Computer Numerical Control (CNC) machines have revolutionized modern manufacturing processes with their precision and versatility. These machines use computer programs to control their movements and operations, resulting in highly accurate and repeatable outcomes. In this comprehensive guide, we will explore the five main types of CNC machines. Understanding these machines is essential for beginners in the world of CNC machining.
So, let’s dive in and explore each type in detail!
#1 CNC Milling Machine
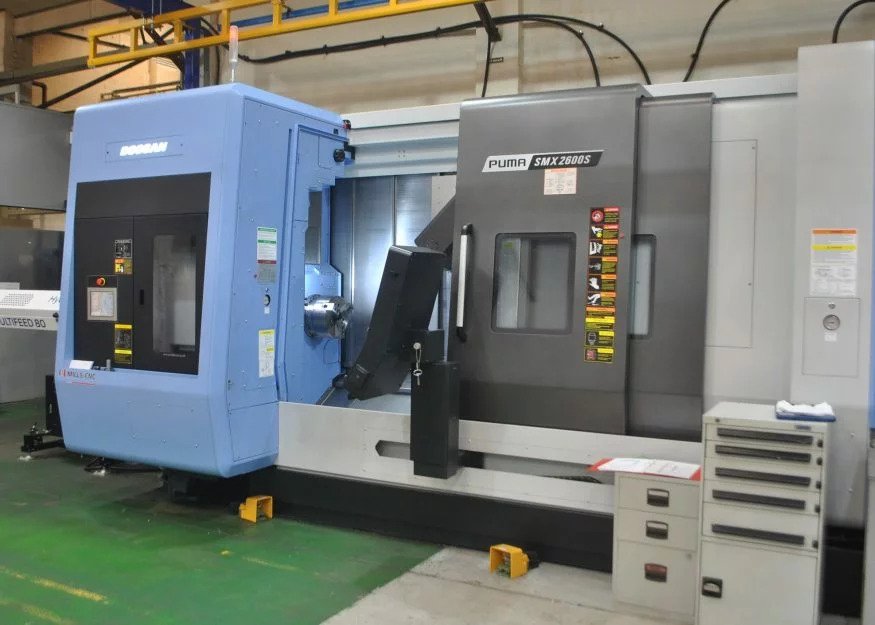
CNC milling is a machining process that utilizes computer control to remove material from a workpiece using rotating cutting tools. The primary function of a CNC milling machine is to precisely shape and cut various materials. By controlling the movement of the cutting tools along multiple axes, CNC milling machines can create complex shapes and contours with high precision.
CNC milling machines come equipped with several features that enhance their functionality. These include multiple axes of movement, tool changers for automatic tool swaps, and coolant systems to maintain optimal operating conditions. The versatility of CNC milling machines allows for a wide range of applications, including prototyping, mold making, and the production of precision parts for various industries.
CNC milling machines offer numerous advantages. Their high accuracy and repeatability ensure consistent results, while their automation capabilities increase productivity and efficiency. However, it’s important to consider the limitations of CNC milling machines as well. They typically require a significant initial investment and demand skilled operators to program and operate them effectively.
#2 CNC Lathe Machine
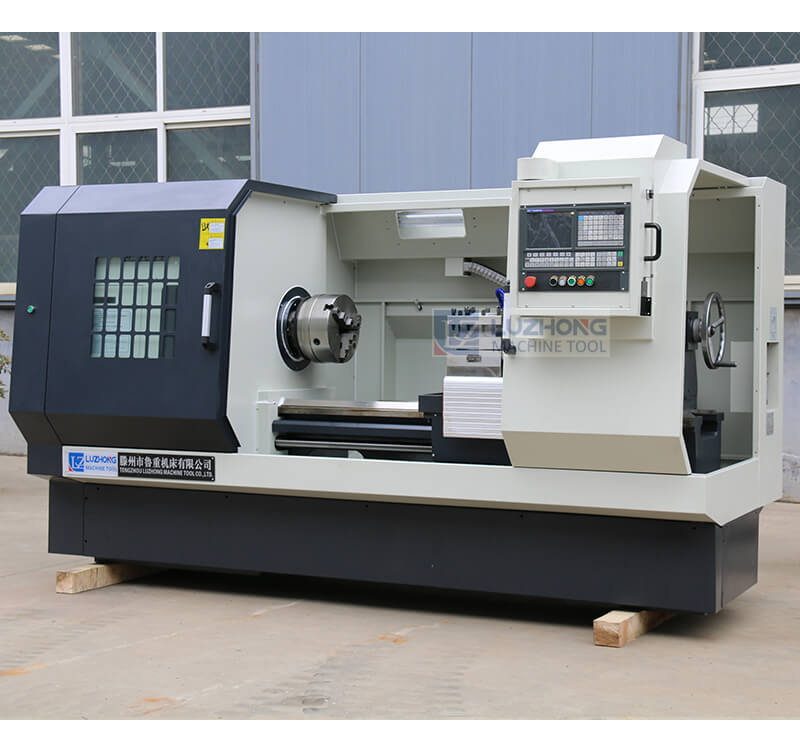
CNC lathe machines are precision machining tools that rotate the workpiece while cutting tools shape it into the desired form. These machines are primarily used in manufacturing to create cylindrical or rotational parts. CNC lathes allow for precise shaping and finishing operations by controlling the movement of cutting tools along multiple axes.
