Fasteners are the unsung heroes of engineering, silently ensuring the integrity of everything from life-saving medical implants to spacecraft exploring the cosmos. For decades, metal fasteners dominated due to their strength and reliability. However, a transformative shift is underway, driven by advanced polymer science and precision CNC machining. CNC-machined plastic screws are no longer just lightweight alternatives for low-stakes applications; they are high-performance components engineered to address modern engineering’s most pressing challenges. By leveraging the unique properties of polymers like PEEK, PVC, and nylon, plastic screws offer targeted solutions for corrosion, weight, electrical interference, and biocompatibility. This article explores how plastic screws, crafted with CNC precision, are revolutionizing industries and redefining what fasteners can achieve.
The Evolution of Plastic Screws: From Niche to Necessity
The perception of plastic screws has evolved dramatically. Once relegated to low-cost consumer goods like toys or furniture, plastic screws are now critical in high-stakes industries such as aerospace, automotive, electronics, and medical device manufacturing. This shift is driven by two key factors: advancements in polymer materials and the precision of CNC machining.
Modern polymers, such as Polyether Ether Ketone (PEEK), Polyvinyl Chloride (PVC), and reinforced nylon, offer exceptional mechanical, chemical, and thermal properties. These materials rival or surpass metals in specific applications, particularly when weight, corrosion resistance, or electrical insulation is paramount. Meanwhile, CNC machining enables the production of plastic screws with intricate designs, tight tolerances, and custom specifications, eliminating the need for costly injection molds.
Plastic screws are no longer a compromise but a strategic choice. Their ability to address complex engineering challenges—corrosion in harsh environments, weight constraints in transportation, electrical risks in electronics, and biocompatibility in medical applications—makes them indispensable. Let’s explore these challenges in detail, highlighting how CNC-machined plastic screws provide innovative solutions.
Challenge 1: Corrosion and Chemical Attack
The Problem: Metal’s Vulnerability to Harsh Environments
Metal fasteners, even those treated with coatings, are inherently susceptible to corrosion. In marine applications, saltwater accelerates rust in steel and galvanic corrosion in dissimilar metal assemblies. In chemical processing plants, exposure to acids, alkalis, and solvents degrades metal fasteners, leading to structural failures, maintenance downtime, and safety risks. For example, in offshore oil platforms, corroded bolts can compromise critical infrastructure, costing millions in repairs and posing environmental hazards.
The Plastic Solution: Inherent Corrosion Resistance
Plastic screws made from engineered polymers are immune to rust and galvanic corrosion, offering unmatched durability in aggressive environments. Consider the following materials:
- PVC Plastic Screws: Polyvinyl Chloride is highly resistant to acids, alkalis, salts, and moisture, making it ideal for chemical processing equipment, wastewater treatment systems, and outdoor electrical enclosures. PVC plastic screws maintain integrity in environments that would destroy steel fasteners within months.
- PEEK Plastic Screws: Polyether Ether Ketone is a high-performance polymer that resists a wide range of chemicals, including hydrocarbons, solvents, and hot water. PEEK plastic screws are used in chemical plants, oil and gas equipment, and marine hardware, where they withstand temperatures up to 250°C (482°F) without degrading.
- Nylon Plastic Screws: Reinforced nylon offers excellent resistance to moisture and mild chemicals, making it suitable for less extreme but still corrosive environments, such as agricultural equipment or coastal infrastructure.
The CNC Advantage: Precision and Customization
Unlike injection molding, which requires expensive tooling and long lead times, CNC machining allows manufacturers to produce custom plastic screws from high-performance polymer stock. For instance, a marine engineer designing a submersible sensor housing may need plastic screws with unique thread profiles or lengths to fit a specific assembly. CNC machining delivers these CNC-machined plastic screws with tolerances as tight as ±0.025 mm, ensuring a perfect fit without the cost of custom molds.
Case Study: Marine Applications
In a recent project for a deep-sea exploration vehicle, engineers replaced stainless steel fasteners with PEEK plastic screws to prevent corrosion in saltwater. The CNC-machined plastic screws were tailored to the vehicle’s unique mounting points, reducing maintenance costs by 30% over five years. This example underscores how plastic screws can extend the lifespan of critical equipment in corrosive environments.
