Introduction: Navigating the Challenges of Standard Components
In the dynamic landscape of manufacturing, procurement professionals, engineers, and business owners frequently encounter the limitations of off-the-shelf components. For critical parts like plastic clips, issues such as improper fit, suboptimal material selection, or inadequate performance can disrupt assembly lines, cause product failures, and compromise quality. These small yet indispensable custom plastic clips, often crafted through CNC machining, are the unsung heroes securing components in applications ranging from automotive interiors to medical devices, consumer electronics, and industrial equipment. When standard plastic clips fail to meet specific requirements, CNC machining offers a tailored solution to deliver precision and reliability.
For sourcing managers, the idea of commissioning custom CNC machined plastic clips may spark concerns about high costs, extended lead times, and the financial risks tied to traditional manufacturing methods like injection molding. However, CNC machining provides a flexible, cost-effective, and agile alternative, particularly for prototyping, low-to-medium volume production, and applications requiring exacting tolerances. This comprehensive guide is tailored for procurement professionals, buyers, and business owners, offering a strategic framework for sourcing custom plastic clips. It explores the business implications of manufacturing choices, material selection strategies, a detailed procurement workflow, real-world case studies, and emerging trends in CNC machining for plastic clips.
Part 1: Strategic Manufacturing Choices for Plastic Clips
Selecting the optimal manufacturing process for plastic clips is a pivotal business decision that impacts project budgets, timelines, and risk profiles. The two primary methods—CNC machining and plastic injection molding—cater to distinct production scenarios, each with unique advantages and trade-offs.
1.1 CNC Machining vs. Injection Molding: Core Differences
Plastic injection molding is a formative process that involves creating a custom steel mold to shape molten plastic into plastic clips. The upfront investment for mold creation can range from $1,500 for simple designs to over $100,000 for complex, multi-cavity tooling. Once the mold is fabricated, the per-part cost becomes exceptionally low, making injection molding the go-to choice for high-volume production of plastic clips. However, design changes require costly and time-consuming mold modifications, posing significant financial risks if the design is not fully validated.
In contrast, CNC machining is a subtractive process that uses computer-controlled tools to carve custom plastic clips from a solid block of plastic. The absence of tooling costs eliminates the need for large upfront investments, offering a “pay-as-you-go” model. While the per-part cost is higher and remains consistent across quantities, CNC machining excels in prototyping, low-to-medium volume runs, and applications requiring rapid design iterations. This flexibility makes CNC machining a low-risk option for developing plastic clips tailored to specific needs.
1.2 Key Business Factors for Sourcing Decisions
To make an informed choice for plastic clips, procurement professionals must evaluate several critical factors:
- Production Volume: For quantities below 500 plastic clips, CNC machining is typically more cost-effective due to the absence of tooling costs. For volumes exceeding 1,000 units, injection molding’s economies of scale often make it more economical. The 500–1,000 unit range requires careful cost-benefit analysis based on part complexity and project priorities.
- Speed to Market: CNC machining delivers functional custom plastic clips in 5–15 business days, ideal for rapid prototyping or meeting tight product launch deadlines. Injection molding, however, requires 4–8 weeks or more for mold fabrication before production can begin.
- Design Flexibility and Risk Management: CNC machining allows seamless design updates through modifications to digital CAD files, minimizing financial risk during development. Injection molding, by contrast, locks in the design early, and any flaw discovered after mold creation can lead to costly rework or project delays.
1.3 The Economic Crossover Point
The crossover point between CNC machining and injection molding hinges on production volume, project timeline, and risk tolerance. For low-volume runs, CNC machining avoids the high upfront costs of molds, making it ideal for custom plastic clips in early-stage development or niche applications. For high-volume production, injection molding’s low per-part cost becomes advantageous. Table 1 provides a detailed comparison to guide sourcing decisions for plastic clips.Table 1: CNC Machining vs. Injection Molding for Plastic Clips
Business Factor | CNC Machining | Injection Molding | Strategic Sourcing Question |
Upfront Investment | None | High ($1,500–$100,000+) | Can my budget absorb tooling costs? |
Ideal Volume | Low–Medium (<1,000 clips) | High (>1,000 clips) | What is the anticipated production volume? |
Per-Part Cost | Higher, consistent | Low at high volumes | What is the target cost per unit? |
Time to First Parts | Fast (1–2 weeks) | Slow (4–8+ weeks) | How critical is speed-to-market? |
Design Flexibility | High (easy CAD updates) | Low (costly mold changes) | Is the design finalized or likely to change? |
Risk Profile | Low financial risk | High due to tooling | How can I minimize financial exposure? |
1.4 When to Choose CNC Machining for Plastic Clips
CNC machining is the preferred method for plastic clips in the following scenarios:
- Prototyping and Validation: When testing form, fit, or function, CNC machining enables rapid production of custom plastic clips without committing to expensive molds.
