CNC drilling is a precision machining process utilized extensively in the manufacturing sector where holes of various sizes and depths are created in metal, plastic, or wood with high accuracy. It employs computer numerical control (CNC) systems for automating the movement and operation of the drill bits, yielding consistent and repeatable results that are critical in mass production and complex designs. Among its types are vertical and horizontal drilling, each suitable for specific applications ranging from automotive and aerospace component fabrication to electronics and construction. By utilizing different tools and techniques, such as peck drilling, through-hole drilling, or spot drilling, manufacturers can achieve precise hole specifications tailored to their project’s demands.
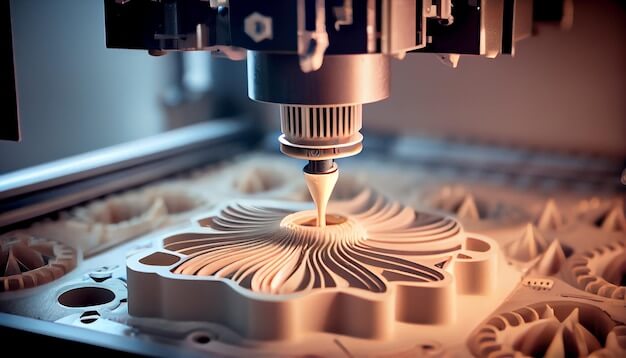
CNC Drilling
Understanding the CNC Drilling Process
Computer Numerical Control (CNC) drilling leverages sophisticated software and automated machinery to achieve precise hole creation in a variety of materials. The operation begins with a digital blueprint, where engineers program the desired dimensions using Computer-Aided Design (CAD) software. This design is then converted into a machine-readable format via Computer-Aided Manufacturing (CAM) software. Upon setup, the CNC drill utilizes pre-decided spindle speeds, feed rates, and depth sequences to execute the task with minimal human intervention. Key advantages include enhanced accuracy, repeatability, increased production speed, and safety compared to manual drilling methods. For example, when drilling circuit board holes, the CNC system can effortlessly replicate minute diameters with exactness across hundreds of units without requiring frequent operator input or supervision.
Types of CNC Drilling Machines
CNC drilling machines come in various configurations, each designed for specific applications. Vertical drilling machines, characterized by their upright structure, are well-suited for quickly making holes in standard material blocks. They effectively handle a variety of workpiece sizes and thicknesses, which makes them suitable for jobs requiring precision and repeatability. On the contrary, horizontal drilling machines stand out with a spindle fixed in a horizontal orientation, often chosen when working on large or heavy workpieces that are challenging to mount vertically. These machines excel at tasks such as creating long, straight holes or when processing objects from the side is necessary. Lastly, there are specialized CNC drilling machines tailored to unique industry needs; these may include multiple axis options for complex patterns, advanced cooling systems crucial for high-intensity drilling, or customized spindles catering to materials like composites.
Materials Suitable for CNC Drilling
CNC drilling is a versatile process that accommodates a variety of materials including metals such as aluminum and steel, plastics like acrylonitrile butadiene styrene (ABS) and polycarbonate, and composite materials which often combine fibers with resin to enhance strength and durability. Selection of material is critical and hinges on the intended application of the final product. For example, aerospace components frequently utilize titanium due to its high strength-to-weight ratio while electrical housings may favor plastics for their insulating properties. The chosen material must not only fit the purpose but also align with the capabilities of the CNC machine, considering factors such as hardness, toughness, and thermal stability, which can impact tool wear and machining efficiency.
Applications of CNC Drilling in Various Industries
CNC drilling plays a critical role across diverse industries by offering precision and efficiency for creating intricate parts. In the aerospace industry, it is instrumental for fabricating high-precision components that meet stringent safety and quality standards. The automotive sector relies on CNC drilling to manufacture parts with complex geometries, ensuring compatibility and performance within tightly controlled engineering specifications. When applied within construction, CNC technology significantly improves the creation of large-scale structural components, streamlining processes and reducing material waste. Additionally, as the demand for smaller, more powerful electronic devices grows, the technology and electronics fields benefit greatly from the miniaturization capabilities and high-accuracy requirements met through advanced CNC drilling techniques.
Innovations in CNC Drilling
Recent technological advancements in Computer Numerical Control (CNC) drilling have significantly enhanced manufacturing efficiency. Newer high-speed spindles, coupled with advanced vibration control systems, allow for faster operation speeds without compromising precision. Furthermore, software plays a crucial role in innovating CNC drilling processes. Developers have integrated intelligent algorithms that optimize tool paths for minimal waste and maximal speed. Adaptive control techniques ensure real-time adjustments during drilling operations to maintain accuracy and prolong tool life. These improvements lead to more accurate and swifter production cycles, illustrating the synergy between hardware upgrades and sophisticated software enhancements in modern CNC drilling applications.
Challenges Faced in CNC Drilling
In CNC drilling, technical challenges often arise from the need to maintain precision and efficiency. For instance, thermal expansion of materials can lead to inaccuracies; a potential solution is implementing real-time monitoring systems that adjust operations according to thermal feedback. Additionally, selecting appropriate drill bit materials and coatings can combat wear and extend tool life. On the environmental front, reducing material waste is paramount. Techniques like using optimized nesting software for material layout and recycling chips and coolants minimize waste and environmental impact. Incorporating these strategies helps address the dual challenges of maintaining high-quality standards while also being mindful of sustainability.
Significance and Future Outlook of CNC Drilling
CNC drilling has cemented its role as a cornerstone in modern manufacturing, affording industries the precision, efficiency, and repeatability crucial for producing complex parts with stringent tolerance requirements. By leveraging computer numerical control, this process eliminates human error, elevates productivity, and enables the creation of intricate designs that would be challenging to achieve manually. Looking ahead, advancements in CNC technology are poised to revolutionize production further by integrating artificial intelligence and advanced analytics for optimized performance and predictive maintenance. This progression will likely lead to smarter, faster, and more energy-efficient CNC drilling machines that can adapt to changing manufacturing needs, reinforcing their impact on future industry landscapes.
Other Articles You Might Enjoy
- CNC Milling vs CNC Drilling? which one to Choose?
Introduction In the context of manufacturing and industrial applications, Computer Numerical Control (CNC) processing plays a crucial role. Two such techniques integral to these operations are CNC milling and drilling.…
- Innovative CNC Machining for Space Exploration Equipment
Innovative CNC Machining for Space Exploration Equipment The technique of Computer Numerical Control (CNC) machining, which involves programming computers to execute precise movements and control machinery tools, has proven significantly…
- Maximizing Precision in CNC Machining: Techniques and Tips
Importance of Precision in CNC Machining Precision is an fundamental component in the field of Computer Numerical Control (CNC) machining. It entails producing parts that are not only accurate but…