According to a report by Grand View Research, the global CNC machining market size was valued at USD 66.6 billion in 2020 and is expected to grow at a compound annual growth rate (CAGR) of 7.0% from 2021 to 2028. The report also notes that the demand for CNC machining services is expected to increase due to the need for mass production of high-quality and precision components.
CNC machining is a subtractive manufacturing process that is widely used to manufacture custom metal parts. Computer numerical control systems provide increasing levels of automation while demanding less manpower.
The milling centers not only perform cutting but also tool changes automatically. Many mill-cutting tools are used in manufacturing a finished object from a block of metal.
Let’s explore the milling machine cutting tools that are used on the machines and their respective functions.
What is Mill Tooling?
A milling cutter is a tool for a milling machine that is used in the machining process of milling to shape an object’s surface. The milling cutter is important to the milling machine’s operation. It is a rotating milling tool and has one or more teeth.
When the cutter is in use, a part of the workpiece is removed by each tooth in turn.
The main purposes of the milling cutter are to mill flat surfaces, steps, grooves, form forms, and cut workpieces.
What Is the Tool for Milling Machine?
There are many different milling cutters on the market with price variations, which enables milling a versatile machining technique. These cutters are available in a variety of forms, sizes, and materials. High-speed steel (HSS) is used in the construction of some CNC milling cutters, whereas carbide tips are used in others.
The following are the types of mill tools that we use in various milling machines:
- Roughing end mill
- Slab mill
- Wood ruff cutter
- End mill cutter
- Fly cutter
- Hollow mill
- Dovetail cutter
- Involute gear cutter
- Thread mill cutter
- Ball mill cutter
- Face mill cutter
- Slide and face cutter
- Hobbing cutter
What Do Milling Cuts Mean?
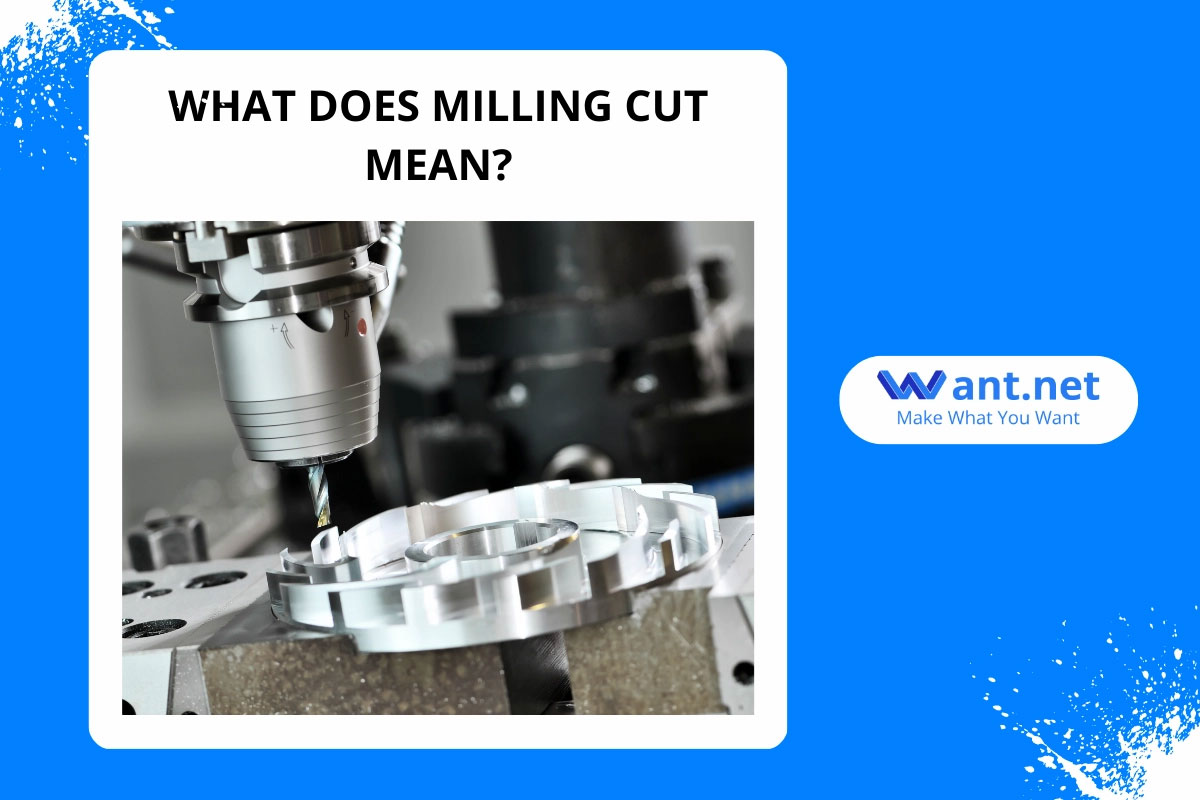
Milling cut is a rotary cutting procedure that uses a milling tool to remove material. This is possible using a wide variety of different milling machine cutting tools with various diameters and harnesses, just like drilling.