- Low-to-Medium Volume Production: For runs under 1,000 units, CNC machining offers cost savings and flexibility, ideal for niche products or custom applications.
- Complex Geometries: CNC machining excels at producing plastic clips with intricate features, tight tolerances, or non-standard shapes that may be challenging for injection molding.
- Urgent Timelines: When speed-to-market is critical, CNC machining delivers custom plastic clips significantly faster than mold-based processes.
- Iterative Design: For projects requiring multiple design iterations, CNC machining minimizes costs and delays by allowing quick adjustments to the CAD model.
1.5 Additional Considerations for Manufacturing Choices
Beyond volume and speed, other factors influence the choice of CNC machining for plastic clips:
- Part Complexity: CNC machining can handle complex features like undercuts, threads, or micro-tolerances that may require expensive mold modifications in injection molding.
- Material Versatility: CNC machining supports a wide range of plastics, from cost-effective ABS to high-performance PEEK, offering flexibility for diverse applications.
- Scalability: While injection molding is suited for mass production, CNC machining can serve as a bridge to validate designs before transitioning to molding for large-scale runs.
Part 2: Material Selection for CNC Machined Plastic Clips
Choosing the right material for CNC machined plastic clips is critical to achieving the desired balance of performance, durability, and cost. While engineers typically specify materials, procurement professionals benefit from understanding the properties, costs, and applications of plastics commonly used in CNC machining. Materials are categorized into three tiers based on performance and cost.
2.1 Tier 1: General-Purpose and Prototyping Plastics
ABS (Acrylonitrile Butadiene Styrene): A cost-effective, versatile plastic ideal for prototyping plastic clips. ABS offers good impact strength and is suitable for form and fit testing in non-demanding environments, such as electronics enclosures or low-stress interior plastic clips. Its limitations include poor resistance to chemicals and UV exposure.
Polypropylene (PP): Lightweight and flexible, PP is another low-cost option for prototyping custom plastic clips. Its chemical resistance makes it suitable for industrial applications, though its lower strength limits its use in high-stress scenarios.
PVC (Polyvinyl Chloride): Known for its chemical resistance and affordability, PVC is used for plastic clips in environments exposed to corrosives, such as plumbing or outdoor applications.
2.2 Tier 2: Workhorse Engineering Plastics
POM (Polyoxymethylene / Delrin®): Renowned for its machinability, POM is a top choice for precision CNC machined plastic clips. Its high stiffness, low friction, and excellent dimensional stability make it ideal for snap-fits, gears, and fasteners in automotive and consumer electronics applications. POM ensures plastic clips maintain performance under moderate stress.
Nylon (Polyamide, PA): Known for its exceptional toughness and wear resistance, Nylon is perfect for durable plastic clips in high-stress environments, such as automotive cable clips or industrial fasteners. Its moisture absorption may affect dimensional accuracy, requiring careful design consideration.
Acrylic (PMMA): Offering optical clarity and moderate strength, Acrylic is suitable for transparent plastic clips in decorative or low-load applications, such as display cases or aesthetic components.
2.3 Tier 3: High-Performance Plastics for Demanding Environments
PEEK (Polyether Ether Ketone): The pinnacle of performance plastics, PEEK offers unmatched strength, chemical resistance, and the ability to operate at temperatures up to 260°C. It is ideal for critical CNC machined plastic clips in aerospace, medical, and automotive applications, such as medical implant clips or engine components. Its high cost is justified by its reliability.
Polycarbonate (PC): Prized for its extreme impact resistance and optical transparency, PC is ideal for rugged plastic clips in safety equipment, electronic housings, and high-impact applications. Its versatility makes it a popular choice for CNC machining projects.
ULTEM (Polyetherimide): A high-performance plastic with excellent thermal and chemical resistance, ULTEM is used for custom plastic clips in aerospace and medical applications requiring sterilization or flame resistance.
2.4 Material Selection Criteria
When selecting materials for CNC machined plastic clips, consider:
- Mechanical Requirements: Assess the stress, friction, and wear the plastic clips will endure.
- Environmental Conditions: Evaluate exposure to chemicals, UV light, moisture, or extreme temperatures.
