The report highlights that China is anticipated to be the most significant contributor to the plasma-cutting machine market, with a projected CAGR of 6.4% from 2021 to 2028. The United States and Europe are also expected to see continued growth, driven by strong demand in the automotive and aerospace sectors.
China Online CNC Machining Service
Once you’ve tried a plasma cutter, you’ll never require oxy-fuel cutting or grinding discs again. Plasma cutters are an extremely useful tool to have in custom sheet metal fabrication areas since they are simple to use and less expensive to operate than oxy-fuel cutters.
What Is a Plasma Cutter?
A plasma cutter passes through a narrow hole while releasing an electric arc through a gas. Plasma cutters increase the temperature of the gas and transform it into plasma, the fourth state of matter.
This tool can pass through metals including steel, aluminum, brass, and copper with little to no resistance when used in conjunction with a suitable plasma torch. This precise welding technique enables smoother, more cut lines and stronger constructions.
Where Does Plasma Cutter Use?
Plasma cutters are necessary for the manufacturing business, from the construction industry to auto shops to locksmiths. The abilities and design of this tool have developed along with technology. Generally, there are two types of plasma cutters: machine plasma cutters and handheld plasma cutters.
Handheld cutters are multifunctional. They are typically portable, making welding tasks simpler and easier. They provide powerful cutting amperage but are usually used to remove extra material in light-metal applications.
Mechanized plasma cutters are used for large-scale projects. They have many features and are utilized in the combination with cutting tables. Since these systems require a larger power source to function, moving them is challenging. Whether to use a machine or a handheld cutter depends on the dimensions, shape, and thickness of the material that needs to be cut.
Moreover, CNC cutting tables come with software that may be programmed to execute intricate designs.
What Is Plasma Cutting?
Plasma cutting is a thermal cutting technology that uses ionized gas to cut sheet metals. This comprises thick or thin metals including copper, titanium, brass, steel, and aluminum. It is one of the most used methods for cutting heavy plasma cut sheet metal.
Hand plasma cutting is possible with a hand-held plasma torch. They are also referred to as plasma cutters, plasma cannons, and plasma arcs. There are various types of plasma torches available based on the thickness of the metal to be cut.
Moreover, plasma cutting has more industrial uses. For example, CNC plasma cutting uses larger metal sheets to cut profiles from digital files. Plasma cutting is extremely precise when cutting surfaces because of these kinds of procedures.
What are the Types of Plasma Cutting?
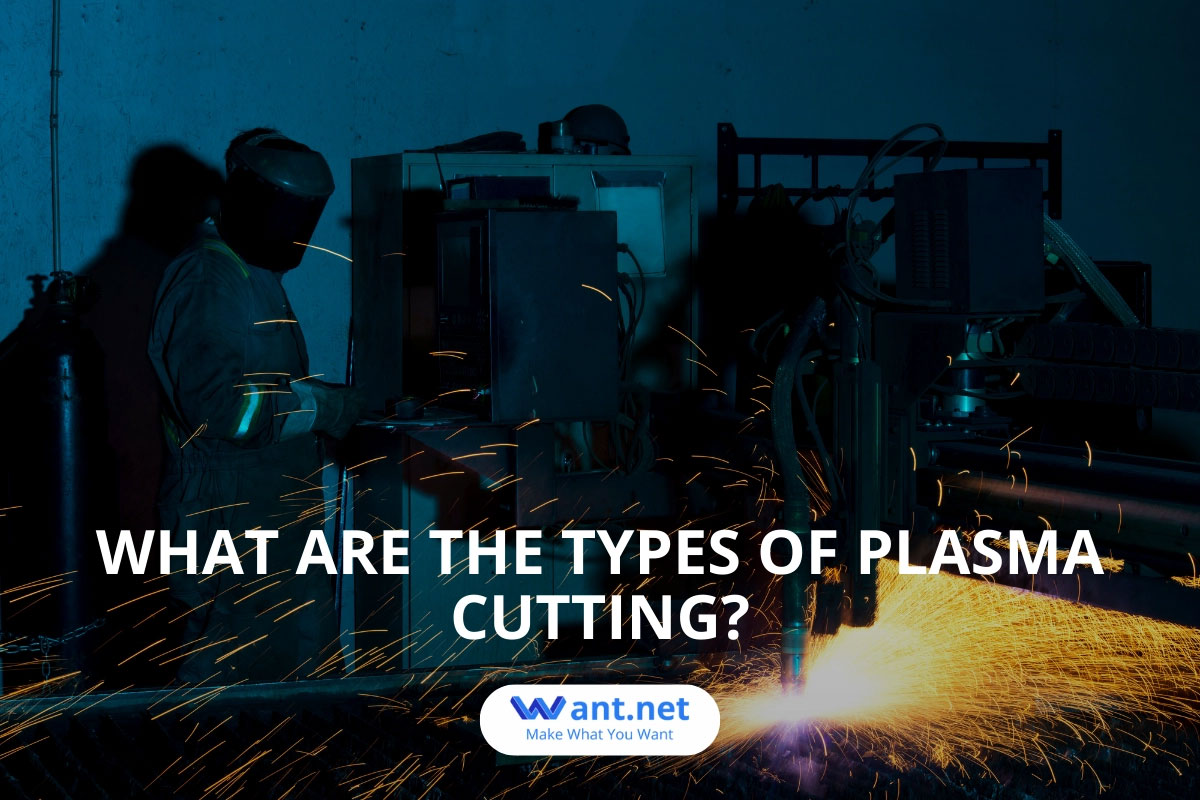
Plasma cutting systems can be broadly divided into two categories: conventional plasma systems and precision plasma systems.
