CNC machining has emerged as a go-to solution for manufacturing prototypes and parts involving cutting or drilling. This technology harnesses the power of a rotating cylindrical cutting tool to shape metal or plastic materials with unparalleled precision and speed. By employing CAD/CAM software, designers can transform their ideas into reality. However, before you embark on the CNC machining journey, it’s crucial to know how to prepare your CAD model effectively. Let’s explore some key considerations and optimization techniques.
Preparing CAD Models for CNC Machining
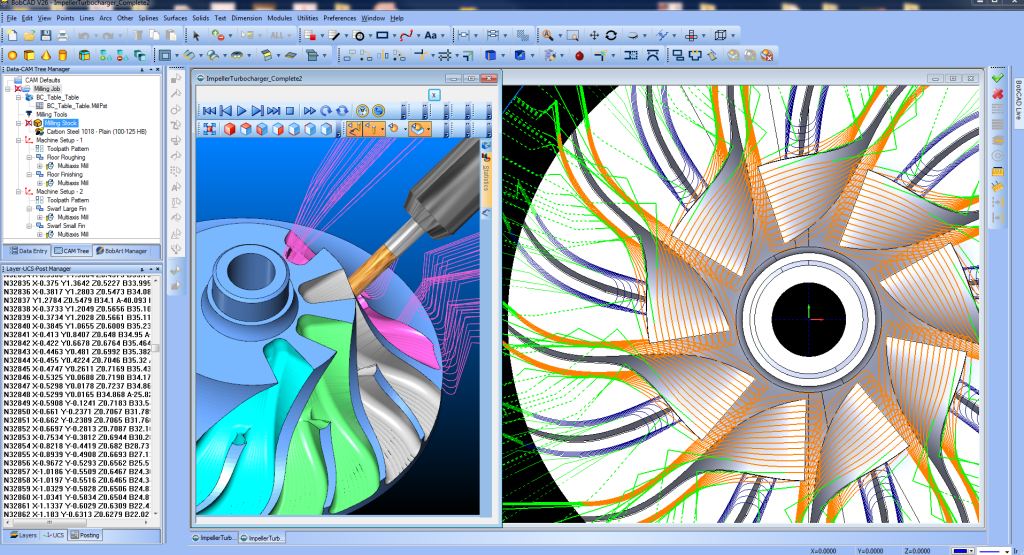
The initial step in the CNC machining process often involves creating the desired model using CAD software. Once the design is complete, it needs to be converted into either DXF or DWG file formats. Subsequently, the drawing is imported into CAM/CNC software, where it is translated into G-code, the programming language that governs the CNC machining machine’s operations.
Design Techniques for CNC Machining
When it comes to designing models for CNC machining, there are a couple of techniques you can employ. One approach involves manually tracing an image using vector cut paths. By outlining the silhouette and essential features of the image, you can save it as a DXF file and import it into a CAM program.
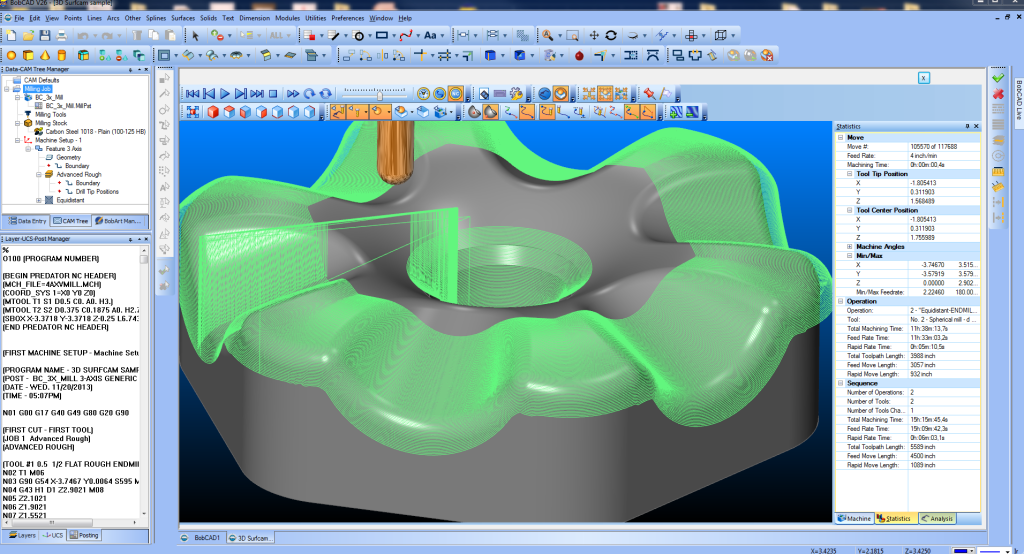
Alternatively, automatic image conversion is another viable method. This entails scanning your sketch, saving it as a PDF file, and converting it into a DXF file. The resulting vector file can then be imported into a CAM/CNC program to generate the necessary G-code.
