The carbon fiber spoiler stands as a symbol of automotive performance, blending aesthetic appeal with functional excellence. Its sleek, woven surface represents speed, precision, and advanced engineering, but its true significance lies in the intricate manufacturing processes—most notably CNC machining—that transform digital designs into dynamic components. This article explores the technologies defining the quality of carbon fiber spoilers, from the foundational role of CNC machining in mold making to the innovative potential of 3D printing, the precision of lamination techniques, and the automated future of Automated Fiber Placement (AFP). By delving into these processes, we uncover how carbon fiber spoilers achieve their lightweight strength, aerodynamic efficiency, and sustainability, meeting the demands of modern automotive and aerospace industries.
Part I: The Genesis of a Spoiler: The Art and Science of Mold Making
The journey to create a carbon fiber spoiler begins with mold making, the critical first step that determines the part’s shape, surface quality, and dimensional accuracy. A high-quality mold ensures that the carbon fiber spoiler meets stringent performance and aesthetic standards, making the choice of manufacturing technology—such as CNC machining—pivotal.
CNC Machining: Precision at the Core of Mold Making
CNC machining, a subtractive manufacturing process, uses computer-controlled tools to carve molds from solid materials like aluminum, steel, or high-temperature tooling board. For producing molds for carbon fiber spoilers in high-volume production, CNC machining is the gold standard due to its unmatched precision and durability.
- Unrivaled Accuracy: CNC machining achieves tolerances as tight as ±0.025 mm, ensuring that molds produce carbon fiber spoilers with exact aerodynamic profiles and seamless vehicle fitment. This precision is critical for maintaining the spoiler’s performance in high-speed conditions.
- Exceptional Surface Finish: CNC machining creates mirror-smooth mold surfaces, translating to glossy, defect-free carbon fiber spoilers that require minimal post-processing, reducing production time and costs.
- Durability for High-Volume Production: Molds crafted through CNC machining from robust materials withstand the high pressures and temperatures of autoclave curing, enabling consistent production of thousands of carbon fiber spoilers without degradation.
- Repeatability: Once programmed, CNC machining ensures identical molds, guaranteeing uniformity across carbon fiber spoiler production runs, which is essential for manufacturers supplying OEMs or aftermarket clients.
For any manufacturer aiming to produce high-performance carbon fiber spoilers at scale, CNC machining is not just a tool but a necessity, laying the foundation for quality and consistency.
3D Printing: Revolutionizing Prototyping for Carbon Fiber Spoilers
While CNC machining dominates production mold making, 3D printing, or additive manufacturing, has emerged as a game-changer for prototyping carbon fiber spoilers. By building molds layer by layer from digital files, 3D printing enables rapid design validation, allowing engineers to test a carbon fiber spoiler’s fit, form, and aerodynamics before investing in costly CNC machining for production tooling.Key advantages of 3D printing in prototyping include:
- Speed: 3D printing can produce a prototype mold for a carbon fiber spoiler in hours, compared to days or weeks for CNC machining, accelerating the design iteration process.
- Cost-Effectiveness: For low-volume or one-off molds, 3D printing is significantly cheaper than CNC machining, making it ideal for early-stage testing of carbon fiber spoilers.
- Complex Geometries: 3D printing excels at creating intricate mold designs with internal features, which can be challenging for CNC machining due to tool access limitations.