CNC lathe machines possess key features that enable various operations. They can perform turning, facing, and threading operations, allowing for the creation of intricate designs and precise measurements. CNC lathes find applications in industries such as automotive, aerospace, and medical, where the production of cylindrical or rotational parts is essential.
CNC lathe machines offer several advantages. They provide high precision and repeatability, ensuring consistent and accurate results. CNC lathes also reduce setup time and enhance productivity by automating the machining process. However, it’s important to note that CNC lathes are primarily suitable for rotational symmetry parts and may not be ideal for complex non-rotational shapes. Additionally, operating CNC lathes requires skilled operators who can program and oversee the machining process effectively.
Recommended Read: Top 15 Terms in CNC Machining: A Beginner’s Glossary
#3 CNC Router

CNC routers are machines designed for material shaping and cutting. They utilize various cutting tools, such as router bits, to carve, engrave, and shape a wide range of materials. CNC routers excel at precise and intricate cuts, making them ideal for detailed designs and patterns.
CNC routers boast several features that enhance their functionality. These include options for different spindle types, vacuum tables to hold materials securely in place, and tool changers for efficient tool swaps. CNC routers find applications in industries such as woodworking, sign-making, and prototyping. They are widely used in furniture production, advertising, and architectural design.
CNC routers offer numerous advantages. They are highly versatile and can work with various materials, including wood, plastic, and foam. CNC routers provide high precision and repeatability, ensuring consistent and accurate cuts. They are also relatively easy to use, with user-friendly software interfaces. However, it’s important to consider limitations, such as cutting depth restrictions that may limit the thickness of materials that can be processed. Additionally, proper dust collection systems are necessary to maintain a clean and safe working environment when using CNC routers.
#4 CNC Plasma Cutter
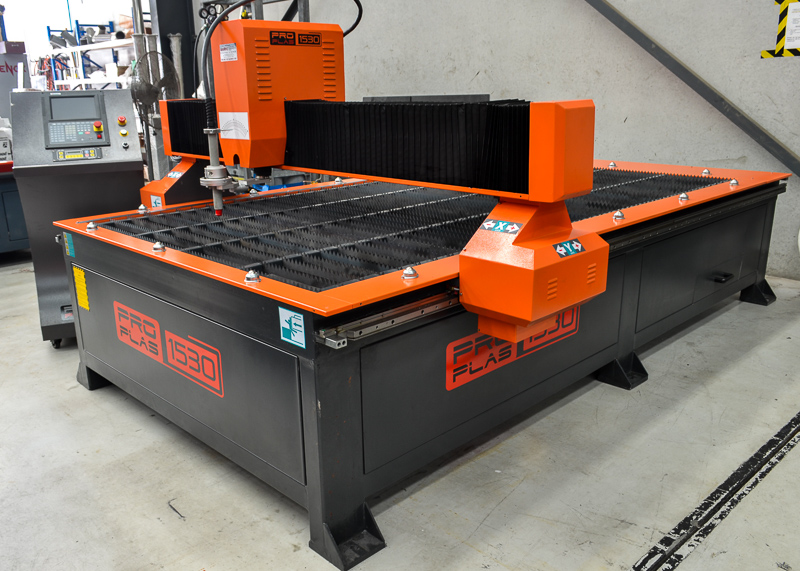
CNC plasma cutters play a crucial role in precision metal cutting. They utilize ionized gas, typically compressed air or nitrogen, to generate a high-temperature plasma arc. This arc melts and blows away electrically conductive materials, resulting in precise and clean cuts.
CNC plasma cutters are equipped with various features that enhance their performance. These include different power sources, torch heads for focused plasma arcs, and CNC controls for precise movement and cutting paths. CNC plasma cutters find applications in industries such as automotive, construction, and metal fabrication, where precise metal cutting is essential.
CNC plasma cutters offer several advantages. They provide high cutting speeds, making them suitable for large-scale production. CNC plasma cutters are versatile, capable of cutting various electrically conductive materials, including steel, aluminum, and stainless steel. They are also cost-effective compared to other cutting methods. However, it’s important to note that CNC plasma cutting may result in heat-affected zones in the surrounding material, requiring additional post-cutting processes. Adequate ventilation is necessary to remove fumes and maintain a safe working environment.
