When considering the production of CNC prototypes, cost is often a top concern. As designers, we strive to find ways to reduce expenses and enhance production efficiency. In this article, we will explore three valuable tips that can help you optimize the cost of CNC machining services.
#1. CNC Split Machining for Complex Parts
When mechanical strength is crucial for prototype testing, machining the part as a single piece is preferred. However, if the parts are used for design or appearance verification, considering CNC Split Machining for complex parts can be a cost-effective solution.
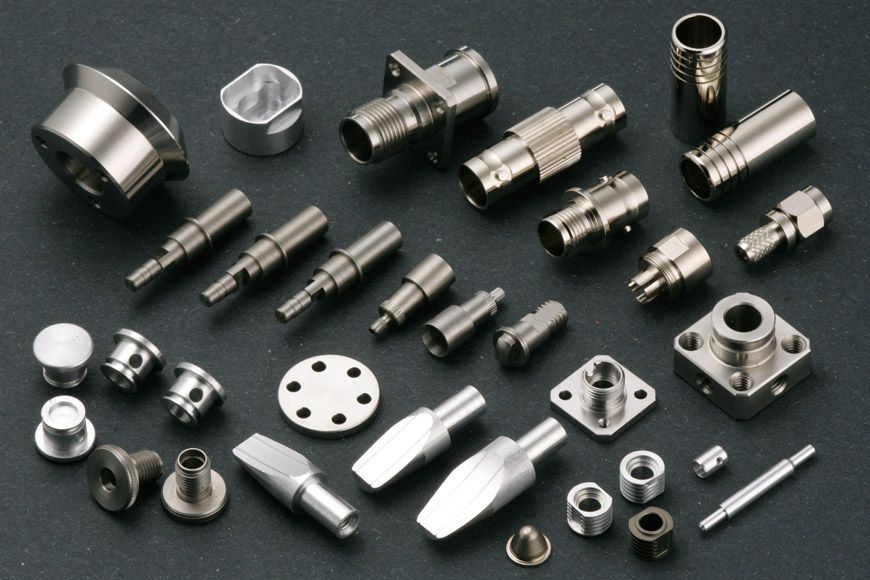
Complex structures often require processing in multiple planes, making the traditional approach challenging. By adopting the CNC Split Machining solution, the parts can be divided into several smaller pieces for processing. This eliminates the need for 5-axis auxiliary processing or frequent jig positioning and clamping, resulting in significant cost savings. Implementing CNC Split Machining optimizes the overall process and reduces processing time.
Cost Optimization:
For plastic parts with large, multi-dimensional structures, especially shell parts, the CNC Split Machining solution is highly recommended. Dividing the parts into separate pieces for processing and subsequently gluing them together is an effective approach. Rest assured that Want.Net possesses extensive experience in this area and employs specialized gluing schemes to ensure strong bonding.
In the case of complex metal parts with intricate internal structures and threads, disassembling and subsequently welding or screwing them together can be a cost-efficient solution.
#2. Internal Fillets for Assembly-Friendly Parts
During the manufacturing process, cutting tools, regardless of their size, are cylindrical with a specific diameter. This means that CNC machined parts cannot have internal corners with a radius. However, in cases where non-radiused corners are necessary for assembly, additional steps like manual corner clearing for plastic parts or electrical discharge machining (EDM) for metal parts can be employed. However, these steps increase costs.
To optimize cost, it is advisable to increase the internal corner radius if the design permits. This allows for the utilization of larger tools during processing, reducing the need for tool changes and shortening processing time.
Cost Optimization:
Set the inner edge with the largest possible and uniformly distributed inner radius to minimize cutter changes. This approach improves precision by reducing the number of tool changes. Visualize the cutting parts of the corner as riding a bicycle through a bend—the larger the bend, the easier it is to turn, ensuring a smoother path. Similarly, if we design the inner corner with a larger radius, the cutter will have more space to operate and minimize shaking.
A larger inner radius enables the use of a larger diameter cutter, allowing more material to be cut in a single machining path and speeding up processing efficiency.
#3. Proper Wall Thickness Design
Optimal wall thickness design is critical to avoid part breakage or deformation. Even with small cutting tools and low speeds, external forces and tool oscillation can affect thin-walled parts. Therefore, it is essential to consider proper wall thickness during the design phase.
Cost Optimization:
Reasonable design of wall thickness is crucial. For metal parts, it is recommended to maintain a wall thickness of over 0.8 mm, while plastic parts should have local areas with a minimum thickness of 0.5 mm. However, specific structural analysis is necessary as these are general guidelines.
In functional structural areas, it is important to increase wall thickness when required. For example, threaded hole portions should have adequate wall thickness to handle applied forces during screw tightening. Insufficient material thickness in these areas may result in thread breakage. Similarly, brass insert holes for tapping require careful consideration of material thickness distribution.
Concluding Remarks
Before initiating a prototype or low-volume production, consider these three cost optimization strategies. By implementing CNC Split Machining, increasing internal fillets, and maintaining proper wall thickness, you can reduce costs and improve the efficiency of your CNC prototype manufacturing process. We hope this article has provided valuable insights on reducing your project budget. For more details or inquiries, please don’t hesitate to contact Want.Net. We are here to assist you throughout the process.
Recommended Reads:
- 9 Advantages of CNC Machining Over Conventional Machining
- How to Optimize Metal Machining Strategies for Improved Prototyping
- CNC Milling: Revolutionizing Automotive Part Production
- How Should Manufacturers Choose Materials For Their Prototypes?
- Preparing Your CAD Model for CNC Machining
Other Articles You Might Enjoy
- Precision CNC Machining of Steel: High-Volume Production
Precision CNC Machining and High-Volume Production As an integral part of modern manufacturing processes, Precision Computer Numerical Control (CNC) machining brings about unmatched accuracy and consistency in the production of…
- Precision CNC Machining for High-End Audio Equipment
Precision CNC Machining in High-End Audio Equipment Manufacturing Precision Computer Numerical Control (CNC) machining refers to a highly-advanced technology where computer-generated codes are used to operate factory machinery and tools.…
- How to Reduce the Cost of CNC Prototyping
CNC prototyping offers tremendous opportunities for product development and manufacturing, but it can also come with a hefty price tag. With the right approach, however, you can significantly reduce the…