In the fast-paced world of CNC machining, where precision and efficiency reign supreme, the CNC Plasma Cutter emerges as a groundbreaking tool. If you’re new to the realm of CNC machining and eager to explore the potential of this technology in ordering machined parts, you’re in for a treat.
CNC Plasma Cutters have revolutionized the manufacturing industry by offering exceptional precision and speed when it comes to cutting various materials. Whether you require precise cuts in metal, wood, or even stone, these automated cutting systems have become the go-to choice across industries, enabling the efficient production of custom machined parts.
How CNC Plasma Cutters Work
Plasma cutting involves the use of an ionized gas, known as plasma, to cut through conductive materials. The plasma is created by passing an electric current through a gas such as nitrogen, oxygen, or compressed air. This process results in the formation of a high-temperature plasma arc that reaches temperatures of up to 30,000 degrees Fahrenheit.
Below are the typical process of CNC plasma cutting:
- Material Preparation: The material is secured on the CNC Plasma Cutter table using clamps or magnets for stability during cutting.
- Design Input and Programming: The desired design is input into the CNC software, which generates the necessary toolpaths and instructions.
- Machine Setup: The CNC operator installs the cutting nozzle, adjusts gas pressure, and sets cutting parameters for the Plasma Cutter.
- Torch Height Control: CNC Plasma Cutters have height control systems that ensure a consistent cutting distance, compensating for material variations.
- Cutting Process: The CNC Plasma Cutter follows programmed toolpaths, controlling the plasma torch’s movement. The intense heat melts the material, while gas blows away molten metal to create the desired cut.
- Cooling and Finishing: After cutting, the material cools and solidifies, ready for safe handling. Additional processes like grinding or deburring may be performed for the desired final result.
Benefits & Applications
CNC Plasma Cutters offer a multitude of benefits, making them a highly sought-after tool in various industries. With their precision and accuracy, they ensure clean and precise cuts, resulting in high-quality output. The versatility of CNC Plasma Cutters allows them to handle a wide range of materials and thicknesses, providing flexibility in cutting applications. Additionally, their speed and efficiency contribute to faster production times, enhancing overall productivity. Moreover, CNC Plasma Cutters offer cost-effectiveness compared to other cutting methods, reducing material wastage and optimizing operational costs.
Harnessing these advantages, CNC Plasma Cutters find extensive applications across diverse industries. From metal fabrication and welding to automotive and aerospace sectors, CNC Plasma Cutters are instrumental in producing precise components for assembly and manufacturing processes. They are also employed in architectural and artistic fields to create customized designs and intricate patterns. In the industrial and manufacturing sectors, CNC Plasma Cutters play a crucial role in cutting metal parts and prototypes for machinery and equipment.
The applications of CNC Plasma Cutters are as vast as their benefits, contributing to the efficiency and quality of various industries. Their ability to deliver precise cuts, handle different materials, and optimize production processes make them indispensable tools in the modern manufacturing landscape.
Materials Used in CNC Plasma Cutting
CNC Plasma Cutting is a versatile technology that can effectively cut a wide range of materials. By harnessing the power of plasma, these cutting systems can effortlessly slice through various substances, including:
Mild Steel
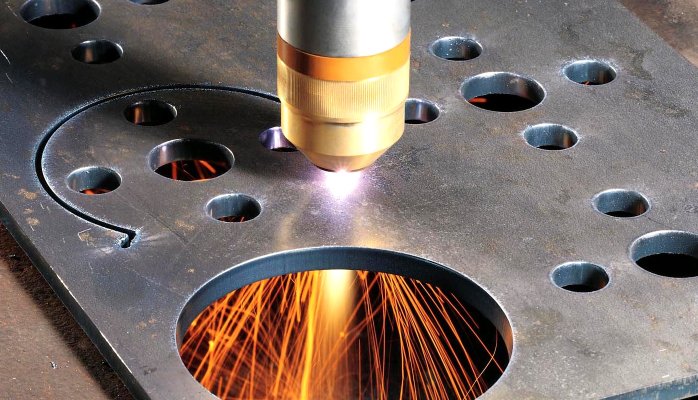
CNC Plasma Cutters excel in cutting mild steel, which is a common material used in many industries. Whether it’s thin sheets or thick plates, the plasma torch can swiftly and accurately slice through mild steel, making it ideal for applications in metal fabrication, automotive manufacturing, and construction.
