The manufacturing industry is undergoing a profound transformation with the advent of Industry 4.0. This groundbreaking initiative, embraced by major companies and countries alike, leverages IT technologies to automate production processes, promising greater efficiency and productivity. One area that stands to benefit significantly from this revolution is CNC machining technology. In this article, we will explore how Industry 4.0 is set to reshape modern machining methods and machine tools, paving the way for a new era of manufacturing.
Harnessing the Power of Big Data for Informed Decision Making
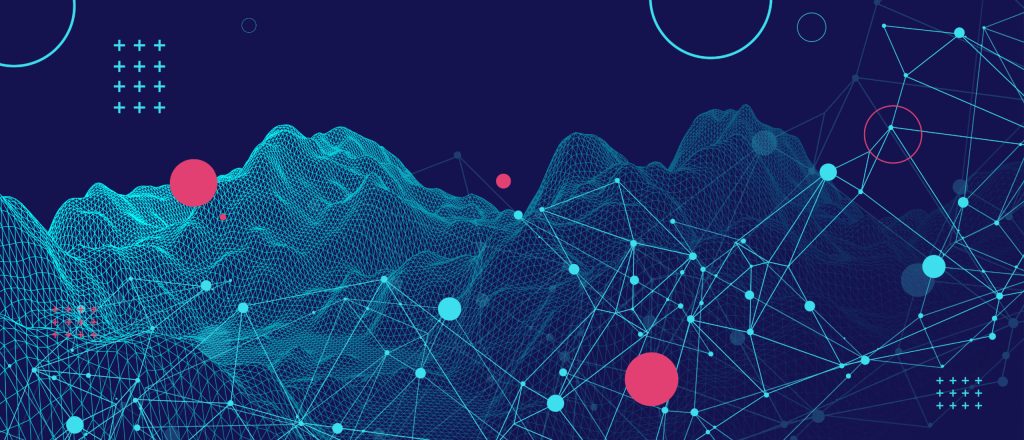
At the heart of Industry 4.0 lies the utilization of Big Data. The exponential growth in database size and the remarkable computational power of modern computers have made it possible to consolidate vast amounts of machining data in a single repository. This wealth of information encompasses the current and previous works of CNC machining shops, enabling a comprehensive analysis of past performance. By employing advanced neural networks, this data can be harnessed to optimize cutting parameters, clamping techniques, tool selection, and more. The machinist is no longer alone in their decision-making process; they now have an intelligent assistant that offers valuable insights and recommendations, streamlining operations and enhancing efficiency.
Empowering Preventative Maintenance with Real-time Monitoring
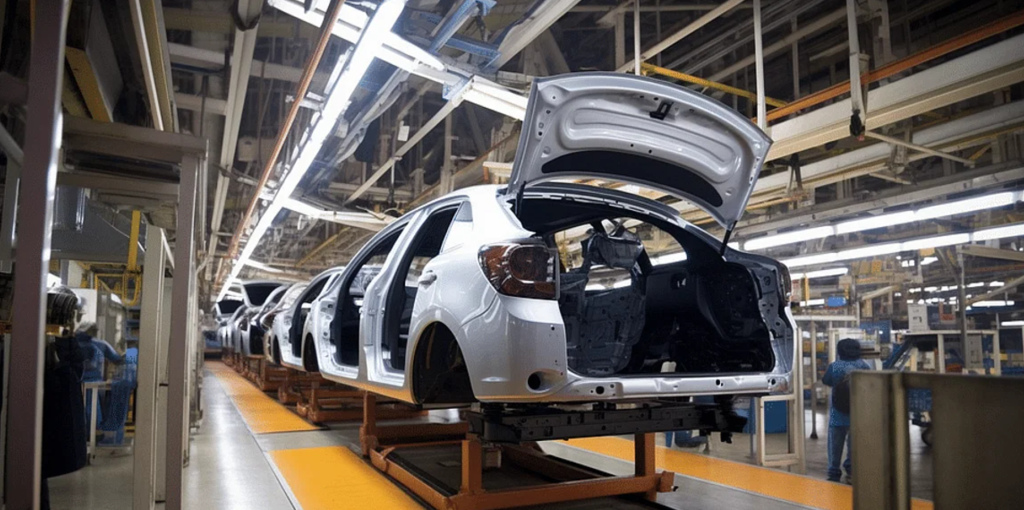
Machining tools, such as 5-axis machining centers, lathes, and grinding machines, are poised for a significant transformation in the Industry 4.0 era. Equipped with an array of sensors, these tools will be seamlessly integrated into comprehensive real-time monitoring systems. These sensors continuously gather data while the machine tools are in operation, providing valuable insights into their performance. For instance, they can estimate tolerance levels and compensate for tool wear by making dynamic adjustments to the tip coordinates or cutter diameters. Furthermore, the sensors can detect early signs of anomalies, allowing for proactive maintenance and replacement of components before they cause significant disruptions. By preventing unexpected breakdowns, machining shops can minimize downtime and maximize productivity.