- Cost Constraints: Balance performance with budget, opting for cost-effective materials like ABS or POM for non-critical applications and reserving high-cost options like PEEK for demanding environments.
- Regulatory Compliance: For medical or aerospace plastic clips, ensure materials meet standards like FDA compliance or flame-retardant certifications.
2.5 Emerging Material Trends
Advancements in material science are expanding options for CNC machined plastic clips. Composite plastics, such as carbon-fiber-reinforced Nylon or glass-filled PEEK, enhance strength and stiffness, making them ideal for high-performance plastic clips in aerospace and automotive applications. Bio-based plastics, derived from renewable sources, are gaining traction for sustainable plastic clips, aligning with environmental regulations and corporate sustainability goals. Additionally, anti-static plastics are increasingly used for plastic clips in electronics to prevent damage to sensitive components.Table 2: Properties of CNC-Machinable Plastics for Plastic Clips
Material | Key Characteristics | Relative Cost | Ideal Applications for Plastic Clips |
ABS | Good impact strength, low cost | Low (●○○○○) | Prototyping, low-stress clips, electronics enclosures |
Polypropylene | Lightweight, chemical-resistant | Low (●○○○○) | Prototyping, industrial clips |
PVC | Chemical-resistant, affordable | Low (●○○○○) | Corrosive environments, outdoor clips |
POM (Delrin®) | High stiffness, low friction, machinable | Mid-Low (●●○○○) | Precision snap-fits, automotive clips |
Nylon 6/6 | Toughness, wear resistance | Mid-Low (●●○○○) | Durable cable clips, high-stress fasteners |
Acrylic | Optical clarity, moderate strength | Mid-Low (●●○○○) | Transparent decorative clips |
Polycarbonate | Extreme impact resistance, transparent | Mid-High (●●●○○) | Safety equipment, rugged clips |
PEEK | Extreme temperature/chemical resistance | High (●●●●●) | Aerospace, medical implant clips |
ULTEM | Thermal/chemical resistance, flame-retardant | High (●●●●○) | Aerospace, sterilizable medical clips |
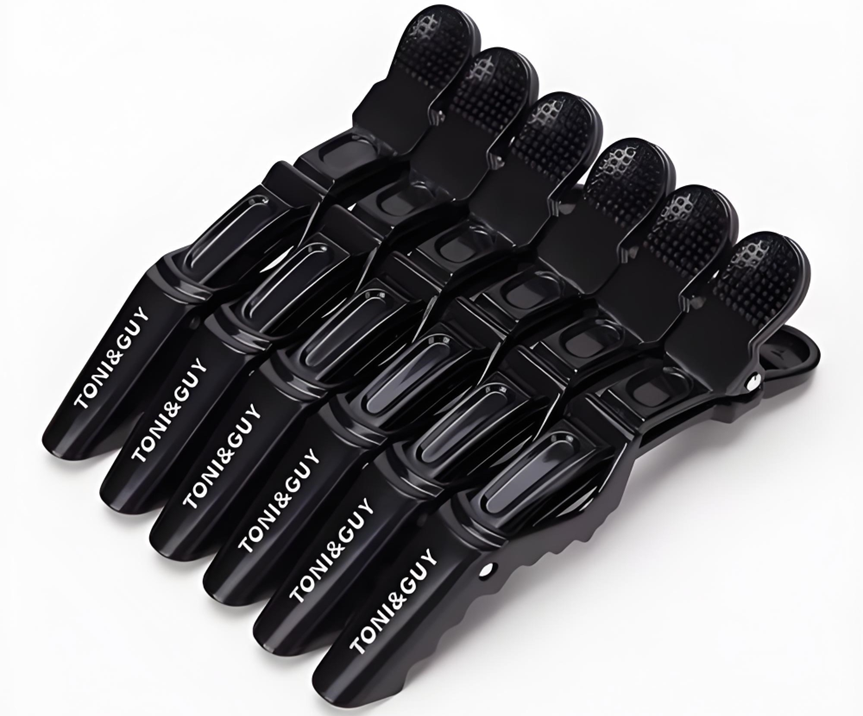
Part 3: The Procurement Workflow for Custom Plastic Clips
Sourcing custom CNC machined plastic clips requires a structured, collaborative process to ensure quality, efficiency, and alignment with project objectives. Below is a detailed workflow to guide procurement professionals.
3.1 Step 1: Prepare a Comprehensive Technical Package
A robust technical package is essential for successful sourcing of plastic clips. It includes:
- 3D CAD Model: The digital blueprint of the custom plastic clips, provided in formats like STEP, IGES, or X_T.
