Welcome to the world of CNC milling, where precision meets creativity! Whether you’re a CNC enthusiast, a DIY hobbyist, or a professional in the manufacturing industry, understanding the importance of selecting the right materials for CNC milling is crucial. In this article, we will explore the top 5 materials best suited for CNC milling, shedding light on their unique properties and applications. To complement your knowledge, don’t forget to check out our article on 10 Key Features of CNC Mills You Should Know to delve deeper into the fascinating world of CNC milling technology.
#1 Aluminum
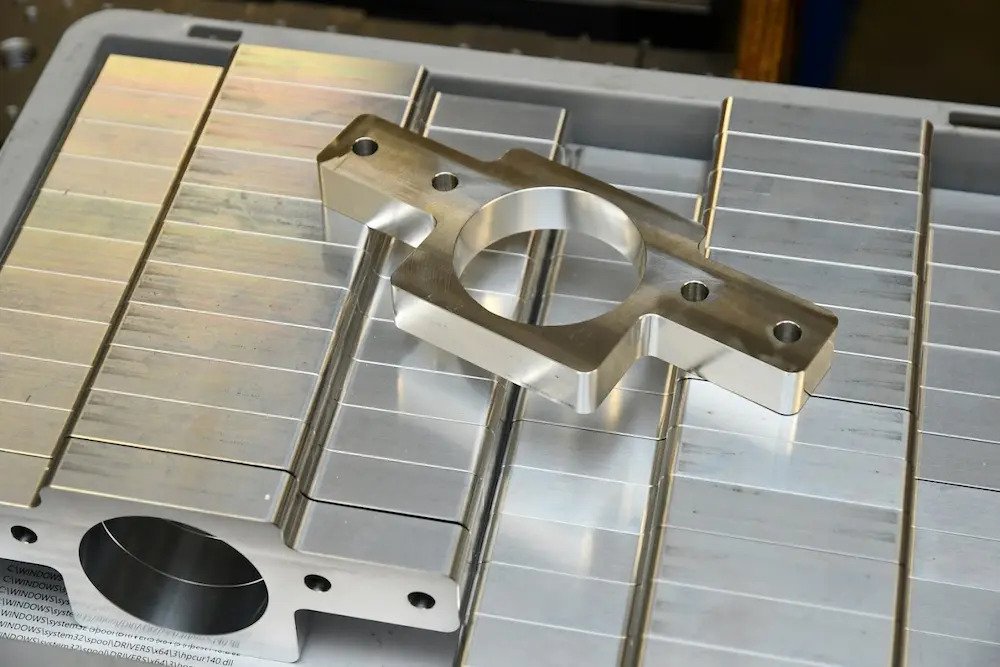
Aluminum, the lightweight powerhouse, stands as one of the most popular materials for CNC milling. Its exceptional properties and versatility make it a go-to choice for a wide range of applications.
Key properties and advantages of aluminum
- Lightweight: Aluminum’s low density ensures that CNC-machined parts remain lightweight without sacrificing structural integrity. This makes it an excellent choice for applications where weight reduction is crucial, such as aerospace components and automotive parts.
- Machinability: Aluminum’s softness and low melting point make it highly machinable. It allows for faster cutting speeds, resulting in increased productivity and reduced machining time. This quality also contributes to extended tool life, making aluminum a cost-effective option.
- Corrosion resistance: Aluminum naturally forms a protective oxide layer, rendering it highly resistant to corrosion. This makes it suitable for applications exposed to harsh environmental conditions, such as marine components and outdoor structures.
- Thermal conductivity: Aluminum exhibits excellent thermal conductivity, making it ideal for heat dissipation applications. Heat sinks and electronic enclosures are just a few examples where aluminum shines due to its ability to efficiently dissipate heat.
The versatility of aluminum lends itself to a multitude of applications in CNC milling.
Some common uses include:
- Prototyping: Aluminum’s machinability and cost-effectiveness make it a preferred choice for prototyping. It allows for quick iterations and the validation of design concepts before moving to production.