However, 3D-printed molds, typically made from plastics like PLA or resin, lack the durability and precision of CNC machining-produced molds, limiting their use to prototyping rather than series production.Table 1: Comparison of CNC Machining and 3D Printing for Mold Making
Attribute | CNC Machining (Production Molds) | 3D Printing (Prototype Molds) |
Dimensional Accuracy | Very High (±0.025 mm) | Low to Medium (±0.1 to ±0.5 mm) |
Surface Finish | Excellent (Mirror-Smooth) | Fair (Layer Lines Often Visible) |
Mold Durability | Excellent (Metal, Tooling Board) | Poor to Fair (Plastics, Resins) |
Speed (for Prototypes) | Slower (Days to Weeks) | Faster (Hours to Days) |
Cost (for Low Volume) | Higher (Material and Setup Costs) | Lower (Material and Equipment) |
Geometric Complexity | Good, Limited by Tool Access | Excellent, Ideal for Intricate Features |
A Synergistic Approach
CNC machining and 3D printing are complementary in the development of carbon fiber spoilers. 3D printing allows rapid prototyping to refine designs, ensuring the carbon fiber spoiler meets aerodynamic and aesthetic goals. Once validated, CNC machining takes over, producing durable, high-precision molds for scalable production. This synergy reduces development time and costs while ensuring the final carbon fiber spoiler meets industry standards.
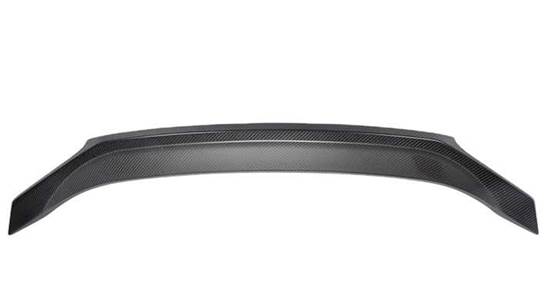
Part II: Lamination Techniques: Crafting the Carbon Fiber Spoiler
With a precision mold crafted by CNC machining, the next phase is forming the carbon fiber spoiler itself. The choice of lamination technique directly impacts the spoiler’s weight, strength, and production efficiency, each method placing unique demands on the mold.
Wet Lay-Up: The Traditional Approach
Wet lay-up is a manual process where dry carbon fiber fabric is placed in a mold, and resin is applied with brushes or rollers. While cost-effective, it has limitations:
- Weight: Excess resin can make carbon fiber spoilers heavier, compromising performance.
- Consistency: Manual application leads to variability, affecting the quality of carbon fiber spoilers.
- Mold Requirements: Wet lay-up molds, often made via CNC machining, need moderate durability, as curing occurs at lower temperatures and pressures.
This method is suitable for low-volume or custom carbon fiber spoilers but is less common in high-performance applications due to its inefficiencies.
Pre-Preg Lamination: The Gold Standard
Pre-impregnated (pre-preg) lamination is the preferred method for high-performance carbon fiber spoilers. Carbon fiber sheets, pre-impregnated with precise amounts of resin, are layered into a CNC machining-produced mold and cured in an autoclave under high heat (up to 180°C) and pressure (up to 6 bar). Benefits include:
- Lightweight Strength: Pre-preg produces “dry carbon” carbon fiber spoilers with optimal fiber-to-resin ratios, minimizing weight while maximizing strength.
- Superior Finish: The process yields glossy, defect-free carbon fiber spoilers with a signature woven aesthetic.
- Mold Durability: Autoclave curing demands CNC machining-crafted molds from materials like aluminum to withstand extreme conditions.
Pre-preg is the choice for premium carbon fiber spoilers used in supercars and motorsports, where performance is paramount.
Resin Transfer Molding (RTM): Balancing Scale and Quality
Resin Transfer Molding (RTM) is an automated process where dry carbon fiber is placed in a two-part mold, and resin is injected under pressure. RTM offers:
- Efficiency: Faster than manual lay-up, making it ideal for mid-to-high-volume carbon fiber spoiler production.
- Consistency: Automated resin injection ensures uniform carbon fiber spoilers.
- Mold Requirements: RTM molds, often produced via CNC machining, must be robust to handle injection pressures but are less demanding than autoclave molds.