Table 1: Corrosion Resistance of Common Fastener Materials
Material | Resistance to Saltwater | Resistance to Acids | Resistance to Alkalis | Max Operating Temperature |
Stainless Steel | Moderate | Low | Moderate | 400°C (752°F) |
PVC Plastic Screws | Excellent | Excellent | Excellent | 60°C (140°F) |
PEEK Plastic Screws | Excellent | Excellent | Excellent | 250°C (482°F) |
Nylon Plastic Screws | Good | Moderate | Good | 120°C (248°F) |
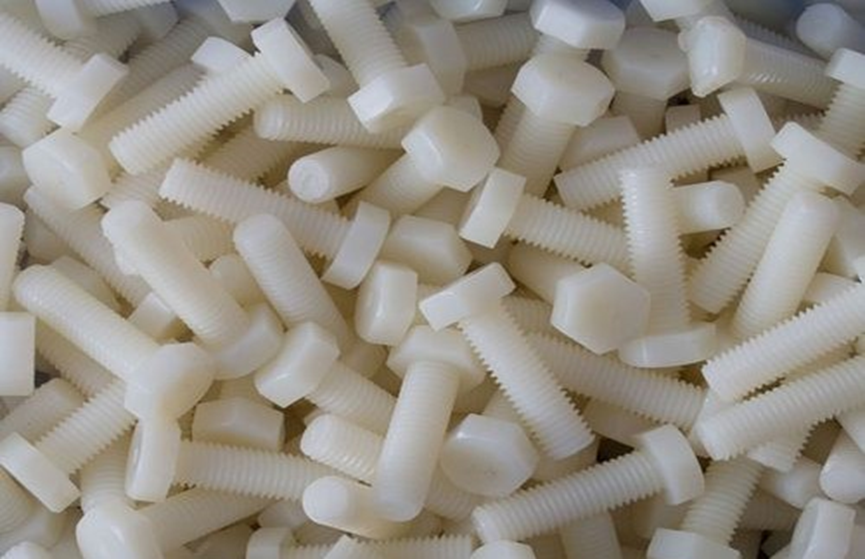
Challenge 2: Weight and Performance
The Problem: The Cost of Excess Mass
In industries like aerospace, automotive, and even consumer electronics, weight is a critical factor. Every gram added reduces fuel efficiency, limits payload capacity, or compromises performance. For example, in commercial aviation, reducing an aircraft’s weight by just 1 kg can save thousands of dollars in fuel costs annually. Fasteners, though small, add up: a single aircraft may use tens of thousands of bolts and screws.
The Plastic Solution: Lightweight Power
Plastic screws offer dramatic weight savings. On average, a plastic screw weighs one-sixth as much as a steel equivalent of the same size. This makes CNC-machined plastic screws a cornerstone of lightweighting strategies across industries:
- Aerospace: PEEK plastic screws are used in non-structural components like cabin interiors, overhead bins, and fairings. Their low density (1.3 g/cm³ compared to steel’s 7.8 g/cm³) reduces aircraft weight without sacrificing strength.
- Automotive: Nylon plastic screws and polypropylene plastic screws fasten interior trim, dashboards, and bumpers. In electric vehicles (EVs), where battery weight is a concern, plastic screws help offset mass, extending driving range.
- Consumer Electronics: Lightweight plastic screws secure components in smartphones, laptops, and wearables, contributing to portability and user comfort.
The CNC Advantage: Prototyping and Composites
High-performance applications often require fasteners made from fiber-reinforced composites, such as carbon-fiber-filled PEEK or glass-filled nylon. These materials are abrasive and difficult to injection mold but are ideal for CNC machining. Engineers can use CNC machining to create prototype plastic screws for testing in real-world conditions, iterating designs quickly without committing to large-scale production.
Case Study: Automotive Lightweighting
A leading electric vehicle manufacturer replaced 2,000 steel fasteners with nylon plastic screws in a sedan’s interior and exterior trim. This reduced the vehicle’s weight by 4 kg, improving range by an estimated 1.5%. The CNC-machined plastic screws were custom-designed to match the vehicle’s aesthetic and functional requirements, showcasing the flexibility of CNC machining.