- 2D Engineering Drawing: Specifies dimensional tolerances, material requirements, surface finishes, and features like threads or snap-fits.
- Application Notes: Details the operating environment, load requirements, and regulatory standards to guide material selection and CNC machining processes.
3.2 Step 2: Identify and Vet Suppliers
Choosing the right manufacturing partner is critical for high-quality CNC machined plastic clips. Key criteria include:
- Certifications: Seek ISO 9001 certification for quality assurance. For medical or aerospace plastic clips, verify compliance with standards like ISO 13485 or AS9100.
- Industry Expertise: Select suppliers with experience in your sector (e.g., automotive, medical, electronics) to ensure familiarity with specific requirements.
- Design for Manufacturability (DFM) Feedback: Quality suppliers provide DFM analysis to optimize plastic clip designs for cost and machinability.
- Advanced Equipment: Ensure the supplier uses modern CNC machining technology, such as 5-axis machines, for complex custom plastic clips.
3.3 Step 3: Request for Quotation (RFQ) Process
A detailed RFQ ensures accurate quotes for custom plastic clips. Include:
- The complete technical package.
- Material specifications (e.g., POM, PEEK).
- Required quantity and delivery timeline.
- Secondary operations (e.g., polishing, threading).
Evaluate quotes holistically, considering unit price, lead times, payment terms, and the supplier’s responsiveness to ensure a reliable CNC machining partnership.
3.4 Step 4: From Purchase Order to Production
Upon placing the purchase order, the supplier initiates:
- Contract Review: Verifies alignment with the RFQ and technical package.
- Material Procurement: Sources certified plastics, ensuring compliance with standards like RoHS or FDA.
- CAM Programming: Translates the CAD model into G-code for CNC machining equipment.
- Machining Process: Produces plastic clips with in-process quality checks.
- Secondary Operations: Applies finishes like polishing or threading if specified.
3.5 Step 5: Quality Assurance and Delivery
Before shipping, CNC machined plastic clips undergo rigorous inspection using tools like digital calipers, Coordinate Measuring Machines (CMMs), or optical comparators. Suppliers should provide:
- Inspection Reports: Documenting dimensional accuracy.
- Material Certificates: Confirming material compliance.
- First Article Inspection (FAI): Validating sample parts for critical plastic clips.
Conduct an incoming inspection upon receipt to ensure the plastic clips meet specifications before assembly.
3.6 Addressing Procurement Challenges
Common challenges in sourcing custom CNC machined plastic clips include:
- Incomplete Technical Packages: Missing details can lead to miscommunication. Solution: Collaborate with engineering teams to provide comprehensive documentation.
- Supplier Expertise Gaps: Inexperienced suppliers may deliver subpar plastic clips. Solution: Vet suppliers with industry-specific case studies or references.
- Lead Time Delays: Material shortages or complex designs can extend timelines. Solution: Plan buffer time and partner with suppliers offering expedited CNC machining services.
Table 3: Procurement Challenges and Solutions for Plastic Clips
Challenge | Impact | Solution |
Incomplete Technical Package | Misaligned parts, delays | Provide detailed CAD models and 2D drawings |
Supplier Expertise Gaps | Poor quality, non-compliance | Vet suppliers with industry experience |
Lead Time Delays | Missed deadlines | Use expedited CNC machining, plan buffers |
Cost Overruns | Budget overruns | Optimize designs via DFM, select cost-effective materials |
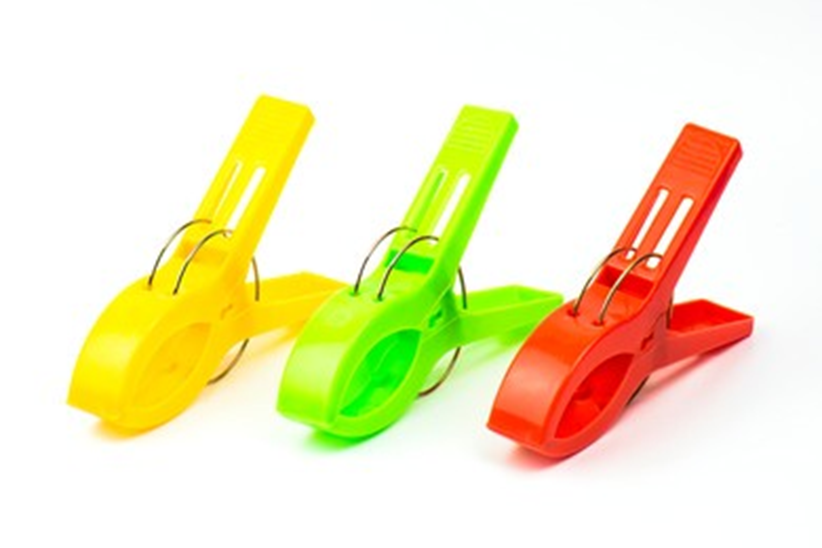
Part 4: Real-World Applications of CNC Machined Plastic Clips
The value of custom CNC machined plastic clips is evident in real-world applications across industries.
