Injection molding has been the dominant method of consumer manufacturing since the 1950s. It is responsible for everything, from action figures to denture boxes. Injection molding is versatile, but there are some design limitations.
To inject plastic pellets into a mold cavity, heat and press them until they flow in; cool the mold; then open the mold and eject the part. You can repeat this process ten thousand times for one plastic manufacturing run and a million more over the lifetime of the mold. It’s not easy to produce hundreds of thousands of parts. However, there are a few plastic part design modifications that can help. One of the easiest is paying attention to the wall thickness of your design.
Limitations on Injection Molding Wall Thickness
You’ll notice that most of the plastic appliances in your home are approximately 1 to 4mm thick. This is the ideal thickness for molding and the same thickness throughout the whole piece.
Why? There are two reasons.
First, thin walls cool more quicker, reducing the mold cycle time or the time each part takes to make. A plastic part that cools faster after being filled with mold material is easier to eject without warping. Also, because the time spent on the injection machine is more expensive, the cost of producing the part will be lower.
Uniformity is the second reason. In the cooling cycle, the plastic part’s outer surface cools first. Cooling causes contraction. If the part has a uniform thickness, the whole part will shrink from the mold uniformly. The part then comes out smooth.
If the part is made up of thick and thin sections, the molten core of the thicker section will continue to cool after the surface, and thin areas have solidified. It can only pull material off the surface if this thick area continues to cool. This creates a small dimple at the part’s surface, called a sink mark.
Sink marks are a sign of poor engineering in hidden areas. However, on cosmetic surfaces, they can cost thousands to retool. How can you determine if your part is susceptible to injection molding problems? Fictiv offers a tool to help you do this.
Solutions for Thick Walls
There are simple solutions to thick walls. First, identify the problem areas. The part below shows two common problems: thickening around screws and thickening where strength is required.
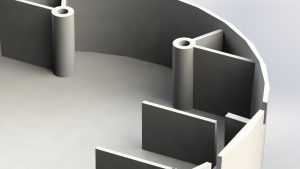
Screw holes in injection-molded parts can be solved using “screw bosses.” This small cylindrical material wraps around the hole and is tied to the rest of the housing with a rib or flange. This will allow for a uniform wall thickness and fewer sink marks.
Ribbing is a simple solution when a part of the piece needs to be particularly strong, but the wall is too thick. You can thin the exterior and add vertical ribs to the interior to make the part more rigid and strong. This allows for easier molding and reduces material requirements, which in turn, lowers costs.
After you have made the necessary changes, you can go back to the DFM tool to verify that the changes were successful. To upload the new part, click on your part, then click on the “Upload revision” option. Once everything is in order, you can test the parts with a 3D printer before manufacturing.
About Want.Net
Want.Net is a reliable manufacturer of injection molding. We have been working in this field for decades. If you have any problems with your order, please don’t hesitate to contact our support team. We are always happy to help. With our fast quoting system, you can get an injection molding online quote easily.
Other Articles You Might Enjoy
- Finishing Options for Injection-Molding
Factors that impact the injection molding surface finish The best way to control the texture of plastic parts is to treat them with a specific finishing process. There are steps…
- Everything You Should Know About ABS Injection Molding
ABS is a common plastic injection molding material that contains three main ingredients. ABS's "A", acrylonitrile, confers hardness, heat, and chemical resistance. The "B", which is butadiene, gives toughness and resistance…
- The Basics of Injection Molding: Procedure, Pros, and Applications
Introduction to Injection Molding Injection molding is a predominant manufacturing process used to create plastic parts by injecting molten material into a specific mold shape. This technique allows for the…