Electrical discharge machining (EDM), also known as spark machining, is a unique process that sets it apart from conventional machining methods like CNC turning and milling. Unlike those processes that rely on sharp cutting tools, EDM utilizes the erosion of metal through a series of electrical discharges. In this article, we will delve deeper into the fundamental concepts behind EDM manufacturing and explore its construction, applications, pros, and cons.
How Does EDM Work?
Electrical discharge machining employs electric sparks generated by an EDM machine to erode specific sections of a workpiece. These “electric sparks” are actually electric arcs formed between two current-carrying conductors brought in close proximity to each other. The electric arcs generate extreme heat, causing the electrically conductive materials to melt and evaporate. In an EDM process, the workpiece is connected to the positive terminal (anode), while the tool responsible for material erosion is connected to the negative terminal (cathode).
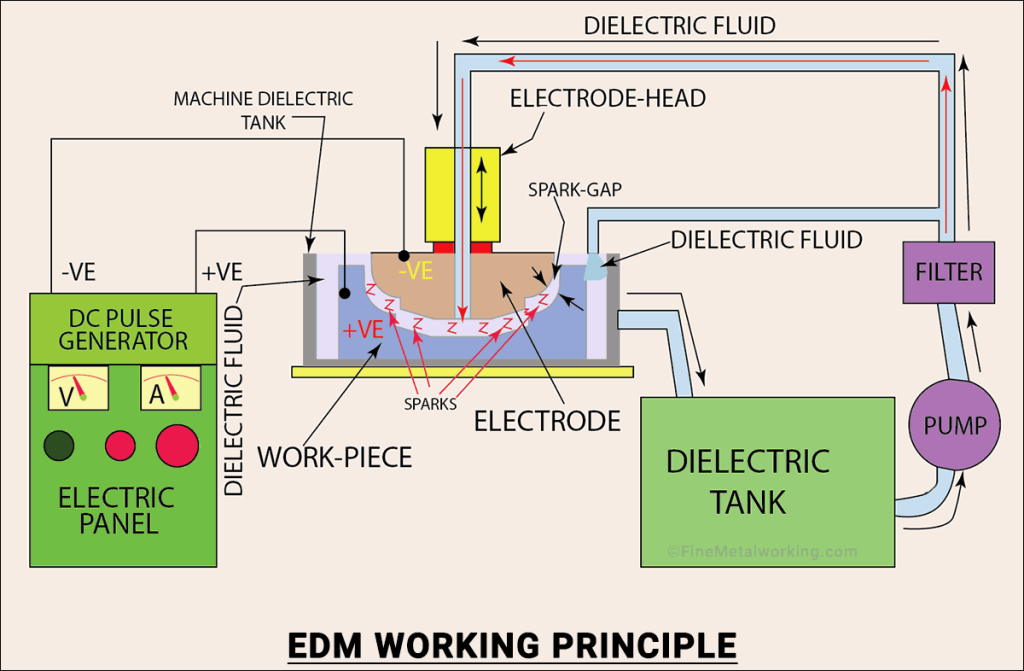
Basic Construction of an EDM System
To understand the working principle of EDM, let’s break down the basic components of an electrical discharge machining system:
- DC Pulse Generator: This component converts the AC power supply into a pulsating DC supply with sufficient voltage to generate sparks between the eroding tool and the workpiece.
- Electrode Tool: The electrode tool is connected to the cathode of the power supply and is mounted on a tool post. Its shape corresponds to the profile left on the workpiece. During the process, a small gap called the arc gap is maintained between the electrode tool and the workpiece. Common electrode materials include copper, tungsten alloy, graphite, steel, and cast iron.
- Servo Motor Mechanism: This mechanism controls the feed and movement of the tool within the EDM machine. The programmed servo motor mechanism precisely controls the arc gap mentioned earlier.
- Spark Generator: The spark generator supplies the necessary voltage for spark generation and discharge maintenance. With the ability to generate up to one hundred thousand sparks per second, significant material removal from the workpiece becomes possible.
- Dielectric Fluid: Both the electrode tool and the workpiece are submerged in a dielectric fluid, which is supplied to the gap between them. The dielectric fluid should circulate at a constant pressure to flush away eroded metal particles. Excessive fluid pressure can slow down the cutting action, while insufficient pressure may cause a short circuit due to unevacuated chips during the erosion process. Common dielectric fluids used include deionized water, glycol, and silicone oil.
- Workpiece: The workpiece, connected to the anode, completes the EDM machine ecosystem. For the process to be effective, the workpiece must be a good electrical conductor.
Types of EDM Processes
EDM processes are categorized based on the shape and approach of the tool used. The three common types in the industry are:
- Wire EDM: This process utilizes a thin wire (usually copper or brass alloy) held by diamond guides to precisely cut two-dimensional shapes on three-dimensional workpieces. The cutting path is controlled by a CNC program, allowing for the creation of complex shapes. Wire EDM is commonly used for cutting metal extrusion dies, punches, and plates.
- Sinker EDM: Also known as ram EDM, sinker EDM employs graphite or copper electrodes shaped in reverse to cut cavities on the workpiece. The tool is machined to match the desired shape left on the workpiece. Sinker EDM is ideal for machining molds used in casting and injection molding, where complex cavity shapes are required.
