The journey from raw material to a high-performance carbon fiber reinforced polymer (CFRP) component is intricate, requiring engineers, designers, and manufacturers to carefully select among various types of carbon fiber and develop precise CNC machining strategies. The types of carbon fiber chosen—defined by precursor material, elastic modulus, weave pattern, and tow size—profoundly influence mechanical properties, machinability, cost, and final part quality. This comprehensive guide explores these classifications in depth, detailing their impact on CNC machining processes and providing actionable insights for optimizing high-value applications. By understanding the interplay between material selection and CNC machining, professionals can achieve superior performance, precision, and efficiency.
1. Precursor Materials: The Foundation of Carbon Fiber Types
The performance of types of carbon fiber begins with the precursor material, which shapes the fiber’s microstructure and suitability for CNC machining. Two primary precursors dominate the industry: polyacrylonitrile (PAN) and pitch, each imparting unique properties to types of carbon fiber.
1.1 Polyacrylonitrile (PAN)-based Carbon Fiber
PAN-based types of carbon fiber account for over 90% of global production, valued for their exceptional tensile strength (typically 3.5–7 GPa) and versatility. These types of carbon fiber are ideal for applications requiring high strength-to-weight ratios, such as:
- Aerospace components: Fuselage panels, wing structures, and landing gear.
- Automotive parts: Racing chassis, suspension components, and body panels.
- Sporting goods: Bicycle frames, tennis rackets, and golf club shafts.
The molecular structure of PAN-based types of carbon fiber results from controlled carbonization, yielding a balance of strength and flexibility suitable for diverse CNC machining processes.
1.2 Pitch-based Carbon Fiber
Pitch-based types of carbon fiber are distinguished by their ultra-high elastic modulus (up to 900 GPa) and superior thermal conductivity (up to 1000 W/m·K). These properties make them indispensable for applications demanding extreme stiffness and thermal management, including:
- Satellite components: Antenna reflectors and structural supports.
- High-performance braking systems: Brake discs for Formula 1 cars and aircraft.
- Thermal management systems: Heat sinks in aerospace electronics.
The graphitic microstructure of pitch-based types of carbon fiber enhances stiffness but increases brittleness, posing unique challenges in CNC machining.
1.3 CNC Machining Impacts of Precursor-Based Carbon Fiber Types
The choice of precursor significantly affects CNC machining outcomes due to differences in microstructure:
- Tool Wear: Pitch-based types of carbon fiber are more abrasive due to their graphite-like structure, accelerating wear on standard carbide tools. Diamond-coated or polycrystalline diamond (PCD) tools are recommended for CNC machining these materials to extend tool life and maintain precision.
- Edge Chipping: The brittleness of pitch-based types of carbon fiber increases the risk of micro-chipping or fracturing during CNC machining. Lower feed rates (e.g., 0.05–0.1 mm/rev) and sharp tool geometries (e.g., rake angles of 10–15°) ensure clean shearing cuts.
- Dust Management: Both types of carbon fiber generate fine, abrasive dust during CNC machining, necessitating robust dust extraction systems to protect equipment and operator health.
Table 1: Comparison of PAN and Pitch-based Carbon Fiber Types
Property | PAN-based Carbon Fiber | Pitch-based Carbon Fiber |
Tensile Strength (GPa) | 3.5–7.0 | 1.5–3.5 |
Elastic Modulus (GPa) | 230–500 | 350–900 |
Thermal Conductivity (W/m·K) | 10–100 | 500–1000 |
CNC Machining Challenges | Moderate tool wear, flexible | High tool wear, brittle |
Typical Applications | Aerospace, automotive | Satellites, braking systems |
2. Elastic Modulus: Defining Stiffness in Carbon Fiber Types
Elastic modulus, a measure of stiffness, is a critical parameter for classifying types of carbon fiber in CNC machining. It determines how much a material deforms under stress, directly influencing part performance and machining strategies. Types of carbon fiber are categorized into four modulus grades, each suited to specific applications and CNC machining requirements.
2.1 Modulus Grades Overview
- Standard Modulus (SM, ~230–240 GPa): These types of carbon fiber offer a cost-effective balance of strength and stiffness, widely used in general CNC machining for automotive and consumer goods.
