types like a diamond-coated honing steel offering slight material removal for minor edge restoration.
- What types of honing steels are available, and which is best for me?
Honing steels come in several types:
- Smooth Honing Steel: Best for daily maintenance of high-quality knives, gently realigning the edge.
- Grooved Honing Steel: Slightly more abrasive, suitable for knives with minor edge damage.
- Diamond-Coated Honing Steel: Aggressive, ideal for heavily used knives needing quick edge restoration.
- Ceramic Honing Steel: Perfect for fine-tuning high-carbon or premium knives, offering a polished edge.
Choose a honing steel based on your knife type and usage frequency. Home cooks often prefer a smooth honing steel, while professionals may opt for a ceramic or diamond-coated honing steel for durability and efficiency. - How does industrial honing differ from grinding or lapping?
Industrial honing uses bonded abrasive stones in a low-speed, surface-contact process to correct bore geometry (e.g., roundness, taper) and create a functional cross-hatch pattern, unlike the edge-focused honing steel. Grinding is a high-speed, point-contact process that prioritizes size and position but risks thermal damage. Lapping uses loose abrasives for mirror-like finishes but offers limited geometric correction. Honing’s “averaging effect” ensures superior precision, making it ideal for engine cylinders and hydraulic systems, far beyond the capabilities of a honing steel.
- Why is the cross-hatch pattern important in industrial honing?
The cross-hatch pattern, created by the helical motion of honing stones, forms microscopic grooves that retain lubricating oil, reducing friction and wear in components like piston rings. Unlike the honing steel’s role in edge alignment, this pattern enhances sealing in high-pressure systems, preventing gas leakage (blow-by) in engines. The angle (e.g., 45° or 60°) is tailored to optimize oil retention and performance, a critical feature absent in honing steel applications.
Reference:
https://zh.wikipedia.org/wiki/%E7%8F%A9%E7%A3%A8
https://www.linguee.com/english-chinese/translation/honing.html
https://zh.wikipedia.org/wiki/%E5%88%87%E5%89%8A%E5%8A%A0%E5%B7%A5
Other Articles You Might Enjoy
- Decoding the Honing Rod: Precision Abrasives in Modern CNC Machining
The honing rod is a term that spans two distinct realms: the culinary kitchen and the high-precision machine shop. In a chef’s hands, a honing rod realigns a knife’s edge…
- Mastering Surface Perfection: The Role of Honing Tools in Modern CNC Machining
In the dynamic world of Computer Numerical Control (CNC) machining, achieving precise dimensions and impeccable surface characteristics is as critical as primary shaping operations. While processes like boring and reaming…
- Precision Perfected: Elevating CNC Surface Finishing with Vapor Honing Technology
Introduction In the competitive landscape of precision CNC machining, achieving a flawless surface finish efficiently and consistently remains a critical challenge. Manual deburring is labor-intensive, time-consuming, and prone to human…
- Precision Perfected: The Science and Strategy of Honing Oil in CNC Machining
Introduction: The Art and Science of Precision Machining In the high-stakes world of modern manufacturing, precision is not just a goal—it’s the cornerstone of success. Industries such as aerospace, automotive,…
- Elevating Surface Finish of CNC Machining Parts with High-Speed Techniques
High-speed cutting techniques have revolutionized CNC machining, offering not only increased production efficiency but also superior surface finishes on machined parts. The appeal of high-speed machining lies in its ability…