The rotating speed needs to be high since the mill is moving in order to produce a hole that is finished cleanly. The objective is to achieve a good balance of movement speed, rotational speed, and required quality.
What are the Purposes of milling?
There are three main types of holes that milling is used for: huge round holes that are unable to be drilled, round slotted holes for connections that need flexibility during construction, and rectangular holes.
What are the Types of Milling Cutters and Their Uses?
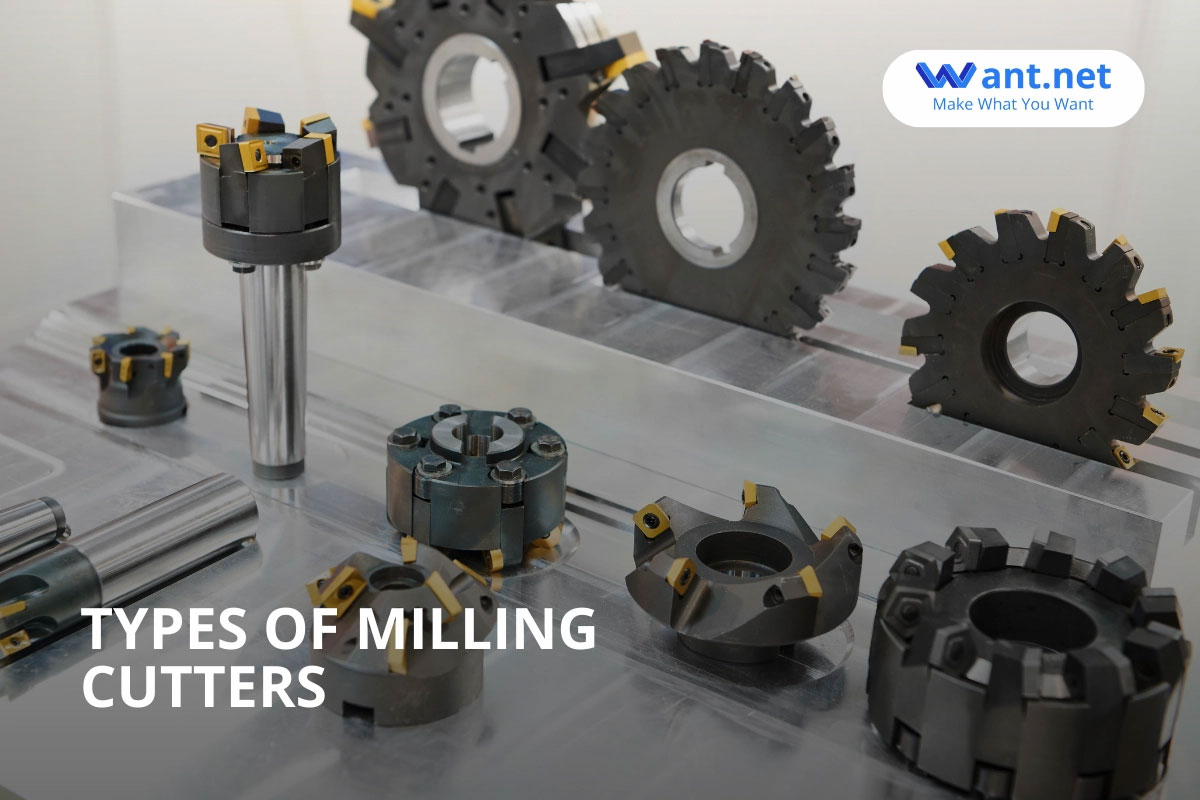
Mill Cutting tools known as milling cutters are commonly used in machining centers or milling machines to carry out milling operations.
The following list of cutters includes descriptions.
1. Roughing End Mill
This cutter is used when a large volume of material must be removed from a work item. We get rough surface finishing by using roughing end mills. They are also known as “Rippa” cutters, roughing end mills. They are used in an array of industrial applications and are more advantageous commercially.
2. Slab Mill
Slab milling cutters often referred to as Plain (Slab) Mills, are used on horizontal milling machines to treat planes. The milling cutter’s circumference is covered with a distribution of cutter teeth. They are separated into straight teeth and spiral teeth based on the shape of the tooth.
There are two types of teeth based on the number of teeth: coarse teeth and fine teeth.
The helical coarse-tooth milling cutter is best for rough machining because it has fewer teeth, a high tooth strength, and a big chip space. Fine-tooth milling cutters are best for finishing. Several milling cutters can be used for wide plane milling, but the combination must include left and right-staggered spiral teeth.
