In the modern era, the success of CNC industries hinges on the production of parts that possess tight tolerances, impeccable surface finishes, and unwavering reliability. These meticulously crafted components contribute to the creation of robust, efficient, and competitive products, propelling industrial progress forward. However, the realization of such parts does not occur by happenstance. We owe our ability to drive cars, traverse continents by air, and even peruse this very text to the skillful discipline of CNC precision machining. This demanding endeavor encompasses a series of stages within the prototype manufacturing industry.
Design Development: A Delicate Balancing Act
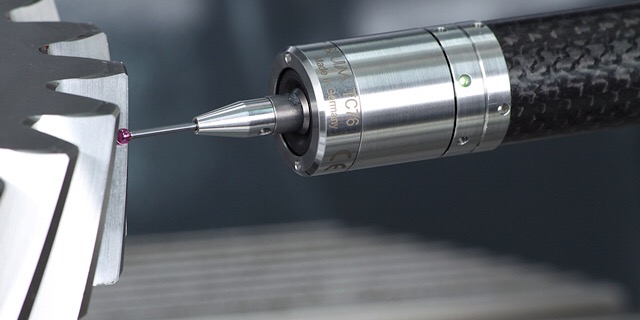
An ongoing struggle between designers and mechanical engineers revolves around the precision of developed parts. Designers approach the task from a theoretical standpoint, aspiring to attain flawless precision in every aspect of the machine, striving for geometrical perfection. However, manufacturing items according to the designers’ ideal specifications would be prohibitively expensive and yield little additional efficiency. The same dilemma arises when dealing with geometric complexity.
Consequently, manufacturing engineers and designers find themselves locked in a perpetual battle. There is even a jest that illustrates this conflict: while a manufacturing engineer envisions an ideal part as a simple wooden log, the designer yearns to create an entire airplane. The resulting compromise manifests in products boasting highly precise surfaces rather than individual components. This struggle eliminates economically inefficient features, reduces costs, and ensures optimal performance.
Deciphering the Main Technological Challenges
Having established that high-precision parts primarily refer to those with finely honed surfaces or groups of surfaces, it becomes apparent that the manufacturing process can be divided into two stages. The initial stage involves producing the required part with satisfactory quality while retaining excess material on the surfaces necessitating utmost precision.
The second stage revolves solely around achieving the desired precision and meeting performance requirements, such as material hardness, tensile strength, and additional surface finish parameters. Each part presents a unique challenge, characterized by distinct combinations of properties. Before designing the manufacturing process, it is crucial to consider how these challenges can be effectively addressed. For instance, if a part features numerous precise surfaces with varying tolerances, the second stage of the manufacturing process may be divided into groups based on these tolerances.
Crafting Strategies in Precision Machining
CNC precision machining predominantly employs abrasive processing due to its ability to yield optimal results. To ensure efficient grinding, the material being worked on must possess a minimum level of hardness. Therefore, most parts undergo some form of heat treatment. However, a considerable number of parts necessitate complex multi-stage hardening processes, requiring special attention to restoring the base surfaces after treatment.
Furthermore, the experts in CNC precision machining at Want.Net have developed various strategies to manufacture specific part features, such as precise deep narrow holes, exceptionally even and smooth planes, or groups of surfaces that require precise positioning relative to one another. For example, achieving this last objective can involve machining both surfaces in a single setup or securing the part with one surface while machining the other.
Meeting Performance Requirements with Finesse
Numerous high-quality parts come with specific performance requirements. Gears, for instance, demand exceptionally hard surfaces while retaining a softer core material. This is achieved through surface hardening techniques. Other parts may necessitate the use of carbon or nitrogen in conjunction with heat treatment to achieve the desired hardness. Certain components require coatings so fine that they are administered at the level of individual ions or atoms. Implementing these methods is intricate, as each material and hardness or coating feature has its own set of parameters.
So, how does one tackle such challenges?
Imagine you have a specialized shaft that requires nitro-carbonizing. Undertaking this unfamiliar process is time-consuming and may prove futile if it’s never needed again after completion. In this case, two solutions arise. One option is to outsource the operation to a machine shop or prototyping facility capable of performing these specialized operations. Although the cost per part may be higher, you ultimately save on investments and personnel hiring. Alternatively, you can discuss with the designer the possibility of switching to a more expensive material that eliminates the need for such a complex treatment.
Recommended Reads
- The 5-Step Guide to Mastering CAM in CNC Machining
- 4 Remarkable Uses of CNC Plasma Cutters
- Common Mistakes to Avoid When Writing G-Code
- Understanding CNC Routers: Top Question Asked
- 5 Essential Components of a CNC Lathe
Other Articles You Might Enjoy
- Zinc Alloys in CNC Machining: Benefits and Limitations
Introduction - CNC Machining and Zinc Alloys Computer Numerical Control (CNC) machining is a highly precise manufacturing process widely utilized in various industries to create complex parts. It makes use…
- Elevating Precision Standards through Chamfer in CNC Machining
1. Introduction: The Pursuit of Unparalleled Precision In the realm of CNC machining, precision is paramount. This section introduces the article by exploring the significance of precision in manufacturing and…
- Precision Prowess: Unveiling the Advantages of China CNC Machining
1. Introduction: The Role of Precision in Manufacturing Excellence In this introductory section, we delve into the critical role that precision plays in manufacturing and set the stage for an…