- Intermediate Modulus (IM, ~290–350 GPa): With higher tensile strength, IM types of carbon fiber are the go-to choice for primary aerospace structures, requiring precise CNC machining for complex geometries.
- High Modulus (HM, ~350–600 GPa): HM types of carbon fiber prioritize stiffness over strength, ideal for applications like satellite frames but challenging in CNC machining due to brittleness.
- Ultra-High Modulus (UHM, >600 GPa): Offering ultimate stiffness, UHM types of carbon fiber are used in cutting-edge aerospace applications, demanding specialized CNC machining techniques.
Table 2: Elastic Modulus Grades of Carbon Fiber Types
Grade | Elastic Modulus (GPa) | Tensile Strength (GPa) | CNC Machining Applications |
Standard Modulus (SM) | 230–240 | 3.5–5.0 | Automotive, consumer goods |
Intermediate Modulus (IM) | 290–350 | 4.0–6.0 | Aerospace structures |
High Modulus (HM) | 350–600 | 2.5–4.0 | Satellite frames, stiff parts |
Ultra-High Modulus (UHM) | >600 | 1.5–3.0 | Advanced aerospace, optics |
2.2 CNC Machining Challenges for Modulus-Based Carbon Fiber Types
As modulus increases, types of carbon fiber become harder and more brittle, complicating CNC machining:
- Delamination Risk: HM and UHM types of carbon fiber are prone to interlayer separation during CNC machining. Compression or down-cut spiral tools apply perpendicular pressure to minimize delamination, ensuring clean cuts.
- Thermal Sensitivity: While types of carbon fiber are heat-resistant, their epoxy resin matrix is not. High-modulus fibers generate more heat during CNC machining, risking resin softening or burning. Cooling methods like cold air or Minimum Quantity Lubrication (MQL) are critical to maintain dimensional accuracy.
- Tool Selection: Machining high-modulus types of carbon fiber accelerates tool wear, reducing lifespan by up to 50% compared to SM fibers. PCD tools, though costly, offer longer life and consistent CNC machining quality.
- Parameter Optimization: Lower cutting speeds (e.g., 50–100 m/min) and feed rates (e.g., 0.02–0.08 mm/rev) are essential for HM and UHM types of carbon fiber to prevent defects in CNC machining.
2.3 Practical Considerations
When selecting modulus-based types of carbon fiber, engineers must balance performance with CNC machining costs. For example, SM fibers are economical for high-volume production, while UHM fibers, though expensive, are justified for niche applications requiring extreme stiffness. CNC machining strategies must be tailored to each modulus grade to optimize yield and quality.
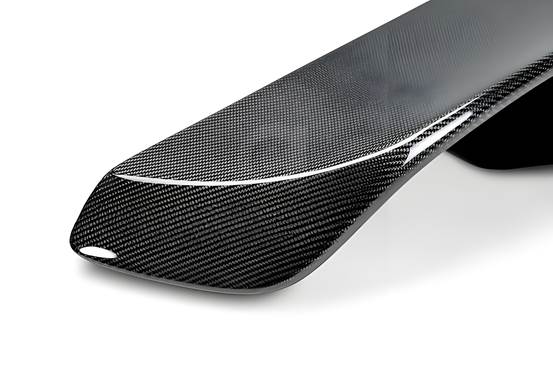
3. Weave Patterns: Structural Design of Carbon Fiber Types
The weave pattern of types of carbon fiber determines not only aesthetics but also mechanical properties and CNC machining performance. The three primary weave patterns—plain, twill, and satin—offer distinct advantages and challenges.
3.1 Types of Weave Patterns
Plain Weave: A “one over, one under” crisscross pattern creates a stable, checkerboard-like structure. Plain weave types of carbon fiber are ideal for flat surfaces but have higher fiber crimp, reducing ultimate strength in CNC machining applications.
Twill Weave: A “two over, two under” or “four over, four under” pattern produces a diagonal appearance. Twill types of carbon fiber offer higher strength and pliability, making them suitable for complex molds in CNC machining.
Satin Weave: With minimal interlacing (e.g., “four over, one under”), satin types of carbon fiber provide a smooth surface and high strength but are less stable, increasing CNC machining challenges.
3.2 CNC Machining Impacts of Weave-Based Carbon Fiber Types
Weave patterns directly affect CNC machining outcomes:
- Edge Burrs and Fiber Pull-out: Satin weave types of carbon fiber are prone to fiber pull-out during CNC machining, leading to burrs and surface defects. Down-cut or compression tools press fibers into the matrix for cleaner cuts.