3. End mill
These milling cutters contain teeth for cutting on both sides. End mills are more commonly used in vertical milling processes. These cutters are made of high-speed steel or cemented carbide. It is also known as HS or HSS.
The hardness of the high-speed steel remains constant as the temperature rises. High-speed steel is therefore used to make end mills because of its greater hardness. The majority of end mill applications include tracer milling, plunging and face milling.
4. Hollow Mill
These cutters are also known as hollow milling cutters. They have thicker walls that resemble pipes. The hollow mills’ cutting teeth are placed on the interior surfaces. The screw machines use hollow milling cutters.
5. Ball Mill Cutter
Ball mill cutters are also known as ball-nosed cutters. They have a hemispherical end, which makes you easily recognizable as ball cutters. Ball cutters commonly referred to as ball end mills are used to reduce the stress concentration.
Ball cutters are used whenever cutting three-dimensional shapes is required in order to achieve flawless cutting.
Elaborate Face Mill Vs End Mill?
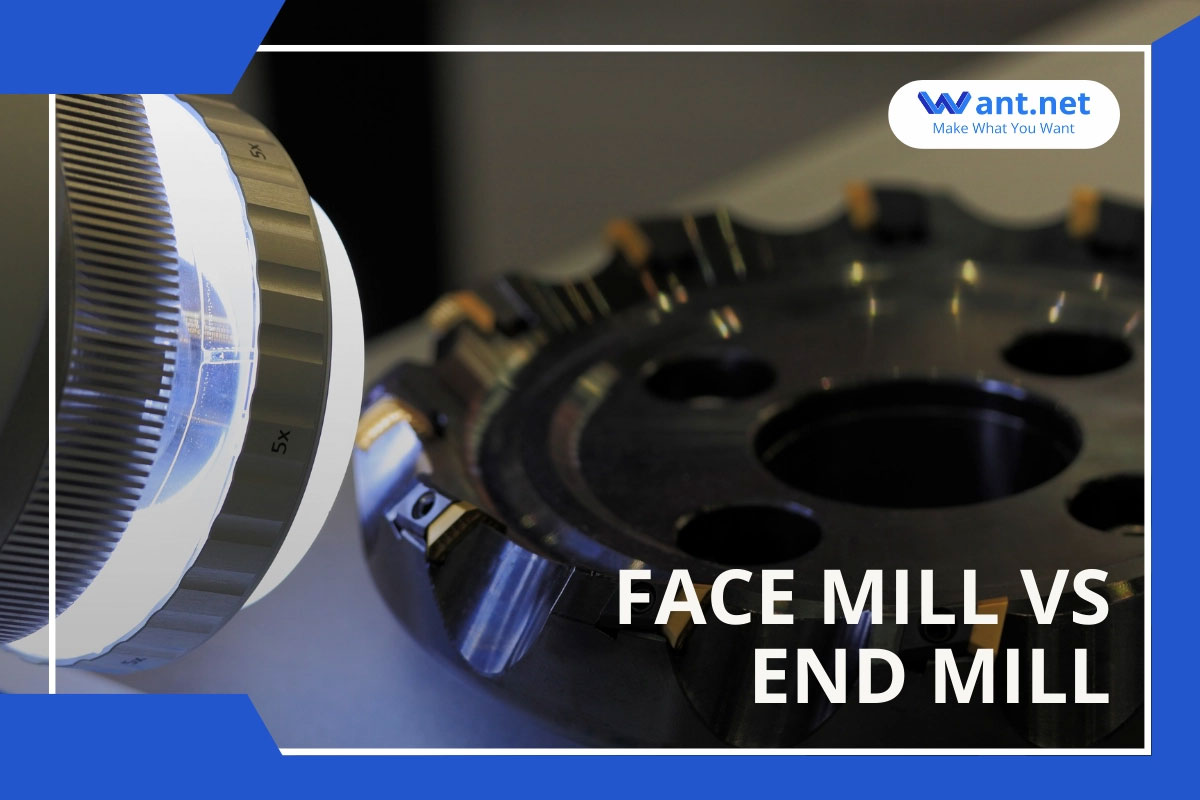
One of the most common questions is the difference between face mill vs end mill. The face mill and the end mill are two common milling processes. They both use different kinds of cutters. End milling and face milling are two different processes since an end mill uses the cutter’s end and sides, whereas face milling is only used for horizontal cutting.
End mills often have flat bottoms. There are also available radiused and round cutters. Drills and end mills both have the ability to cut axially. Yet, the ability to perform lateral cutting gives milling a unique advantage.
Face mills are not able to cut axially. Instead, the sidewalls of the cutting head are where the cutting edges are always located. There are replaceable carbide inserts for cutting teeth.
