Introduction: Beyond Hardness—Why Titanium Carbide is a Game-Changer in Modern Machining
In precision manufacturing, the pursuit of speed, accuracy, and efficiency drives innovation. The evolution of Computer Numerical Control (CNC) machining has enabled the automated production of complex parts. However, a machine’s performance hinges on the capability of its cutting edge. Titanium carbide emerges not just as a hard material but as a transformative technology redefining CNC machining. Titanium carbide’s unique properties make it a cornerstone of advanced CNC machining, enabling manufacturers to achieve unparalleled efficiency and precision in high-speed applications.Titanium carbide is a key technology for achieving higher productivity, mirror-like surface finishes, and the ability to machine next-generation alloys. Its value lies in synergistic combinations with other materials, revolutionizing CNC tooling in three key forms:
- Titanium carbide-based cermet inserts: Engineered for high-speed finishing, offering exceptional wear resistance and surface quality.
- Titanium carbide tool coatings: Providing a durable “armor” for substrates like cemented carbide, enhancing performance.
- Titanium carbide specialty cemented carbide materials: Delivering unique properties for specific, high-performance applications.
This guide explores the material science of titanium carbide, its applications in CNC machining, a comparison with tungsten carbide, and practical guidance for engineers and machinists on tool selection, parameter optimization, and troubleshooting.
Part 1: The Atomic Blueprint of Performance—A Primer on Titanium Carbide Material Science
To understand titanium carbide’s exceptional performance in CNC machining, one must examine its atomic structure and physical properties, which underpin its advantages in practical applications.
Why Titanium Carbide Excels in CNC Machining
Titanium carbide’s combination of hardness, thermal stability, and low density makes it an ideal material for high-performance CNC tools. Its unique characteristics at the atomic level translate into macroscopic benefits, enabling machinists to push the boundaries of speed and precision.
Crystal Structure and Chemical Bonds: The Source of Extreme Hardness
The extraordinary hardness of titanium carbide stems from its face-centered cubic (FCC) crystal structure, resembling sodium chloride (a tightly packed 3D grid). Strong covalent bonds between titanium (Ti) and carbon (C) atoms form a robust, rigid lattice. This structure resists plastic deformation, resulting in a Mohs hardness of 9 to 9.5, comparable to tungsten carbide and second only to diamond. Titanium carbide’s Vickers Hardness (HV) ranges from 2800 to 3200, surpassing high-strength steels and conventional tungsten carbide (WC). However, this rigidity reduces slip planes, leading to brittleness, making titanium carbide ideal for resisting abrasive wear in finishing but prone to fracture under shock loads like heavy roughing.
Unmatched Thermal and Chemical Stability
High-speed CNC machining generates extreme temperatures at the tool tip. Titanium carbide’s thermal stability, with a melting point of approximately 3,160°C (5,720°F), ensures it maintains hardness and integrity under intense heat, critical for tool longevity. Its chemical inertness resists oxidation and chemical attack, reducing adhesion and diffusion wear when machining reactive materials like stainless steel, improving workpiece surface quality.
The Lightweight Advantage: Density and Modulus
Titanium carbide’s low density of 4.93 g/cm³, compared to tungsten carbide’s 15.6 g/cm³, makes titanium carbide tools significantly lighter. This reduces inertia in high-speed milling, easing spindle load and enhancing dynamic performance. With an elastic modulus of ~400 GPa and shear modulus of ~188 GPa, titanium carbide remains stiff under cutting forces, ensuring precision.
Thermal Conductivity and Heat Management
Titanium carbide’s thermal conductivity (21–25 W/m⋅K) is lower than tungsten carbide’s (84–100 W/m⋅K), acting as a thermal barrier. This protects titanium carbide tools and workpieces by directing heat into chips, preventing thermal softening and enabling higher cutting speeds.
