Introduction
In the competitive landscape of precision CNC machining, achieving a flawless surface finish efficiently and consistently remains a critical challenge. Manual deburring is labor-intensive, time-consuming, and prone to human error, leading to inconsistent results that can undermine product quality. Traditional surface finishing methods, such as dry blasting, often risk damaging delicate workpieces, causing warpage, or failing to meet the increasingly stringent specifications demanded by industries like aerospace, medical, and automotive. These challenges directly impact production efficiency, increase operational costs, and limit profitability for CNC workshops striving to maintain a competitive edge.
Vapor honing emerges as a transformative solution, redefining CNC surface finishing with its innovative, dust-free, and non-erosive process. Unlike conventional methods, vapor honing delivers superior finish quality, streamlines workflows, and creates a safer, cleaner, and more sustainable work environment. By integrating cleaning, deburring, and surface preparation into a single step, vapor honing empowers CNC professionals to achieve unparalleled precision while optimizing operational efficiency. This comprehensive guide explores the science behind vapor honing, compares its advantages to traditional techniques, and provides a detailed roadmap for its implementation in modern CNC shops, equipping professionals with the knowledge to make informed technology investments.
Part 1: Mastering Surface Finishing with Vapor Honing Technology
1.1 Defining Vapor Honing: Precision and Versatility
Vapor honing is a cutting-edge surface finishing process that utilizes a pressurized slurry of water, abrasive media, and compressed air to clean, deburr, and polish CNC workpieces with exceptional accuracy. Known by alternative names such as wet blasting, vapor blasting, aqua blasting, liquid honing, or slurry blasting, vapor honing employs a meticulously balanced slurry—a mixture of water and abrasive media—to deliver consistent, high-quality results across diverse materials and part geometries. This innovative vapor honing technology eliminates confusion from industry terminology while offering a versatile solution for CNC applications, from delicate components to robust industrial parts.
The slurry, the heart of vapor honing, is tailored to the specific needs of each workpiece, ensuring optimal outcomes for metals, plastics, composites, and ceramics. By combining mechanical abrasion with the lubricating properties of water, vapor honing achieves a level of precision and control unattainable with traditional methods, making it a game-changer for CNC shops seeking to elevate their finishing processes.
1.2 The Science of Vapor Honing: Flow Over Force
The defining principle of vapor honing is its “flow, not impact” approach, which fundamentally differentiates it from traditional dry blasting. While dry blasting relies on the aggressive, high-impact force of dry abrasive particles striking the surface, vapor honing employs a high-velocity, water-cushioned slurry to gently scrub the workpiece. This gentle yet effective mechanism prevents damage, erosion, or abrasive embedding, producing a smooth, uniform satin finish that enhances both aesthetics and functionality.
The presence of water in vapor honing serves multiple critical functions. It acts as a lubricant, cushioning the abrasive particles to minimize surface damage and create a polished, non-directional finish. Additionally, water eliminates frictional heat, a common issue in dry blasting that can warp thin-walled or precision CNC parts. By maintaining a cool operating environment, vapor honing ensures dimensional stability, making it ideal for components with tight tolerances. Furthermore, the non-erosive nature of vapor honing preserves the integrity of the workpiece, allowing CNC professionals to process delicate parts without compromising critical features like threads or sealing surfaces.
1.3 Anatomy of a Vapor Honing System: Engineered for Efficiency
A vapor honing system is designed for durability, precision, and cost-efficiency, making it a valuable addition to any CNC workshop. Key components include a corrosion-resistant stainless steel enclosure that maintains a clean and safe workspace, a wear-resistant slurry pump that circulates the abrasive mixture, and a blast gun with a precision nozzle for controlled slurry delivery. The recirculation system is a cornerstone of vapor honing’s cost-effectiveness, filtering and reusing the slurry to extend abrasive life and minimize water consumption.
Modern vapor honing systems often feature advanced closed-loop filtration, which recycles water and abrasive, reducing waste and eliminating the need for floor drains. Additional features, such as adjustable pressure controls and ergonomic designs, enhance operator efficiency and ensure consistent results. By integrating these components, vapor honing systems deliver a seamless, sustainable solution for CNC surface finishing, aligning with the demands of modern manufacturing.