- Automotive components: From engine parts to suspension components, aluminum finds extensive use in the automotive industry. Its lightweight nature contributes to improved fuel efficiency and overall performance.
- Aerospace industry: Aluminum alloys, such as 7075 and 6061, are widely employed in the aerospace sector. They offer a high strength-to-weight ratio, ensuring structural integrity while minimizing weight.
- Consumer electronics: The excellent thermal conductivity of aluminum makes it an excellent choice for heat sinks in electronic devices. It efficiently dissipates heat, keeping electronic components cool and enhancing their lifespan.
#2 Steel
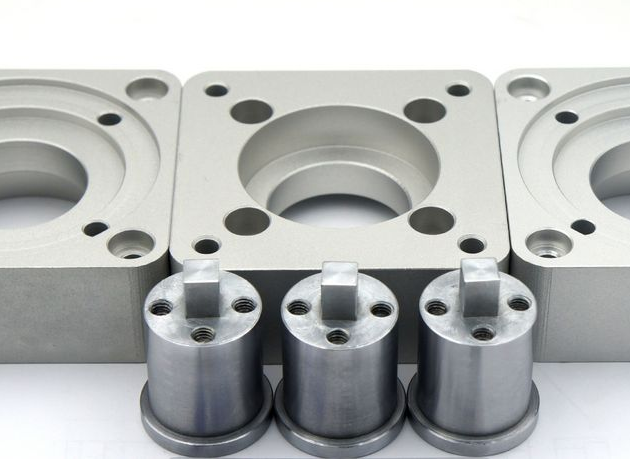
Steel, an alloy primarily composed of iron and carbon, holds a prominent place in CNC milling due to its exceptional mechanical properties. With its broad range of formulations and characteristics, steel offers versatility in achieving precise and reliable CNC-machined parts.
Different types of steel suitable for CNC milling
- Stainless steel: Renowned for its corrosion resistance, stainless steel is a popular choice for CNC milling. It contains chromium, which forms a protective layer on the surface, preventing rust and making it ideal for applications in harsh or corrosive environments.
- Tool steel: Designed for specific cutting tools and dies, tool steel exhibits high hardness, wear resistance, and toughness. It retains its cutting edge for extended periods, making it suitable for precision machining operations that demand durability and sharpness.
- Carbon steel: Carbon steel, a widely used alloy, contains varying amounts of carbon, which enhance its strength and hardness. It is known for its affordability, machinability, and versatility, making it suitable for a broad range of CNC milling applications.
Key properties of steel
Steel possesses several key attributes that contribute to its popularity in CNC milling:
- Strength: Steel exhibits exceptional strength, making it suitable for applications where structural integrity is paramount. Its high tensile strength allows for the fabrication of robust and load-bearing components.
- Durability: With excellent durability and resistance to wear, steel components can withstand demanding environments and heavy usage. This makes it suitable for applications requiring long-lasting and reliable parts.
- Heat resistance: Steel showcases remarkable heat resistance, maintaining its structural integrity at elevated temperatures. This property is particularly valuable in applications involving high temperatures, such as automotive and industrial machinery components.
Important factors to consider when machining steel
When machining steel in CNC mills, several factors should be taken into account:
- Tool selection: Choosing the appropriate cutting tools, such as carbide or high-speed steel, is crucial for efficient and precise machining of steel.
- Cutting parameters: Optimizing cutting speed, feed rate, and depth of cut helps achieve desired results while minimizing tool wear and heat generation.
- Coolant and lubrication: The use of coolant or lubricants during steel machining aids in chip evacuation, reduces heat buildup, and prolongs tool life.
- Tool wear monitoring: Regularly monitoring tool wear ensures timely tool changes, maintaining the quality of machined steel parts.