RTM is increasingly used for carbon fiber spoilers in performance vehicles, balancing quality and scalability.Table 2: Comparison of Lamination Techniques for Carbon Fiber Spoilers
Technique | Weight | Strength | Production Volume | Mold Durability (CNC Machining) | Cost |
Wet Lay-Up | Heavier | Moderate | Low | Moderate | Low |
Pre-Preg Lamination | Lightest | Highest | Low to Medium | High (Autoclave-Compatible) | High |
Resin Transfer Molding | Moderate | High | Medium to High | High (Injection-Compatible) | Moderate |
Part III: The Automated Future: Precision at Scale with AFP
As demand for carbon fiber spoilers grows in automotive and aerospace applications, automation is transforming production. Automated Fiber Placement (AFP) represents the cutting edge, leveraging CNC machining-like precision in an additive process.
What is Automated Fiber Placement (AFP)?
AFP uses a robotic arm, guided by CNC machining-inspired control systems, to place narrow strips of pre-preg carbon fiber (tows) onto a mold. A compaction roller and heat source fuse the material, building the carbon fiber spoiler layer by layer. This process ensures precision and repeatability, critical for high-performance carbon fiber spoilers.
Advantages of AFP
AFP combines the accuracy of CNC machining with the flexibility of additive manufacturing:
- Precision Fiber Placement: AFP controls fiber orientation to optimize the strength of carbon fiber spoilers, tailoring load-bearing properties to specific aerodynamic requirements.
- Efficiency and Speed: Automated layup is faster than manual methods, reducing labor costs and material waste in carbon fiber spoiler production.
- Complex Geometries: Narrow tows enable intricate carbon fiber spoiler designs, such as curved or variable-thickness profiles, unachievable with traditional methods.
- Scalability: AFP supports high-volume production, making it viable for mainstream automotive carbon fiber spoilers.
AFP in the Automotive Sector
Originally developed for aerospace, AFP is now revolutionizing automotive manufacturing. Companies like Lamborghini and BMW use AFP to produce carbon fiber spoilers, chassis components, and body panels with aerospace-grade quality. For example, AFP enables the creation of carbon fiber spoilers with integrated structural reinforcements, enhancing both performance and safety.
Case Study: AFP in High-Performance Vehicles
In 2023, a leading supercar manufacturer adopted AFP to produce carbon fiber spoilers for its latest hypercar model. By using AFP, the company reduced production time by 30% and material waste by 25% compared to manual pre-preg lamination, while achieving a 10% weight reduction in the carbon fiber spoiler. This case underscores AFP’s potential to transform carbon fiber spoiler manufacturing.
Part IV: Industry Trends Driving Carbon Fiber Spoiler Production
The evolution of carbon fiber spoiler manufacturing is driven by broader industry trends, from performance demands to sustainability imperatives.
Performance and Efficiency Demands
The automotive and aerospace industries are obsessed with weight reduction to improve fuel efficiency, extend electric vehicle range, and enhance performance. Carbon fiber spoilers, with their exceptional strength-to-weight ratio (up to 5 times stronger than steel at one-fifth the weight), are critical to these goals. Technologies like CNC machining and AFP enable manufacturers to produce carbon fiber spoilers that meet stringent performance standards, such as reducing drag by up to 15% in high-speed conditions.
Sustainability in Composite Manufacturing
Sustainability is reshaping the production of carbon fiber spoilers. Key innovations include:
- Bio-based Precursors: Research into lignin-based carbon fiber, derived from wood, aims to replace petroleum-based precursors, reducing the carbon footprint of carbon fiber spoilers by up to 20%.
- Energy-Efficient Curing: Low-energy curing methods, such as microwave or UV curing, are being developed to reduce the energy consumption of autoclave processes by up to 30%.
- Recyclable Materials: Thermoplastic resins, unlike traditional thermosets, can be melted and reused, enabling a circular economy for carbon fiber spoilers. For example, recycled thermoplastic carbon fiber spoilers retain 90% of their original strength.
