CNC (Computer Numerical Control) machining has revolutionized the manufacturing industry, enabling precise and efficient production of complex parts. One of the key differentiating factors in CNC machining is the number of axes involved in the process. In this article, we will explore the differences between 3-axis, 4-axis, and 5-axis CNC machining techniques and the impact they have on the manufacturing process. Let’s delve into each axis and understand their significance.
3-Axis CNC Machining
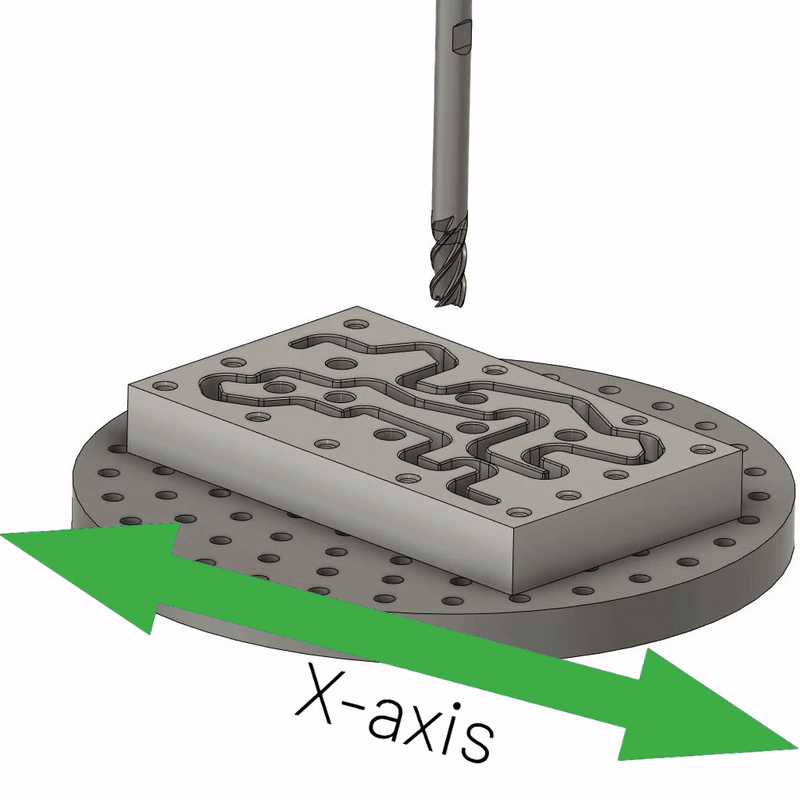
In 3-axis CNC machining, the cutting tool moves along three linear axes: X, Y, and Z. The X-axis represents the horizontal movement, the Y-axis represents the vertical movement, and the Z-axis represents the up and down movement. This configuration allows for the creation of three-dimensional objects and the production of a wide range of CNC machined parts. However, 3-axis machining is limited in its ability to create complex geometries and may require repositioning of the workpiece to access different angles.
4-Axis CNC Machining
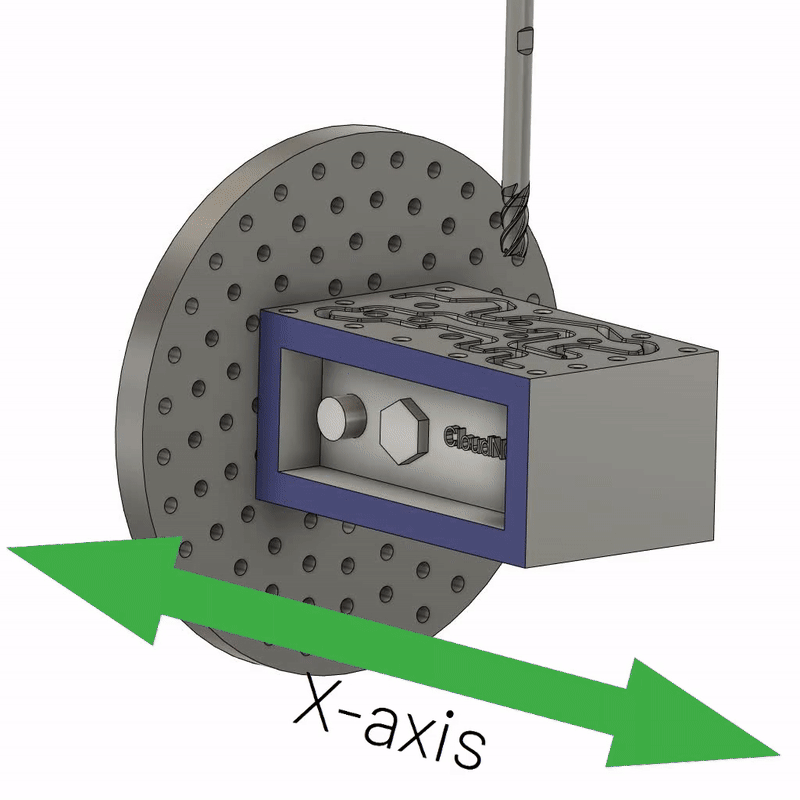