#3 Acrylic
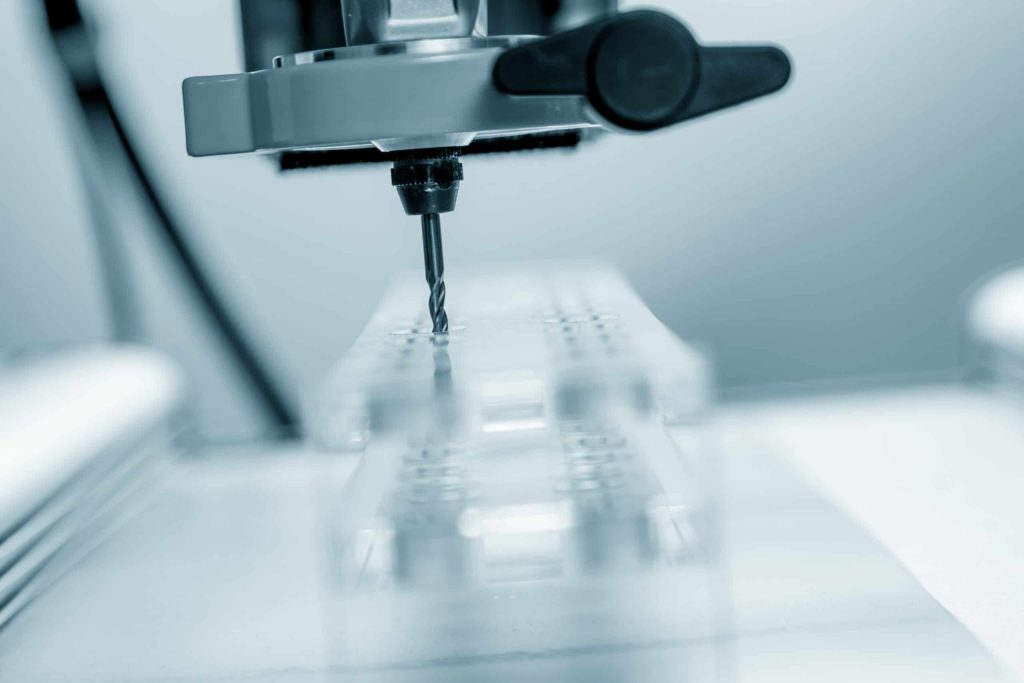
Acrylic, also known as Polymethyl methacrylate (PMMA), a versatile thermoplastic, is widely recognized for its optical clarity, ease of machining, and wide range of colors. Its popularity in CNC milling stems from its ability to achieve intricate shapes with precision and excellent surface finish.
Key advantages and applications of acrylic in CNC milling
- Versatility: Acrylic can be easily machined into various shapes and sizes, providing design flexibility for CNC milling projects. It can also be bonded, polished, and engraved, further expanding its range of applications.
- Impact resistance: Acrylic exhibits superior impact resistance compared to glass, making it suitable for applications requiring durability, such as protective covers, displays, and signage.
- Weather resistance: Acrylic has excellent weatherability, with high resistance to UV radiation and environmental factors. This makes it suitable for outdoor applications, including architectural elements and outdoor signage.
- Wide color options: Acrylic is available in a vast array of colors, allowing for CNC-machined parts that are visually appealing or match specific branding requirements.
Precautions and techniques for successful acrylic milling
To ensure successful acrylic milling, it is important to consider the following precautions and techniques:
- Proper tool selection: Selecting sharp, high-quality cutting tools specifically designed for acrylic machining helps achieve clean cuts and reduces the risk of melting or chipping.
- Optimized cutting parameters: Adjusting cutting speeds, feed rates, and depth of cut to prevent excessive heat buildup and minimize chip formation is crucial for achieving precise and smooth acrylic surfaces.
- Chip evacuation: Efficient chip evacuation is important to prevent re-cutting of chips, which can lead to heat buildup and surface imperfections. Proper dust collection or air blowing systems aid in removing chips during the milling process.
- Workholding: Securely and evenly holding down acrylic workpieces during machining prevents vibration and material shifting, ensuring accurate cuts and surface finish.