#5 CNC EDM (Electrical Discharge Machining)
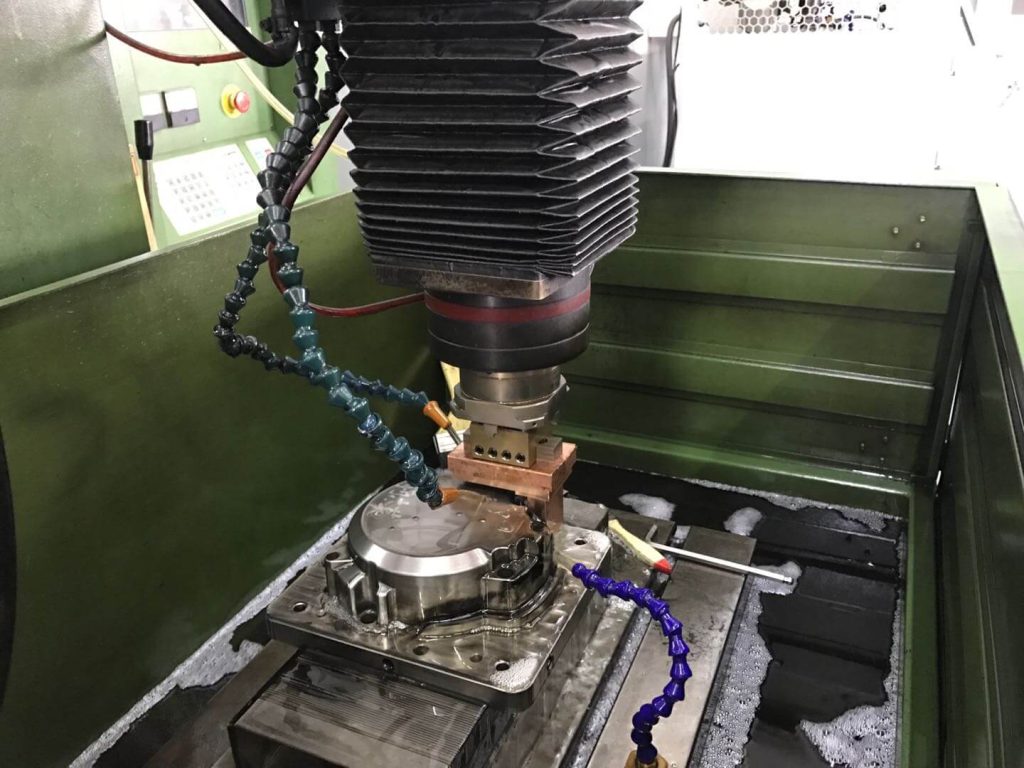
CNC EDM is a machining process that utilizes electrical discharges to remove material from conductive workpieces. It employs a controlled spark erosion process to shape intricate and complex parts with high precision. By creating a series of electrical discharges between an electrode and the workpiece, CNC EDM machines can precisely remove material without direct contact.
EDM machines possess unique features that contribute to their effectiveness. These machines can be configured as wire EDM or sinker EDM, depending on the specific application. They also incorporate advanced control systems to ensure precise and accurate machining. CNC EDM finds applications in industries such as aerospace, tool and die making, and medical device manufacturing, where intricate and highly precise parts are required.
CNC EDM offers several advantages. It enables the machining of complex shapes and profiles with exceptional precision and surface finish. CNC EDM machines can work with hard materials and are capable of producing intricate details that may be challenging for other machining methods. However, CNC EDM does have limitations. It is primarily suitable for conductive materials, and the process is relatively slow compared to other machining techniques. Additionally, CNC EDM requires skilled operators to program and oversee the machining process effectively.
Conclusion
We have delved into the world of CNC machining, exploring its rich history and the main types of CNC machines. Each of these machines, with its distinct features, functions, advantages, and limitations, plays a vital role in modern manufacturing processes.
By understanding the intricacies of the machines mentioned above, beginners entering the realm of CNC machining gain a solid foundation. These machines offer precise, efficient, and versatile production capabilities that have transformed the manufacturing industry.
From the early days of CNC machining to the present, these technologies have revolutionized the way we shape and create objects. By harnessing the power of CNC machines, manufacturers can achieve unprecedented levels of precision, streamline processes, and produce complex designs with ease.
As CNC machining continues to advance, it’s crucial for aspiring machinists and industry professionals to stay updated with emerging technologies and techniques. By embracing the capabilities of CNC machines and leveraging their potential, manufacturers can stay at the forefront of innovation and drive the future of manufacturing.
Other Articles You Might Enjoy
- 3 Types of CNC Milling Machines: Process & Production
What Is CNC Milling Machining Process? CNC milling is a process that uses rotating cutters to gradually remove material from a block until the required customs form is created. It…
- Types Of CNC Machine Tools: A Comprehensive Guide
CNC machines have revolutionized the manufacturing industry with their ability to perform a wide range of CNC machining procedures accurately and efficiently. One of the key factors that contribute to…
- Custom CNC Machining for High-Tech Security Systems
Introduction to CNC Machining for High-Tech Security Systems Custom Computer Numerical Control (CNC) machining plays an integral role in the production of high tech security systems. It is a manufacturing…