Table 3: Sustainability Innovations in Carbon Fiber Spoiler Production
Innovation | Benefit | Impact on Carbon Fiber Spoilers | Adoption Stage |
Bio-based Precursors | Reduces reliance on petroleum | Lower carbon footprint for carbon fiber spoilers | Research/Prototype |
Energy-Efficient Curing | Decreases energy consumption | Cost-effective production of carbon fiber spoilers | Early Adoption |
Thermoplastic Resins | Enables recycling and reuse | Sustainable lifecycle for carbon fiber spoilers | Growing Adoption |
Market Dynamics and Consumer Trends
The global market for carbon fiber spoilers is expanding, driven by demand for performance vehicles and electric cars. According to industry reports, the automotive carbon fiber market is projected to grow at a CAGR of 7.5% from 2023 to 2030, with carbon fiber spoilers playing a significant role in aftermarket and OEM applications. Technologies like CNC machining and AFP are enabling manufacturers to meet this demand with high-quality, cost-competitive carbon fiber spoilers.
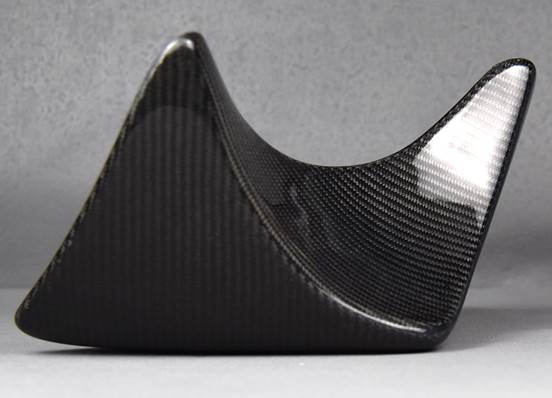
Part V: Challenges and Future Directions
While CNC machining, 3D printing, and AFP have transformed carbon fiber spoiler production, challenges remain:
- Cost: CNC machining and AFP require significant upfront investment in equipment and expertise, limiting adoption by smaller manufacturers.
- Scalability: While AFP enhances scalability, its high initial costs make it more suited to large-scale OEMs than niche producers of carbon fiber spoilers.
- Sustainability Barriers: Recycling carbon fiber remains complex, with only 1% of global carbon fiber waste currently recycled due to technical and economic hurdles.
Future advancements may address these challenges:
- Hybrid Manufacturing: Combining CNC machining with additive techniques like AFP could reduce costs while maintaining precision for carbon fiber spoiler production.
- AI-Driven Design: Artificial intelligence is being integrated with CNC machining and AFP to optimize carbon fiber spoiler designs, predicting aerodynamic performance and reducing material use.
- Recycling Innovations: Advances in chemical recycling could increase the recyclability of carbon fiber spoilers to 50% by 2035, supporting a circular economy.
Conclusion
The carbon fiber spoiler is more than a performance accessory; it is the culmination of a sophisticated manufacturing journey. CNC machining lays the foundation with precision molds, enabling high-quality lamination techniques like pre-preg and RTM. Meanwhile, 3D printing accelerates prototyping, and AFP represents the future of automated, scalable production. As the automotive and aerospace industries demand lighter, stronger, and more sustainable components, technologies like CNC machining and AFP will continue to evolve, ensuring that carbon fiber spoilers remain at the forefront of performance and innovation. By integrating digital design, precision manufacturing, and sustainable practices, the production of carbon fiber spoilers is redefining what’s possible in high-performance engineering.
FAQ:
1. What is a carbon fiber spoiler, and why is it used in high-performance vehicles?
A carbon fiber spoiler is an aerodynamic component made from carbon fiber composites, designed to enhance vehicle stability and reduce drag at high speeds. Used in supercars, motorsports, and premium vehicles, carbon fiber spoilers leverage the material’s lightweight strength (up to 5 times stronger than steel at one-fifth the weight) to improve performance, fuel efficiency, and aesthetics. Their production often relies on CNC machining for precise molds to ensure optimal fit and finish.