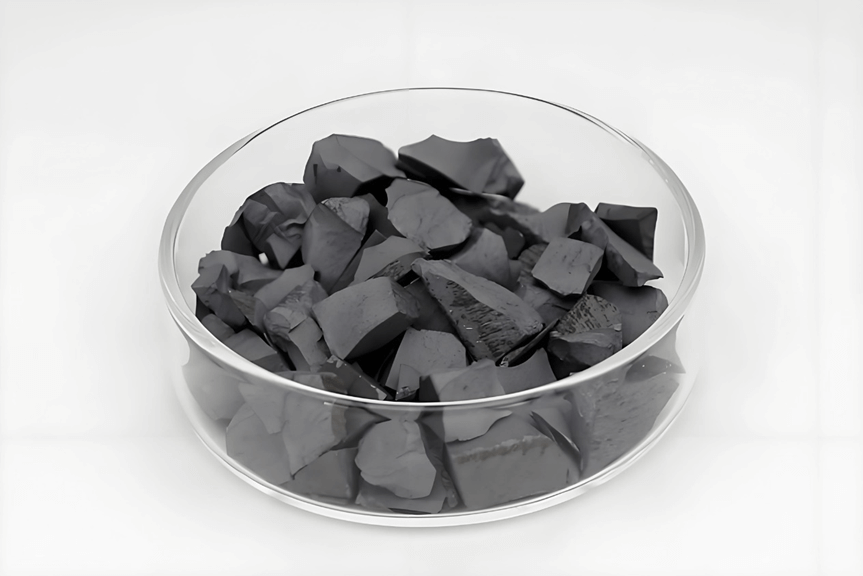
Part 2: Titanium Carbide in Action—Revolutionizing CNC Tooling Technology
Titanium carbide serves as a platform technology, enhancing CNC tooling through synergistic applications in cermets, coatings, and specialty materials, transforming productivity and performance.
Titanium Carbide-Based Cermets: The King of High-Speed Finishing
Titanium carbide-based cermets combine ceramic hardness with metallic toughness. Comprising titanium carbonitride (Ti(C,N)) with titanium carbide as a core component, these cermets use nickel (Ni) or cobalt (Co) binders, often enhanced with tantalum carbide (TaC) or tungsten carbide (WC). Titanium carbide cermets excel in high-speed finishing due to their hot hardness, chemical stability, and resistance to crater wear. Their low affinity with steel prevents built-up edge (BUE) formation, achieving mirror-like finishes in steels, sintered metals, and ductile cast iron.
Titanium Carbide Coatings: A Performance-Multiplying Shield
Titanium carbide coatings, applied via Physical Vapor Deposition (PVD) or Chemical Vapor Deposition (CVD), enhance tool substrates like cemented carbide. Titanium carbide coatings offer extreme hardness and wear resistance, ideal for continuous cutting of high-hardness steels and cast iron. Titanium carbonitride (TiCN) coatings, derived from titanium carbide, reduce friction for interrupted cutting and sticky materials like stainless steel. PVD preserves sharp edges for end mills, while CVD’s thicker coatings suit heavy-duty turning inserts.
Selecting the Right Titanium Carbide Coating: A Practical Guide
Choosing the appropriate coating is critical for optimizing titanium carbide tools in CNC machining. The performance of titanium carbide-based coatings varies depending on the workpiece material, cutting conditions, and desired outcomes, such as tool life or surface finish. For instance, titanium carbide coatings excel in abrasive environments, while TiCN coatings reduce friction for sticky materials. The table below serves as a quick-reference guide, summarizing the properties, advantages, and ideal applications of titanium carbide and related coatings. This guide empowers machinists to match coating types to specific machining challenges, ensuring efficiency and precision.