Moving on to 4-axis CNC machining, an additional rotational axis, typically referred to as the A-axis, is introduced. This axis enables the workpiece to rotate around the X-axis, adding more flexibility to the machining process. With the ability to rotate the workpiece, 4-axis CNC machines (including CNC turning and CNC milling machines) can create more complex parts and achieve greater accuracy by reaching multiple sides of the workpiece without repositioning. This capability proves particularly useful when machining cylindrical or curved surfaces.
5-Axis CNC Machining

Now let’s explore the realm of 5-axis CNC machining, which takes versatility and precision to another level. In addition to the X, Y, and Z linear axes and the A-axis, 5-axis machines introduce a second rotational axis known as the B-axis. The B-axis allows the workpiece to tilt or pivot around the Y-axis, providing even greater freedom of movement. With the ability to maneuver the cutting tool from different angles, 5-axis CNC machine excel at producing highly complex parts and achieving intricate geometries with sharp edges.
Advantages of Additional Axes
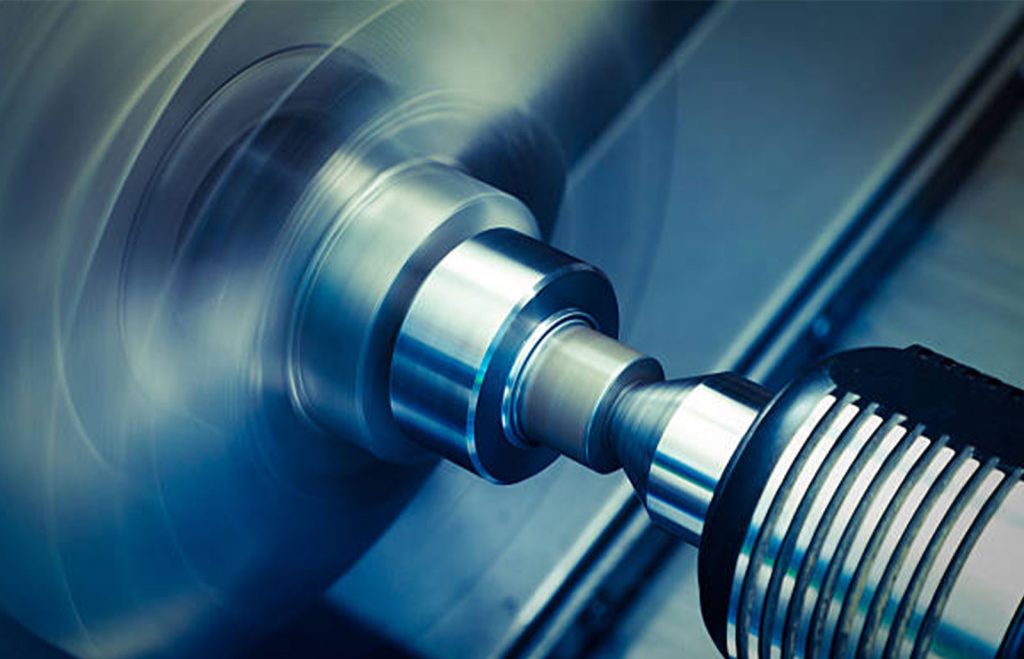
The incorporation of additional axes in CNC machining brings a numerous benefits that significantly enhance the manufacturing process. Let’s delve deeper into these advantages to understand the impact of additional axes on CNC machining operations.
