The term “grinding machine” might be unfamiliar to many, but it plays an indispensable role in our daily lives. Whether it’s the car you drive, the electronics you use, or the medical devices in hospitals, grinding machines are crucial. So, what exactly is a grinding machine? How does it work? Let’s explore.
What is a Grinding Machine?
Imagine sanding wood or stone at home; a grinding machine operates on a similar principle but is a specialized tool in manufacturing. The main task of a grinding machine is to ensure that parts achieve superior surface quality and precision, akin to performing microsurgery on products to refine their appearance. Grinding machines remove material from a workpiece using rotating abrasive wheels, shaping, smoothing, or finishing it.
Primary Uses of Grinding Machines
Grinding machines have a variety of uses. They can perform initial shaping and smoothing of cylindrical and conical surfaces, excel at finishing internal cylinders or bores, and manufacture and hone cutting tools. The use of grinding machines eliminates rough projections from castings and stampings and can also clean, polish, and buff surfaces. Although initially designed primarily as a finishing technique, modern production-grade grinding machines often handle both roughing and finishing tasks.
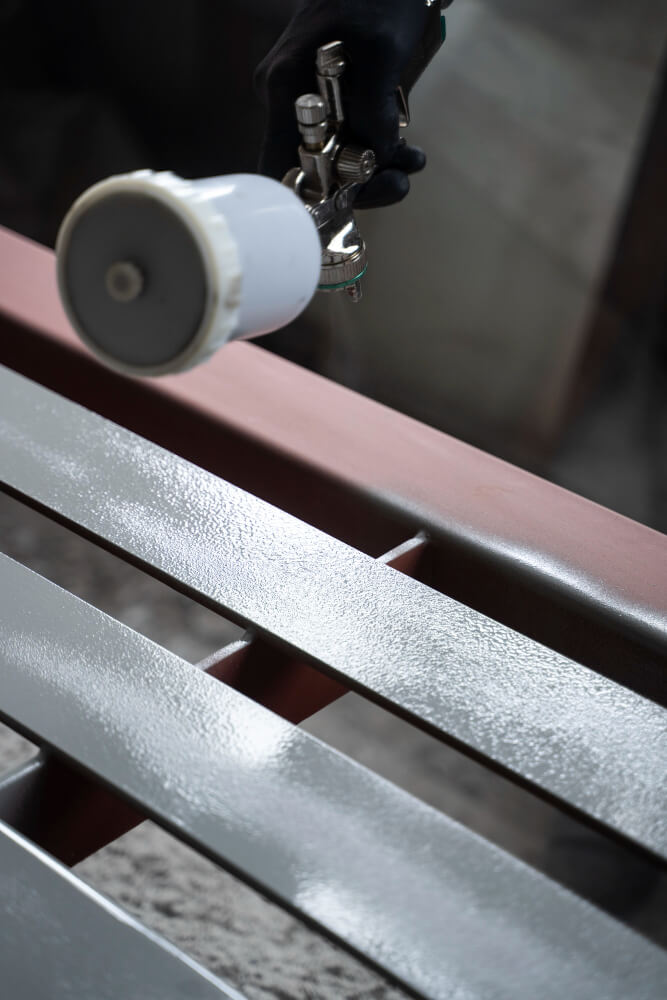
Applications of Grinding Machines in Various Industries
Aerospace Industry
In the aerospace sector, grinding machines are commonly used to manufacture aircraft engine components and lightweight structural parts. Grinding ensures that these components maintain stability during flight, guaranteeing the aircraft’s safety. Grinding machines can achieve very high precision, allowing these critical parts to fit perfectly.
Automotive Industry
Grinding machines are equally important in automotive manufacturing. Engine components and precision parts of transmission systems, such as crankshafts and camshafts, require high precision. During engine operation, the parts need to fit together seamlessly, and grinding ensures the dimensions and smoothness of these parts are optimal, providing excellent and reliable automotive performance.
Medical Industry
In the medical device manufacturing industry, precision is a key criterion. Especially for artificial joints or implantable devices, surface smoothness directly affects their compatibility with human tissue, reducing friction and tissue damage risks. Grinding machines achieve extremely high precision, meeting the strict standards of the medical industry to ensure successful surgeries and patient safety.
Hardware, Communication Equipment, Mechanical Parts
Many of the hardware, communication equipment, and mechanical parts we use daily undergo grinding. These parts may be complex in shape, vary in hardness, or be a combination of metals and non-metals. Grinding machines solve the difficulties of machining complex shapes and enhance precision and quality, significantly improving the overall quality of products.
