In today’s ever-evolving technological landscape, clients have increasingly high expectations for the devices manufactured by companies like Want.Net. Just a mere 5-10 years ago, the idea of having phones, watches, cameras, or lights that could function underwater seemed like something out of a sci-fi movie. However, these days, if we come across a non-waterproof watch, we can’t help but frown upon it. While many tablet and cellphone models can now be submerged or withstand accidental drops into puddles, certain devices like blenders, electric pots, and other home appliances still struggle with waterproofing. But the journey to creating a truly waterproof device is no easy feat.
The Key to Water Resistance
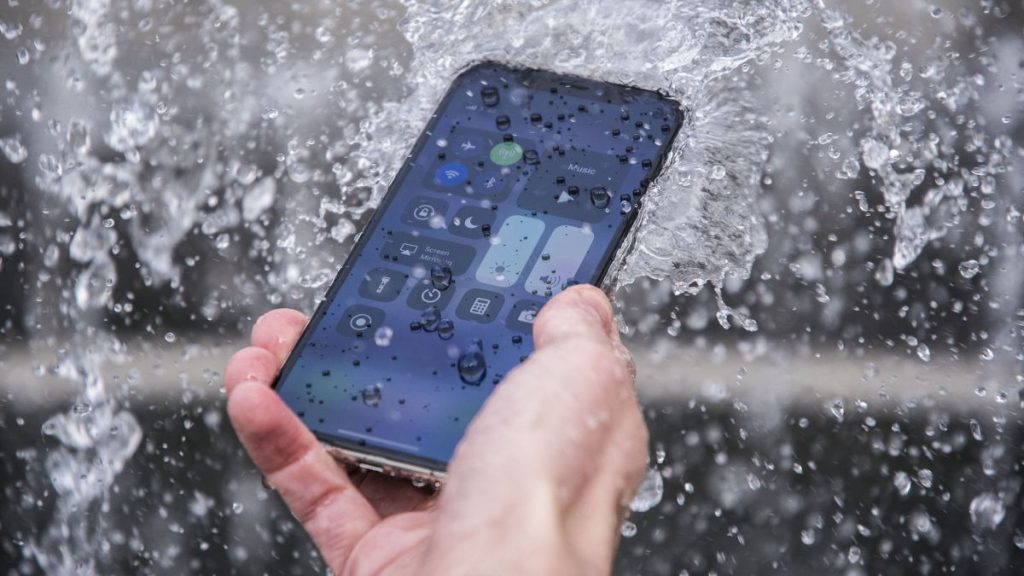
The crucial element in achieving water resistance lies in the design of the case itself. The case must effectively prevent water from infiltrating and short-circuiting the delicate electronics within. To accomplish this, special features must be incorporated to create barriers that deter the flow of water. However, even with these features, it is essential to create a waterproof plastic prototype of the case to conduct comprehensive tests and ensure that it remains impervious to leaks. So, without further ado, let’s delve into a few design tips for creating custom plastic cases and explore some insights on metal cases that offer protection against water. Additionally, we will uncover some rapid prototyping tips to expedite the development process.
Understanding Waterproof Case Standards
To embark on your journey to waterproofing, it is vital to comprehend the various degrees of waterproof cases. These degrees are rated according to the widely recognized International Protection (IP) and National Electrical Manufacturers Association (NEMA) standards. For the purpose of this guide, we will focus on the IP standards. Let’s explore the IP-rated watertight degrees:
- IP65: This standard demands that the case can withstand a water jet. To test this, an case is subjected to water being poured from every conceivable angle through a 6.3 mm nozzle. The parameters for this test are as follows: distance – 3 meters, nozzle diameter – 6.3 mm, water pressure – 30 kPa, and water volume – 12.5 liters per minute.
- IP66: cases adhering to this standard must withstand high-pressure water jets. The test involves exposing the case to a 12.5 mm diameter water nozzle, which delivers water at a rate of 100 liters per minute with a pressure of up to 100 kPa for a duration of 3 minutes.
- IP67: This standard requires a completely waterproof design. The case is submerged under 1 meter of water for half an hour during testing.
These IP standards offer varying levels of water protection. This versatility allows designers to precisely estimate the working conditions their devices are expected to endure and determine the appropriate extent to which water deflection features should be integrated. It is worth noting that creating a completely waterproof design is significantly more expensive than producing an case that can withstand water jets or occasional drops.