1. Reduced Repositioning Needs
One of the primary advantages of additional axes is the reduction in the need for repositioning the workpiece during the manufacturing process. In 3-axis machining, repositioning is often required to access different angles and surfaces of the workpiece. However, with the introduction of additional axes, such as the A-axis and B-axis in 4-axis and 5-axis machining, the machine can manipulate the workpiece from various orientations without the need for manual repositioning. This results in significant time savings, improved efficiency, and smoother workflow.
2. Streamlined Complex Part Production
The use of additional axes enables the creation of more complex parts in a single setup. With 3-axis machining, intricate geometries may require multiple setups or reorienting the workpiece to machine all the necessary features. However, in 4-axis and 5-axis machining, the ability to manipulate the workpiece along rotational axes eliminates the need for additional setups. This streamlines the production process, reduces the overall production time, and increases productivity. Moreover, by machining complex parts in a single setup, the potential for errors and inaccuracies associated with aligning multiple setups is minimized.
3. Increased Accuracy
The movement of multiple axes in 4-axis and 5-axis machining significantly enhances the precision and accuracy of the machining process. The ability to approach the workpiece from different angles and orientations allows for precise machining of intricate features, tight tolerances, and complex geometries. The rotational axes, such as the A-axis and B-axis, enable the machine to follow the exact contours of the part, resulting in superior surface finishes and intricate detailing. This level of precision is particularly crucial in industries such as aerospace, medical, and automotive, where high accuracy is paramount.
4. Cost and Time Savings
By reducing the need for repositioning, enabling single-setup machining of complex parts, and improving accuracy, additional axes in CNC machining contribute to significant cost and time savings. The elimination of manual repositioning reduces labor requirements and eliminates potential errors associated with aligning multiple setups. Moreover, the streamlined production process allows for faster time-to-market, enabling manufacturers to meet deadlines and customer demands more efficiently. These cost and time savings contribute to improved overall productivity and a competitive edge in the industry.
5. Expanded Design Possibilities
The introduction of additional axes expands the design possibilities for CNC machined parts. Complex geometries, intricate contours, undercuts, and compound angles can be easily achieved with 4-axis and 5-axis machines. This versatility opens up new avenues for innovation and allows designers to push the boundaries of what can be achieved in terms of part complexity and aesthetics. Manufacturers can create highly customized and visually appealing components that meet the evolving demands of various industries.
Applications of Multi-Axis CNC Machining
Multi-axis CNC machining, including 4-axis and 5-axis techniques, finds extensive applications in various industries. The ability to produce complex parts with high accuracy makes it valuable in aerospace, automotive, medical, and defense sectors. Multi-axis machining is particularly advantageous for creating parts with curved surfaces, intricate contours, undercuts, and compound angles. It facilitates the production of prototypes, molds, turbine blades, impellers, and other mechanical components with demanding geometries.