- Hole Drilling EDM: In this type of EDM process, the electrode tool is used to create extremely thin and deep holes that cannot be achieved with conventional drilling methods. The tool is designed to allow the dielectric fluid to be fed directly through the hole, making it a hollow electrode. Hole drilling EDM does not produce burrs on the workpiece and is commonly used for machining relief holes on turbine blades, dies, and molds.
Applications of EDM Machining
EDM machining is highly capable of producing intricate shapes and geometries, making it suitable for precise applications where conventional machining falls short. Let’s explore some common applications of EDM machining:
- Small Hole Drilling: Manufacturers often turn to EDM machining for drilling extremely tiny holes, reducing the risk of tool deflection and damage. EDM machined holes can be incredibly small and are found on turbine blades, microscopic orifices in fuel system components, and more.
- Mold and Die Making: EDM machining complements conventional machining in mold and die fabrication. Wire EDM is used for forming blanks, sinker EDM for creating complex cavity shapes, and hole drilling EDM for pressure release holes.
- Component Disintegration: The EDM machine is used to remove stuck metal components that cannot be extracted by conventional means. Disintegrating these components involves selectively removing the material without causing damage. Examples include sheared bolts, stuck tooling, or pins lodged in delicate parts.
- Medical Components: EDM machined products produce burr-free surfaces, making them ideal for manufacturing various medical implant components.
- Aerospace Components: EDM machining tackles features on aerospace parts that cannot be achieved with standard cutting tools. It excels at producing challenging features like turbine rotor discs, thin slots, sharply squared holes, and tight deep holes.
Why is EDM Preferred?
Highly Capable of Machining Complex Profiles: EDM provides greater cutting freedom compared to conventional machining operations. It can easily create intricate pockets, fine deep holes, thin walls, and irregularly shaped geometries that are often impossible with end mills and drills.
High Accuracy: EDM technology achieves precision up to the smallest tolerances in the metal manufacturing industry. The process applies minimal stress to the workpiece and avoids aggressive vibrations. Additional skimming processes can enhance precision and accuracy.
Burr-free Surface Finish: EDM machining results in burr-free workpieces because the eroded metal disintegrates into microparticles that are flushed away. Unlike end mills, saws, and drills, EDM cutting does not involve sharp cutting tools that can cause burrs.
Ability to Cut Hard Metals: EDM machining can effortlessly cut hard metals with low force, as long as they are conductive. The hardness of the material does not affect the overall process.
Low Stress: Unlike other machining methods where cutting tools contact the surface, EDM tools do not touch the workpiece directly, minimizing stress on the material.
Highly Scalable Manufacturing: EDM machining processes are versatile and suitable for low to high-volume manufacturing. They offer high repeatability, ensuring consistent quality across multiple parts.
Limitations of the EDM Process
Limited Applicability to Conductive Materials Only: EDM machining relies on electrical discharges for material erosion, making it unsuitable for non-conductive materials like composites and plastics.
Low Material Removal Rate: EDM machining removes material gradually, resulting in slower material removal rates compared to conventional milling and turning processes.
Higher Production Costs: EDM production costs encompass factors such as high power consumption, increased tool wear, and longer machining times.
Summary
Electrical discharge machining (EDM) serves as a valuable addition to conventional CNC machining processes. It excels at producing special features that are challenging to achieve through milling and turning. With exceptional accuracy in cutting hard, electrically conductive metals, EDM machining minimizes strain duringprocessing. Additionally, the burr-free surfaces and scalability of EDM make it a preferred choice in various industries.
In summary, EDM offers a unique approach to machining, relying on electrical discharges to erode materials. It has a diverse range of applications, including small hole drilling, mold and die making, component disintegration, and the production of medical and aerospace components. The advantages of EDM include the ability to machine complex profiles, high accuracy, burr-free surface finish, the capability to cut hard metals, low stress on the workpiece, and highly scalable manufacturing. However, it is important to note the limitations of EDM, such as its applicability only to conductive materials, slower material removal rates, and higher production costs.
Despite its limitations, EDM continues to be a valuable tool in the manufacturing industry, enabling the creation of intricate shapes and achieving high precision. As technology advances, EDM processes may further evolve to overcome current limitations and offer even greater capabilities in the future.
Recommended Reads:
- 5 Key Differences between CNC Routers and CNC Mills
- Understanding CNC Routers: Top Question Asked
- 5 Essential Components of a CNC Lathe
- Differences Between CNC Lathes and CNC Mills
- Discovering CNC Lathes: 10 Fascinating Features to Know
Related Posts
- Applications and Advantages of Bronze CNC Machining
1. Introduction: The Enduring Allure of Bronze in CNC Machining In this opening section, we explore the timeless appeal of bronze as a material for CNC machining. From its rich…
- The Multifaceted Applications of Bead Blasting in CNC Machining
1. Introduction: Unveiling the Versatility of Bead Blasting In this opening section, we introduce the concept of bead blasting in CNC machining and set the stage for an in-depth exploration…
- Precision CNC Machining of Steel: High-Volume Production
Precision CNC Machining and High-Volume Production As an integral part of modern manufacturing processes, Precision Computer Numerical Control (CNC) machining brings about unmatched accuracy and consistency in the production of…