Table 1: Quick Selection Guide for Titanium Carbide-Based PVD/CVD Tool Coatings
Coating | Common Color | Core Advantage | Best Application Area (Workpiece Material/Condition) |
TiN (Titanium Nitride) | Gold | Versatile, cost-effective | General-purpose machining, low-carbon steel |
Titanium Carbide (TiC) | Black/Gray | High hardness, wear resistance | High-hardness steel, cast iron (continuous cutting) |
TiCN (Titanium Carbonitride) | Blue-gray/Violet-bronze | Hardness, low friction | Stainless steel, aluminum alloys, interrupted cutting |
TiAlN (Titanium Aluminum Nitride) | Violet-black/Dark gray | High-temperature resistance | High-speed dry cutting, hard steel, superalloys |
How to Use This Table: Machinists can select titanium carbide coatings for high-hardness materials like cast iron to maximize wear resistance, or opt for TiCN coatings when machining stainless steel to minimize adhesion. For high-temperature dry cutting, TiAlN complements titanium carbide’s capabilities, offering versatility across demanding conditions. By aligning the coating choice with the machining task, titanium carbide tools can significantly enhance productivity and tool longevity.
Part 3: Titanium Carbide vs. Tungsten Carbide: A Head-to-Head Comparison
Choosing between titanium carbide and tungsten carbide (WC) tools requires understanding their performance trade-offs. Titanium carbide excels in specific high-speed, precision applications, while tungsten carbide remains a reliable choice for general-purpose machining. The decision hinges on factors like workpiece material, cutting speed, machine rigidity, and cost considerations. The comparison table below provides a detailed breakdown of titanium carbide and tungsten carbide properties, offering machinists a clear framework to evaluate which material best suits their needs.
Understanding Titanium Carbide vs. Tungsten Carbide
The choice between titanium carbide and tungsten carbide tools is not one-size-fits-all. Titanium carbide’s lightweight design and superior thermal stability make it ideal for high-speed finishing and dry cutting, particularly in applications requiring fine surface finishes. In contrast, tungsten carbide’s higher toughness suits heavy roughing and interrupted cuts where stability is critical. The table below outlines key properties, their values, and practical implications, enabling machinists to make informed decisions. By understanding these trade-offs, users can leverage titanium carbide’s strengths to optimize CNC machining processes for specific tasks.
Table 2: Titanium Carbide vs. Tungsten Carbide for Machinists
Property | Titanium Carbide (TiC) | Tungsten Carbide (WC) | What It Means for the Machinist |
Hardness (HV) | 2800–3200 | 1800–2400 | Titanium carbide offers superior wear resistance for finishing. |
Fracture Toughness (MPa⋅m½) | 1.3–3.8 | 7–13 | WC is tougher for roughing; titanium carbide needs stable conditions. |
Density (g/cm³) | 4.93 | 15.6 | Titanium carbide reduces spindle load in high-speed milling. |
Thermal Stability | Resists oxidation up to 800°C | Oxidizes above 500°C | Titanium carbide excels in high-temperature dry cutting. |
Thermal Conductivity (W/m⋅K) | 21–25 | 84–100 | Titanium carbide directs heat to chips, protecting tools. |
Cost | Higher | Lower | Titanium carbide’s efficiency offsets higher initial cost. |
Ideal Application | High-speed finishing, dry cutting | Roughing, interrupted cuts | Task-specific trade-off. |
How to Use This Table: When planning a CNC machining operation, refer to this table to match tool material to the task. For high-speed finishing of steels, choose titanium carbide tools to leverage their wear resistance and thermal stability. For heavy-duty roughing or less stable setups, tungsten carbide is preferable due to its toughness. By aligning tool selection with these properties, machinists can optimize performance, reduce costs, and achieve consistent results with titanium carbide tools.