1.4 Why CNC Shops Need Vapor Honing
Vapor honing addresses the core pain points of CNC surface finishing: inconsistency, inefficiency, and safety concerns. Unlike manual methods that rely on operator skill, vapor honing delivers repeatable results, ensuring every part meets exacting standards. Its ability to handle a wide range of materials and part complexities makes it a versatile tool for CNC shops of all sizes. Moreover, vapor honing’s dust-free operation eliminates health risks associated with airborne particles, creating a safer workplace and reducing cleanup time, which translates to significant cost savings and improved throughput.
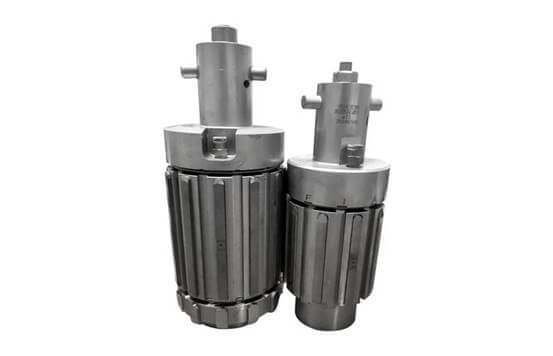
Part 2: Vapor Honing vs. Traditional CNC Surface Finishing Methods
2.1 Vapor Honing vs. Dry Blasting: Precision, Safety, and Cleanliness
Vapor honing outperforms dry blasting across critical metrics. Dry blasting’s high-impact approach often results in a rough, uneven surface with directional marks, while vapor honing produces a smooth, non-directional satin finish that enhances both aesthetic appeal and functional performance. The dust-free nature of vapor honing captures all abrasive particles and debris in water, eliminating the risk of silicosis and other respiratory hazards associated with dry blasting’s dusty environment. This makes vapor honing a safer choice for CNC operators and reduces the risk of dust-related explosions, a critical consideration for workshops handling flammable materials.
Dry blasting’s frictional heat can warp delicate parts or embed abrasives into the surface, compromising workpiece integrity. In contrast, vapor honing’s cool, cushioned process preserves dimensional accuracy and prevents abrasive embedding, making it ideal for precision components. Additionally, vapor honing streamlines workflows by combining cleaning, degreasing, and finishing in a single step, eliminating the need for separate processes and extensive post-blast cleanup required with dry blasting.
2.2 Vapor Honing vs. Vibratory Tumbling: Speed and Flexibility
Vapor honing offers significant advantages over vibratory tumbling, particularly for CNC applications requiring speed and precision. While vibratory tumbling can take hours to process parts, vapor honing completes the task in minutes, enabling faster turnaround times in high-pressure production environments. The bright, uniform satin finish achieved through vapor honing surpasses the duller, less consistent results of tumbling, delivering superior aesthetic and functional outcomes.
Vibratory tumbling is best suited for bulk processing of small, simple parts, but it struggles with large, complex, or delicate CNC components that risk damage during the tumbling process. Vapor honing’s line-of-sight control allows operators to target specific areas with precision, making it ideal for intricate or high-value parts. This flexibility positions vapor honing as a versatile solution for CNC shops handling diverse workloads.
2.3 Vapor Honing vs. Chemical Polishing: Eco-Friendly Precision
Chemical polishing introduces environmental and safety challenges that vapor honing elegantly avoids. By eliminating the need for hazardous chemicals, vapor honing simplifies regulatory compliance and enhances worker safety in CNC shops. Chemical processes can be unpredictable, risking excessive erosion if not carefully controlled, whereas vapor honing provides precise mechanical control for consistent, repeatable finishes.
Vapor honing’s adaptability to a wide range of materials—metals, plastics, composites, and ceramics—makes it far more versatile than chemical polishing, which is often limited to specific substrates. By adjusting abrasive media and pressure settings, vapor honing delivers tailored results for diverse CNC applications, from lightweight polymers to heavy-duty alloys, without compromising environmental sustainability.