How Grinding Machines Work
Grinding machines are primarily used for finishing operations and are known for their structural rigidity. They use grinding wheels composed of fine, extremely hard particles to perform precision grinding operations. The grinding process is crucial for achieving the desired shape and surface quality of products. Typically, grinding follows roughing operations that remove most residual material from the workpiece, with subsequent grinding work eliminating any remaining excess material to create a finely finished surface.
Grinding machines consist of a base or pallet, worktable, and vertical column. The base houses mechanisms for controlling the longitudinal and transversal movements of the worktable and mounts for the wheel spindle’s motion. Longitudinal table movement is generated and controlled by an oil dynamic circuit, ensuring smooth and consistent motion even with gear transmission.
The wheel’s movement may require rotation around both horizontal and vertical axes. Vertical spindle orientation is suitable for quick and effective grinding using cup grinding wheels, although it may leave traces on the surface. In contrast, horizontal spindle orientation uses disk wheels that can smooth a part’s surface and machine longitudinal grooves and grooved shafts.
Types of Grinding Machines
Grinding machines come in various types, each tailored to specific processing needs. Here are some common types:
Bench Grinder
Bench grinders are usually fixed on a workbench or table. They have one or two grinding wheels and can be operated manually or with power, commonly used for sharpening cutting tools.
Hand Grinder
Hand grinders are not fixed and are maneuvered by the operator. An example is an angle grinder, used for non-precision cutting, grinding, and polishing tasks.
Pedestal Grinder
Pedestal grinders are powered by electricity and mounted on a pedestal frame on the ground. They typically have a grinding wheel on both sides of the motor shaft and are used in workshops for sharpening cutting tools and cleaning parts after molding.
Portable Grinder
Portable grinders are compact and electrically operated, easily carried to different locations, often used for tasks like cleaning heavy welds.
Flexible Grinder
Flexible grinders feature an electric motor with a flexible shaft allowing the grinding wheel to move in any direction, suitable for large grinding tasks.
Precision Grinder
Precision grinders are designed for high accuracy and smooth finishes, including various subtypes like cylindrical grinders, plunge cut grinders, form grinders, internal grinders, centerless grinders, surface grinders, universal grinders, and tool and cutter grinders.
Cylindrical Grinder
Cylindrical grinders are used to grind surfaces that have been made plain, such as sleeves, pins, rods, and taper pins. Types include plain cylindrical grinders, roll grinders, and piston grinders.
Plunge Cut Grinder
Plunge cut grinders are used for grinding small shafts, often referred to as crankshaft grinding machines, also used for camshaft grinding.
Form Grinder
Form grinders use different shapes of grinding wheels to match the desired profile for non-standard shapes.
Internal Grinder
Internal grinders are designed for grinding round and hollow features, including cylindrical surfaces with different internal shapes.
Centerless Grinder
Centerless grinders are powered and support the workpiece at three separate points, allowing continuous motion. Types include through-feed, in-feed, and end-feed centerless grinding.
Surface Grinder
Surface grinders are ideal for flat surface grinding and can use rotary or reciprocating tables, further classified into vertical spindle and horizontal spindle surface grinders.
Factors to Consider When Choosing a Grinding Machine
Choosing the right grinding machine involves several considerations to ensure it meets your specific needs and intended applications. Key factors include:
- Type of grinding: Whether it’s surface grinding, cylindrical grinding, or tool and cutter grinding.
- Materials: Some grinding machines are better suited for specific materials like metals, ceramics, or plastics.
- Precision requirements.
- Grinding wheel type, size, and composition.
- User-friendliness.
- Safety features like wheel guards, emergency stops, and safety interlocks.
- Machine specifications: Size of the grinding wheel, power requirements, speed, control type (manual or CNC), and spindle orientation (horizontal or vertical).
- Automation features for high production rates: Tool/nozzle changers, loading aids, closed-loop measurement, and large quantities of parts.
- Effective cooling system to prevent overheating and maintain workpiece integrity.
- Ease of maintenance and availability of service and replacement parts.
- Budget.
- Reputable supplier or manufacturer known for reliable grinding machines and excellent customer support.
Materials That Can Be Machined Using Grinding Machines
Grinding machines are versatile tools capable of machining a wide range of materials, including:
- Metals: Carbon steel, stainless steel, aluminum, brass, iron, titanium, Monel, Inconel, tool steels, etc.