Table 2: Weight Comparison of Fastener Materials
Material | Density (g/cm³) | Weight of M6 Screw (g) | Typical Applications |
Steel | 7.8 | 6.0 | Structural components |
Aluminum | 2.7 | 2.1 | Lightweight structural parts |
PEEK Plastic Screws | 1.3 | 1.0 | Aerospace, medical implants |
Nylon Plastic Screws | 1.1 | 0.9 | Automotive interiors, electronics |
Challenge 3: Electrical Interference and Safety
The Problem: Conductivity Risks in Electronics
Metal fasteners conduct electricity, posing risks in densely packed electronic assemblies. A stray metal screw can cause short circuits, disrupt high-frequency signals, or lead to catastrophic failures in devices like servers, medical diagnostic equipment, or telecommunications systems. As electronics shrink and complexity grows, these risks become more pronounced.
The Plastic Solution: Natural Insulation
Plastic screws are inherently non-conductive, making them ideal for electronic applications. By using CNC-machined plastic screws, engineers can:
- Secure printed circuit boards (PCBs) without risking shorts.
- Assemble consumer electronics casings, such as smartphones and laptops.
- Mount components in telecommunications equipment, ensuring signal integrity.
Plastic screws eliminate the need for insulating washers, reducing part counts, simplifying assembly, and lowering costs. For example, nylon plastic screws are widely used in PCB mounting due to their affordability and insulation properties.
The CNC Advantage: Precision for Miniaturization
Modern electronics demand micro-sized fasteners to fit compact designs. CNC machining delivers plastic screws with tolerances as tight as ±0.025 mm, enabling the production of tiny, intricate screws for wearables, medical devices, and IoT sensors. This precision ensures CNC-machined plastic screws meet the exacting requirements of next-generation electronics.
Case Study: Telecommunications
A 5G infrastructure project used PEEK plastic screws to secure antenna components, preventing signal interference caused by metal fasteners. The CNC-machined plastic screws were designed with custom thread patterns to withstand vibrational stress, improving equipment reliability by 20%.
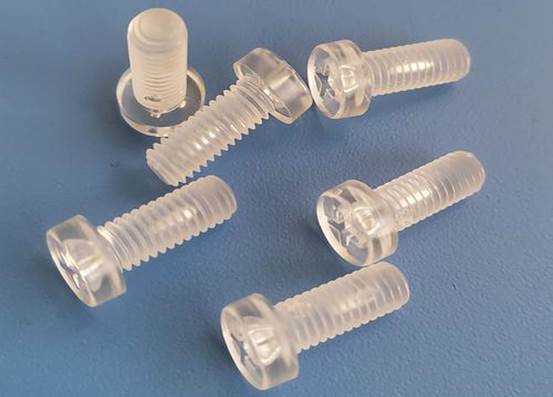
Challenge 4: Biocompatibility and Medical Imaging
The Problem: Stringent Requirements for Medical Devices
Materials used in medical implants must meet rigorous standards: they must be biocompatible, sterilizable, and compatible with imaging technologies like X-rays and MRIs. Metal implants, such as titanium screws, can cause allergic reactions in some patients and create imaging artifacts that obscure diagnostic scans.
The Plastic Solution: PEEK’s Medical Revolution
PEEK plastic screws are transforming medical device manufacturing:
- Biocompatibility: PEEK is accepted by the human body, making it suitable for long-term implants like bone screws and spinal fusion cages.
- Radiolucency: PEEK plastic screws are transparent to X-rays and MRIs, allowing clear imaging of implant sites and surrounding tissues.
- Sterilizability: PEEK withstands repeated sterilization via steam, gamma radiation, or ethylene oxide without degrading.
These properties make plastic screws the gold standard for orthopedic implants, dental devices, and suture anchors.
The CNC Advantage: Patient-Specific Solutions
CNC machining enables the production of patient-specific plastic screws under ISO 13485 medical manufacturing standards. For example, a surgeon may require a PEEK plastic screw with a precise length and diameter for a patient’s spinal surgery. CNC machining delivers these custom plastic screws quickly, improving surgical outcomes and reducing recovery times.