2.4 Cost and Efficiency Comparison
Vapor honing’s recirculation system extends abrasive life 8-10 times longer than dry blasting, significantly reducing consumable costs. Its dust-free operation minimizes cleanup, while its single-step process eliminates the need for multiple finishing stages, saving time and labor. Compared to vibratory tumbling’s slow processing and chemical polishing’s regulatory burdens, vapor honing offers a cost-effective, efficient solution that enhances profitability without sacrificing quality.
Table 1: Comparative Analysis of Surface Finishing Methods for CNC Parts
Metric | Vapor Honing | Dry Blasting | Vibratory Tumbling |
Finish Quality | Smooth, uniform satin | Rough, directional matte | Dull, less consistent |
Tolerance Impact | No impact, non-erosive | High risk, erosive | Potential damage from impact |
Processing Speed | Fast (minutes) | Medium | Slow (hours) |
Operational Safety | High (dust-free, chemical-free) | Low (dust/silicosis risk) | Medium |
Environmental Impact | Low (recyclable water & media) | High (dust & waste) | Medium |
Ideal Application | Precision parts of all sizes | Rapid stripping, durable parts | Bulk processing of small parts |
Part 3: Vapor Honing’s Transformative Impact on CNC Machining
3.1 Achieving Flawless Finishes with Vapor Honing
CNC machining often leaves tool marks, scratches, or surface imperfections that detract from a part’s appearance and performance. Vapor honing excels at removing these flaws, blending the surface into a uniform, non-directional satin finish that meets both aesthetic and functional requirements. In many cases, the finish achieved through vapor honing is the final desired outcome, eliminating the need for additional processing steps and streamlining CNC workflows. This efficiency is particularly valuable for high-value parts where precision and presentation are paramount.
3.2 Streamlined Deburring with Vapor Honing
Manual deburring remains a significant bottleneck in many CNC shops, driving up labor costs and delaying production. Vapor honing revolutionizes this process by combining deburring and finishing in a single, efficient step. The gentle flow of the slurry sweeps away burrs without damaging delicate edges or compromising part geometry, making vapor honing ideal for intricate components with complex features. By reducing reliance on manual labor, vapor honing enhances productivity and ensures consistent quality across production runs.
3.3 Preserving Tolerances: The Non-Destructive Advantage of Vapor Honing
Maintaining tight tolerances is a make-or-break requirement for CNC professionals. Vapor honing’s water-cushioned, non-erosive process ensures no material removal, preserving critical dimensions, threads, and sealing surfaces. This non-destructive approach contrasts sharply with dry blasting’s erosive nature, which can alter part geometry and compromise functionality. Additionally, vapor honing introduces a peening effect, creating compressive stress that closes micro-cracks and enhances fatigue resistance, improving the durability and longevity of CNC components.
3.4 Optimizing Coating Preparation with Vapor Honing
A flawless coating begins with a pristine surface. Vapor honing creates an ideal anchor pattern for treatments like anodizing, Cerakote, painting, or PVD/CVD coatings. Its clean, uniform texture ensures maximum adhesion, preventing coating failures and delivering durable, high-quality finishes. By integrating cleaning, degreasing, and surface preparation into one step, vapor honing simplifies the coating process, saving time and resources while ensuring superior results for CNC parts destined for demanding applications.
3.5 Enhancing Workflow Efficiency and Scalability
Vapor honing optimizes CNC shop workflows by reducing processing time, minimizing cleanup, and eliminating the need for multiple finishing stages. Its dust-free operation creates a cleaner work environment, while its versatility accommodates parts of varying sizes and complexities. For high-volume production, automated vapor honing systems further enhance scalability, allowing shops to meet tight deadlines without sacrificing quality. By adopting vapor honing, CNC shops can achieve higher throughput, lower operational costs, and consistent results, positioning them for success in competitive markets.
