Introduction
In the intricate world of CNC machining, bead blasting emerges as a paramount finishing technique, essential for refining the surface quality of machined components. This method employs a stream of abrasive bead media, propelled at high velocity, to cleanse or modify the workpiece’s surface. This intricate process is not only pivotal for eradicating surface flaws but also crucial for enhancing the surface finish and preparing for subsequent treatments like painting or anodizing.
The Bead Blasting Process: Step-by-Step
Step 1: Preparation of the Workpiece and Blasting Area
1.1 Cleaning
The bead blasting journey begins with a meticulous cleaning of the workpiece, aimed at stripping away any lingering residues, oils, or contaminants. This preparatory step is fundamental, ensuring that the subsequent blasting process proceeds without hindrance.
1.2 Masking
Strategic masking follows, safeguarding specific regions of the workpiece from the abrasive onslaught of the blasting media. This precision masking is crucial for preserving critical dimensions and features, maintaining the integrity of the workpiece.
Step 2: Selection of Bead Media
Choosing the right bead media is pivotal and is influenced by the desired outcome and the material of the workpiece.
Table 1: Bead Media Selection Guide
Media Type | Application | Finish Quality |
---|---|---|
Glass | Non-aggressive cleaning, cosmetic finishing | Smooth, satin finish |
Ceramic | Tough cleaning, surface preparation | Matte, slightly rough |
Steel | Heavy material removal, aggressive cleaning | Rough, textured finish |
2.2 Media Size
The size of the bead media significantly impacts the surface finish, with smaller beads yielding a finer finish and larger beads suited for more robust material removal.
Step 3: Setting Up the Blasting Equipment
Proper setup of the blasting equipment is crucial for an efficient and effective bead blasting process.
3.1 Blasting Cabinet
The blasting cabinet should be meticulously cleaned and checked for any remnants from previous operations to prevent cross-contamination.
3.2 Air Compressor and Pressure Settings
The air compressor is calibrated to achieve the optimal pressure setting, which is instrumental in controlling the velocity and impact force of the blasting media.
Step 4: Bead Blasting Operation
4.1 Blasting Technique
A consistent technique in handling the blast gun is essential, maintaining uniform angle and distance to achieve an even surface finish without over-blasting any area.
Figure 1: Optimal Blasting Technique Diagram
A diagram illustrating the recommended angle and distance of the blast gun from the workpiece, highlighting the importance of even sweeps across the surface.
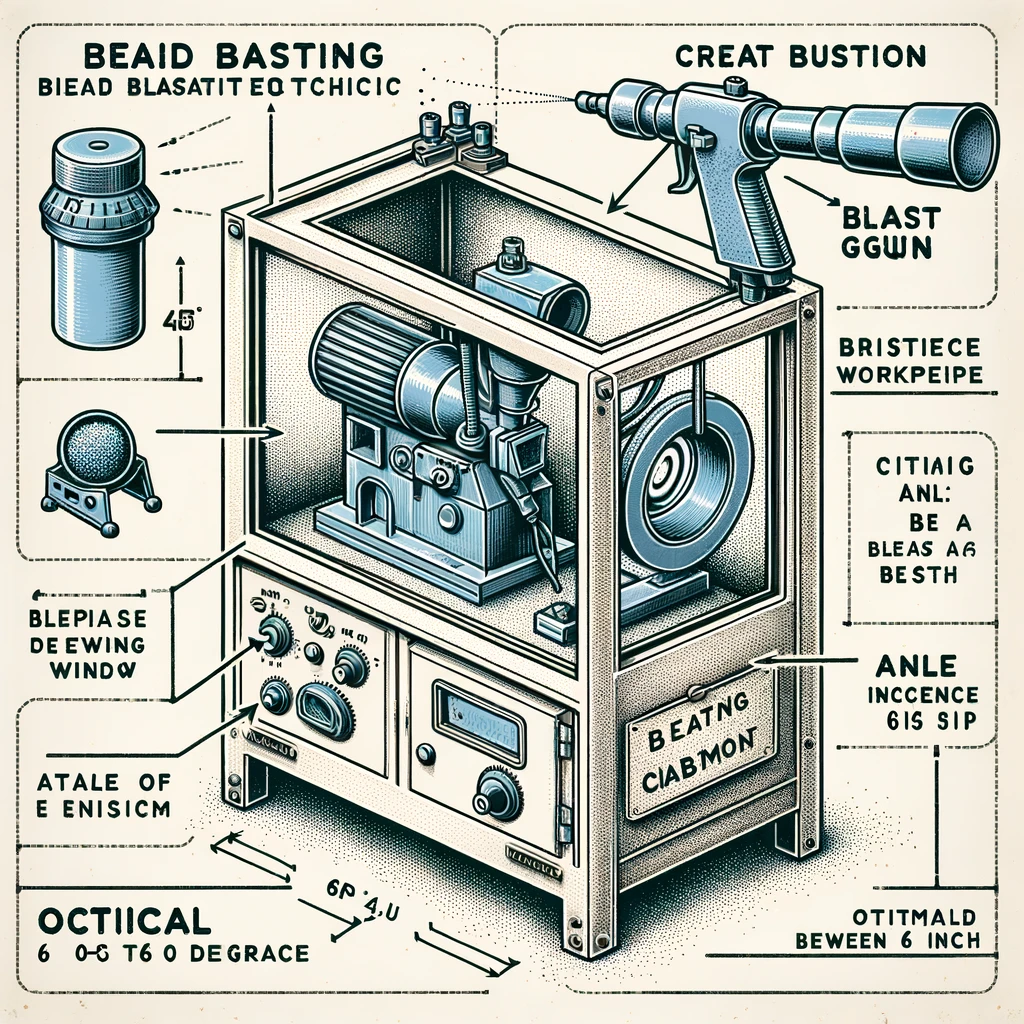
The diagram above illustrates the optimal setup and technique for bead blasting within a blasting cabinet. Key points include:
- The workpiece is securely placed inside the cabinet.
