Machining curved surfaces is a fascinating aspect of profile/contour CNC milling. This technique allows for the creation of intricate shapes and continuous curves with varying degrees of slant, concavity, or convexity. It plays a crucial role in producing uniquely shaped bespoke parts, requiring CNC machining service providers to possess advanced knowledge of fundamental machining principles and programs.
Fundamentals of Profile CNC Milling
1. Profile CNC Milling Processes
Before achieving the final machined part, the milling process involves several stages: roughing/semi-roughing, semi-finishing, finishing, and super-finishing. The number of operations increases with the size and complexity of the component. By categorizing the operations, it becomes possible to maximize the potential of the tooling and parameters used.
Roughing: The first stage of machining, roughing involves cutting the raw material block into a shape or profile that is close to the desired final form. This leaves sufficient material for subsequent operations.
Semi-finishing: In this process, the part is machined to meet dimensional requirements or to remove any remaining stock. Semi-finished parts may undergo further processing to achieve specific surface finish requirements.
Finishing: Following the semi-finishing operation, the finishing process focuses on enhancing the surface finish of the part by removing visible burrs and other surface flaws. The use of high-performing tools is essential, as it significantly impacts the final appearance of the work part.
Super-finishing: For parts that require a mirror finish or an exceptionally smooth profile, the operation advances to super-finishing. This stage involves utilizing high-speed machining techniques and high-precision tools to achieve the desired surface quality.
2. Tools Used in CNC Milling of Curved Surfaces
To achieve smooth-curved surfaces, various types of rounded end mills are employed. These include rounded inserts, ball nose indexable end mills, and ball nose solid carbide tools. Rounded tooling is preferred for contouring applications as it minimizes visible tool path marks.
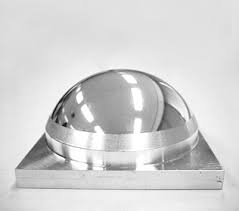
Insert-type end mills with rounded inserts: These tools, available in larger diameters, offer high stability and impressive productivity, making them suitable for roughing operations.
Solid ball nose end mills: These end mills are known for delivering excellent surface finishes. Although they may have lower stability due to their structure, they are commonly used for finishing rather than roughing operations.
Indexable head ball nose end mills: Similar to solid carbide end mills, these tools feature exchangeable heads. This flexibility allows for the replacement of the end when needed, providing versatility in machining operations.
Useful Tips for CNC Milling of Curved Surfaces
1. Necessary Preparations
Before embarking on profile milling for custom parts, it is crucial to consider various factors that may influence the CNC milling process. By identifying these aspects, it becomes easier to select the most suitable machining techniques. Here are some essential preparatory considerations:
- Cavity depths: The depth of the cavities in part designs plays a significant role in selecting the appropriate cutting tools and determining the required gauge length.
- Material subtraction: Understanding how much material needs to be removed from the raw block helps in planning the necessary operations, such as additional procedures after semi-finishing and semi-roughing.
- Workpiece clamping: Determining the optimal clamping method ensures proper fixation of the workpiece during the milling process, necessitating the use of suitable fixtures.
2. The Importance of Feeds and Speeds
Feeds and speeds are critical factors that determine the rate of material removal and the achievement of an excellent surface finish.
Calculations based on factors such as depth of cut, tooling, material hardness, part profile, and required accuracy are necessary for optimal results. Here are some basic guidelines:
- Material hardness: The depth of cut and feed rate vary depending on the hardness of the materials being machined. Harder materials require lower feeds and depths of cut compared to softer materials like aluminum. Additionally, the cutting speed should be faster for harder materials.
- Roughing vs. finishing: Feed rates and depths of cut for roughing operations are more aggressive than those for finishing operations. Achieving an excellent surface finish depends on a combination of high-speed techniques and the use of appropriate tools.
3. Optimal Tooling Utilization
The market offers a wide range of tools for CNC milling, catering to different requirements. For roughing operations, tooling rigidity is prioritized to withstand the aggressive cutting demands. On the other hand, sharp end mills are preferable for finishing operations to ensure a clean tool path. Additionally, roughing tools typically have larger diameters compared to finishing tools.
4. Minimizing Vibration in CNC Milling Processes
Vibration during milling can adversely affect surface finish, cause chatter, and damage cutting tools. To minimize these issues, several measures can be taken:
- Runout accuracy: Tools with good runout accuracy help reduce vibration and ensure consistent machining results.
- Overhang limitation: During roughing operations, excessive overhang in end mills can lead to vibrations. Using extension bars or holders can provide better stability and reduce vibration.
- Secure work holding fixtures: Properly gripping and balancing work holding fixtures during cutting operations enhances stability and minimizes vibration.
- Avoid aggressive cuts: When working with hard metals, avoiding overly aggressive cuts can help prevent vibrations and improve surface finish.
Conclusion
CNC milling of curved surfaces involves a gradual progression through various operations, including roughing, semi-finishing, finishing, and super-finishing. Rounded tooling, such as ball nose end mills, is commonly used for this type of milling. To achieve optimal results, proper preparation, correct feeds and speeds, appropriate tool selection, and vibration reduction techniques are crucial. By implementing these guidelines, CNC milling professionals can achieve outstanding surface finishes and create intricate curved surfaces with precision and finesse.
Recommended Reads:
- How Industry 4.0 Revolutionizes CNC Machining
- 3 Essential Solutions for Manufacturing Prototyping Projects
- What is Diamond Machining
- Why Custom Prototypes Are Shaping the Future of Manufacturing
- Precision Rotor Blade Prototypes through 5-Axis Machining
Related Posts
- Revolutionizing Renewable Energy with CNC Machined Components
Introduction: Renewable Energy and CNC Machined Components Renewable energy harnesses power from natural sources such as the sun, wind, and water, making it a sustainable and eco-friendly alternative to traditional…
- Is Copper the Right Choice for Electrical Component CNC Machining? A Detailed Analysis
CNC Machining of Electrical Components Utilizing Copper In the field of electrical engineering, Computer Numerical Control (CNC) machining plays an integral role, particularly in the development and manufacturing of electrical…
- CNC Machining Brass vs. Bronze: Cost, Properties, and Applications Showdown?
Introduction to CNC Machining Brass vs. Bronze: Cost, Properties, and Applications Showdown? In this article, we delve into the debate between brass and bronze machining for an important manufacturing process…