Injection molding is expected to develop at a compound annual growth rate of roughly 6.2% over the next five years. Its growth is primarily driven by the rising demand for plastic components in the consumer goods, medical, packaging, automotive, and packaging industries, as well as the rising use of advanced technologies like 3D printing service and robotics.
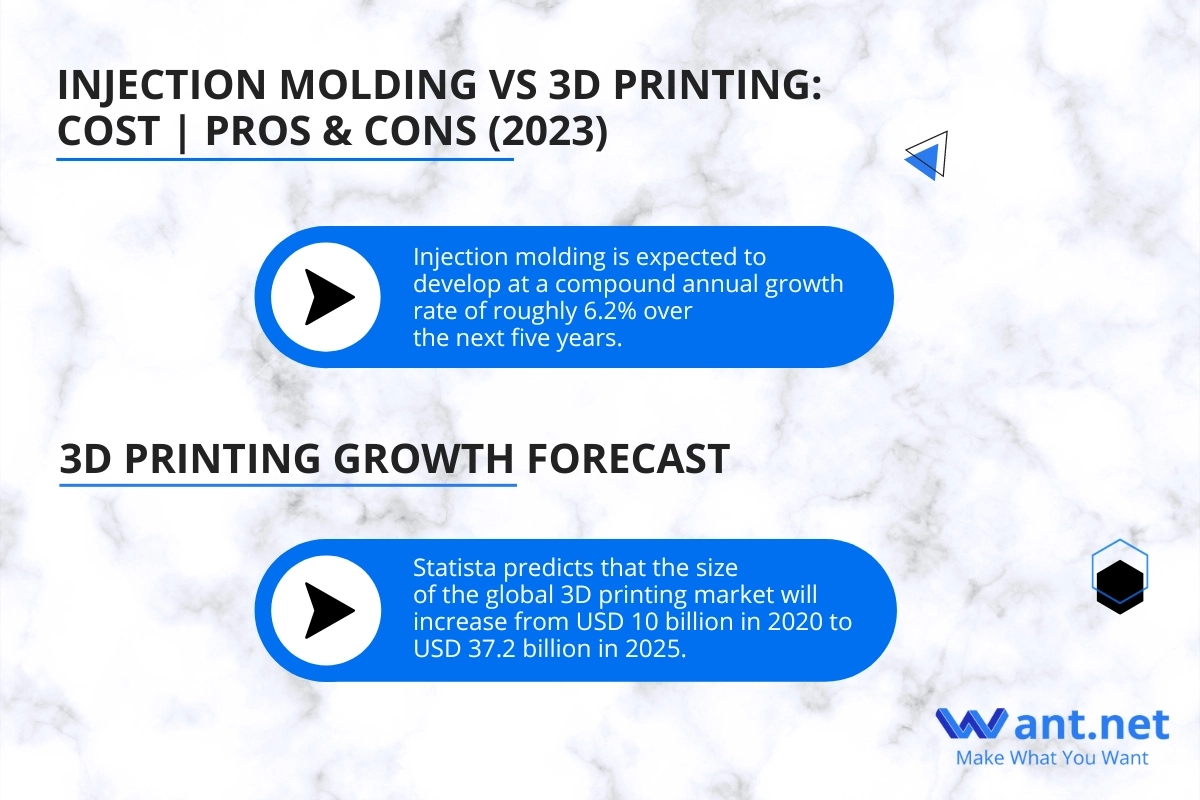
3D Printing Growth Forecast
In the coming years, 3D printing is expected to grow significantly. Statista predicts that the size of the global 3D printing market will increase from USD 10 billion in 2020 to USD 37.2 billion in 2025. This would indicate a compound annual growth rate (CAGR) of 19.6%. According to some reports, the growth rate might reach 28.9% CAGR.
The rising demand for 3D printed components and goods, the expansion of 3d printing applications, and the declining cost of 3D printing technology are some of the factors that are driving this growth. It is expected that the rise in 3D printing will continue as technology advances.
Injection molding is a large-volume manufacturing process. It is most commonly applied in mass manufacturing processes, where the particular component is produced hundreds or even countless times.