4.1 Automotive Industry
A Tier 1 automotive supplier faced production delays due to tolerance mismatches between plastic clips and fasteners sourced from different vendors. By consolidating production with a single CNC machining supplier, the company ensured a perfect fit, resolving assembly issues and accelerating production. In another case, a client required plastic clips with a flawless surface finish for aesthetic interior components. The supplier implemented pre-polishing before CNC machining, achieving a 100% acceptance rate and improving delivery times.
4.2 Medical Device Industry
A medical device manufacturer sought to replace a reusable metal endoscope component with single-use plastic clips to enhance patient safety. Injection molding couldn’t achieve the required 5-micron tolerances to prevent leakage. A hybrid approach—molding the base part and using CNC machining to refine critical features—delivered custom plastic clips that met stringent medical standards at a lower cost than full CNC machining.
4.3 Consumer Electronics
A consumer electronics company developing a wearable device needed lightweight, durable plastic clips for securing internal components. CNC machining with Nylon enabled rapid prototyping, allowing multiple design iterations in weeks. The flexibility of CNC machining ensured the final custom plastic clips met tight tolerances and aesthetic requirements, speeding up the product launch.
4.4 Aerospace Applications
An aerospace manufacturer required plastic clips for securing wiring in a satellite system, using PEEK for its resistance to extreme temperatures and radiation. CNC machining delivered custom plastic clips with precise tolerances, meeting aerospace standards without the high tooling costs of injection molding.
4.5 Industrial Machinery
A manufacturer of heavy machinery needed plastic clips to secure hydraulic lines in harsh environments. CNC machining with Polycarbonate provided durable, impact-resistant plastic clips that withstood vibration and chemical exposure, improving equipment reliability.
Part 5: Advanced Considerations for Sourcing Plastic Clips
5.1 Design for Manufacturability (DFM)
DFM is critical for optimizing CNC machined plastic clips. Suppliers offering DFM feedback can:
- Simplify complex geometries to reduce machining time.
- Adjust tolerances to balance precision and cost.
- Recommend alternative materials to lower expenses without compromising performance.
For example, increasing a fillet radius on a plastic clip can reduce stress concentrations, enhancing durability and machinability.
5.2 Sustainability in CNC Machining
Sustainability is a growing priority in sourcing plastic clips. CNC machining produces less waste than additive manufacturing and supports recyclable plastics like ABS or bio-based materials. Procurement professionals should seek suppliers with sustainable practices, such as recycling machining scraps or using eco-friendly plastics, to align with environmental goals.
5.3 Cost Optimization Strategies
To minimize costs for CNC machined plastic clips:
- Batch Production: Combine multiple designs in a single run to reduce setup costs.
- Material Selection: Use cost-effective plastics like POM for non-critical applications.
- Hybrid Approaches: Leverage CNC machining for prototypes and transition to injection molding for high-volume production.
- Supplier Negotiation: Secure volume discounts or favorable payment terms for long-term projects.
5.4 Future Trends in CNC Machining for Plastic Clips
Advancements in CNC machining are transforming the production of plastic clips:
- Automation: Automated CNC machining systems reduce labor costs and improve consistency.
- Multi-Axis Machining: 5-axis CNC machining enables complex plastic clip designs with fewer setups, lowering costs and lead times.
- Digital Integration: IoT and AI integration allows real-time monitoring of CNC machining processes, enhancing quality control.
- Hybrid Manufacturing: Combining CNC machining with additive manufacturing or injection molding offers new possibilities for cost-effective, high-precision plastic clips.
Part 6: Conclusion: Precision Sourcing with CNC Machining
Sourcing custom CNC machined plastic clips is a strategic endeavor that enhances product quality, reduces risks, and accelerates time-to-market, particularly for prototypes and low-to-medium volume production. By leveraging CNC machining, procurement professionals can achieve precise, reliable plastic clips without the high upfront costs of injection molding. Success hinges on a comprehensive technical package, a trusted CNC machining partner with industry expertise, and a deep understanding of material and manufacturing trade-offs.