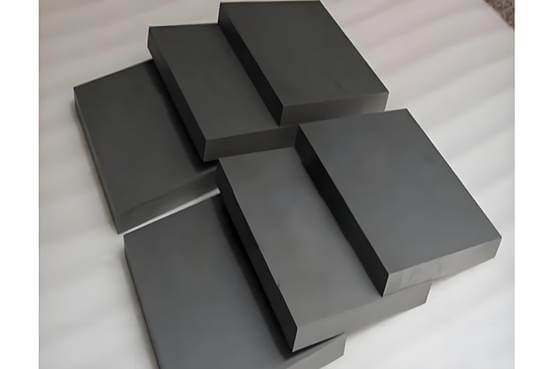
Part 4: A Practical Guide to Titanium Carbide Tool Selection and Implementation
Titanium carbide tools, including cermets and coatings, are selected based on workpiece properties and machining conditions. A systematic approach ensures optimal performance.
Tool Selection for Specific Workpieces
Carbon and Alloy Steels: Titanium carbide-based cermets achieve excellent finishes at high speeds, resisting crater wear. TiCN-coated titanium carbide tools balance wear resistance and toughness for milling and turning.
Cast Iron: Titanium carbide’s hardness suits abrasive cast iron; titanium carbide or TiAlN coatings resist wear.
Stainless Steel: TiCN-coated titanium carbide tools prevent BUE due to low friction. TiAlN coatings excel in high-speed machining.
High-Temperature Alloys: TiAlN or nanostructured titanium carbide coatings handle titanium and nickel-based alloys, though uncoated carbide may be used for sharp edges.
Optimizing Cutting Parameters
For titanium carbide-based cermets, prioritize stability and shallow cuts. Recommended parameters for steel finishing:
- Low-Carbon Steel: 350–450 m/min (1150–1476 sfm), 0.08–0.15 mm/rev (0.003–0.006 ipr), 0.2–0.8 mm depth (0.008–0.031 inch).
- Alloy Steel: 300–400 m/min (980–1310 sfm), 0.08–0.12 mm/rev (0.003–0.005 ipr), 0.2–0.6 mm depth (0.008–0.024 inch).
Dry cutting avoids thermal shock in titanium carbide cermets. Chipping/Fracture: Reduce feed/depth, enhance rigidity, or use tougher titanium carbide-coated tools for interrupted cuts. - Rapid Wear: Lower speed, select wear-resistant titanium carbide grades (e.g., CVD-coated cermets).
- Built-Up Edge (BUE): Increase speed, use low-friction titanium carbide coatings (TiCN).
- Poor Surface Finish: Replace worn titanium carbide inserts, optimize speed, or use wiper inserts.
Troubleshooting Titanium Carbide Tools
Part 5: The Future of High-Performance Machining: Advanced Applications of Titanium Carbide
Titanium carbide’s unique properties position it as a key material for future manufacturing, particularly in nanoscale engineering and high-tech industries.
Nanoscale Engineering
Nanostructured titanium carbide and TiCN coatings enhance toughness while maintaining hardness, reducing internal stress and improving adhesion. Multilayer coatings, alternating titanium carbide with TiN, prevent crack propagation, ideal for machining gas turbine rotors.
Aerospace and Biomedical Applications
Aerospace: Titanium carbide coatings and cermets enable precision machining of titanium and nickel-based alloys, meeting strict tolerances for aircraft components.
Biomedical: Titanium carbide’s biocompatibility makes titanium carbide-coated tools ideal for machining medical implants, reducing contamination and enhancing surface quality. Titanium carbide is also used in high-performance surgical instruments.
Conclusion: Why Titanium Carbide is Essential for Modern Machining
Titanium carbide’s unique properties have proven its value as a high-performance material, driving CNC machining forward. Titanium carbide tools enable higher cutting speeds, extend tool life through superior wear resistance, and deliver exceptional surface finishes. By integrating titanium carbide tools into your CNC processes, you can achieve significant gains in productivity and quality. Explore titanium carbide-based tools today to stay ahead in precision manufacturing—visit [Insert Relevant Link] for more information.
FAQ:
- What is titanium carbide (TiC) and why is it important in CNC machining?