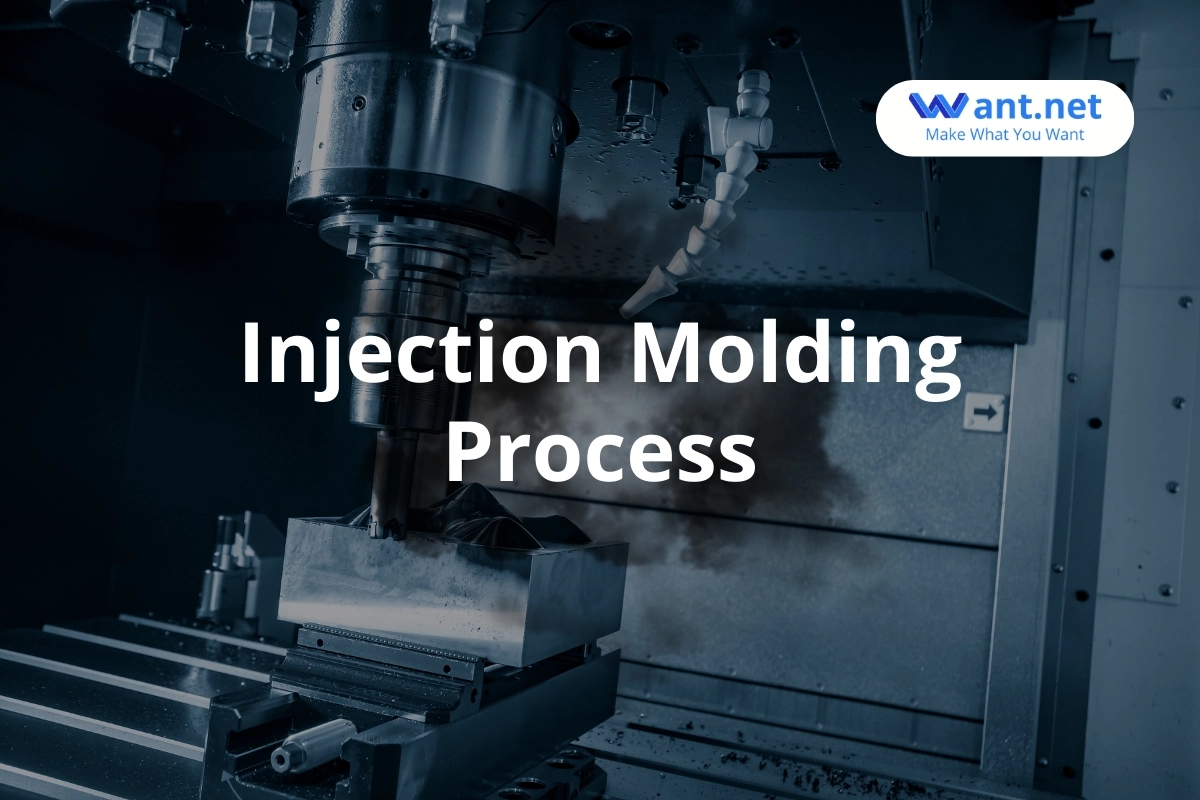
Injection Molding Process in 2023
Injection molding normally involves injecting hot, pressured, molten plastic or resin into a mound cavity, letting it cool, and then allowing it to solidify into the desired form.
Several industries, including the automotive, aerospace, medical, and consumer product sectors, use injection molding. Its ability to manufacture high-quality parts at a minimal cost has made it particularly popular in the plastics industry.
Why 3D Printing Mold?
3D printing molds have various advantages over traditional molds. Molds created with 3D printing may be made much more quickly and with a shorter lead time than conventional molds. Moreover, 3D-printed molds provide a far better level of accuracy and detail, including extremely small details that are impossible to accomplish with traditional molds.
3D-printed molds are also less expensive to produce and use than traditional molds. Finally, the ability to generate molds in a range of sizes and shapes makes 3D printed molds far more versatile in terms of 3d printing designs.