#4 Brass and Copper
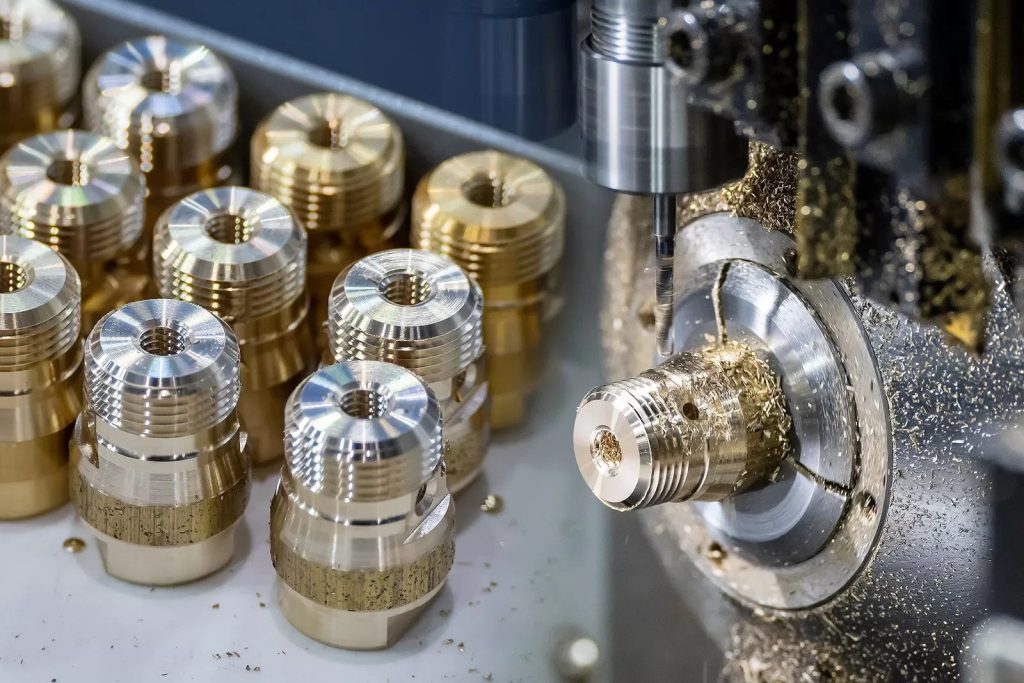
Brass and copper, two highly conductive metals, offer unique properties that make them valuable choices for CNC milling. In this section, we will provide an overview of brass and copper, emphasizing their thermal and electrical conductivity. We will explore common applications that benefit from CNC milling with these metals and discuss special considerations and techniques for machining brass and copper.
Special considerations for machining brass and copper
When machining brass and copper in CNC milling, it is essential to consider the following:
- Tool selection: Choose sharp and durable cutting tools, such as high-speed steel or carbide, to achieve clean and precise cuts in brass and copper.
- Cutting parameters: Optimize cutting speeds, feed rates, and depth of cut to prevent overheating and ensure proper chip evacuation. These metals have lower thermal conductivity than aluminum, so managing heat buildup is crucial to avoid workpiece deformation.
- Lubrication and cooling: Apply appropriate lubricants or coolants to reduce friction and dissipate heat during the machining process. This helps to extend tool life and maintain surface finish.
- Chip control: Efficient chip evacuation is vital in brass and copper milling to prevent re-cutting and ensure the integrity of the machined surface. Proper chip management techniques, such as using suitable chip breakers and coolant flow, aid in chip control.
By implementing these considerations and techniques, CNC milling brass and copper can yield high-quality parts with excellent conductivity properties. The thermal and electrical conductivity of these metals opens up possibilities for applications in various industries.