Custom plasma cutting
Normally, shop air is used as the plasma gas, and the torch’s nozzle determines the shape of the arc. Custom plasma cutting falls under the category of standard plasma systems, as do uses where the tolerance of the materials being cut is lower.
Although these kinds are popular, they are less accurate than the other type of plasma cutting.
Systems for precision plasma
Use a range of gases, including oxygen, nitrogen, or a mixture of hydrogen, argon, and nitrogen, to create the best cuts on a variety of conductive materials. These CNC-controlled tools are designed to generate the most accurate cuts possible with plasma.
The torches and the patterns they carve are more intricate, and the arc’s shape is constricted to increase precision.
How Plasma Cutter Work?
Plasma cutting functions by passing a super-fast flow of warm plasma through conductive metals to cut through them.
An electric arc is sent through a gas, like nitrogen or oxygen, to create the plasma. As a result, plasma, the fourth state of matter, is produced. The nozzle-like, tiny opening through which the plasma is pushed can then be used to cut through conductive metal.
Plasma-cutting sheet metal professionals prefer the plasma technique because it is safer than using a saw to cut metals.
Several plasma-cutting systems function in various ways. There are three different kinds of cutting operations.
What are the Three Types of Plasma Cutting Processes?
High-Frequency Contact: It is a low-cost type. This procedure is also not suitable for CNC plasma cutters due to the potential of interfering with current equipment due to its high frequency. High voltage and high-frequency sparks are used in high-frequency contact cutting.
The plasma torch makes contact with the metal being cut, which causes a spark to form. The contact completes the circuit, starts the spark, and produces the cutting plasma.
Pilot Arc: In this cutting process, a combination of a low-current circuit and a high-voltage source creates the spark within the torch. This spark helps produce a tiny amount of plasma called a “pilot arc.” The plasma cutter creates a cutting arc when it comes into contact with the workpiece, allowing the machinist or operator to start the cutting process.
Spring Loaded Plasma Torch Head: Workers press the torch against the workpiece to make a short circuit. The current starts to flow once a short circuit has been created. Engineers release the pressure to create the pilot arc.
What Is Plasma Cutting Used For?
Plasma cutting is widely applied in on-site construction sites or salvage yards for all kinds of metal production projects. The most typical applications for designers and artists are in sculpture and signs, as well as in decorative panels for interior construction.