Leveraging Data for Enhanced Process Planning and Optimization
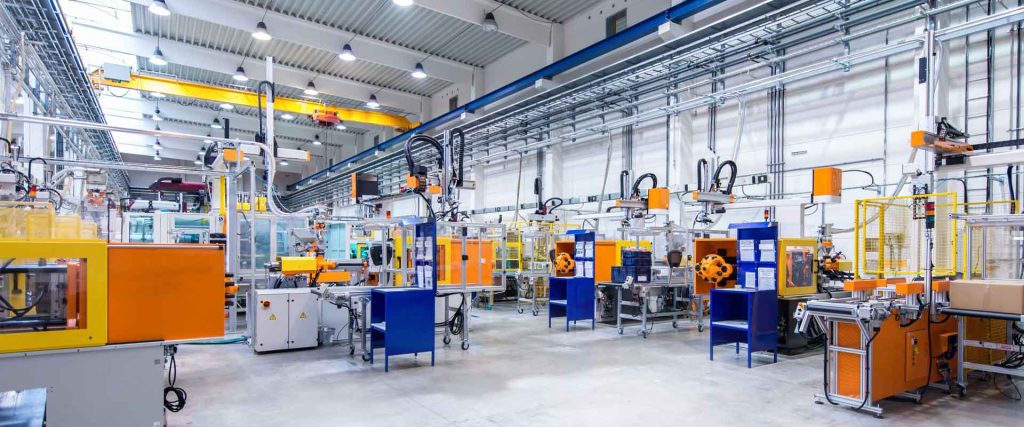
Traditionally, machine tools spend a significant portion of their operational time waiting for machined parts from previous operations. However, Industry 4.0 aims to revolutionize this by integrating all equipment within a unified digital management system. By having a comprehensive understanding of the required manufacturing operations for each part, the management system can swiftly calculate optimized machining routes. This intelligent system can dynamically adjust the routes when new parts are introduced or operational conditions change. As a result, the overall efficiency of the machining process significantly improves. With increased cutting time and decreased waiting time, the percentage of actual cutting in machine tools rises, leading to a substantial boost in productivity.
Automated and Streamlined Quality Control
Quality control has long been a complex and time-consuming aspect of manufacturing. However, Industry 4.0 brings forth a paradigm shift in quality control practices. Machine tools will be equipped with advanced sensors that continually evaluate key parameters such as part tolerance, surface finish, and hardness. This real-time evaluation occurs while the machine tools are actively cutting the material, eliminating the need for separate inspection processes. The integration of sensor data into the machining process ensures that parts are assessed without interrupting the manufacturing workflow. As a result, overall control time is reduced, allowing for faster production cycles and improved quality assurance.
Efficient Management of Machine Shop Supply
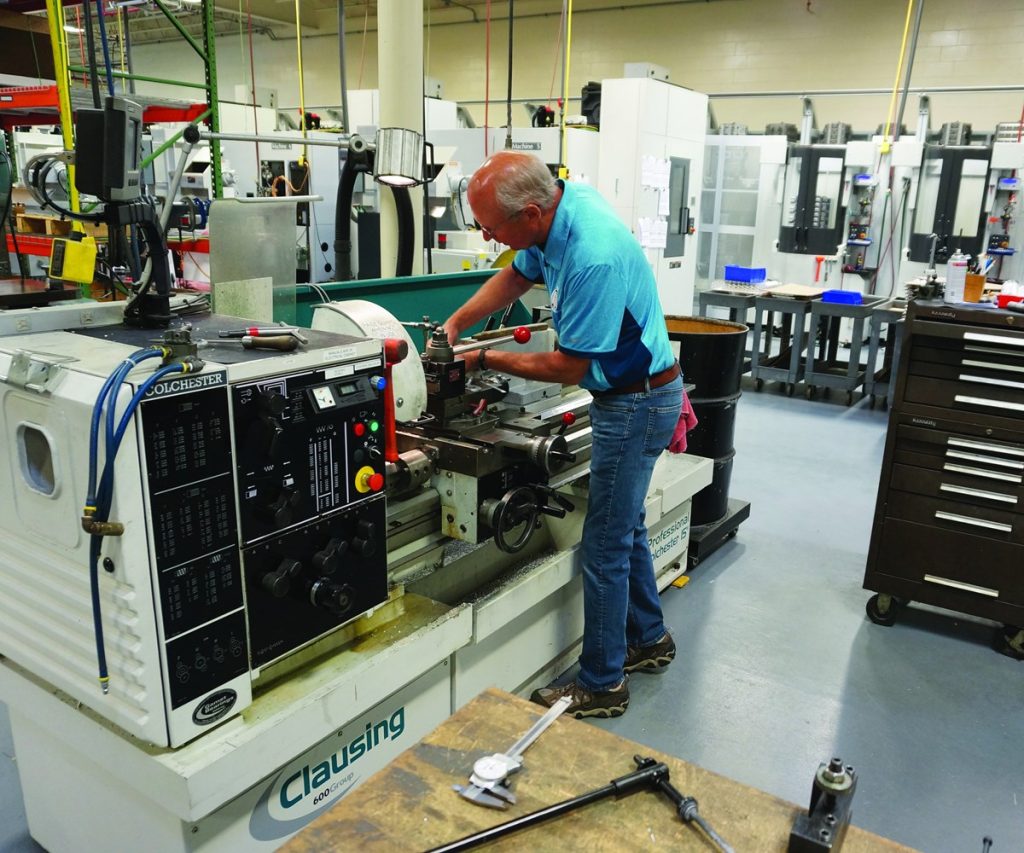
Industry 4.0 enables comprehensive automation and intelligent management of machining shops, extending to the realm of supply chain management. With the aid of neural networks, these systems can monitor supply storages, predict the materials and tools required for upcoming projects, and even generate automated orders from supply companies. By leveraging predictive analytics and real-time inventory management, machining shops can avoid production downtime caused by supply shortages. The materials and tools needed for each project will beavailable just in time, ensuring seamless operations and minimizing delays. This level of efficiency in supply management allows machining shops to optimize their production schedules, meet customer demands promptly, and maximize productivity.
The Rise of Online CNC Machining Services
In the era of Industry 4.0, the integration of Computer-Aided Manufacturing (CAM) systems and cloud technologies has revolutionized access to machining services. Engineers and machinists can now leverage the power of the Internet of Things (IoT) to remotely access and configure various types of machine tools. Through cloud-based platforms, clients can upload their CAD models, specify machining requirements, and seamlessly communicate with machining service providers. This streamlined process eliminates the need for extensive face-to-face discussions and reduces the time spent on administrative tasks. Clients can simply place their orders and await the delivery of their custom-manufactured parts, transforming the manufacturing experience into an efficient and convenient online shopping-like process.