- Surface Consistency: Plain weave types of carbon fiber distribute cutting forces evenly, resulting in smoother finishes in CNC machining. Twill and satin weaves, with longer fiber floats, require precise tool paths to avoid uneven surfaces.
- Tool Path Optimization: For satin and twill types of carbon fiber, CNC machining strategies should incorporate multi-pass cutting to reduce burring and ensure high-quality edges.
3.3 Aesthetic and Functional Trade-offs
While twill and satin types of carbon fiber are favored for their aesthetic appeal in visible components (e.g., automotive interiors), plain weave types of carbon fiber are preferred for structural parts where CNC machining precision and stability are paramount. Selecting the right weave involves balancing form and function.
4. Tow Size: Dimensional Choices in Carbon Fiber Types
Tow size, indicated by the “K” value (e.g., 3K = 3,000 filaments), defines the thickness of types of carbon fiber and influences CNC machining dynamics. Tow size affects both material buildup and machining behavior.
4.1 Small Tow (1K, 3K)
Small-tow types of carbon fiber are finer and more pliable, ideal for:
- Lightweight parts: Drone frames, medical devices.
- Complex geometries: Intricate molds and aerodynamic components.
- Aesthetic applications: Consumer electronics and luxury goods.
These types of carbon fiber allow precise resin saturation, enhancing CNC machining accuracy for detailed parts.
4.2 Large Tow (12K, 24K+)
Large-tow types of carbon fiber enable rapid material buildup, reducing costs in:
- Industrial applications: Wind turbine blades, structural beams.
- Heavy-duty components: Marine hulls, infrastructure supports.
However, their thickness poses CNC machining challenges due to increased fiber bundle size.
4.3 CNC Machining Impacts of Tow-Based Carbon Fiber Types
Tow size affects CNC machining performance:
- Fiber Pull-out: Large-tow types of carbon fiber (e.g., 12K) risk fiber pull-out if tools are not sharp, leading to surface defects. High-rigidity tools and lower feed rates (e.g., 0.03–0.07 mm/rev) ensure clean cuts.
- Cutting Force Fluctuations: Thicker tows cause cyclic force variations during CNC machining, inducing micro-vibrations that affect accuracy. Rigid machine setups and vibration-damping fixtures are essential.
- Surface Quality: Small-tow types of carbon fiber produce smoother surfaces in CNC machining due to finer fiber bundles, while large-tow fibers require additional finishing steps.
Table 3: Tow Size Characteristics and CNC Machining Impacts
Tow Size | Filaments | Advantages | CNC Machining Challenges |
Small (1K, 3K) | 1,000–3,000 | Pliable, high detail, aesthetic appeal | Higher cost, slower buildup |
Large (12K, 24K+) | ≥12,000 | Cost-effective, rapid buildup | Fiber pull-out, force fluctuations |
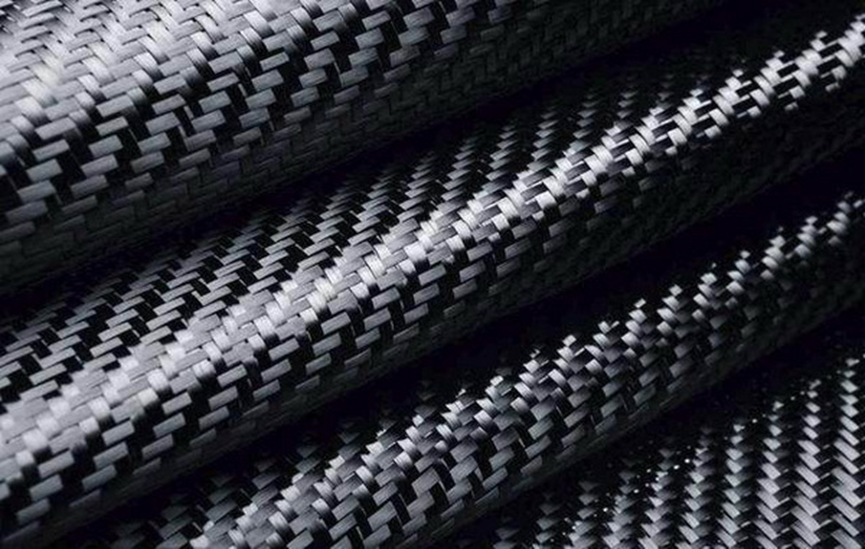
5. Holistic Approach to Carbon Fiber CNC Machining
The success of CNC machining types of carbon fiber lies in a systematic approach that integrates material selection with machining strategy. Key considerations include:
- Material-Machine Synergy: Match types of carbon fiber to CNC machining capabilities. For example, pitch-based or high-modulus fibers require advanced tools and cooling systems.