Stainless Steel
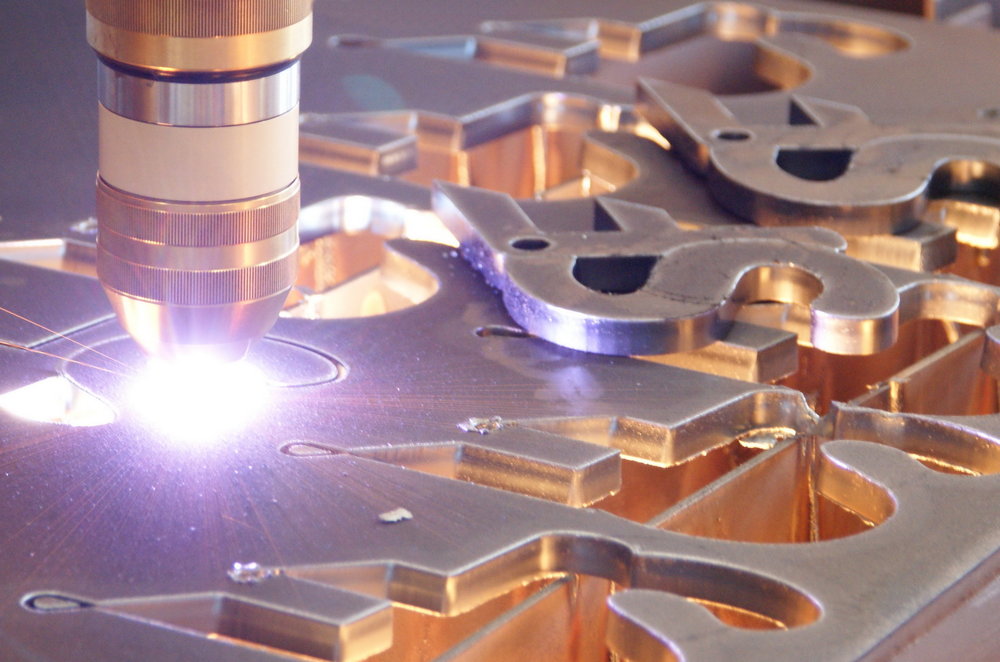
CNC Plasma Cutting is equally proficient in handling stainless steel. This material is known for its corrosion resistance and durability, making it a popular choice in the food industry, medical equipment manufacturing, and architectural applications. CNC Plasma Cutters can precisely cut stainless steel sheets, plates, and components, meeting the stringent requirements of these industries.
Aluminum
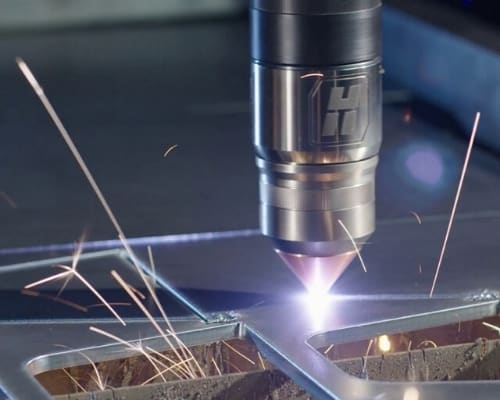
Aluminum is widely used due to its lightweight, strength, and excellent thermal conductivity. CNC Plasma Cutters are capable of cutting aluminum sheets and plates, making them suitable for industries such as aerospace, automotive, and marine. The high precision and efficiency of plasma cutting ensure clean cuts without compromising the integrity of the material.
Copper and Brass
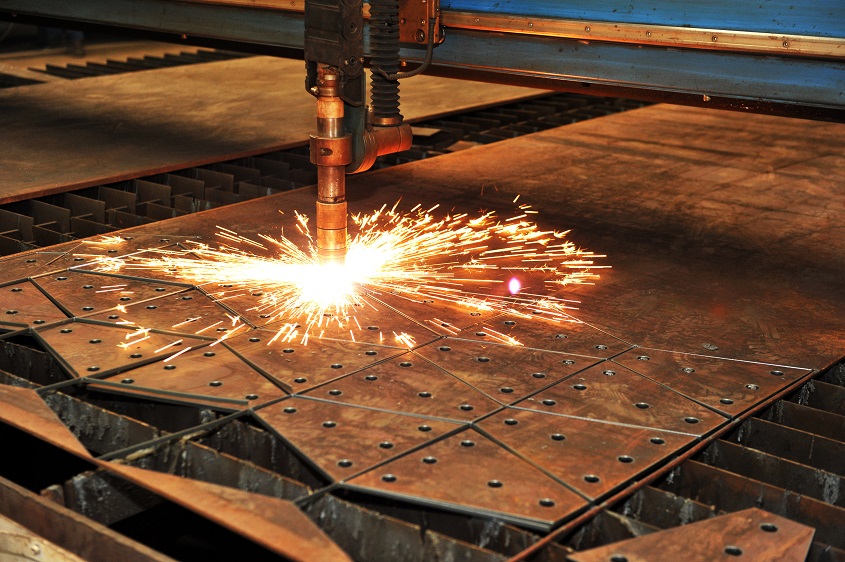
CNC Plasma Cutters can handle non-ferrous metals like copper and brass, which are valued for their electrical and thermal conductivity. These metals find applications in electrical components, plumbing fixtures, decorative art, and jewelry. The precision of plasma cutting allows for intricate designs and precise cuts on copper and brass materials.
CNC Plasma Cutters can also cut a range of other metals, including titanium, nickel alloys, and various alloys used in specialized industries. These materials often require high cutting precision and heat resistance, and CNC Plasma Cutting meets these requirements effectively. In addition to metals, CNC Plasma Cutters can be used to cut other materials like plastic and wood, although their primary focus is on metal cutting applications.
Other Articles You Might Enjoy
- 4 Remarkable Uses of CNC Plasma Cutters
CNC plasma cutters may sound like something out of a science fiction movie, but they are actually incredible machines that can do some pretty amazing things! CNC stands for Computer…
- CNC Plasma Cutters: 3 Hidden Secrets Only Experts Know
CNC plasma cutters have revolutionized the world of precision cutting and fabrication. With their remarkable versatility and precision, these machines have become an integral part of numerous industries. In this…
- Precision CNC Machining of Steel: High-Volume Production
Precision CNC Machining and High-Volume Production As an integral part of modern manufacturing processes, Precision Computer Numerical Control (CNC) machining brings about unmatched accuracy and consistency in the production of…