Five Effective Methods for Waterproof Connections
Now that we are well-versed in the standards for watertight plastic cases, let’s explore five effective methods commonly employed to achieve water resistance when manufacturing custom plastic cases that comply with IP66-67 standards:
Seals and Gaskets
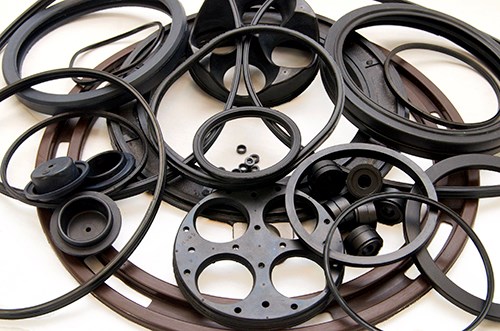
Rubber seals are the most common, cost-effective, and practical solution for creating waterproof plastic cases, regardless of whether they are made of aluminum, metal, or other materials. These seals leverage the elasticity of rubber to cover the connecting parts, forming a protective barrier against liquid infiltration. Among the various seal options available, o-seals stand out as highly effective. These circular rubber rings with a roundcross-section exhibit exceptional suppression rates against liquids, making them ideal for safeguarding against water intrusion. In fact, o-seals can even be utilized to create dynamic seals, where one part moves while the other remains stationary. By incorporating 2-3 grooves with o-seals in the static part of the case, a reliable and flexible seal can be achieved.
Insert Molding
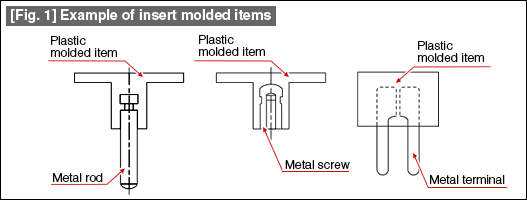
This technique proves beneficial for aluminum or metal cases. It involves molding an elastic element onto a metal part, resulting in a smaller and more secure seal. By integrating the seal directly into the molding process, the risk of losing or misplacing the seal is mitigated.
Overmolding
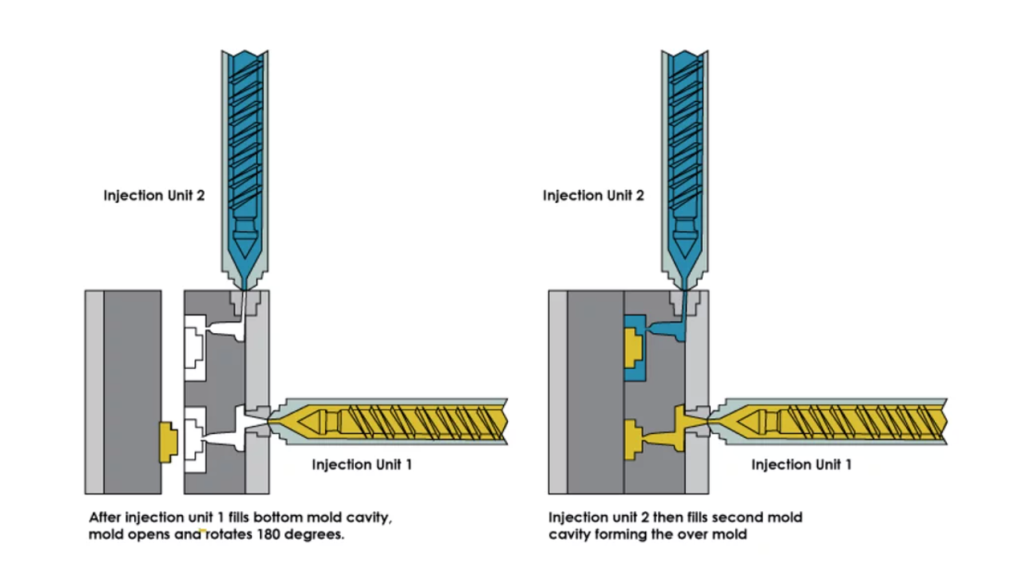
Similar to insert molding, overmolding involves the use of plastic as the base component, along with the metal part. This method is particularly viable for mass production, as it employs the cost-effective process of plastic injection molding. However, it’s important to note that overmolding requires sophisticated equipment and expertise. Thanks to advancements in manufacturing technology, designers can now leverage prototyping services that offer rapid injection molding, allowing for efficient testing and cost-effective production of prototype batches.