Titanium carbide is an ultra-hard material with a Mohs hardness of 9–9.5. Its importance lies in its high hardness, thermal stability, and chemical inertness, enabling titanium carbide tools to excel in high-speed finishing with superior wear resistance and surface quality.
- What are the advantages of titanium carbide over tungsten carbide (WC)?
Titanium carbide has lower density (4.93 g/cm³ vs. 15.6 g/cm³), reducing spindle load, and better thermal stability (up to 800°C). It’s ideal for high-speed finishing, while tungsten carbide suits roughing and interrupted cuts.
3. Where are titanium carbide tools most effective in CNC machining?Titanium carbide tools shine in high-speed finishing of:
- Carbon/alloy steels: Titanium carbide cermets deliver mirror-like finishes.
- Cast iron: Titanium carbide coatings resist abrasion.
- Stainless steel: TiCN-coated titanium carbide tools prevent BUE.
- High-temperature alloys: TiAlN-coated titanium carbide tools handle tough materials.
4. How do titanium carbide cermets differ from coatings?
Titanium carbide cermets are composites for high-speed finishing, combining hardness and toughness. Titanium carbide coatings (1–5 µm) enhance substrates, offering wear resistance for continuous or interrupted cutting.
5. How do I choose the right titanium carbide coating?
Select based on workpiece and conditions:
- Titanium carbide (TiC): High-hardness steel, cast iron (continuous cutting).
- TiCN: Stainless steel, interrupted cutting (low friction).
- TiAlN: High-speed dry cutting of hard alloys. See Table 1 in the article for details.
6. What are common issues with titanium carbide tools and their fixes?
- Chipping/Fracture: Reduce feed/depth, increase rigidity, or use tougher titanium carbide coatings.
- Rapid Wear: Lower speed, choose wear-resistant titanium carbide grades.
- Built-Up Edge (BUE): Increase speed, use TiCN-coated titanium carbide tools.
- Poor Surface Finish: Replace worn titanium carbide inserts or use wiper inserts.
7. Are titanium carbide tools suitable for all CNC tasks?
Titanium carbide excels in high-speed finishing and dry cutting but is less suited for heavy roughing or unstable interrupted cuts due to lower toughness. Tungsten carbide is better for those tasks.
Reference:
https://www.acapublishing.com/dosyalar/baski/BEN_2020_79.pdf
https://en.wikipedia.org/wiki/Titanium_carbide
https://www.sciencedirect.com/topics/materials-science/titanium-carbide
https://www.azonano.com/article.aspx?ArticleID=3379
Other Articles You Might Enjoy
- Cemented Carbide: The Material Science and Application Strategies Driving High-Performance CNC Machining
Part 1: The Material Science of Cemented Carbide: The Core of CNC Machining As a machinist with 15 years of experience, I’ve come to appreciate cemented carbide as the unsung…
- Silicon Carbide and CNC Machining: A Comprehensive Technical Analysis of Materials, Processes, and Applications
Introduction Silicon carbide (SiC) stands as a pinnacle of advanced ceramics, engineered to thrive in environments that push materials to their limits. Its extraordinary hardness, thermal resilience, and chemical stability…
- Machining the 'Black Diamond': A Comprehensive Guide to Advanced CNC Techniques for Boron Carbide
Boron carbide, often hailed as the "black diamond," is an advanced ceramic renowned for its extraordinary hardness, surpassed only by diamond and cubic boron nitride (cBN). Its unique blend of…
- Tungsten Carbide: From Powder to Performance in CNC Machining
I. Introduction: The Powerhouse Behind Precision CNC Machining In the fast-paced world of precision manufacturing, where aerospace components demand flawless tolerances and medical implants save lives, one material reigns supreme:…
- Performance, Selection, and Process Optimization of CNC Carbide Burrs in CNC Machining
Introduction: The Transformative Power of Carbide Burrs in CNC Machining In the fast-evolving realm of CNC machining, where precision, automation, and efficiency are paramount, the carbide burr—often referred to as…