To source custom plastic clips that meet your exact specifications, partner with an ISO 9001-certified CNC machining supplier today. Their expertise in CNC machined plastic clips will ensure your project achieves precision, efficiency, and cost-effectiveness, driving your business forward.
FAQ:
1. What are custom CNC machined plastic clips, and why are they important?
Custom CNC machined plastic clips are precision-engineered fasteners or connectors carved from solid plastic blocks using CNC machining. They are critical for securing components in industries like automotive, medical, electronics, and aerospace, where standard plastic clips may not meet specific fit, material, or performance requirements. Their importance lies in ensuring product reliability, reducing assembly issues, and supporting rapid prototyping or low-to-medium volume production.
2. How does CNC machining compare to injection molding for producing plastic clips?
CNC machining is a subtractive process that eliminates tooling costs, making it ideal for prototyping, low-to-medium volume runs (under 1,000 plastic clips), and rapid design iterations. It offers flexibility and quick lead times (5–15 days). Injection molding requires costly molds ($1,500–$100,000+), making it better for high-volume production (over 1,000 plastic clips) but less agile for design changes. CNC machining reduces financial risk and speeds up time-to-market.
3. What materials are best suited for CNC machined plastic clips?
Common materials for CNC machined plastic clips include:
- ABS: Low-cost, ideal for prototyping plastic clips.
- POM (Delrin®): Highly machinable, suited for precision snap-fits and automotive plastic clips.
- Nylon: Tough and wear-resistant, perfect for durable plastic clips in high-stress applications.
- Polycarbonate: Impact-resistant, used for rugged plastic clips in safety equipment.
- PEEK: High-performance for critical plastic clips in aerospace and medical applications.
Material choice depends on mechanical, environmental, and regulatory requirements.
4. What is the typical lead time for CNC machined plastic clips?
CNC machining typically delivers custom plastic clips in 5–15 business days, depending on part complexity, material availability, and supplier capacity. This is significantly faster than injection molding, which requires 4–8 weeks for mold fabrication before production begins. Expedited CNC machining services can further reduce lead times for urgent projects.
5. How can I ensure the quality of custom CNC machined plastic clips?
To ensure quality:
- Provide a comprehensive technical package with 3D CAD models and 2D drawings specifying tolerances and materials.
- Partner with an ISO 9001-certified CNC machining supplier with industry-specific expertise.
- Request inspection reports, material certificates, and First Article Inspection (FAI) for critical plastic clips.
- Conduct incoming inspections to verify compliance before assembly.
6. What industries commonly use CNC machined plastic clips?
CNC machined plastic clips are widely used in:
- Automotive: For securing interior panels, cables, or under-hood components.
- Medical Devices: For single-use clips in endoscopes or implants requiring tight tolerances.
- Consumer Electronics: For lightweight, durable plastic clips in wearables or devices.
- Aerospace: For high-performance plastic clips in wiring or structural applications.
- Industrial Machinery: For impact-resistant plastic clips in harsh environments.
Reference:
https://www.scribd.com/presentation/164891186/Plastic-Cable-Clips
https://en.wikipedia.org/wiki/Clip
Other Articles You Might Enjoy
- Unraveling the World of CNC Machined Plastic Parts(CNC machined plastic parts Mabel)
Modern innovations have taken traditional manufacturing methods to new heights. One such innovation that stands out is Computer Numerical Control (CNC) machining, a process used extensively in various industries from…
- CNC Machined Plastic Parts: An In-depth Overview(CNC machined plastic parts Norman)
Computer Numeric Control (CNC) machining is an advanced manufacturing process where pre-programmed software dictates the movement of factory machinery and tools. These applications can carry out complicated manufacturing tasks with…
- What Is Plastic CNC Machining For Custom Parts
Plastics play a crucial role in today's manufacturing sector since they are widely accessible, generally economical, and suitable for common production techniques like CNC machining, 3D printing, and injection molding.…
- CNC Plastic Machining: Custom Finished Parts for Your Project
In most cases, many people will directly understand CNC machining as a metal workpiece machining process. However, the fact is that CNC machining is not only widely used in metal…
- Understanding the Different Types of Plastic for CNC Machining
Title: Understanding the Different Types of Plastic for CNC Machining Introduction CNC machining, a revered and precise manufacturing process, is not limited to metals and alloys. Plastics, with their versatile…