Optimizing Designs for CNC Machining
Optimizing your design for CNC machining is crucial for achieving successful outcomes. Several factors determine the level of optimization required. Here are some tips to keep in mind:
Implementing Cavities, Edges, Walls, and Holes
Take into account the limitations of the CNC machine and optimize intricate sections of your CAD model for production.
- Depth and Diameter of Cavities: Limit the depth of cavities to four times the tool diameter to ensure optimal results.
- Edges: Adjust the corner radii above the recommended value by about 1mm for improved surface finish. Incorporate T-bone undercuts for internal corners at 90-degree angles.
- Wall Thickness: Be cautious when reducing wall thickness, as it can affect material stiffness, resulting in reduced surface finish quality. Maintain a minimum wall thickness of 0.8mm for metal designs and 1.5mm for plastic designs.
- Creating Holes: Plan the diameter and depth of holes based on the capabilities of standard drill bits. Utilize reamers and boring tools for holes requiring tight tolerances. Aim for thread sizes above M2, preferably M6 or higher for optimal results.
Integrating Text
When incorporating text into your design, consider the following:
- Maintain at least 0.5mm spacing between individual characters.
- Recess the text and use clear and concise fonts like Arial, Sans-Serif, or Verdana.
Eliminating Overlapping Geometry
To ensure smooth CNC machining, eliminate overlapping vectors in your design. Overlapping vectors cause redundant movement of the CNC machine.
Optimize your model by deleting duplicate objects, merging overlapping lines, and combining aligned sections of the design.
Placing Geometry on a Single Layer
Streamline your CAD drawing by reducing the number of vector lines to the minimum required without compromising design quality. When converting to a DXF file, export only the necessary parts of your model.
Defining the Scale of your Vector Image
Scale your vector image appropriately to optimize the CNC machining process. Stick to millimeters as the system unit and maintain a precision or tolerance of around 0.5 microns.
Recommended Read: 8 Must-Know Features of CAD Software for CNC Machining
Conclusion
By following these tips and refining your CAD design for CNC machining, you can significantly enhance the quality of your final part. When seeking professional-grade CNC machining services, platforms like Want.Net can offer the expertise and state-of-the-art machinery needed to bring your design to life. However, optimizing your CAD drawing using these techniques will ensure your design is primed for the CNC machine, resulting in parts and prototypes with exceptional precision and a superior surface finish.
Other Articles You Might Enjoy
- How to Optimize Your CAD Models for CNC Machining
In this article, we will explore the essential steps to optimize your CAD models for CNC machining. We will delve into various aspects such as geometry, tolerances, material selection, and…
- Precision CNC Machining of Steel: High-Volume Production
Precision CNC Machining and High-Volume Production As an integral part of modern manufacturing processes, Precision Computer Numerical Control (CNC) machining brings about unmatched accuracy and consistency in the production of…
- 8 Must-Know Features of CAD Software for CNC Machining
In the world of computer-aided design (CAD) and CNC machining, CAD software plays a pivotal role in transforming design concepts into precise and intricate machine instructions. CAD software allows engineers,…