- Tool Selection: Invest in PCD or diamond-coated tools for abrasive types of carbon fiber to reduce wear and improve CNC machining efficiency.
- Parameter Optimization: Adjust cutting speeds, feed rates, and tool paths based on the specific types of carbon fiber to minimize defects like delamination and burrs.
- Quality Control: Implement real-time monitoring during CNC machining to detect issues like thermal damage or fiber pull-out early.
5.1 Practical Strategies for Engineers
To optimize CNC machining of types of carbon fiber, engineers should:
- Conduct Material Testing: Evaluate the mechanical properties of types of carbon fiber before machining to select appropriate tools and parameters.
- Simulate Machining Processes: Use CAD/CAM software to model CNC machining outcomes for different types of carbon fiber, reducing trial-and-error costs.
- Invest in Training: Ensure operators are skilled in handling the unique challenges of CNC machining various types of carbon fiber, particularly high-modulus or large-tow materials.
- Leverage Advanced Cooling: Implement MQL or cryogenic cooling to manage heat in CNC machining high-modulus types of carbon fiber.
5.2 Case Studies
Aerospace Application: A manufacturer machining IM types of carbon fiber for an aircraft wing used PCD tools and MQL cooling, reducing delamination by 40% and improving surface finish.
Automotive Application: A racing team machining 3K twill types of carbon fiber for a chassis employed down-cut tools, achieving a 30% reduction in edge burrs during CNC machining.
Conclusion: Mastering Carbon Fiber Types for CNC Machining Excellence
Selecting and machining types of carbon fiber is a complex but rewarding process. By understanding the interplay of precursor materials, elastic modulus, weave patterns, and tow sizes, engineers can tailor CNC machining strategies to maximize performance and quality. Key takeaways include:
- Use PCD tools for pitch-based and high-modulus types of carbon fiber to enhance CNC machining durability.
- Employ compression tools for satin or twill types of carbon fiber to minimize burrs in CNC machining.
- Optimize feed rates and cooling for large-tow types of carbon fiber to ensure defect-free CNC machining.
FAQ:
- What are the main types of carbon fiber used in CNC machining?
The primary types of carbon fiber used in CNC machining are classified by precursor material, elastic modulus, weave pattern, and tow size:
- Precursor Materials: Polyacrylonitrile (PAN)-based types of carbon fiber offer high tensile strength, while pitch-based types of carbon fiber provide superior stiffness and thermal conductivity.
- Elastic Modulus: Standard (SM), Intermediate (IM), High (HM), and Ultra-High Modulus (UHM) types of carbon fiber vary in stiffness, impacting CNC machining strategies.
- Weave Patterns: Plain, twill, and satin weaves influence aesthetics and machinability in CNC machining.
- Tow Size: Small (1K, 3K) and large (12K, 24K+) tow types of carbon fiber affect material buildup and CNC machining precision.
Each of these types of carbon fiber requires tailored CNC machining approaches to optimize performance and quality.
- How does the precursor material affect CNC machining of carbon fiber?
The precursor material—PAN or pitch—defines the microstructure of types of carbon fiber, directly impacting CNC machining:
- PAN-based Carbon Fiber: These types of carbon fiber are less abrasive, causing moderate tool wear during CNC machining. They are easier to machine but require sharp tools to avoid fiber pull-out.
- Pitch-based Carbon Fiber: More abrasive due to their graphite-like structure, these types of carbon fiber accelerate tool wear in CNC machining, necessitating diamond-coated or PCD tools. Their brittleness also increases the risk of edge chipping, requiring lower feed rates (e.g., 0.05–0.1 mm/rev).
Selecting the right tools and parameters is critical for effective CNC machining of these types of carbon fiber.
- Why is elastic modulus important when selecting types of carbon fiber for CNC machining?
