In the world of CNC milling, experts employ a myriad of techniques to maximize the capabilities of their CNC machines. These techniques are tailored to the size, shape, features, and material of the part being machined. Among these techniques, two prominent cutting approaches are widely used: down milling and back milling. The choice of the cutting approach plays a vital role in the success of the machining process. In this article, we will delve into the definitions of each technique, explore their differences, and highlight their advantages and best applications.
Down Milling: Efficient and Heat-Reducing
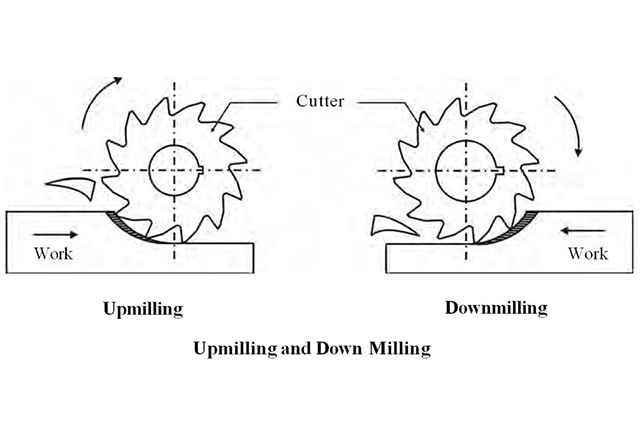
Down milling, also known as climb milling, involves feeding the work part in the same direction as the rotation of the cutting tool. This results in a downward cutting force. As the cutting tool engages with the work part, it progressively removes the maximum material until it reaches zero while rotating. By having the feed and cutting tool rotation in the same direction, down milling reduces resistance between the cutter and the workpiece. This, in turn, leads to less heat generation during the machining process.
Additionally, down milling offers several advantages. It exhibits a reduced load on the cutting edge, resulting in lower tool wear and a longer tool life. The cutting approach, from thick to thin, ensures a smooth surface finish. Furthermore, down milling requires a less critical work holding fixture and provides improved chip evacuation. These advantages make down milling the preferred choice for finishing operations.
Back Milling: Traditional and Resilient
Back milling, also known as up milling, follows the conventional milling method where the work part is fed against the rotation direction of the cutting tool. This creates an upward cutting force. Unlike down milling, in back milling, the cutting tool presses against the work part during engagement, resulting in relatively higher friction and heat generation. The cutter starts by removing the minimum amount of material and gradually cuts the maximum material as it rotates.
Back milling has its own set of advantages and best applications. It is traditionally used in situations where machines lack backlash eliminators. Back milling effectively counters the errors caused by machine backlash. This approach is preferred for rough cutting of tough and brittle materials such as hardened, cast, or forged parts. It is also favored when dealing with thin-walled and extended surfaces, as the opposing forces in back milling help minimize deflection during cutting.
Key Differences between Up Milling and Down Milling
To better understand the disparities between up milling and down milling, let’s compare them in terms of tooth engagement, chip evacuation, cutting forces, cutter wear, and cooling.
1. Tooth Engagement
Back milling, with its opposing cutting direction, results in minimal chip load on the teeth initially. As the tooth engages with the workpiece, the width of the chips gradually increases from zero to its maximum. In contrast, down milling starts by cutting the maximum material and gradually reduces it to zero as each tooth engages with the workpiece.
Achieving an excellent surface finish relies on maintaining the lowest possible chip thickness at the end of the cut. Therefore, back milling is the preferred choice for roughing processes, while down milling excels in finishing operations.
2. Chip Evacuation
Another crucial distinction between the two milling approaches is the direction in which the resulting chips separate from the work part. During back milling, chips are thrown upward, while in down milling, chips separate in a downward direction. Consequently, in up milling, chips tend to accumulate at the cutting zone, potentially obstructing the process and compromising the surface finish. On the other hand, down milling allows chips to evacuate easily without interfering with the cutting action. This makes down milling more suitable for effective chip management.
3. Cutting Forces
The cutting forces in both up milling and down milling vary based on the entry and exit of the cutting tool. In back milling, the cutting force starts from zero and gradually reaches its maximum. Conversely, in down milling, the cutting force begins at its maximum and gradually decreases to zero. Due to the cutting action in down milling, CNC milling can achieve relatively low power consumption.
Moreover, the cutting force in back milling tends to be directed towards the opposite side, potentially lifting the workpiece from its clamping. In contrast, the cutting force in down milling is directed downward, ensuring secure clamping of the work part and reducing the chances of dislodging.
4. Cutter Wear
Back milling, operating in the opposing direction, experiences higher friction, which increases the chances of cutter edge wear. Conversely, down milling minimizes tool wear since it cuts the material in the same direction as its feed.
When to Utilize Back Milling and Down Milling
Both back milling and down milling have their advantages and best applications. Here’s a closer look at when to use each technique:
Advantages of Back Milling:
Back milling, or up milling, is the traditional milling approach used before backlash eliminators were integrated into machines. It effectively counters the errors caused by machine backlash.
Back milling is preferred for rugged cutting demands involving tough and brittle materials such as hardened, cast, or forged parts. It is also the technique of choice when cutting thin-walled and extended surfaces, as it helps minimize deflection caused by opposing forces during cutting.
Advantages of Down Milling:
As CNC milling technology evolved, backlash eliminators were integrated into machines, enabling machinists to utilize down milling in their processes.
Down milling is generally considered the most efficient approach for machining parts under normal circumstances. Its advantages include reduced load on the cutting edge, resulting in lower tool wear and a longer tool life. The cutting approach, from thick to thin, ensures a smooth surface finish. Down milling also generates lower heat compared to back milling. It requires a less critical work holding fixture and provides better chip evacuation.
However, it’s important to exercise caution when employing down milling. Machine backlash and potential deflection of both the cutter and the work part should be taken into account.
Conclusion
In summary, down milling and back milling represent distinct approaches used in CNC milling services, each offering advantages in specific situations or applications. The fundamental difference lies in their cutting and feed directions. Down milling involves providing the material in the same direction as the cutting tool’s rotation, while back milling feeds the material in the opposite direction.
To achieve the desired outcomes in CNC milling, it is crucial to select the appropriate milling technique based on the task at hand. By understanding the differences, advantages, and best applications of up milling and down milling, machinists can optimize their CNC milling processes and achieve exceptional results.
Recommended Reads:
- The Art of CNC Precision Machining: Crafting High-Quality Parts
- Increase Your CNC Production Efficiency with a Robotic Arm
- AI Revolutionizing CNC Manufacturing
- Precision CNC Turning Services: Achieving Unparalleled Precision and Efficiency
- Precision 5-Axis CNC Machining in the Automotive Industry
Other Articles You Might Enjoy
- Revolutionizing Renewable Energy with CNC Machined Components
Introduction: Renewable Energy and CNC Machined Components Renewable energy harnesses power from natural sources such as the sun, wind, and water, making it a sustainable and eco-friendly alternative to traditional…
- Is Copper the Right Choice for Electrical Component CNC Machining? A Detailed Analysis
CNC Machining of Electrical Components Utilizing Copper In the field of electrical engineering, Computer Numerical Control (CNC) machining plays an integral role, particularly in the development and manufacturing of electrical…
- CNC Machining Brass vs. Bronze: Cost, Properties, and Applications Showdown?
Introduction to CNC Machining Brass vs. Bronze: Cost, Properties, and Applications Showdown? In this article, we delve into the debate between brass and bronze machining for an important manufacturing process…