- The blast gun is held at an angle of approximately 45 to 60 degrees relative to the workpiece surface.
- The optimal distance between the blast gun and the workpiece is maintained at 6 to 8 inches to ensure even surface coverage and efficient material removal.
Annotations highlight the crucial components and optimal conditions for bead blasting, providing a visual guide to achieving the best results.
4.2 Monitoring
Vigilant monitoring during the blasting process allows for real-time adjustments, ensuring the desired surface finish is achieved and maintained throughout the operation.
Step 5: Inspection and Quality Control
Post-blasting inspections are critical for ensuring the quality and consistency of the finish.
5.1 Visual Inspection
A thorough visual inspection is conducted to ensure the surface finish is uniform and free from defects, with no areas left unblasted or overblasted.
5.2 Dimensional Inspection
Precision tools measure critical dimensions of the workpiece, confirming that they remain within specified tolerances after the blasting process.
Step 6: Post-Blasting Treatment
6.1 Cleaning
A final cleaning process removes any remaining blasting media and dust, often employing compressed air or a specialized cleaning station to ensure the workpiece is free from contaminants.
6.2 Further Finishing Processes
If necessary, the workpiece may undergo additional finishing processes, such as anodizing or painting, where the bead-blasted surface provides an ideal substrate for subsequent coatings.
Conclusion
Bead blasting is an indispensable process in CNC machining, significantly contributing to the finished parts’ aesthetic and functional qualities. By adhering to a meticulous step-by-step procedure, manufacturers can achieve exceptional surface finishes, enhance the material properties of components, and ensure compliance with stringent industry standards. Through continuous innovation and adherence to best practices, bead blasting will remain a cornerstone of surface finishing in CNC machining.
Other Articles You Might Enjoy
- Ceramic Tooling in CNC Machining: Breaking the Myths About Durability and Performance?
CNC Machining and Ceramic Tooling: Busting the Myths Computer Numerical Control (CNC) machining is an advanced method of manufacturing where pre-programmed software controls the movement of factory machinery, giving intricate…
- Unraveling Bead Blasting Process in CNC Machining(cnc machining china Sid)
Bead blasting is a significant process within the realm of Computer Numerical Control (CNC) machining, providing numerous industries with quality finishes for various types of products. From aircraft parts to…
- Titanium Grade 5 vs. Grade 23 in CNC Machining: Which is the Superior Choice?
Introduction: Understanding Titanium Grades and Their Importance in CNC Machining Titanium, a metallic element well-known for its high strength and low weight, is categorized into different grades based on its…