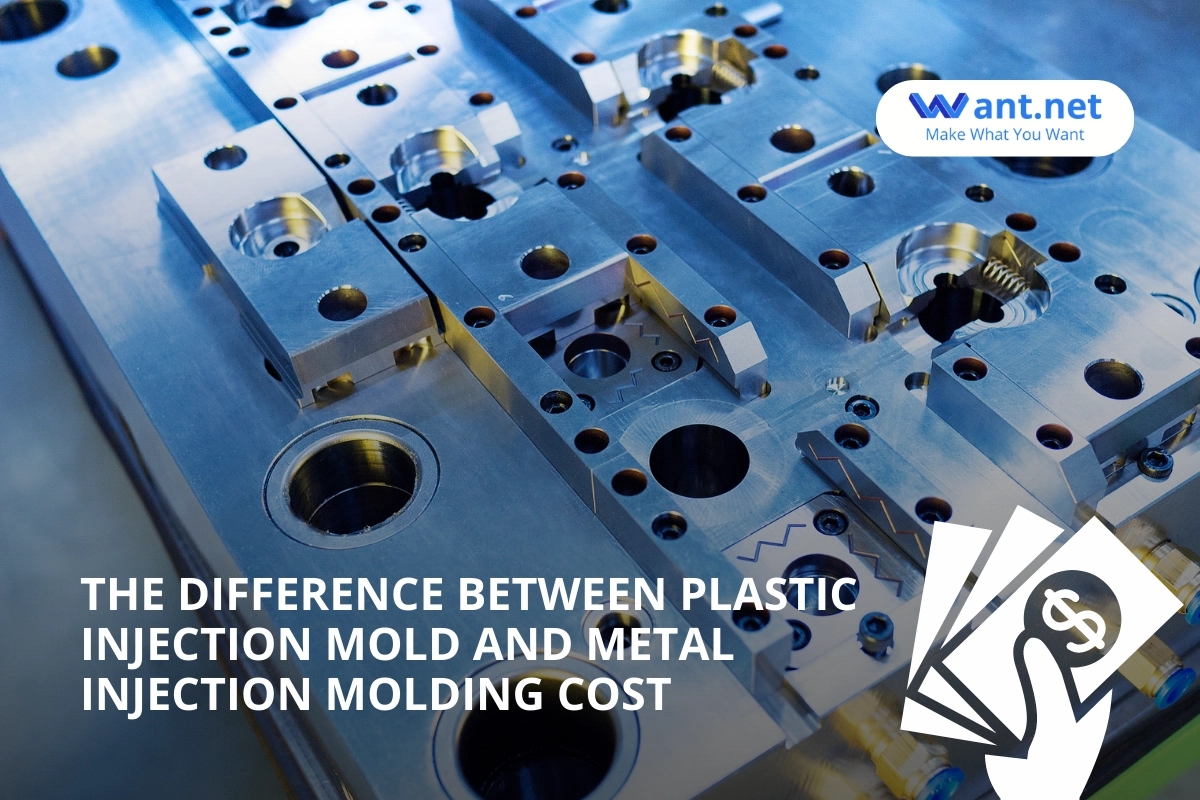
The Difference Between Plastic Injection Mold and Metal Injection Molding Cost
Molds & Tooling | 3D Printed Plastic Molds & Tooling @ Want.net | 3D Printed Metal Molds & Tooling at Want.net |
Parts Production costs | High | Low |
Custom Parts Production speed | Long | Short |
Custom Mold cooling time | Short to long | Long |
Parts Mold durability | High | Low |
Design flexibility | Low | High |
3D Printed Plastic Molds Pros & Cons
Pros:
- Cost-effective: 3D-printed plastic molds can be manufactured fast and cheaply, enabling companies to manufacture goods without having to spend a lot of money on molds.
- Versatile: Almost any product form or size may be produced using 3D-printed plastic molds.
- Customizable: 3D-printed plastic molds can be modified to produce one-of-a-kind goods.
- Durable: 3D-printed plastic molds can resist high temperatures and are more durable than traditional molds.
Cons:
- Limited material selection: The types of materials that can be used for 3D printing plastic molds are limited.
- Potential imperfections: 3D-printed plastic molds may have flaws like air bubbles or uneven surfaces.
- Potential for warping: If 3D-printed plastic molds are not properly supported during printing, they may warp.
- Possible contamination: 3D-printed plastic molds may include contaminants from the manufacturing environment.
Prototype Molds for Prototype Products
Prototype molds are also used to manufacture a product prototype before mass manufacturing. They are used to produce a 3D representation of a product and are often made of silicone or plastic. The prototype may be further tested and inspected to verify it matches the required specifications before going into full production.
A CAD program is used to design the product in the first step, after which a 3D model is produced using this design. After that, the 3D model is used to create a prototype mold.