3.6 Sustainability and Cost Savings
Vapor honing’s closed-loop filtration systems recycle water and abrasive media, significantly reducing waste and consumable costs. This eco-friendly approach aligns with modern sustainability goals, minimizing environmental impact while lowering operating expenses. Compared to traditional methods that generate high waste volumes or require costly chemical disposal, vapor honing offers a sustainable, cost-effective solution that enhances profitability without compromising performance.
Part 4: Practical Guide to Implementing Vapor Honing in CNC Shops
4.1 Selecting Abrasives for Optimal Vapor Honing Results
The choice of abrasive media in vapor honing is critical to achieving the desired finish. Key properties—hardness, shape, and size—determine performance. Common abrasives for CNC applications include:
- Glass Beads: Round, medium-hardness media that produce a bright, smooth satin finish, ideal for polishing aluminum or bare parts.
- Aluminum Oxide: Angular, high-hardness media that create a matte, etched surface for coating pre-treatment.
- Ceramic Beads: Hard, round media for fine finishes and peening to enhance part strength.
- Plastic Media: Soft, angular media for delicate cleaning or paint stripping without surface damage.
- Hybrid Media: A blend of abrasives for custom finishes, balancing deburring and aesthetic outcomes.
By selecting the appropriate abrasive, CNC professionals can tailor vapor honing to specific materials and applications, ensuring optimal results for every part.
Table 2: Abrasive Selection Guide for Vapor Honing in CNC Applications
Abrasive | Shape | Hardness (Mohs) | Resulting Finish | Primary CNC Application |
Glass Beads | Round | 5-6 | Bright, smooth satin | Polishing aluminum, bare part finishing |
Aluminum Oxide | Angular | 8-9 | Uniform, matte etch | Coating pre-treatment |
Ceramic Beads | Round | 9+ | Very fine, smooth satin | Peening, precision finishing |
Plastic Media | Angular | 3-4 | Cleaned, no etch | Delicate cleaning, paint stripping |
Hybrid Media | Mixed | Mixed | Deburrs with uniform finish | Deburring and cosmetic finishing |
4.2 Step-by-Step Vapor Honing Workflow
To achieve consistent, high-quality results with vapor honing, follow this best-practice workflow:
- Pre-Cleaning and Disassembly: Remove heavy oils, grease, and non-target components like bearings or seals to prepare parts for vapor honing. This step is critical to prevent damage and ensure optimal results.
- Blasting Technique: Maintain a 3-4 inch distance between the nozzle and workpiece, using small, circular motions to ensure even coverage. If dark patches (hot spots) occur, adjust to 8-12 inches and sweep again to correct.
- Post-Processing: Rinse parts thoroughly to remove residual abrasive, especially from blind holes or internal passages. Dry with compressed air and apply rust inhibitors for ferrous parts or clear coats (e.g., Cerakote) for aluminum to protect the vapor honing finish.
4.3 Advanced Equipment Features for Vapor Honing
Investing in advanced vapor honing equipment maximizes efficiency and ROI. Closed-loop filtration systems recycle water and abrasive, reducing costs and environmental impact. Turntables and custom fixturing ensure uniform coverage for complex or heavy parts, while automated vapor honing systems streamline high-volume production. Adjustable pressure controls and ergonomic designs further enhance operator precision and comfort, making vapor honing a seamless addition to modern CNC workflows.
4.4 Training and Operator Best Practices
Successful vapor honing implementation requires proper operator training. New users should practice on sample parts to master blasting techniques and abrasive selection. Regular maintenance, such as checking slurry consistency and replacing worn nozzles, ensures consistent performance. By investing in operator training and routine equipment care, CNC shops can maximize the benefits of vapor honing and achieve repeatable, high-quality results.