Advantages of Plasma Cutting
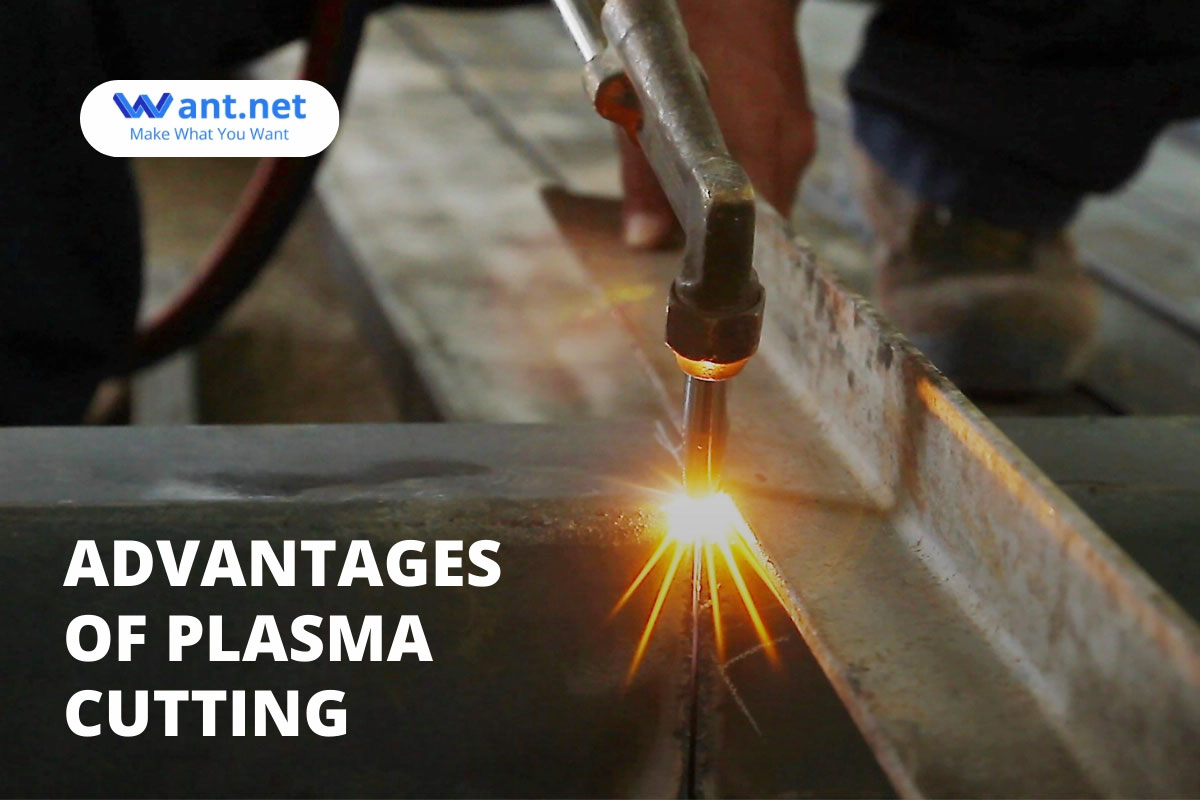
Plasma cutting has various advantages over conventional metal fabrication technologies, ranging from cost effectiveness to improved productivity and better cut quality. Here are a few other benefits.
High Cutting Quality
Plasma cutting offers metals a greater cutting quality when compared to other metal fabrication procedures like flame cutting or waterjet cutting. This is because the heat-affected zone is smaller and there is no residual scum on the metal cut edge.
Versatility and Flexibility
This method is incredibly adaptable and can cut any metal that uses electricity. Metals like aluminum and high-alloy steel with high thicknesses can be cut with ease. It is excellent for marking, planning, and cutting grooves in metals. The method can also cut metals in the water while producing less noise.
High Speed
Plasma cutting is around ten times faster than oxy-fuel cutting and one hundred times faster than laser cutting. In comparison to other methods, it increases productivity and cuts down on the amount of time needed for metal manufacture.
Higher Precision and Repeatability
The use of heat throughout the cutting process results in parts with greater precision and surface quality. Furthermore, the speed of fabrication enhances repeatability while decreasing the time required for plasma-cutting steel.
Disadvantages of Plasma Cutting
Although using plasma cutting to fabricate metals has many advantages, there are drawbacks as well.
- It only cuts conductive materials.
- It is not recommended for thicknesses over 150mm.
- The process may produce bright flashes that are harmful to human eyes.
- It sometimes creates noise during operation.
- Fumes are produced when cutting in the air.
- It could be expensive due to low-life consumables such as nozzles and electrodes.
Conclusion
Although plasma cutting is a very complex operation, there is a large and highly competitive market for plasma cutter services.
Today, plasma cutting (along with other types of metal cutting) is frequently used to make a variety of components and appliances for our daily lives as well as for large projects like buildings, infrastructure, and other structures.
Other Articles You Might Enjoy
- What is a CNC Plasma Cutter?
In the fast-paced world of CNC machining, where precision and efficiency reign supreme, the CNC Plasma Cutter emerges as a groundbreaking tool. If you're new to the realm of CNC…
- Beyond Cutting: Exploring the Multifaceted CNC Machining Process
1. Introduction: Unveiling the Layers of CNC Machining In this introductory section, we peel back the layers of the CNC machining process, going beyond the traditional understanding of cutting. It…
- Transforming the Marine Industry with Precision CNC Machined Parts
Introduction to CNC Machining and its Application in the Marine Industry CNC machining, which stands for Computer Numerical Control machining, is a manufacturing process where pre-programmed computer software dictates the…