Case Study: Orthopedic Surgery
In a recent spinal fusion procedure, CNC-machined PEEK plastic screws were tailored to a patient’s vertebral anatomy, reducing surgical complications by 15% compared to standard metal screws. The radiolucency of PEEK plastic screws allowed for clearer post-operative imaging, aiding in long-term monitoring.Table 3: Properties of Medical-Grade Fastener Materials
Material | Biocompatibility | Radiolucency | Sterilization Methods | Typical Medical Applications |
Titanium | Good | Poor | Steam, Gamma | Bone screws, dental implants |
PEEK Plastic Screws | Excellent | Excellent | Steam, Gamma, Ethylene Oxide | Spinal cages, suture anchors |
Nylon Plastic Screws | Moderate | Good | Steam, Chemical | Temporary implants, external fixation |
Broader Applications and Future Trends
The versatility of CNC-machined plastic screws extends beyond the core challenges discussed. Here are additional applications and emerging trends:
- Renewable Energy: Plastic screws are used in solar panels and wind turbines, where corrosion resistance and electrical insulation are critical. For instance, PVC plastic screws secure solar panel frames, withstanding UV exposure and weathering.
- Robotics and Automation: Lightweight nylon plastic screws reduce the mass of robotic arms, improving speed and energy efficiency. CNC machining allows for rapid prototyping of custom plastic screws for experimental robotic designs.
- Additive Manufacturing Integration: While CNC machining is subtractive, it complements 3D printing by finishing plastic screws with high precision. Hybrid manufacturing approaches are emerging, combining 3D-printed polymer blanks with CNC-machined threads.
Looking ahead, advancements in polymer science are expanding the capabilities of plastic screws. Bio-based polymers, such as PLA (Polylactic Acid), are being explored for sustainable plastic screws in eco-conscious industries. Additionally, smart polymers with self-healing or temperature-responsive properties could lead to next-generation CNC-machined plastic screws that adapt to environmental conditions.
Why CNC Machining Matters
CNC machining is the linchpin of this revolution. Its ability to produce plastic screws with unparalleled precision and customization sets it apart from traditional manufacturing methods. Key advantages include:
- Flexibility: CNC machines can work with a wide range of polymers, from commodity plastics like PVC to high-performance materials like PEEK.
- Speed: Prototypes and small-batch plastic screws can be produced in days, compared to weeks for injection molding.
- Cost-Effectiveness: By eliminating the need for custom molds, CNC machining reduces upfront costs for bespoke CNC-machined plastic screws.
Overcoming Misconceptions About Plastic Screws
Despite their advantages, plastic screws face skepticism from engineers accustomed to metal fasteners. Common misconceptions include:
- Strength Concerns: While plastic screws may not match steel in tensile strength, materials like PEEK offer tensile strengths up to 100 MPa, sufficient for many applications. Fiber reinforcement further enhances durability.
- Durability Doubts: PEEK plastic screws and nylon plastic screws withstand extreme conditions, from high temperatures to chemical exposure, often outlasting metal in corrosive environments.
- Cost Perceptions: Although high-performance polymers like PEEK are expensive, the long-term savings from reduced maintenance and weight outweigh initial costs.
Education and real-world case studies are dispelling these myths, positioning CNC-machined plastic screws as a go-to solution for forward-thinking engineers.
Conclusion: A New Era for Fasteners
Plastic screws are no longer a secondary option but a strategic asset in modern engineering. Whether combating corrosion in marine environments, reducing weight in aerospace, ensuring electrical safety in electronics, or enabling life-saving medical implants, CNC-machined plastic screws deliver elegant, reliable solutions. By combining advanced polymers with the precision and flexibility of CNC machining, these polymer screws empower engineers to push the boundaries of innovation.
FAQ:
1. What are CNC-machined plastic screws, and how do they differ from metal screws?
CNC-machined plastic screws are fasteners made from advanced polymers like PEEK, PVC, or nylon, precision-crafted using computer numerical control (CNC) machining. Unlike metal screws, plastic screws resist corrosion, are non-conductive, and weigh significantly less—often one-sixth the weight of steel. They excel in applications requiring chemical resistance, electrical insulation, or biocompatibility, such as marine equipment, electronics, and medical implants. CNC machining ensures plastic screws meet tight tolerances (±0.025 mm) and custom specifications without costly molds.