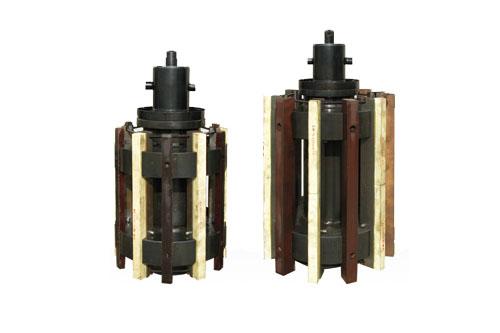
Part 5: Vapor Honing in High-Stakes Industries
5.1 Aerospace and Defense: Precision and Reliability
Vapor honing is a trusted solution in aerospace and defense, where precision and reliability are non-negotiable. Wet shot peening, a specialized vapor honing technique, enhances turbine and fan blade fatigue life by over 1000% while creating aerodynamic surfaces for optimal performance. For composites and additive manufacturing, vapor honing prepares surfaces for bonding without damaging fibers and cleans intricate 3D-printed channels that other methods struggle to access. In non-destructive testing (NDT), vapor honing cleans cracks to improve visibility during dye penetrant inspections, ensuring safety and quality in critical components.
5.2 Medical Device Manufacturing: Biocompatibility and Purity
In medical device manufacturing, vapor honing delivers biocompatible surfaces for implants and surgical instruments. For orthopedic and dental implants, vapor honing creates micro-textured surfaces on titanium alloys to promote osseointegration and enhance biocompatibility. Surgical instruments benefit from vapor honing’s ability to achieve sterilizable, non-reflective surfaces with precise roughness (Ra 0.25-0.6 µm), ensuring safety and performance in operating rooms. The dust-free, chemical-free nature of vapor honing eliminates contamination risks, meeting the medical industry’s stringent purity standards.
5.3 Automotive and Industrial Applications
Vapor honing is widely adopted in automotive and industrial sectors for finishing precision components like gears, molds, and engine parts. Its ability to clean, deburr, and prepare surfaces for coatings in a single step streamlines production, delivering consistent quality for high-volume applications. For example, vapor honing enhances the durability of automotive components by creating uniform surfaces that resist wear and corrosion, making it a preferred choice for manufacturers seeking efficiency and reliability.
5.4 Emerging Applications in Additive Manufacturing
Additive manufacturing (AM) presents unique challenges, such as cleaning complex internal geometries and removing residual powder from 3D-printed parts. Vapor honing excels in these applications, gently cleaning intricate channels without damaging delicate structures. Its versatility extends to post-processing AM parts for aerospace, medical, and industrial uses, ensuring smooth, functional surfaces that meet exacting standards. As AM adoption grows, vapor honing is poised to become an essential tool for CNC shops integrating additive and subtractive manufacturing.
Part 6: Maximizing ROI with Vapor Honing
6.1 Cost-Benefit Analysis
Vapor honing delivers significant cost savings compared to traditional methods. Its recirculation system extends abrasive life, reducing consumable costs by up to 90% compared to dry blasting. The dust-free process minimizes cleanup time, while the single-step workflow eliminates the need for separate cleaning, degreasing, and finishing stages. For CNC shops, these efficiencies translate to lower labor costs, faster turnaround times, and higher throughput, making vapor honing a high-ROI investment.
6.2 Scalability for Small and Large Shops
Vapor honing systems are available in a range of sizes, from compact units for small CNC shops to large-scale automated systems for high-volume production. This scalability ensures that shops of all sizes can adopt vapor honing without overextending budgets. Small shops benefit from affordable, space-efficient systems, while larger operations leverage automation to maximize productivity. By tailoring equipment to specific needs, vapor honing delivers flexibility and value across the CNC industry.
6.3 Sustainability and Regulatory Compliance
Vapor honing aligns with modern sustainability goals by minimizing waste and eliminating hazardous chemicals. Closed-loop filtration systems reduce water and abrasive consumption, while the dust-free process lowers environmental impact compared to dry blasting’s high waste output. Additionally, vapor honing’s chemical-free operation simplifies compliance with environmental regulations, reducing costs associated with chemical handling and disposal. For CNC shops prioritizing sustainability, vapor honing offers a forward-thinking solution.
6.4 Case Studies: Real-World Success with Vapor Honing
Leading CNC shops have embraced vapor honing to achieve remarkable results. For example, an aerospace manufacturer reduced finishing times by 70% by adopting vapor honing for turbine blade processing, improving both quality and throughput. A medical device company used vapor honing to create biocompatible implant surfaces, meeting FDA standards while cutting production costs. These success stories highlight vapor honing’s ability to deliver measurable benefits in real-world applications, reinforcing its value for CNC professionals.