#5 Wood
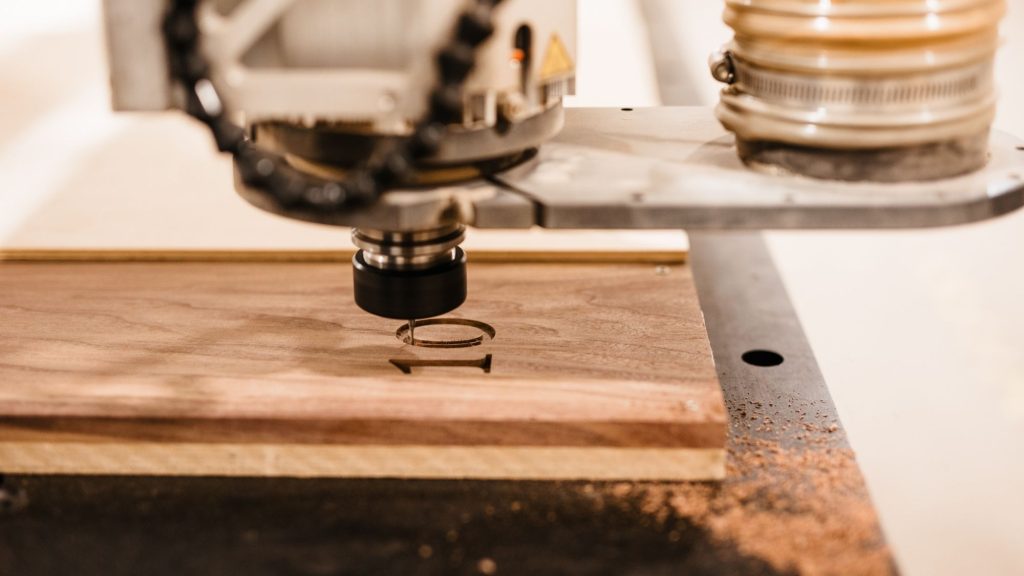
Wood, a renewable and abundant resource, offers a wide range of possibilities for CNC milling projects. Its natural warmth, unique grain patterns, and tactile qualities make it an attractive choice for various applications. Wood can be milled into intricate shapes, allowing for the creation of decorative, functional, and artistic pieces.
Tips for successful wood milling
To achieve successful results when CNC milling wood, consider the following tips:
- Wood type selection: Choose the appropriate wood species based on the desired aesthetics, strength requirements, and machining characteristics. Common hardwoods such as maple, oak, and walnut are popular choices for their durability and beautiful grain patterns. Engineered wood products like plywood and MDF offer cost-effectiveness and dimensional stability.
- Moisture content: Ensure that the wood has appropriate moisture content to avoid warping or cracking during and after milling. It is recommended to work with properly dried and stabilized wood to achieve dimensional accuracy.
- Tool selection: Select appropriate cutting tools based on the type of wood and desired outcome. Carbide or high-speed steel tools with sharp edges are commonly used for wood milling. Consider factors such as flute geometry and tool diameter for efficient chip evacuation and smooth cuts.
- Feed rates and cutting speeds: Optimize feed rates and cutting speeds to prevent burning or chipping of the wood. Balancing these parameters ensures efficient material removal while maintaining surface quality. Adjustments may be necessary based on the hardness and density of the wood.
- Hold-down and fixturing: Securely hold down the workpiece to prevent movement or vibration during milling. Proper fixturing techniques, such as clamping or vacuum systems, contribute to accurate and consistent results.
- Dust collection: Wood milling generates a significant amount of dust. Implementing effective dust collection systems helps maintain a clean work environment, prolongs tool life, and ensures operator safety.
Main Takeaway
When it comes to CNC milling, selecting the right materials plays a vital role in achieving successful outcomes. As you embark on your CNC milling journey, keep the following main takeaways in mind:
Consider project requirements and choose materials accordingly. Each project has unique demands for strength, aesthetics, conductivity, and more. The material introduced above offer distinct advantages, so select the best material based on your desired characteristics and applications.
Other Articles You Might Enjoy
- 7 Amazing Projects You Can Create with CNC Mills
When it comes to manufacturing and creating innovative designs, CNC mills have revolutionized the industry. These powerful machines offer unparalleled precision and versatility, making them ideal for a wide range…
- Using the Right Milling Technique: Down Milling vs. Back Milling
In the world of CNC milling, experts employ a myriad of techniques to maximize the capabilities of their CNC machines. These techniques are tailored to the size, shape, features, and…
- 10 Key Features of CNC Mills You Should Know
The significance of CNC mills in the modern manufacturing industry cannot be overstated. These cutting-edge machines are instrumental in the precise shaping and cutting of materials, ensuring impeccable accuracy. By…