2. How does CNC machining contribute to carbon fiber spoiler production?
CNC machining is critical for creating high-precision molds used in carbon fiber spoiler manufacturing. It achieves tolerances as tight as ±0.025 mm, ensuring molds produce carbon fiber spoilers with flawless aerodynamic surfaces and vehicle fitment. CNC machining also delivers durable molds from materials like aluminum, capable of withstanding autoclave curing for high-quality carbon fiber spoilers.
3. What role does 3D printing play in making carbon fiber spoilers?
3D printing is used for rapid prototyping of carbon fiber spoilers, allowing engineers to test designs quickly and cost-effectively before committing to CNC machining for production molds. While 3D-printed molds lack the durability for high-volume production, they excel in creating complex geometries for prototype carbon fiber spoilers, speeding up the design iteration process.
4. What are the main lamination techniques for carbon fiber spoilers?
The three primary lamination methods for carbon fiber spoilers are:
- Wet Lay-Up: A manual, cost-effective process producing heavier carbon fiber spoilers with less consistency.
- Pre-Preg Lamination: The gold standard, using autoclave-cured pre-impregnated sheets for lightweight, high-strength carbon fiber spoilers.
- Resin Transfer Molding (RTM): An automated method for mid-to-high-volume carbon fiber spoiler production, balancing quality and efficiency.
Each method relies on CNC machining-crafted molds for precision.
5. What is Automated Fiber Placement (AFP), and how does it benefit carbon fiber spoiler manufacturing?
AFP is an advanced automation technology using CNC machining-guided robotic arms to place pre-preg carbon fiber tows onto molds, building carbon fiber spoilers with precision. AFP enhances carbon fiber spoiler production by optimizing fiber orientation for strength, reducing material waste, and enabling complex geometries, making it ideal for high-volume, high-performance applications.
6. Why are CNC-machined molds essential for high-performance carbon fiber spoilers?
CNC machining produces molds with exceptional accuracy (±0.025 mm) and smooth finishes, critical for creating carbon fiber spoilers with aerodynamic precision and glossy aesthetics. These molds, made from durable materials like aluminum, withstand the high pressures and temperatures of autoclave curing, ensuring consistent, high-quality carbon fiber spoiler production for supercars and motorsports.
Reference:
https://zh.wikipedia.org/wiki/%E6%93%BE%E6%B5%81%E6%9D%BF
https://patents.google.com/patent/CN219406664U/zh
Other Articles You Might Enjoy
- Carbon Fiber 3D Printer: The Ultimate Guide to High-Strength, Lightweight Printing
Introduction: What Is Carbon Fiber 3D Printing? Hello there, and welcome to my ultimate guide on carbon fiber 3D printer technology. I’ve spent a good chunk of my career around…
- Carbon Fiber vs. Fiberglass: Strength, Cost, and Application Showdown
Introduction of Carbon Fiber and Fiberglass In the world of composites, Carbon Fiber and Fiberglass hold significant places due to their unique characteristics. Originally discovered in 1860, carbon fiber is…
- Carbon Fiber vs. Fiberglass: Strength, Cost, and Application Showdown
Introduction to Carbon Fiber and Fiberglass In the world of synthetic materials, carbon fiber and fiberglass are two distinct but essential elements which have become indispensable across various industries. Carbon…
- CNC Machining of Composite Materials: Carbon Fiber vs. Kevlar
CNC Machining and Composite Materials: Carbon Fiber and Kevlar Computer Numerical Control (CNC) machining is a highly precise and automated process employed in manufacturing industries to create intricate parts and…
- What Is White Carbon Fiber? Applications and CNC Processing Explained
Introduction White carbon fiber is a fascinating material that combines the strength and lightweight properties of traditional black carbon fiber with a striking aesthetic appeal. Unlike the typical black or gray…
- From Raw Material to Finished Part: A Comprehensive Guide to Technical Selection for Carbon Fiber CNC Machining
The journey from raw material to a high-performance carbon fiber reinforced polymer (CFRP) component is intricate, requiring engineers, designers, and manufacturers to carefully select among various types of carbon fiber…