What type of mold we can make with Injection molding?
The type of mold used can be injection, extrusion, or roto-molding, depending on the material used. The material is then poured into the mold, which is frequently liquid plastic, and allowed to cool and set. The prototype product is then taken out of the mold after it has dried and become solid.
The prototype item can then be tested and evaluated to make sure it meets the required standards. This involves doing tests on the product’s general design, durability, and strength. If any changes or adjustments are required, they can be made on the prototype first before the product is mass-produced.
A prototype mold is a crucial component of product design because it enables engineers and designers to test and evaluate a product before it is produced in bulk. They also make it possible to make quick adjustments and tweaks without having to start from scratch.
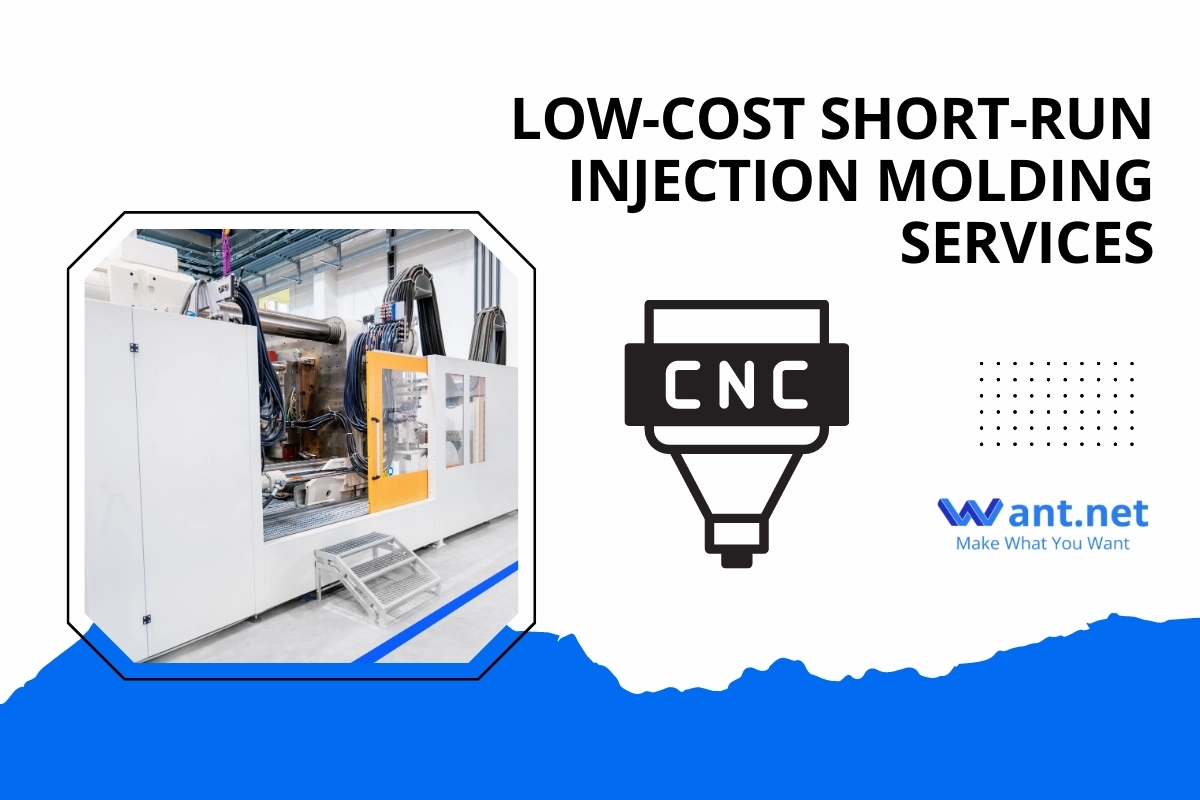
Low-Cost Short-Run Injection Molding Services
The best method to save cost on injection molding is to make a mold with a professional injection molding service. Similarly, the cost can be further reduced by manufacturing molding parts in large batches.
Introduction to Materials of Plastic Molds
Plastic molds are used to shape and mold various plastic goods. A plastic mold is a tool used to shape plastic into a certain form or pattern.
Polystyrene, polycarbonate, polypropylene, polyethylene, polyamide, and polyurethane are the materials that are most frequently used to make plastic molds. The plastic mold material used is determined by the application and required qualities of the plastic part.