- Concrete: Used for smoothing and preparing concrete surfaces.
- Tiles: Cutting and shaping ceramic or porcelain tiles.
- Stone: Machining natural and synthetic stones like granite, marble, quartz, and engineered stone.
Price Factors of Grinding Machines
The price of grinding machines can vary significantly based on several key factors:
- Type and size: Smaller, simpler machines like bench grinders are more affordable than larger, specialized CNC grinding machines.
- Features: Machines with advanced capabilities, such as automation and precision controls, typically cost more.
- Brand and quality: Well-known brands with a track record for quality often command higher prices.
- Condition: New machines are pricier than used ones.
- Specifications: Differences in power, capacity, precision, tolerance levels, and accessories can affect the price.
- Service and support: The level of service and support provided by the supplier can also impact the cost.
Average Price of Grinding Machines
It’s challenging to provide an exact price range for grinding machines due to the wide variety of options and specifications. The cheapest grinding machines are usually handheld types, ranging from $50 to a few hundred dollars. Bench grinders follow, with prices also reaching a few hundred dollars. However, CNC grinders are the most expensive, with some cylindrical grinders costing between $300,000 and two million dollars. Centerless grinders can also sell for over $80,000.
Safety Precautions for Using Grinding Machines
When using grinding machines, it’s essential to follow some safety guidelines:
- Always wear safety goggles.
- Check grinding wheels for cracks using the ring test before mounting.
- Never exceed the recommended speed for grinding wheels.
- Do not adjust the workpiece or any mounting devices while the machine is in operation.
- Ensure the depth of cut for both the grinding wheel and the machine does not exceed their recommended limits.
- Remove the grinding wheel from the workpiece surface before turning off the machine.
- Utilize appropriate wheel guards on all grinding machines.
- For bench grinders, adjust the tool rest to be 1/16 to 1/8 inch away from the wheel.
Are Grinding Machines Expensive?
It depends on the specific situation. The cost of grinding machines can vary widely depending on several factors. Grinding machines come in various types and sizes, from small, affordable bench grinders to large, specialized, and extremely pricey industrial CNC grinding machines. Whether they are considered expensive largely depends on the intended use and your budget. For individuals or small businesses with limited grinding needs, basic and affordable options may suffice. On the other hand, industrial applications requiring precision and high production rates often necessitate more expensive, specialized machines. The price can also be influenced by factors such as features,
precision, brand reputation, and whether the machine is new or used.
Alternatives to Grinding Machines
Alternatives to grinding machines depend on the specific machining or finishing task. Common alternatives include:
- Milling machines
- Lathes
- Electrical discharge machining (EDM)
- Waterjet cutting
- Laser cutting
- Abrasive blasting
- Chemical etching
- Ultrasonic machining
In summary, grinding machines play a vital role in modern manufacturing. Whether in aerospace, automotive, medical, or everyday products, grinding machines provide crucial support. By understanding the principles, types, and applications of grinding machines, we can better appreciate how these “unsung heroes” bring convenience and safety to our lives.
Other Articles You Might Enjoy
- CNC Machining of Biodegradable Materials for Sustainable Manufacturing
Introduction to CNC Machining and Sustainable Manufacturing CNC machining stands as a pivotal technology in modern manufacturing, utilizing computer-controlled processes to precisely shape materials. This method not only enhances efficiency…
- 3 Types of CNC Milling Machines: Process & Production
What Is CNC Milling Machining Process? CNC milling is a process that uses rotating cutters to gradually remove material from a block until the required customs form is created. It…
- Cobalt Chrome Alloys in Medical Implant Manufacturing: CNC Machining Considerations?
Introduction: Overview of Cobalt Chrome Alloys in Medical Implant Manufacturing Cobalt chrome alloys are extensively involved in the production of medical device implants due to their superior characteristics such as…
- 5 Main Types of CNC Machines: A Comprehensive Guide
Computer Numerical Control (CNC) machines have revolutionized modern manufacturing processes with their precision and versatility. These machines use computer programs to control their movements and operations, resulting in highly accurate…
- CNC Machining for High-Temperature Applications: Inconel vs. Stainless Steel
Introduction to CNC Machining CNC (Computer Numerical Control) machining, a vital part of today's manufacturing industry, uses pre-programmed computer software to direct the motions of sophisticated machinery during the fabrication…
- What Is Mill Tooling? Five Types of Mill Tools
According to a report by Grand View Research, the global CNC machining market size was valued at USD 66.6 billion in 2020 and is expected to grow at a compound…