Welding
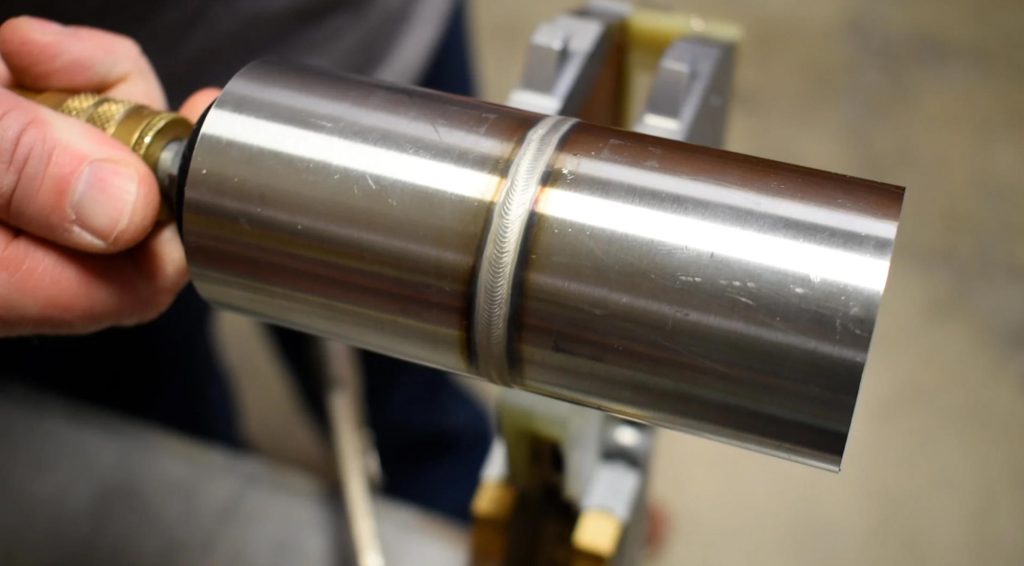
Welding is commonly employed in metal cases for electronics. It involves melting the metal around the rims of the joined parts, creating a hermetically sealed and unified component. However, it is essential to consider the potential drawbacks of complete sealing. While welding ensures maximum water resistance, it can make device repairs challenging, as accessing and repairing the enclosed components becomes significantly more difficult. Additionally, welding may result in the entrapment of air within the case, which can lead to pressure buildup and potential bursting under temperature changes.
Foam Tape and Adhesives
Foam tape and adhesives offer a simple yet effective solution for achieving water resistance in cases. These materials are easy to apply and provide reliable protection against water infiltration. Foam tape and adhesives are particularly useful in scenarios where design modifications are impractical or where rapid prototyping and design verification tests are conducted. However, it is important to consider that these methods are typically suitable for single-use or semi-permanent connections, as they may pose challenges when disassembling and reassembling the case due to adhesive residue.
Waterproof Case Rapid Prototyping
Once you have determined the optimal placement of O-rings, welding points, and adhesive connections, it is crucial to validate the effectiveness of your design through physical testing. This is where rapid prototyping plays a pivotal role. By manufacturing a prototype of the waterproof case, you can conduct thorough tests and make necessary refinements before moving forward with mass production.
To facilitate rapid prototyping, different techniques can be employed depending on the materials used:
3D Printing
Small plastic cases and medium-sized ones can be realized through 3D printing. This additive manufacturing process allows for the creation of intricate designs with relative ease, enabling rapid iteration and modifications.
CNC Machining
Metal case designs can be actualized through CNC machining. This subtractive manufacturing process utilizes precision machining tools to shape the case from solid blocks of metal, ensuring accuracy and durability.
Rapid Injection Molding
Overmolded designs or prototype batches can be efficiently manufactured using rapid injection molding, a cost-effective alternative to conventional molding. This technique involves the use of flexible mold designs and allows for the production of high-quality prototypes at a lower cost and shorter lead times compared to traditional molding methods.
During the assembly of prototypes, meticulous attention to detail is crucial to ensure optimal test results. If the tests yield unsatisfactory outcomes, it becomes necessary to revisit the design and initiate remanufacturing. Rapid prototyping offers the flexibility to incorporate modifications swiftly and receivea modified prototype promptly, accelerating the iterative design process.
By following these comprehensive guidelines and leveraging the capabilities of rapid prototyping, you can successfully create a waterproof plastic prototype case. Thorough testing and refinement will enable you to meet the increasing demands of clients for reliable and water-resistant devices. Embrace the journey of waterproofing your products and embrace the ever-growing expectations of the modern consumer.
Recommended Reads:
- 5 Main Types of CNC Machines: A Comprehensive Guide
- Top 15 Terms in CNC Machining: A Beginner’s Glossary
- 5 Exciting Evolutionary Milestones in CNC Machining History
- 12 Essential Components of a CNC Machine Every Beginner Should Know
- Comparing 3-Axis, 4-Axis, and 5-Axis CNC Machining Techniques
Other Articles You Might Enjoy
- Precision CNC Machining of Steel: High-Volume Production
Precision CNC Machining and High-Volume Production As an integral part of modern manufacturing processes, Precision Computer Numerical Control (CNC) machining brings about unmatched accuracy and consistency in the production of…
- Prototype CNC Machining: Everything You Need to Know
The emergence of CNC machining has changed the entire manufacturing industry. This technology has been developed for more than 70 years and is now very mature. And used in various…
- CNC Plastic Machining: Custom Finished Parts for Your Project
In most cases, many people will directly understand CNC machining as a metal workpiece machining process. However, the fact is that CNC machining is not only widely used in metal…