Elastic modulus measures the stiffness of types of carbon fiber, influencing both part performance and CNC machining challenges:
- Standard Modulus (SM, 230–240 GPa): Cost-effective and versatile, these types of carbon fiber are easier to machine, suitable for general CNC machining applications like automotive parts.
- Intermediate Modulus (IM, 290–350 GPa): Ideal for aerospace, IM types of carbon fiber require precise CNC machining to handle higher strength.
- High/Ultra-High Modulus (HM/UHM, 350–900+ GPa): These brittle types of carbon fiber are prone to delamination and thermal damage in CNC machining, requiring specialized tools and cooling methods like MQL.
Matching modulus to application ensures optimal CNC machining outcomes.4. How do weave patterns impact the CNC machining process for carbon fiber?Weave patterns—plain, twill, and satin—affect the mechanical properties and CNC machining performance of types of carbon fiber:
- Plain Weave: Stable and uniform, these types of carbon fiber produce smooth surfaces in CNC machining but have lower strength due to fiber crimp.
- Twill Weave: Offering a balance of strength and pliability, twill types of carbon fiber are versatile but require careful tool selection to avoid uneven cuts in CNC machining.
- Satin Weave: With high strength and smooth surfaces, satin types of carbon fiber are prone to fiber pull-out, necessitating down-cut tools for clean CNC machining.
Choosing the right weave pattern optimizes both aesthetics and CNC machining efficiency.
5. What role does tow size play in CNC machining carbon fiber?
Tow size, indicated by the “K” value (e.g., 3K, 12K), determines the thickness of types of carbon fiber and influences CNC machining:
- Small Tow (1K, 3K): These types of carbon fiber are pliable and ideal for detailed, lightweight parts, producing smoother surfaces in CNC machining.
- Large Tow (12K, 24K+): Cost-effective for industrial applications, large-tow types of carbon fiber risk fiber pull-out and force fluctuations during CNC machining, requiring rigid setups and sharp tools.
Adjusting feed rates and tool paths is essential for machining these types of carbon fiber effectively.
6. What tools are best for CNC machining different types of carbon fiber?
Tool selection for CNC machining types of carbon fiber depends on material properties:
- PAN-based and SM/IM Fibers: Carbide tools suffice for less abrasive types of carbon fiber, but diamond-coated tools improve longevity in CNC machining.
- Pitch-based and HM/UHM Fibers: PCD or diamond-coated tools are essential for abrasive types of carbon fiber to reduce wear and maintain precision in CNC machining.
- Satin/Twill Weaves: Compression or down-cut spiral tools minimize burrs and pull-out during CNC machining of these types of carbon fiber.
Investing in high-quality tools enhances CNC machining efficiency and part quality.
Reference:
https://www.scribd.com/presentation/356266276/Carbon-Fiber
https://www.sciencedirect.com/science/article/pii/S2666548425000289
Other Articles You Might Enjoy
- CNC Machining of Composite Materials: Carbon Fiber vs. Kevlar
CNC Machining and Composite Materials: Carbon Fiber and Kevlar Computer Numerical Control (CNC) machining is a highly precise and automated process employed in manufacturing industries to create intricate parts and…
- Carbon Fiber Sheets in CNC Machining: Applications, Techniques, and Cost Insights
Introduction When it comes to lightweight and high-strength materials, carbon fiber sheets are among the top choices for industries like aerospace, automotive, and electronics. Their unique properties, such as rigidity,…
- Carbon Fiber 3D Printer: The Ultimate Guide to High-Strength, Lightweight Printing
Introduction: What Is Carbon Fiber 3D Printing? Hello there, and welcome to my ultimate guide on carbon fiber 3D printer technology. I’ve spent a good chunk of my career around…
- The Ultimate Carbon Fiber Case CNC Machining Manual for Custom Enclosures
Chapter 1: Introduction If you’ve ever held a carbon fiber case, you probably noticed how ridiculously light it feels—yet somehow, it feels tougher than metal. That’s not just a gimmick. Carbon…
- Carbon Fiber Sheets in CNC Machining: Applications, Techniques, and Cost Insights
Introduction When it comes to lightweight and high-strength materials, carbon fiber sheets are among the top choices for industries like aerospace, automotive, and electronics. Their unique properties, such as rigidity,…