Conclusion
Vapor honing is more than a surface finishing method—it’s a strategic upgrade for CNC workshops seeking to overcome the limitations of traditional techniques. By delivering superior finish quality, preserving tolerances, streamlining deburring, optimizing coating preparation, and creating a safer, cleaner work environment, vapor honing addresses the core challenges of modern CNC machining. Its versatility, efficiency, and sustainability make it an essential tool for shops aiming to enhance product quality, reduce costs, and stay competitive in demanding markets.
CNC professionals are encouraged to move beyond outdated methods and embrace vapor honing to transform their operations. Contact a trusted vapor honing equipment provider today to request a free sample part test and experience its game-changing benefits firsthand. For additional resources on optimizing CNC surface finishing with vapor honing, visit want.net. Elevate your workshop with vapor honing and unlock new levels of precision, efficiency, and profitability.
FAQ:
1. Will vapor honing damage threads or sealing surfaces on CNC parts?
No, vapor honing’s gentle, flow-based process cleans threads and sealing surfaces without erosion or damage, preserving the integrity of the base material.
2. Does vapor honing affect the tolerances of CNC parts?
No, vapor honing is a non-erosive process that does not remove parent material, ensuring critical dimensions and tolerances remain intact.
3. What are the consumable costs associated with vapor honing?
Vapor honing’s recirculation system extends abrasive life 8-10 times longer than dry blasting, significantly reducing consumable costs. Water and abrasive recycling also minimizes waste disposal expenses.
4. Can CNC parts be vapor honed without disassembly?
No, parts must be fully disassembled before vapor honing to prevent slurry from penetrating and damaging sensitive components like bearings or seals.
5. What maintenance is required for vapor honing equipment?
Vapor honing systems require minimal maintenance, including periodic replacement of water, worn abrasive, nozzles, and gloves to ensure consistent performance.
6. How can I protect the finish achieved through vapor honing?
For aluminum parts, apply a high-quality clear coat (e.g., Cerakote) or metal wax. For ferrous parts, use a rust inhibitor immediately after vapor honing to prevent flash rust.
7. How does vapor honing compare to manual deburring for CNC parts?
Vapor honing combines deburring and finishing in a single, efficient step, delivering consistent results and eliminating the labor-intensive, inconsistent nature of manual deburring.
8. Is vapor honing suitable for non-metal CNC components?
Yes, vapor honing can process plastics, composites, and ceramics by adjusting abrasive media and pressure, offering versatility for diverse materials.
Reference:
https://en.wikipedia.org/wiki/Abrasive_blasting
https://www.thefabricator.com/
Other Articles You Might Enjoy
- Elevating Surface Finish of CNC Machining Parts with High-Speed Techniques
High-speed cutting techniques have revolutionized CNC machining, offering not only increased production efficiency but also superior surface finishes on machined parts. The appeal of high-speed machining lies in its ability…
- How Can Electropolishing Improve the Surface Finish of CNC Machined Stainless Steel?
The Role of Electropolishing in Enhancing CNC Machined Surfaces Electropolishing is a critical finishing process used extensively in the fabrication of stainless steel components. This process not only enhances the…
- How Can Surface Finish Be Optimized in CNC Machining of Stainless Steel?
What Factors Affect Surface Finish in CNC Machining of Stainless Steel? The quality of the surface finish in CNC machining stainless steel is influenced by a variety of factors ranging…
- How to Choose the Right Surface Finish Techniques for Precision CNC Machining of Food Automation Machinery?
Surface Finish in Precision CNC machining Precision CNC machining plays a pivotal role in manufacturing components for food automation machinery. The surface finish of these components is crucial not only…
- Minimizing Chatter in CNC Machining: Tips and Tricks for Better Surface Finish
Are you tired of poor surface finish in your CNC machining? Chatter might be the culprit. Chatter is a common problem that can cause poor surface finish, reduced tool life,…