This increases a tool’s lifespan while maintaining good cutting quality.
What Is Surface Milling Cutter and Its applications?
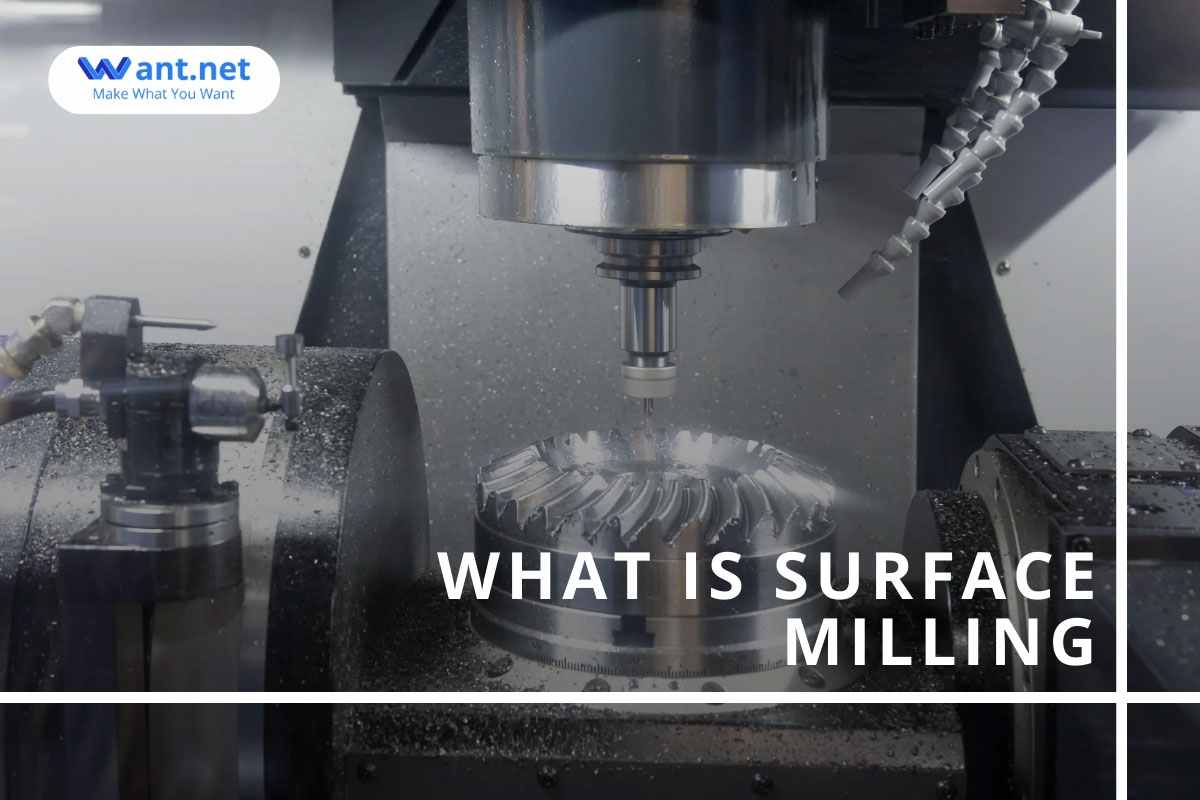
Surface milling cutter has helical or straight teeth and is also known as a slab or plain milling cutters. Moreover, its teeth cut flat surfaces parallel to the cutter axis on cylindrical or peripheral surfaces.
When more material needs to be removed from the workpiece, this kind of cutter is employed. We achieve rough surface finishing by using roughing end mills.
Conclusion
It is important to consider a number of factors when selecting a milling cutter for a CNC milling machine or a standard cutting milling machine, including the material and hardness of the workpiece and the milling cutter’s specifications, including the length of the cutting edge, the tool’s length, the diameter of the cutting edge, and the shank diameter.
Conventional milling machines often use high-speed steel CNC milling cutters, whereas CNC milling machines use cemented carbide blades.
Other Articles You Might Enjoy
- Understanding CNC Turning and Types of Rivets(shell mill Harriet)
CNC (Computer Numerically Controlled) machining is a popular type of subtractive manufacturing technology. Among the various types available, CNC turning stands out due to its efficiency and versatility. On the…
- Exploring CNC Turning and Diverse Rivet Types(shell mill Odelette)
CNC (Computer Numerical Control) turning is a key facet of the machining industry, relied upon for its precision and efficiency in providing bespoke parts. Similarly, rivets, though often overlooked, come…
- CNC Machining with Exotic Alloys: Are They a Game Changer for Your Production?
Introduction: CNC Machining and Exotic Alloys CNC (Computer Numerical Control) machining is a manufacturing process that employs pre-programmed computer software to dictate the movements of factory tools and machinery. It…