Typically, a block of material like aluminum, steel, or plastic is machined into the mold. The mold is then heated, and plastic that has just melted is forced into it. The plastic is then cooled frequently with the help of a release agent extracted from the mold.
The precision and surface finish of the items made with a plastic mold depends on the competence of the mold maker and the mold’s construction quality.
A suitable plastic mold must be made with a long lifespan and an even distribution of the pressure from the injection process. The mold also needs to be built so that the plastic may be properly vented when it cools.
Plastic molds are used to make a wide range of products, including bottles, cups, and toys, as well as automobile parts and medical equipment. Plastic molds have the advantages of lower costs, higher precision, and reproducibility.
3D Printing Technology for Plastic Molds and Tooling
The use of 3D printing technology for plastic molds and tooling is gaining popularity. When compared to traditional technologies such as CNC machining and injection molding, 3D printing has numerous advantages.
3D printing is a more efficient and affordable way to generate parts and components, and it also enables greater design flexibility by quickly producing complicated shapes and intricate features.
3D printing can also be used to create molds and tooling for a variety of plastics, allowing for a wide range of 3d printing applications. 3D printing is perfect for creating custom, one-of-a-kind molds and tooling, as well as small batches of parts
Furthermore, complex molds and tools that are hard to make or impossible to make using conventional techniques can be produced using 3D printing machines.
Metal 3D Printed Mold Pros & Cons
Metal 3D printing, also called metal additive manufacturing, is a method of making metal components and parts using a 3D printer. A 3D object is created by melting metal powder layer by layer in a 3D printer.
This technology may make complicated shapes that are unattainable using conventional methods and is quicker and more affordable than typical metal machining methods.
Pros:
- Metal 3D-printed molds provide excellent resolution and precision for delicate shapes and features.
- They are cheap to make since they require less work and resources.
- They are strong and lightweight, making them perfect for usage in high-pressure and temperature conditions.
- Metal 3D-printed molds are useful to make a variety of items such as plastic, ceramics, and rubber.
Cons:
- Metal 3D printed molds can be costly, particularly in comparison to conventional molds.
- Metal 3D printed molds demand specialist equipment and skill to manufacture.
- Metal 3D-printed molds might not be compatible with particular materials, such as composites.
- Metal 3D printed molds require additional post-processing techniques to achieve the best results.
What Materials Do We Require for Metal 3d Prints?
Metal Molds created via 3D printing are a sort of tooling used to make parts and components. They are used to manufacture small to medium-sized parts and components for a wide range of sectors, including automotive, aerospace, healthcare, electronics, and consumer products.
Metals such as aluminum, steel, and titanium are used to create 3D-printed molds. These molds have a variety of benefits over conventional tooling, including shorter lead times, reduced costs, and greater design freedom. They also minimize the need for machining, which may be costly and time-consuming.
Furthermore, 3D-printed molds have increased accuracy and repeatability, which makes them perfect for intricate designs and very precise parts.
3D Printing for Vacuum Forming Molds
3D printing can be a great way to create custom vacuum-forming molds. 3D printing allows for the creation of complicated shapes and elaborate designs that would be challenging or impossible to create with conventional methods. 3D printing also provides greater material versatility, as several forms of plastic can be used to produce molds.
Moreover, 3D printing online is very affordable in comparison to other techniques, making it a desirable choice for vacuum-forming molds.
Why Want. Net for 3D Printing and Injection Molding?
Want.net offers excellent injection molding and 3D printing services at a very competitive price. We have state-of-the-art tools to make cheaper and more reliable molds with faster turnaround. Check out our service and get a free quote from us today!
Other Articles You Might Enjoy
- design for 3d printing how to reduce your cost
Relevance and Benefits of Cost Reduction in 3D Printing In an era where innovation is pivotal, 3D printing emerges as a transformative force across numerous industries, from manufacturing complex aerospace…
- Understanding 3D Printing: Processes, Benefits, and Uses
Introduction to 3D Printing Technology 3D printing, a transformative approach to manufacturing and prototyping, enables the creation of complex structures from digital blueprints by successively layering material until a three-dimensional…
- Finishing Options for Injection-Molding
Factors that impact the injection molding surface finish The best way to control the texture of plastic parts is to treat them with a specific finishing process. There are steps…