Rotor blades are essential components in aero engines, responsible for converting the energy of a flowing medium into mechanical work. While many may find rotor blades mysterious, passionate engineers dedicate their minds to perfecting these vital components. Their ultimate goal is to achieve high-precision rotor blade prototypes, ensuring optimal performance. This article delves into the cutting-edge process of creating flawless rotor blades using 5-axis CNC machining, revolutionizing the manufacturing of these critical components.
Understanding the Essence of Rotor Blades
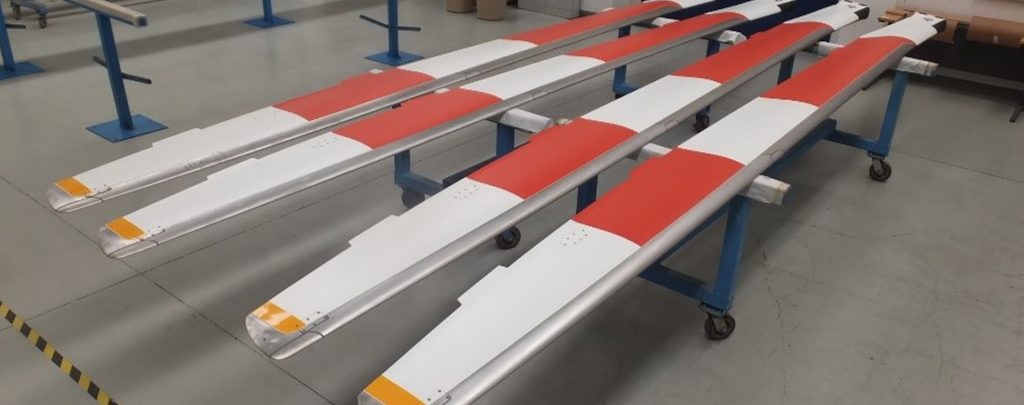
Rotor blades play a significant role in aero engines, gas turbines, and steam turbines. These rotary power machines harness the energy of a flowing medium, transforming it into mechanical work. For engineers with an unwavering commitment to excellence, the creation of a meticulously crafted rotor blade prototype is crucial to ensure optimal performance. But how does one create such a masterpiece using 5-axis CNC machining?
The Background of Rotor Blades
Natural gas combustion stands as one of the world’s largest power generation methods. Gas turbines, responsible for converting natural gas into electrical energy, face a significant challenge during the manufacturing process—the creation of rotor blades. Over time, turbine blade development has evolved from solid blades to intricate hollow designs, eliminating residual blade material and embracing oriented (single crystal) hollow blades. These modern blades exhibit increasingly complex shapes and internal structures.
Machining: Unleashing the Potential
Milling, a CNC machining process that entails material removal using a rotary cutting tool, plays a pivotal role in creating intricate components. Industries such as mold making and aerospace rely on machining to shape freeform surfaces. Turbine blades and impellers, with their intricate designs, are ideal candidates for precision machining operations.
Overcoming Traditional Fixture Challenges
To utilize 5-axis machining for rotor blades, a robust fixture is crucial. However, traditional turbine fixture methods face several limitations:
- Limited clamping force: The size of the cylinder restricts the clamping force, compromising overall effectiveness.
- Complex fixture design: Non-rotating lever arms demand precise coaxiality, imposing high demands on the upper and lower mechanisms.
- Restricted machining space: Upper lever arms consume valuable machining space, placing demands on tools and machining programs.
- Cumbersome installation: Maintenance and air connections prove inconvenient due to poor design and limited versatility.
An Innovative Fixture Solution
To overcome these challenges, an innovative pneumatic spring self-locking fixture was developed. This solution offers the following advantages:
- Freedom in machining features: The fixture allows for flexible tool selection and unrestricted machining paths.
- Enhanced versatility: By modifying positioning blocks and pull studs, the fixture accommodates different part types, increasing overall adaptability.
- Easy installation and maintenance: The lightweight and simplified design of the fixture streamlines installation and maintenance processes.
Machining and Inspecting the Rotor
To ensure consistent and precise blade processing, auxiliary surfaces are created on each side of the blade. These surfaces act as guides for generating tool paths.
The achieved surface quality consistently satisfies requirements, never exceeding 1 μm Ra. Comparing blade roughness, the second blade exhibits lower roughness than the fourth blade.
Challenges arise when machining the other side of the blade, mainly due to the elongated geometry’s lack of rigidity. Audible chattering, blade vibrations, and surface burrs become evident.
To address these issues, a strategy involving machining thin aluminum walls and alternating machining of side channels in multiple stages is implemented. This approach reduces noise, burrs, and improves overall rigidity.
After meticulous deburring and sanding, bead blasting creates an appealing surface finish. Dimensional inspections using CMM (Coordinate Measurement Machine) and 3D scanners ensure high precision, meeting the customer’s requirements of +/-0.005″.
Conclusion
Rotor blades hold significant importance in aero engines and serve as a testament to a company’s capabilities. Want.Net, a professional one-stop prototype provider, excels in the art of crafting rotor parts with intricate structures through 5-axis CNC machining. With their innovative fixture solution and commitment to precision, Want.Net ensures the creation of flawless rotor blade prototypes. If you require exceptional CNC machining or CNC aluminum services, contact Want.Net at [email protected]. Experience the difference of superior prototypes that exceed your expectations.
Recommended Reads
- The Art of CNC Precision Machining: Crafting High-Quality Parts
- Increase Your CNC Production Efficiency with a Robotic Arm
- AI Revolutionizing CNC Manufacturing
- Precision CNC Turning Services: Achieving Unparalleled Precision and Efficiency
- Precision 5-Axis CNC Machining in the Automotive Industry
Other Articles You Might Enjoy
- Precision 5-Axis CNC Machining in the Automotive Industry
The automotive industry is an integral part of our daily lives, shaping our work commutes and leisure activities. Within this industry, CNC automotive technology plays a pivotal role, transforming the…
- Elevating Precision Standards through Chamfer in CNC Machining
1. Introduction: The Pursuit of Unparalleled Precision In the realm of CNC machining, precision is paramount. This section introduces the article by exploring the significance of precision in manufacturing and…
- Precision Prowess: Unveiling the Advantages of China CNC Machining
1. Introduction: The Role of Precision in Manufacturing Excellence In this introductory section, we delve into the critical role that precision plays in manufacturing and set the stage for an…