Choosing the Right Technique for Your Project
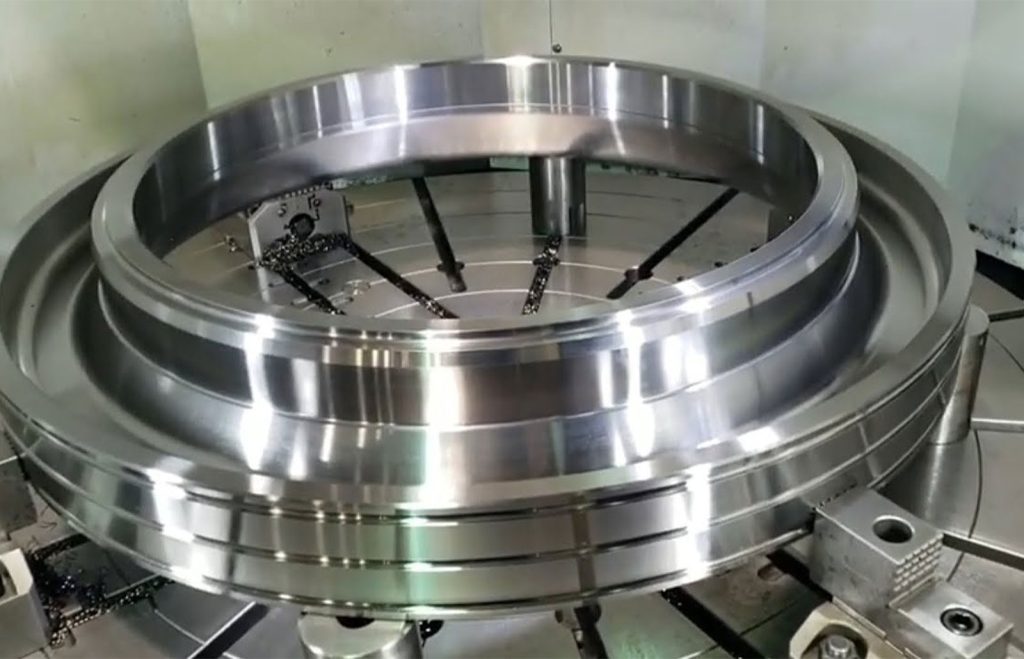
When it comes to selecting the most suitable CNC machining technique for your project, several factors should be taken into consideration. These factors include the specific requirements of your project, the complexity of the parts to be produced, and budget constraints. Let’s explore these aspects in more detail to help you make an informed decision.
Understanding Project Requirements
To determine the appropriate CNC machining technique, it’s crucial to have a clear understanding of your project requirements. Consider the size, shape, and intricacy of the parts you need to produce. If your project involves relatively simple parts with straightforward geometries, 3-axis machining might be a cost-effective and efficient choice. However, if your project requires the production of complex parts with intricate contours, undercuts, or compound angles, 4-axis or 5-axis machining would be more suitable due to their enhanced capabilities.
Assessing Complexity
The complexity of your parts plays a vital role in choosing the right CNC machining technique. If your project involves parts that require machining from various angles and surfaces, such as turbine blades or impellers, the multi-axis capabilities of 4-axis or 5-axis machines are essential. These machines enable you to access and machine multiple sides of the workpiece without the need for repositioning, resulting in improved efficiency and reduced setup time. On the other hand, if your project primarily involves simple, flat parts, 3-axis machining might be sufficient to meet your requirements.
Budget Constraints
Budget considerations are another important factor when selecting a CNC machining technique. Generally, as the number of axes increases, so does the complexity and cost of the machines. 3-axis machines are typically the most affordable option, making them suitable for projects with limited budgets or simpler part requirements. However, it’s important to evaluate the long-term benefits and potential cost savings offered by 4-axis or 5-axis machines. These advanced techniques can often streamline the production process, reduce labor costs, and eliminate the need for multiple setups, ultimately providing a higher return on investment for more complex projects.
Conclusion
In summary, the main difference between 3-axis, 4-axis, and 5-axis CNC machining lies in the number of axes involved and their capabilities. While 3-axis machines provide a solid foundation for manufacturing three-dimensional parts, 4-axis machines introduce rotational movement for enhanced flexibility. 5-axis machines, with two additional rotational axes, offer unparalleled precision and the ability to create complex geometries in a single setup. By choosing the appropriate CNC machining technique, manufacturers can optimize the production of their desired components, taking into account factors such as part complexity, accuracy requirements, and cost considerations.
Remember, CNC machining relies on the coordinated movement of axes and cutting tools to remove material and shape the workpiece. The precise configuration and operation of CNC machines, regardless of the number of axes, require skilled operators and proper maintenance to ensure consistent and reliable results.
Other Articles You Might Enjoy
- Impeller five-axis CNC precision machining technology
The impeller is the most important part on the rotor, and is generally composed of a wheel disc, a wheel cover and a blade. An integral impeller is an impeller…
- Precision 5-Axis CNC Machining in the Automotive Industry
The automotive industry is an integral part of our daily lives, shaping our work commutes and leisure activities. Within this industry, CNC automotive technology plays a pivotal role, transforming the…
- Precision Rotor Blade Prototypes through 5-Axis Machining
Rotor blades are essential components in aero engines, responsible for converting the energy of a flowing medium into mechanical work. While many may find rotor blades mysterious, passionate engineers dedicate…