The Future of Automated Manufacturing Systems
As Industry 4.0 continues to advance, machine automation and system integration are set to reach new heights. This progress will reshape the layout and operation of machine shops. Robotic manufacturing equipment will seamlessly integrate with machine tools, taking on tasks such as loading and unloading blanks, clamping and unclamping workpieces, inspecting part quality, and even changing cutting tools. This integration of robotics and machine tools creates advanced manufacturing cells that operate autonomously, reducing the need for constant human supervision. These cells are capable of working tirelessly, driven by a virtual management system and supplied with the necessary materials. By automating routine tasks and leveraging advanced technologies, machining shops can achieve unprecedented levels of efficiency, productivity, and flexibility.
In conclusion, the emergence of Industry 4.0 brings forth a wave of transformative changes to the field of machining. From harnessing the power of Big Data and real-time monitoring for decision making and preventative maintenance to streamlining quality control and supply chain management, the possibilities are vast. Cloud-based machining services offer convenient access to customized manufacturing solutions, while the integration of robotics ushers in a new era of automated manufacturing systems. As we embrace these advancements, the future of machining holds great promise, empowering businesses to achieve new levels of efficiency, quality, and competitiveness in the dynamic landscape of modern manufacturing.
Recommended Reads:
- 5 Key Differences between CNC Routers and CNC Mills
- Understanding CNC Routers: Top Question Asked
- 5 Essential Components of a CNC Lathe
- Differences Between CNC Lathes and CNC Mills
- Discovering CNC Lathes: 10 Fascinating Features to Know
- Comparing 6 Best CNC Milling Machines in the Market Today
Related Posts
- Precision CNC Machining of Steel: High-Volume Production
Precision CNC Machining and High-Volume Production As an integral part of modern manufacturing processes, Precision Computer Numerical Control (CNC) machining brings about unmatched accuracy and consistency in the production of…
- Material Versatility in CNC Machining: From Titanium to Thermoplastics
Introduction to CNC Machining CNC machining stands as a cornerstone in the manufacturing sector, enabling the precise creation of parts and components. This process utilizes computer numerical control (CNC) to…
- Precision CNC Machining for High-Performance Industrial Machinery
Precision CNC Machining for High-Performance Industrial Machinery The process of Precision CNC (Computer Numerical Control) machining is at the core of manufacturing high-performance industrial machinery. This technique leverages a computer's…