2. In which industries are plastic screws most commonly used?
Plastic screws are widely used in aerospace, automotive, electronics, medical, and renewable energy sectors. For example:
- Aerospace: PEEK plastic screws secure lightweight cabin components.
- Automotive: Nylon plastic screws reduce vehicle weight in interiors and bumpers.
- Electronics: Plastic screws insulate PCBs and prevent short circuits.
- Medical: PEEK plastic screws are biocompatible for implants.
- Renewable Energy: PVC plastic screws withstand weathering in solar panels.
3. Are plastic screws strong enough for heavy-duty applications?
Yes, plastic screws made from high-performance polymers like PEEK offer tensile strengths up to 100 MPa, suitable for many non-structural applications. Fiber-reinforced plastic screws, such as those with carbon or glass fibers, enhance durability for demanding uses like aerospace panels or automotive assemblies. While not as strong as steel, CNC-machined plastic screws provide sufficient strength for specific engineering needs, especially where corrosion resistance or weight savings are critical.
4. How does CNC machining improve the production of plastic screws?
CNC machining allows for precise, custom plastic screws without the need for expensive injection molds. It supports:
- Customization: Tailored thread profiles, lengths, and diameters for unique applications.
- Precision: Tolerances as tight as ±0.025 mm for micro-sized plastic screws in electronics or medical devices.
- Material Versatility: Works with abrasive composites like carbon-filled PEEK, ideal for high-performance plastic screws. This flexibility makes CNC-machined plastic screws cost-effective for prototyping and small-batch production.
5. Can plastic screws withstand harsh environments?
Absolutely. Plastic screws excel in corrosive environments where metal fails. For instance:
- PVC plastic screws resist acids, alkalis, and saltwater, ideal for chemical plants and marine settings.
- PEEK plastic screws handle extreme temperatures (up to 250°C) and aggressive chemicals, perfect for oil and gas or aerospace applications. CNC machining ensures these plastic screws are crafted to precise specifications, enhancing their performance in harsh conditions.
6. Are plastic screws suitable for medical applications?
Yes, PEEK plastic screws are widely used in medical devices due to their biocompatibility, radiolucency (transparency to X-rays/MRIs), and ability to withstand sterilization. CNC-machined plastic screws can be tailored to patient-specific needs, such as custom bone screws for spinal surgeries, meeting stringent ISO 13485 standards.
Reference:
https://en.wikipedia.org/wiki/Screw
https://en.wikipedia.org/wiki/Plastic_extrusion
https://www.sciencedirect.com/science/article/abs/pii/S2214860425002192
Other Articles You Might Enjoy
- Beyond Bronze: How CNC-Machined Plastic Bushings Solve the Core Failures of Metal Components
Executive Summary CNC-machined plastic bushings are transforming industrial applications by addressing the inherent failures of metal bushings. Unlike bronze or steel, plastic bushings eliminate lubrication needs, resist corrosion, and reduce…
- Plastic Washers Too Specific for Off-the-Shelf? CNC Machining Has the Answer
Introduction (Brief) Plastic washers often seem like simple, minor parts. I used to think the same—until I faced an issue where standard off-the-shelf plastic washers just couldn't solve my problem.…
- Unraveling the World of CNC Machined Plastic Parts(CNC machined plastic parts Mabel)
Modern innovations have taken traditional manufacturing methods to new heights. One such innovation that stands out is Computer Numerical Control (CNC) machining, a process used extensively in various industries from…
- CNC Machined Plastic Parts: An In-depth Overview(CNC machined plastic parts Norman)
Computer Numeric Control (CNC) machining is an advanced manufacturing process where pre-programmed software dictates the movement of factory machinery and tools. These applications can carry out complicated manufacturing tasks with…
- How to Select The Right Plastic For Your CNC Machined Parts
One of the most important steps in designing a part is to decide what material it should be made of. If you decide to use plastic, you know there are…